Procédé Manhès-David
Le procédé Manhès-David est un procédé d'affinage des mattes de cuivre inventé en 1880 par l'industriel français Pierre Manhès et son ingénieur Paul David. Inspiré du procédé Bessemer, il consiste en l'utilisation d'un convertisseur pour oxyder avec de l'air les éléments chimiques indésirables (essentiellement le fer et le soufre) contenus dans la matte afin de la transformer en cuivre.
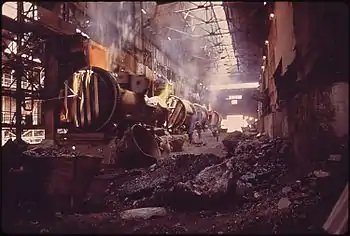
La quantité des éléments à oxyder, ainsi que la faible chaleur produite par les réactions chimiques, ont imposé des modifications du convertisseur. Manhès et David lui donnent la forme d'un cylindre, avec des tuyères alignées d'un bout à l'autre. Quelques années plus tard, les Américains William H. Peirce et Elias A. C. Smith le maçonnent avec un revêtement réfractaire basique, beaucoup plus durable que celui utilisé par les inventeurs français. Si cette amélioration ne modifie pas les principes du procédé, elle facilite son utilisation à grande échelle, accélérant le basculement de la production de cuivre du Royaume-Uni vers les États-Unis.
Au début du XXIe siècle, le convertisseur Peirce-Smith assure l'affinage de 90 % des mattes cuivreuses et intervient dans 60 % du nickel extrait. Ce convertisseur, comme l'addition d'oxygène pur, l'automatisation de la conduite, le traitement des fumées et la taille croissante des outils ont assuré la pérennité du procédé Manhès-David, même si les outils modernes n'ont plus guère de rapport avec leurs ancêtres.
Genèse du procédé
Filiation avec le procédé Bessemer
Tout comme le fer produit par un haut fourneau en sort allié à d'autres éléments chimiques pour former la fonte, le cuivre extrait du minerai se présente sous la forme d'un alliage de cuivre, de soufre, de fer, etc. appelé matte. Appliquer les mêmes procédés à ces deux métaux est donc une démarche logique. Transposer le procédé Bessemer à la métallurgie du cuivre a été ainsi proposé, et le principe validé en 1866, soit dix ans après l'invention de Henry Bessemer, par l'ingénieur russe Semenikow[L 1]. Pourtant, l'application pratique est plus complexe :
« Les analogies entre ces deux fabrications sont en effet très grandes. De même qu'au haut fourneau, le minerai est réduit à l'état de fonte, combinaison de fer et de carbone, de même le minerai de cuivre est transformé […] en un composé sulfuré, formé de cuivre, de fer et de soufre. Dans ces deux opérations, on sépare les métaux des gangues, et l'on obtient des produits principaux analogues ; d'un côté, c'est un carbure et un siliçure de fer et de manganèse ; de l'autre, un sulfure de fer et de cuivre.
Par la simple action du vent, on élimine pendant l'opération Bessemer le silicium, le manganèse et le carbone ; de la même manière, on enlève à la matte son soufre et son fer, qui sont tous deux plus oxydables que le cuivre. Mais les difficultés rencontrées dans le traitement des mattes sont bien plus grandes que celles du traitement de la fonte, où les éléments à oxyder ne dépassent pas 9 à 10 % du poids du métal ; [dans] la matte, au contraire, […] il faut enlever par oxydation 80 % des matières traitées. Les éléments étrangers de la fonte, silicium et carbone, développent en brûlant une quantité considérable de chaleur[…]. Le soufre et le fer, au contraire, ne produisent qu'une [fraction de cette chaleur][1]… »
— P. L. Weiss, Le Cuivre
En effet, les mesures montrent que l'affinage de la fonte au convertisseur est possible car la combustion des éléments indésirables est fortement exothermique : l'oxydation du silicium et du carbone y produit respectivement 32,8 et 10,3 kilojoules par kilogramme[2]. À l'inverse, si une matte de cuivre contient en abondance du fer et du soufre, il faut d'abord dissocier ces éléments, ce qui consomme 6,8 kilojoules par kilogramme de FeS, avant que leur oxydation, qui ne produit respectivement que 5,9 et 9,1 kJ/kg, puisse commencer[H 1] - [1].
Premiers essais
Les premiers affinages de matte cuivreuse par un convertisseur sont réalisés à Ducktown, dans le Tennessee, où A. Raht[note 1] réalise de 1866 à 1875 un affinage partiel de la matte. En 1867, les Russes Jossa et Latelin essaient de valider expérimentalement les études de Semenikow. En 1870, ils stoppent leurs expériences après n’avoir parvenu qu'à élever la teneur en cuivre de leur matte de 31 % à 72-80 %[H 2].
En Angleterre, John Hollway approfondit ces essais jusqu'en 1878[note 2]. Comme ses prédécesseurs, il constate que si le soufflage commence de manière satisfaisante, celui-ci devient de plus en plus intermittent au fur et à mesure de l'avancement de l'affinage. Les obstacles relevés sont nombreux[L 2] :
- le poids des scories produites est égal à celui du cuivre, leur volume beaucoup plus important que celui du métal enfourné. Il faut donc vidanger régulièrement la cornue ;
- la densité du métal en fusion évolue fortement (le cuivre ayant une densité triple des pyrites dont il est issu) ;
- la durée du soufflage, qui atteint 2 heures, amène d'importantes pertes thermiques ;
- le revêtement réfractaire siliceux est absorbé par les scories[note 3], dans lequel il sert de fondant[note 4].
Toutes les difficultés rencontrées ne peuvent être facilement résolues : le bilan thermique de la réaction d'affinage à l'air du cuivre n'est pas aussi favorable que pour le fer, la matte se solidifie au nez des tuyères avant d'être affinée[1]. Même modifié, un convertisseur Bessemer n'est capable, au mieux, que d'ôter le fer et une partie du soufre[6]. Hollway échoue, mais en publiant tous les détails de ses expériences, il identifie les problèmes essentiels[7].
Les tuyères latérales
Dans les années 1870, l'industriel français Pierre Manhès commence des essais avec un petit convertisseur Bessemer ordinaire de 50 kg, dans son usine de Vedène, puis aux usines d'Éguilles, près d'Avignon[1]. Il cherche à affiner une matte à 25 à 30 % de cuivre préalablement fondue dans un creuset. Mais comme Hollway, il ne parvient pas à affiner complètement la matte. L'oxydation des éléments indésirables se produit comme prévu, mais l'opération est vite perturbée par l'apparition du cuivre métallique[8]. En effet, la matte, qui est un composé ionique, est immiscible avec les scories, mais aussi avec le métal en fusion. Ce dernier, plus dense (ρcuivre ≈ 9), descend au fond du convertisseur[9] et colmate les tuyères :
« Au début de l’opération, le bain conservait sa fluidité, grâce au dégagement de chaleur produit par l’oxydation du fer et du soufre. Mais quand une quantité notable de cuivre était épurée, ce métal plus dense, se rassemblait au fond, et ne tardait pas à se figer en obstruant les tuyères, pendant qu’à la surface la réaction devenait tumultueuse, en amenant des projections de scories. On était, par suite, obligé de couler avant l'épuration complète, sous peine de voir le bain se prendre en masse[8]. »
— H. Moissan et L. Ouvrard, Le Nickel
Pierre Manhès brevète alors l'utilisation d'additifs[note 5] dont l'oxydation dégagerait suffisamment de chaleur pour éviter tout figeage. Finalement c'est le Français Paul David, alors ingénieur dans cette usine, qui, en 1880, suggère la solution. Il propose des tuyères horizontales, placées à une distance suffisante du fond du convertisseur, de telle sorte que le cuivre puisse se réunir au-dessous d'elles et que le vent souffle constamment dans la matte[6]. En 1881, leur convertisseur est à la fois techniquement opérationnel et rentable[L 3].
Pendant l'automne 1884, le procédé est adopté aux États-Unis, par la Parrot Silver and Copper Company, à Butte[P 1]. En 1885, A. J. Schumacher parvient à y réaliser un affinage complet dans une même cornue. Sa méthode est ensuite perfectionnée par C. O. Parsons et F. Klepetco à Great Falls dans le Montana. Enfin, Franklin Farrel, toujours aux Parrot Works, systématise le débouchage des tuyères par ringardage. La forme de la cornue y est perfectionnée et devient le standard jusqu'à ce que le convertisseur cylindrique la supplante[7].
La forme cylindrique
Vers 1883-1884, au moment de l'adoption du procédé aux États-Unis, les deux inventeurs français étudient une évolution de la forme du convertisseur, qui devient un cylindre d'axe horizontal[L 3]. L'alignement des tuyères sur une génératrice du cylindre fait qu'elles se situent toutes à la même immersion[6]. La forme permet aussi de limiter la hauteur du bain, ce qui simplifie la conduite du procédé car la pression nécessaire pour souffler l'air est plus faible, et la couche de cuivre qui stagne au fond est moins épaisse. De plus, il est facile de corriger la profondeur d'immersion des tuyères en pivotant plus ou moins le convertisseur. Il est aussi possible de couler la matte par une ouverture située à une extrémité, près de l'axe de rotation, et de vidanger les scories par une autre ouverture latérale, diamétralement opposée aux tuyères[note 6] - [L 4].
Le convertisseur cylindrique se généralise progressivement[note 7], sans toutefois faire disparaître rapidement les convertisseurs verticaux en forme de cornue[12] - [note 8]. Les deux types de convertisseurs deviennent de plus en plus gros, passant d'une capacité de 1 tonne à 8 tonnes en 1912[L 3], voire 15 tonnes pour les convertisseurs cylindriques en 1920[6].
- Convertisseur cylindrique, brevet de Pierre Manhès.
- Convertisseur Manhès-David dit « en barrique », reconnaissable à ses deux fonds bombés, d'une capacité de 7 tonnes.
- Convertisseur de type Great Falls en 1920. Ce compromis entre les formes en cornue et cylindrique a été exploité jusqu'au début des années 1980[12].
L'amélioration de Peirce et Smith
Les scories s'enrichissant en oxyde de fer pendant le soufflage, elles deviennent basiques et se combinent alors avec le revêtement réfractaire siliceux, qui est très acide[L 3]. Un revêtement basique ne serait pas attaqué et diminuerait donc le coût de production. L'adoption d'un revêtement inspiré de celui mis au point par Sidney Thomas et Percy Gilchrist en 1877[13] est suggérée par Hollway lors de ses derniers essais au début des années 1800[L 3]. Mais l'idée n'est pas testée, des problèmes fondamentaux liés au soufflage étant alors plus prioritaires que l'optimisation du réfractaire[1].
En 1890, un revêtement réfractaire basique est essayé sur un des convertisseurs Manhès-David de Parrot Smelter, à Butte, sous la direction de Herman A. Keller. Les essais ne débouchent pas sur un revêtement compatible avec une marche industrielle[L 6]. Puis Ralph Baggaley, toujours dans le Montana, parvient, après de nombreux essais, à industrialiser en 1906 un revêtement basique à la Pittsmont Smelter[note 9]… qui est abandonné en 1908 lorsqu'il quitte l'usine[7]. Pour autant, le Norvégien Knudsen réussit dès 1903 à utiliser un revêtement basique à la Sulitjelma gruber : il y réalise deux soufflages successifs, d'abord dans un petit convertisseur au revêtement basique, puis dans un deuxième convertisseur classique, au revêtement acide[L 6].
Enfin, en 1909[11] - [15], à la Baltimore Copper Company's Smelter, les Américains William H. Peirce et Elias A. C. Smith parviennent à traiter les principaux inconvénients des réfractaires basiques. Ceux-ci sont en effet plus fragiles, et surtout se dilatent et dissipent plus la chaleur que les réfractaires acides[L 7]. En mettant au point un maçonnage adapté au convertisseur cylindrique et en augmentant la quantité de métal enfournée, ils résolvent les derniers problèmes[L 8] - [note 10].
Le convertisseur de Peirce et Smith s'avère beaucoup plus avantageux que celui de Manhès et David. Le réfractaire basique, qui ne réagit pas avec les scories, dure beaucoup plus longtemps. Cette amélioration permet de s'affranchir des manutentions dues au remplacement des convertisseurs, d'éviter la construction d'installations de maçonnage[L 9] et de convertisseurs de rechange (deux convertisseurs en maçonnage pour un en service en 1897 à l'Anaconda Copper[16]), et de limiter les risques de percées dues à un mauvais contrôle de l'usure du réfractaire[P 3]. La couche de réfractaire peut alors être plus fine, ce qui augmente la capacité du convertisseur. Celle-ci ne dépend pas de l'usure du réfractaire, ce qui simplifie la gestion des flux de métal en fusion dans l'usine[L 10].
Si la matière utilisée pour préparer le réfractaire acide contient du cuivre, voire de l'argent ou de l'or (fréquemment associés au cuivre dans les quartz aurifères[17]), ces métaux rejoignent la matte au fur et à mesure de l'ablation du revêtement. Au vu de sa destruction rapide, l'avantage économique d'un réfractaire acide ne se conçoit donc que si sa consommation apporte de la valeur au procédé[L 11]. Cette situation est cependant assez rare et, même dans ce contexte, une silice riche en métaux précieux peut être économiquement valorisée par d'autres moyens. Ainsi, en 1921, le réfractaire basique est considéré comme « le principal élément de la réduction des coûts dans la pyrométallurgie des minerais de cuivre[14] ». Dans certains cas, une baisse du coût de la conversion, de 15–20 dollars à 4–5 dollars, a été rapportée[18].
- Convertisseur Manhès-David : le maçonnage est grossier et la quantité de réfractaire est maximisée.
- Brevet de Peirce et Smith[15], avec des jeux de dilatation et une ouverture latérale pour un brûleur de réchauffage.
Le procédé
La matte
Le procédé ne justifie son intérêt économique qu'avec des qualités précises de matte, appelées parfois « matte bronze[6] ». En effet, si l'oxydation des éléments indésirables (essentiellement le fer) est exothermique, il est nécessaire d'apporter en proportion de la silice afin de limiter la viscosité des scories. Or la silice est enfournée froide et les scories n'ont pas de valeur[note 11], ces scories contenant de plus toujours un peu (0,5 % au début du XXIe siècle[9]) de cuivre[L 12].
Pour un revêtement acide, la matte contient couramment 40 à 50 % de cuivre (soit respectivement 32 à 22 % de fer), mais il est possible, dans certains cas, de descendre jusqu'à 32 % de cuivre tout en restant rentable[L 12]. Mais dans ce cas, la teneur en fer ne doit pas être trop élevée, pour éviter une consommation trop rapide du réfractaire[L 11].
Si, au début XXe siècle aux États-Unis, une matte est dite pauvre quand elle contient 45 à 50 % de cuivre[P 4], en Europe, « des mattes contenant de 15 à 35 % de cuivre y sont rentablement affinées au convertisseur[P 5] », même si cela complique les opérations. Le soufflage est alors bien plus long et l'opération se déroule en plusieurs étapes. Un revêtement acide, dans ces conditions, ne dure que de 7 à 10 soufflages[P 5]. Un revêtement basique s'avère beaucoup plus adapté : comme il n'est pas attaqué par les scories, il peut affiner des mattes très pauvres et le soufflage peut être optimisé pour diminuer la teneur en cuivre des scories[19]. Depuis la fin du XXe siècle, la conversion d'une matte de 50 à 60 % de cuivre avec un convertisseur basique Peirce-Smith est courante[9].
Il est aussi possible d'affiner un « cuivre noir », contenant plus de 70 % de cuivre, du fer et un peu de soufre[9]. Il est issu du recyclage de déchets cuivreux ou d'un traitement direct du minerai[20]. Un tel composé métallique peut être utilisé pur ou mélangé avec la matte à divers stade du soufflage[21].
Le convertisseur
Quelques différences apparaissent selon que le revêtement réfractaire est acide (silice liée par de l'argile[L 11]) ou basique (à base de magnésite[L 13])[L 4].
Au début du XXe siècle, un convertisseur d'une capacité de 7 tonnes utilise 16 tonnes de réfractaire acide qui durent de 6 à 9 soufflages. La conception du convertisseur prend en compte les interventions fréquentes : il peut s'ouvrir en deux (partie inférieure et supérieure) pour que la régénération de la couche d'usure, en sable damé, ne dure qu'une heure et demie[L 14].
À la même époque, le revêtement basique, beaucoup plus performant, permet de réaliser des convertisseurs d'une capacité d'une quarantaine de tonnes, dont le revêtement en briques magnésiennes tient jusqu'à 75 coulées[note 9]. Ce réfractaire, qui ne réagit pas avec les scories, ne génère pas de fondant acide : s'il ne se combine pas à la silice, les scories évoluent vers une masse infusible d'oxydes de fer[L 8]. Manhès[1], Baggaley[22] et d'autres, qui avaient essayé d'introduire du sable par les tuyères, avaient échoué car celui-ci n'a pas le temps de réagir avec les scories[7] - [note 4]. La difficulté est contournée en enfournant, avant la matte en fusion, quelques tonnes de sable[L 8].
Acide[L 15] - [17] (début du XXe siècle) |
Basique[L 14] - [H 4] (début du XXe siècle) |
Basique[E 3] - [11] (début du XXIe siècle) | |
---|---|---|---|
Capacité (tonnes de matte) | 7 (moyenne) | 35 à 45 | 220 |
Nombre de tuyères | 14 | 27 | 60 |
Épaisseur de réfractaire (cm) | 55 à 70 | 25 | 50 |
Durée de vie du réfractaire (tonnes de matte) |
42 à 63 | 2 000 à 3 000 | 60 000 à 90 000 (tuyères uniquement) |
Inadapté à la production en masse, le revêtement acide disparait progressivement au début du XXe siècle. En 1912, aux États-Unis, 80 % de l'affinage du cuivre est réalisé dans des convertisseurs revêtus de réfractaire basique, dont beaucoup ont été conçus pour un réfractaire acide[7]. En 1925, le revêtement acide a disparu : « chaque livre de cuivre affinée dans le monde l'est dans un convertisseur revêtu de réfractaire basique[23] ».
Au début du XXIe siècle, une usine moderne dispose de 2 à 5 convertisseurs, d'une capacité unitaire de 100 à 250 tonnes[E 4], transformant chacun 600 à 1 000 tonnes de matte en 500 à 900 tonnes de cuivre par jour[E 5]. La durée de vie d'un convertisseur Peirce-Smith moderne se situe entre 50 000 et 90 000 tonnes (soit, en 1984, 100 à 200 jours[11]). Le maçonnage dure une semaine. Les réfractaires les plus performants sont les briques en magnésie liée au chrome[E 6]. En 2010, avec 250 convertisseurs opérationnels dans le monde, les convertisseurs cylindriques Peirce-Smith assurent 90 % de l'affinage des mattes cuivreuses[E 7].
Déroulement d'un soufflage
Le principe fondamental du convertisseur Manhès-David est calqué sur celui de Bessemer. Il consiste à se débarrasser de tous les éléments indésirables plus oxydables que le cuivre. Le soufflage oxyde successivement le fer et le soufre, et doit être stoppé quand tous les éléments indésirables ont été oxydés[L 16].
Les réactions d'oxydation doivent être suffisamment exothermiques[note 12] pour que la température reste supérieure à celle du métal en fusion. Mais il faut également que les scories soient suffisamment fluides. Pour cela, il faut qu'elles se combinent à un fondant, la silice. Celle-ci est apportée soit par le revêtement réfractaire du convertisseur (réfractaire acide)[L 3], soit par un enfournement préalable d'une charge de sable dont le poids atteint, approximativement, 10 % du poids de la matte (réfractaire basique)[L 17].
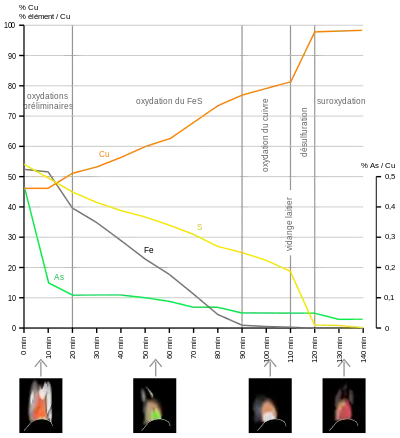
La matte à affiner est versée entre 900 °C[H 3] et 1 200 °C[E 5]. Suit alors une brève étape, caractérisée par une flamme rouge avec un épais panache de fumée blanche, où sont oxydés les constituants secondaires (carbone, arsenic, etc.)[L 18].
Lorsque la flamme devient verte, l'oxydation ne concerne plus que le sulfure de fer(II) (FeS)[note 14], qui se prolonge jusqu'à l'épuisement du fer. Alors que le fer s'oxyde en oxyde de fer(II) (FeO) et passe dans les scories, le soufre s'oxyde en dioxyde de soufre (SO2), qui sort du réacteur sous forme gazeuse[L 18] :
FeS + 3 O → FeO + SO2
L'oxydation du fer génère l'essentiel de la chaleur et des scories produites pendant l'affinage[L 18]. Pendant tout ce temps, la température doit rester supérieure à 1 208 °C[note 15] pour que la silice puisse se combiner au FeO[H 3] :
2 FeO + SiO2 → Fe2SiO4 si T > 1 208 °C[note 4]
Lorsque tout le fer a été oxydé, la flamme devient blanche avec une teinte bleue : elle correspond à l'oxydation du cuivre en présence de scories. En effet, à haute température, l'oxydation produit essentiellement des silicates de cuivre (Cu4SiO4[H 7]) au lieu de réagir avec le soufre. On vidange donc les scories et on ajoute une charge de déchets cuivreux à recycler afin de refroidir la charge[L 18]. À ce stade, le métal a atteint une teneur en cuivre d'environ 80 %. Il ne contient plus de fer, mais reste riche en soufre et en éléments difficilement oxydables : on appelle cet alliage intermédiaire « métal blanc »[9] ou « matte blanche[26] ».
Puis le soufflage reprend pour oxyder le reste du soufre[H 7] :
Cu2S + 3 O → Cu2O + SO2
Cu2S + 2 Cu2O → 6 Cu + SO2
Pendant cette dernière phase, la flamme devient plus petite, claire et peu éclairante, avec une teinte rougeâtre. La fin du soufflage ne se traduisant pas par une modification de la flamme, il est décidé à partir de prises d'échantillons[L 18]. Pour autant, l'oxydation du cuivre à la fin du soufflage est importante : alors que les scories vidangées à l'issue du premier soufflage ne contiennent que 2 % de cuivre, les scories finales peuvent en contenir plus de 20 %. Même si elles sont alors avantageusement recyclé en amont de la filière, il vaut mieux limiter leur quantité en multipliant, si nécessaire, les vidanges[L 19] - [H 8] ou en visant une quantité maximale de cuivre en fin de soufflage par des appoints réguliers de matte[L 17].
Pendant tout le soufflage, le convertisseur est de plus en plus incliné pour éloigner les tuyères du fond. Celles-ci ayant quand même tendance à se colmater, il est nécessaire de les déboucher régulièrement au moyen d'une barre en acier[L 18]. Le soufflage est donc une opération exigeante et, si on est en réfractaire acide, la gestion du revêtement s'ajoute à celle du métal en fusion. « Peut-être, qu'aucune opération métallurgique ne requiert un personnel plus expérimenté, et une surveillance plus attentive et globale, que le procédé de conversion[P 6]. »
Le métal issu du convertisseur contient plus de 99 % de cuivre[L 20]. Il est appelé « blister »[9] (c'est-à-dire « cloque ») à cause des bulles de SO2 dissous qui s'y forment quand il se solidifie[E 4] - [P 7].
Évolutions
Soufflage à l'air enrichi à l'oxygène
En 1895, Carl von Linde réussit la liquéfaction de l'air. Indépendamment de cette démarche, Georges Claude met en service en 1905 un procédé industriel de liquéfaction de l'air. Leurs brevets autorisent la production industrielle, et surtout économique, de grandes quantités d'oxygène et d'azote liquide. Des entreprises naissent rapidement (Claude fonde Air liquide, alors que von Linde crée Linde AG et Praxair). Dans les années 1920, les sidérurgistes expériment l'enrichissement en oxygène de l'air soufflé dans les convertisseurs. Après la seconde Guerre mondiale, la méthode se généralise, jusqu'à la mise au point du convertisseur à l'oxygène, qui supplante rapidement les convertisseurs Thomas et Martin-Siemens[27].
L'enrichissement à l'oxygène avec un convertisseur Peirce-Smith est essayé plus tardivement, la première fois en 1966 à la Saganoseki Smelter, au Japon. L'addition d'oxygène facilite le bouclage énergétique du soufflage et rend le procédé plus flexible. La pratique se répand au début des années 1970. Pour autant, contrairement à la sidérurgie, aucun convertisseur à l'oxygène pur n'est mis au point[28] même si la teneur en oxygène peut exceptionnellement atteindre 60 %[29]. En effet, de très hauts niveaux d'enrichissement sont généralement improductifs : au-delà de 25 %, la durée de vie des réfractaires peut baisser[E 6]. Dans ce cas, une injection périphérique d'azote aux tuyères permet de les ménager[K 1]. Un fort enrichissement ne se justifie en fait qu'en début de soufflage, quand l'utilisation de l'oxygène est maximale (les tuyères sont alors profondes et l'abondance d'éléments oxydables protège le cuivre). En 2010, la teneur en O2 atteint couramment 30 %[E 8] et la moitié des convertisseurs est opérée à plus de 29 % de O2[E 9].
L'injection d'oxygène accélère significativement les réactions chimiques. En début de soufflage, utiliser un air enrichi à 25-30 % d'O2 permet un gain de temps de 15 à 30 %. Vers le milieu du soufflage, l'enrichissement est progressivement arrêté. Sur l'ensemble de l'opération, la chaleur se dissipe moins et il est possible de fondre des additions cuivreuses (scories des fours à anodes, de scories de conversion, déchets cuivreux, etc.). Selon leur qualité, on compte 3 à 8 tonnes d'additions froides par tonne d'oxygène ajoutée[30]. Pour éviter les surchauffes au nez des tuyères, on injecte aussi par les tuyères des minerais de cuivre concentrés en poudre[H 9] - [9]. En 2010, 10 à 15 % du blister est issu d'additions froides[9].
Enfin, l'enrichissement du vent se traduit par des fumées à la fois moins abondantes et plus riches en SO2, ce qui facilite leur traitement. Avec 25,1 % d'oxygène, la teneur en SO2 des fumées d'un convertisseur avec une captation de fumées de type Hoboken passe de 8 à 10 %[30].
Extension à la pyrométallurgie du nickel
Les pyrites cuivreuses contiennent souvent du nickel[31]. Les procédés d'extraction sont semblables à ceux du cuivre, et permettent d'obtenir une matte contenant environ 20 % de cuivre et 25 % de nickel[32]. Ainsi « M. Manhès a aussitôt cherché à appliquer son procédé au traitement des minerais sulfurés et arséniés de nickel, et réussit à obtenir de bons résultats, au moyen de quelques modifications[33]. »
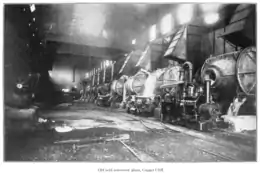
En effet, au début du soufflage, une matte contenant du nickel s'oxyde comme une matte cuivreuse. Mais lorsqu'il reste dans la matte moins de 1 à 0,5 % de fer, le nickel commence à s’oxyder énergiquement, aussi vite que le soufre[note 16]. Par ailleurs, l'oxydation du nickel étant peu exothermique, il n'est pas possible de finir le soufflage. On l'interrompt donc au stade de la matte blanche, qui ne contient alors presque plus de fer, mais reste riche en soufre. Si l'affinage d'une matte de nickel ne peut pas être aussi complet que celui d'une matte cuivreuse, le convertisseur reste pertinent : en 1896, Henri Moissan constate qu'il permet « en une seule opération, [de] passer d’une matte première à 16 % de nickel à une matte riche contenant 70 %, et cela en quelques heures, en évitant toute une série de grillages suivis de fusions, si longue et si dispendieuse. » La matte est facile à traiter, et les scories, qui contiennent alors 5 % de nickel, sont avantageusement recyclées[33].
Au début du XXIe siècle, l'efficacité du convertisseur du Peirce-Smith fait qu'il est universellement adopté dans l'affinage de la matte issue des minerais sulfureux de nickel (pentlandite). La teneur en nickel de la matte brute varie suivant les procédés : environ 30 % pour les mattes issues du four électrique, 40 % pour celles produites par fusion flash[K 2]. On bascule le convertisseur, ou on injecte de l'azote, dès que le fer est suffisamment oxydé. Généralement, la matte affinée contient 40 à 70 % de nickel, et 20 % de soufre. La teneur finale en fer dépend des procédés avals : 1 à 4 % si on traite par lixiviation, 0,5 % si on traite par solidification lente ou électrolyse. Les scories issues du convertisseur sont presque systématiquement envoyées dans un four électrique qui les maintient en fusion, afin de décanter toutes les gouttes de métal en fusion qu'elles contiennent car l'agitation importante du bain dans le convertisseur ne permet pas une séparation parfaite entre scorie et matte[K 3]. On ne recycle les scories que si elles contiennent plus de 0,6 % de nickel[K 4].
La température de travail, 1 400 °C, est plus haute que pour le cuivre[K 4]. Le nickel se combine avec la silice pour former une scorie très pâteuse, qui colmate les tuyères. Le ringardage ne doit donc jamais s'interrompre, sinon tout est bouché en moins d'une minute[35]. En 2011, l'injection d'oxygène se généralise pour les mêmes raisons qu'avec la production de cuivre[K 5].
En 2011, le procédé Manhès-David, en participant au traitement des minerais sulfureux de nickel, intervient dans 60 % de l'extraction du nickel[K 6]. Quelques procédés consistent même à ajouter du soufre dans le ferronickel brut issu des latérites, afin d'en faire une matte compatible avec le procédé Manhès-David[K 7]. Mais, comme pour le cuivre, le convertisseur est pénalisé par ses émissions de fumées polluantes[K 8]. Ainsi, des procédés alternatifs d'affinage du nickel ont été développés. Par exemple, une fusion flash suffisamment oxydante peut donner directement une matte blanche. L'affinage en continu est aussi moins polluant que le convertisseur[K 3].
Contextes
Impact environnemental
Avant même l'invention du procédé Manhès-David, le voisinage supportait mal les pluies acides dues au traitement des minerais de cuivre riches en soufre : les industriels américains qualifient alors de smoke farming (« agriculture des fumées »), l'activité des agriculteurs consistant à leur intenter des procès[note 17]. Le traitement des fumées n'est alors guère pratiqué : « Plutôt que de subir un tel racket, les fondeurs trouvaient plus économique de, soit acheter les fermes voisines, soit les cultiver eux-mêmes, ou de les louer en se couvrant par une clause relative aux fumées[19]. »
Au début du XXe siècle, l'apparition de grands complexes métallurgiques rend le traitement des fumées à la fois nécessaire et économiquement possible. Le procédé Manhès-David s'avère aussi polluant que le grillage et la fusion du minerai de cuivre, qui génèrent les mêmes fumées sulfureuses[37] et chargées d'oxydes et de sulfate de zinc, de plomb, d'arsenic, etc. Toutes les fumées sont alors collectées et cheminent dans des carneaux, parfois longs de plusieurs kilomètres, dans lesquels les particules se déposent. La cheminée des usines atteint quelquefois des records de hauteur. Cela s'avérant encore insuffisant, les premiers filtres à manches et électrofiltres sont alors industrialisés[19].
- Plan de l'usine de Washoe, de l'Anaconda Copper en 1916. Les ateliers sont organisés autour des carneaux de fumées (en vert), qui convergent vers l'Anaconda Smelter Stack.
- En 1919, l'Anaconda Smelter Stack (178,3 m), supplante la cheminée de l'Asarco (174 m), une autre fonderie de cuivre, comme plus haute construction du monde en maçonnerie. Les fumées passent avant dans des filtres électrostatiques.
- L'Inco Superstack (380 m), construite en 1974, est, en 2015, la deuxième plus haute cheminée du monde.
À cause des progrès réalisés dans le traitement des fumées, son remplacement par une cheminée plus basse est envisagé.
La contrainte environnementale se durcit ensuite tout au long du xxe siècle. Des investissements importants s'imposent pour, à la fois, satisfaire aux normes et rester compétitif. Aux États-Unis, entre 1975 et 1987, la capacité de fusion a diminué de 36 %. En Europe, en 2001, 99 % du soufre est retraité[37]. L'obtention d'un tel résultat représente un quart des coûts de transformation du minerai en cuivre[38]. Parmi les outils utilisés, « le convertisseur reste le principal problème environnemental dans les fonderies de cuivre ». Il est en effet difficile à étancher, et son fonctionnement intermittent perturbe les installations de traitement des fumées[E 10].
Le traitement des fumées de convertisseur consiste généralement à un dépoussiérage, puis d'une transformation du dioxyde de soufre en acide sulfurique. Les étapes du traitement consistent alors en, successivement[E 11] :
- un dépoussiérage, par des électrofiltres ;
- un refroidissement, par récupération de chaleur dans une chaudière de récupération ;
- un lavage par aspersion d'un brouillard d'eau, qui absorbe les poussières fines ainsi que les gaz solubles (fluorures, chlorures, etc.) ;
- un réchauffage qui précède une oxydation catalytique du SO2 en SO3 ;
- la production d'acide sulfurique H2SO4, par hydratation du SO3.
Une usine produit, selon la teneur en soufre de la matte, de 2,5 à 4 tonnes d'acide sulfurique par tonne de cuivre produite[9]. Pour un traitement économique[note 18], la fumée captée doit être la plus riche possible en SO2[note 19] - [39]. En général, le procédé est géré pour que la concentration en SO2 de la fumée entrant dans l'unité de production d'acide ne soit jamais inférieure à 3 %[9] (la concentration en SO2 se situe entre 8 et 12 % à l'intérieur d'un convertisseur Peirce-Smith moderne). L'aspiration des fumées est un point délicat : trop puissante, elle dilue la fumée et la refroidit, ce qui génère des condensats corrosifs vis-à-vis des installations de traitement[E 13].
La contrainte environnementale a motivé beaucoup d'améliorations du convertisseur. Par exemple, le convertisseur Hoboken, développé dans les années 1930[39], dispose d'une aspiration fixe, donc étanche. La teneur SO2 des fumées dépasse alors 12 %[E 12]. Avec le captage des fumées, la conduite du procédé par l'observation des flammes devient une pratique complètement obsolète : la composition chimique de la fumée est analysée en permanence par des capteurs dédiés. Au-delà de ces améliorations, certains procédés alternatifs combinent la fusion et l'affinage dans un même réacteur, qui est directement inspiré du convertisseur, comme dans les procédés Noranda et Mitsubishi, développés à partir des années 1980[note 20]. L'objectif est à la fois d'avoir un procédé continu et d'éviter à la matte en fusion de voyager hors du réacteur[39]. Mais le remplacement est lent à cause de l'excellente efficacité chimique et opératoire du convertisseur Peirce-Smith[E 10].
- Unité de production d'acide sulfurique au pied de la cheminée de la fonderie de Copperhill, en 1939 aux États-Unis.
- Paysage entre Ducktown et Copperhill en 1939 : les fumées acides ont tué toute végétation, entraînant une érosion importante des sols.
- Unité de désulfuration de la fonderie de Timna, Israël (années 1960). On distingue deux amas de soufre.
- Le convertisseur Hoboken, un convertisseur Peirce-Smith conçu pour améliorer le captage des fumées.
Contexte technico-économique
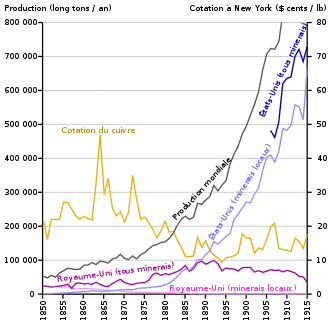
À la fin du XVIe siècle, la Grande-Bretagne produit 75 % du cuivre mondial[40], essentiellement issu des mines corniques[L 21]. Vers 1870, selon Paul Louis Weiss, elle en produit encore plus de la moitié, avec des minerais importés de toutes les parties du globe, principalement du Chili, d'Espagne et d'Allemagne. En effet, les procédés mis au point, comme le four à réverbère ou la flottation par moussage, sont tenus secrets et consolident le monopole britannique[40]. Mais à partir de cette date, l'expansion rapide de l'extraction du cuivre en Amérique du Nord enlève aux métallurgistes britanniques leur prépondérance. En 1873, les Américains du Nord deviennent les premiers producteurs de cuivre du monde[41]. En 1881, l'arrivée du chemin de fer à l'énorme gisement de Butte, donne aux compagnies américaines la domination mondiale de la production de cuivre[40].
Le procédé Manhès-David ne fait pas partie des améliorations britanniques sur le grillage et la fusion. Il complète une série d'innovations qui échappent à la Grande-Bretagne, comme le grillage sur sole tournante ou l'électrolyse, accélérant le basculement de la production vers le Nouveau Monde[L 22] :
« Satisfaire l'énorme demande actuelle en métal aurait été impossible avec les vieilles méthodes et les fours traditionnels. Le plus fort stimulus à l'adoption de ces procédés nouveaux ou modifiés a été le basculement des principaux centres de production, des plus vieux et conservateurs vers les nouveaux centres émergents de l'Ouest, où [alimentés] d'un flux toujours croissant — et presque illimité — d'approvisionnement en minerai disponible, et libérés de la nécessité de prendre en compte les investissements déjà consentis dans de vieilles usines, les hommes […] ont pu développer leurs idées avec originalité et énergie[L 23]. »
— Donald M. Levy, Modern copper smelting
Ce basculement sur les volumes s'accompagne d'une évolution similaire sur les prix qui enterre définitivement les vieux procédés. Le XIXe siècle est en effet marqué par une érosion continue du prix du cuivre : 160 £ la tonne sur la première décennie, puis 130 £, 101 £, 94 £ et 88 £ sur la période 1841-1850[42]. Bien que les secrets de la méthode galloise viennent d'être éventés par la chimie moderne[note 12], les fondeurs gallois parviennent à s'entendre pour maintenir les prix à ce niveau jusqu'au début des années 1870. De 1885 à 1887, le prix du cuivre atteint un bas historique, sous les 50 £ la tonne, malgré une forte demande attisée par les progrès de l'électricité et du téléphone[L 24]. Les progrès techniques adoptés aux États-Unis (filière haut fourneau - convertisseur - raffinage par électrolyse) permettent aux nouveaux mineurs américains, canadiens et australiens[note 21] de maintenir leur profits, même à ces cours[L 22].
La domination américaine va aussi se développer au détriment du Chili, pourtant doté de formidables gisements. En effet, la production de cuivre y baisse de moitié pendant la guerre du Pacifique (1879-1884), avant de s'interrompre presque complètement pendant la guerre civile de 1891[41] : les mineurs chiliens ne peuvent poursuivre leurs investissements. En Europe, la créativité des industriels[note 7], dont fait partie Pierre Manhès, ne peut compenser la rareté du minerai. Enfin, après l'échec du corner sur le cuivre de 1887, les industriels américains vont constituer plusieurs cartels qui, en générant une série de mouvements spéculatifs, vont déconnecter les cours du cuivre des coûts de production[43] - [L 24].
Généralisation et modernisation du convertisseur Peirce-Smith
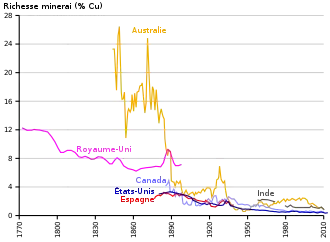
L'appellation Manhès-David disparait dans le milieu des années 1920, en même temps que le convertisseur à revêtement acide[23]. Le convertisseur Peirce-Smith qui le supplante ne présente pourtant pas de différence notable sur le procédé[note 10], mais il représente un tel progrès pour les fondeurs américains engagés dans une croissance capacitaire, que ceux-ci ne se réfèrent plus à Manhès et David. En outre, bien qu'ils reconnaissent volontiers la paternité de l'invention aux deux Français[44], ils ne voient aucun intérêt dans les améliorations postérieures proposées par David, comme le sélecteur. L'adoption du terme Peirce-Smith illustre le développement d'une filière typiquement américaine, fondée sur de nouveaux procédés et adaptée à la production de masse à partir de minerais plus pauvres[6] - [H 10].
Mais, contrairement à la sidérurgie qui a abandonné les procédés Bessemer et Thomas pendant la seconde moitié du XXe siècle, le convertisseur Peirce-Smith n'a pas été remplacé par un procédé plus performant : en 2010, il représente encore 90 % de l'affinage des mattes cuivreuses[E 7]. En effet, la sidérurgie a eu accès à des gisements de plus en plus riches au cours du XXe siècle, avec des teneurs en fer supérieure à 50 %[45]. À l'inverse, l'extraction du cuivre, s'est faite à partir de gisements de plus en plus pauvres, la teneur moyenne en cuivre du minerai passant de 3 % au début du XXe siècle[46] à 0,6 % au début du XXIe siècle[47] - [48]. Avec ces minerais, la pyrométallurgie ne représente maintenant plus que 10 % de l'énergie nécessaire à toute l'extraction du cuivre[49]. L'effort de recherche s'est alors concentré sur les étapes amont de prétraitement du minerai.
Pour autant, le convertisseur Peirce-Smith a évolué. Dans la seconde moitié du XXe siècle des recherches ont été menées pour épauler l'opérateur dans la conduite du soufflage[9]. Depuis, il n'est plus question de se fonder uniquement sur la couleur de la flamme pour déterminer l'avancement du soufflage. La composition de la fumée est analysée en permanence, la température est contrôlée par un pyromètre optique, installé dans une tuyère, sinon au bec du convertisseur[K 8]. Des machines automatiques réalisent le débouchage des tuyères[E 14].
Bien que les convertisseurs sont maintenant des outils géants, affinant souvent plus de 200 tonnes de matte à chaque soufflage, la modernisation de leur conduite les a rendu beaucoup plus flexibles. Par exemple, la silice enfournée peut être remplacée par du minerai concentré de cuivre, selon des quantités variant de quelques dizaines à plusieurs centaines de kilogrammes par tonne de matte. En modulant finement la teneur en oxygène du vent et en contrôlant le rapport FeO/SiO2 des scories, il est possible d'améliorer encore le rendement de l'opération, et de limiter les coûts de traitement des fumées et des scories. Ainsi, au début du XXIe siècle, à l'instar de beaucoup de procédés pyrométallurgiques, les convertisseurs Peirce-Smith évoluent essentiellement pour parfaire le procédé inventé par Pierre Manhès et Paul David[9].
Notes et références
Notes
- On relève aussi, en 1866, un brevet de William L. Raht relatif à l'utilisation d'un convertisseur Bessemer pour retirer le soufre, l'arsenic et l'antimoine présents dans des mattes diverses[3].
- Brevets anglais no 1131 du 21 mars 1878 et no 4549 du 9 novembre 1878[4] - [P 1].
- La silice (SiO2) du revêtement réfractaire est fortement acide, elle est donc absorbée par l'oxyde de fer(II) (FeO), qui est basique[5] - [P 2]. Hollway propose de contourner cette difficulté en enfournant une charge additionnelle de silice en même temps que le métal. Il propose aussi d'adopter un réfractaire basique[L 3].
- Le point de fusion du FeO est de 1 377 °C. Si le FeO ne se combine pas immédiatement avec la silice pour former de la fayalite (Fe2SiO4)[H 3], dont le point de fusion est de 1 208 °C, son oxydation continue et il se transforme alors en Fe3O4. Or le point de fusion du Fe3O4 est de 1 597 °C. Le Fe3O4 s'agglomère alors en une masse solide qui empêche le soufflage et ne peut être évacuée du convertisseur[E 1], si ce n'est par l'utilisation de fondants réducteurs, comme le spiegeleisen[H 4].
Une autre raison pour combiner le FeO avec le SiO2 vient du fait que des scories riches en oxydes de fer peuvent oxyder le Cu2S suivant la réaction : FeO(scories) + Cu2S(matte) → FeS(matte) + Cu2O(scories) Une telle réaction est indésirable car elle fait migrer le cuivre de la matte vers les scories. Pour cette raison, les métallurgistes évitent de produire des mattes à plus de 60 % de cuivre, même si les avantages à traiter une matte riche sont évidents[E 2]. - Pierre Manhès évoque le charbon de bois comme combustible, mais recommande plutôt le soufre en poudre injecté avec le vent[10].
- Dans la sidérurgie, on sépare l'acier des scories (appelées laitier) à la fin du soufflage : cela se fait aisément par un trou de coulée latéral qu'un basculement de la cornue, en fin de soufflage, amène sous le bain. L'acier s'y écoule d'abord, puis les scories qui surnagent sur le métal. Au contraire, dans l'affinage du cuivre, il faut vidanger régulièrement les scories avant le métal : un trou de coulée situé en partie haute du bain est donc préférable.
- Le premier convertisseur cylindrique a été essayé à Livourne en Italie, et est devenu industriel en 1891 à Lanteira en Espagne, puis est arrivé en Amérique du Nord, d'abord à la Vivian Plant de Grand Sudbury au Canada, puis à la Copper Queen Company aux États-Unis[11] - [H 5].
- Le modèle vertical présente l'avantage de mieux faire réagir l'air avec le bain en fusion, étant donné la plus grande hauteur de liquide traversée : l'oxydation est plus rapide. Les formes concaves du réacteur permettent un meilleur maintien du revêtement réfractaire, qui s'use aussi plus lentement et de manière plus uniforme. Par contre, la pression de l'air insufflé doit être importante, ce qui complique le contrôle de la réaction[L 5], rendant nécessaire, pour les mattes de moins de 25 % en cuivre, deux opérations successives[6].
- Le tout premier revêtement basique de R. Baggaley fonctionne du 7 octobre 1905 au 31 janvier 1906, produisant 480 tonnes de cuivre avant d'être remaçonné[7]. En 1921, W. A. Mueller cite une durée de vie record pour un réfractaire basique de 3 228 soufflages, soit 85 578 tonnes de matte affinées pendant 2 ans et demi[14].
- L'évolution du procédé calque l'évolution de la métallurgie du fer : le convertisseur Thomas, inventé en 1877, est également un convertisseur Bessemer doté d'un revêtement réfractaire basique. Mais, alors que les réactions chimiques dans le convertisseur Thomas diffèrent sensiblement de celles obtenues dans un convertisseur Bessemer, il n'existe pas de différences notables entre la chimie d'un convertisseur Manhès-Davis et celle d'un Peirce-Smith : tous deux opèrent en milieu acide.
- Pour des mattes très impures, la quantité de métal obtenue est si faible qu'après avoir vidangé les scories à mi-soufflage, on refait un appoint de matte brute et on reprend le soufflage. On a aussi recours à cette pratique pour les convertisseurs maçonnés avec un revêtement acide : lorsqu'ils sont encore peu usés, leur volume interne est insuffisant pour emmagasiner la chaleur nécessaire à l'achèvement du soufflage[L 10]
- Les procédés antérieurs d'affinage du cuivre, fondés sur des grillages successifs dans des fours à réverbère, sont plus longs et en plusieurs étapes, dispersant ainsi la chaleur dégagée par l'oxydation. C'est la rapidité des réactions, combinée avec la quantité de métal, qui permet de conserver la chaleur dans le réacteur chimique[L 5]. Ainsi, l'extraction du cuivre par la méthode galloise, qui a permis à la Grande-Bretagne d'acquérir une situation prépondérante dans la production de cuivre, consiste en 6 passages au four à réverbère. Le traitement du minerai dure de 10 à 15 jours et consomme 15 tonnes de charbon, alors que la fusion et le soufflage de la matte se font en 4 heures et ne nécessitent que 500 kg de coke[24].
- Ici, les teneurs en soufre, fer et arsenic ont été divisées par la teneur en cuivre, ce qui explique que ∑éléments ≥ 100 %. Il s'agit donc de la quantité relative de ces éléments par rapport au cuivre : par exemple, 50 % de fer signifie que le poids en fer est égal à la moitié du poids en cuivre. Cette représentation permet de mieux visualiser l'oxydation. Pour l'analyse chimique massique exacte, voir ici, pour l'analyse molaire, là[25] - [H 6].
- L'oxydation peut aussi se porter sur le Cu2S, en générant les mêmes produits[H 3] :
- Cu2S + 3 O → Cu2O + SO2
- Cu2O + FeS → Cu2S + FeO
- En 1914, Heinrich Oscar Hofman recommande une température supérieure à 1 270 °C[H 3]. Au début du XXIe siècle, pour ménager le réfractaire basique, on évite généralement de dépasser 1 250 °C. Les convertisseurs modernes peuvent recycler des déchets cuivreux ou souffler un vent enrichi en oxygène pour refroidir ou réchauffer le bain[E 5].
- Pour descendre à 5 % de soufre dans la matte, il faut oxyder 80 % du nickel[35].
- Pendant l'hiver 1904-1905, les dégâts dus aux émissions de dioxyde de soufre décident les fermiers de la vallée de Salt Lake de s'associer pour porter plainte devant l'United States District Court of Utah. Le jugement rendu interdit à toutes les fonderies locales traitant un minerai contenant plus de 10 % de soufre « de rejeter ledit soufre dans l'atmosphère, que ce soit sous forme d'acide ou autre, et de ne plus rejeter d'arsenic, sous quelque forme que ce soit », entraînant ainsi la fermeture immédiate des trois fonderies de cuivre concernées[36].
- L'acide sulfurique est un sous-produit peu rentable : en 2002, pour une tonne de cuivre vendue environ 1 100 $, une fonderie vend 2,7 t d'acide à environ 40 $[9].
- Les fumées du four à réverbère, procédé concurrent des convertisseurs, a une plus faible teneur en SO2. Cette faible concentration complique sa récupération, et est actuellement une des raisons principales de son abandon progressif[E 12].
- Le four à réverbère a suivi la même évolution, avec le développement des procédés flash d'Outokumpu et d'INCO.
- En 1885, l'Australie ne connait encore que la méthode galloise. La richesse des minerais et les faibles quantités extraites retardent l'adoption du procédé Manhès-David. Le nouveau procédé est pourtant reconnu très supérieur à l'ancien[24].
Références
- (en) Donald M. Levy, Modern Copper Smelting, C. Griffin & company, limited, (lire en ligne) (voir dans la bibliographie)
- p. 192
- p. 192-193
- p. 193
- p. 197
- p. 195
- p. 193-194
- p. 198 ; 202
- p. 200-203
- p. 214
- p. 212
- p. 200-202
- p. 203-204
- p. 198
- p. 202
- p. 197-198 ; 201
- p. 194
- p. 212-213
- p. 205-210
- p. 211
- p. 206
- p. 5
- p. 10
- p. 11
- p. 11-13
- (en) Marc E. Schlesinger, Matthew J. King, Kathryn C. Sole et William G. I. Davenport, Extractive Metallurgy of Copper, (voir dans la bibliographie)
- p. 127
- p. 68
- p. 130 ; 135
- p. 128
- p. 138
- p. 142
- p. 143
- p. 141
- p. 135
- p. 232
- p. 208-235
- p. 207
- p. 206
- p. 136-137
- (en) Edward Dyer Peters, Modern Copper Smelting, The Engineering and Mining Journal, , 7e éd. (lire en ligne)
- p. 528
- p. 536
- p. 561-562
- p. 538
- p. 549
- p. 551
- p. 226-227
- (en) Heinrich Oscar Hofman, Metallurgy of Copper, MacGraw Hill Book Company, (lire en ligne)
- p. 329
- p. 299
- p. 323
- p. 342
- p. 305
- p. 326-327
- p. 324
- p. 316-320
- p. 340
- p. 308
- (en) Frank K. Krundwell, Michael S. Moats, Venkoba Ramachandran, Timothy G. Robinson et William G. Davenport, Extractive Metallurgy of Nickel, Cobalt and Platinum Group Metals, Elsevier, , 610 p. (ISBN 978-0-08-096809-4, lire en ligne)
- p. 241
- p. 215
- p. 237-238
- p. 103-104
- p. 239
- p. 2 ; 15
- p. 104-105
- p. 242
- Autres références
- Weiss 1894, p. 191-193
- Adolf Ledebur (trad. Barbary de Langlade, revu et annoté par F. Valton), Manuel théorique et pratique de la métallurgie du fer, Tome I et Tome II, t. 2, Librairie polytechnique Baudry et Cie éditeur, [détail des éditions], p. 472
- (en) William L. Raht, « Improvement in treating metalliferous ores (patent US 57376 A) », USPTO,
- (en) John Hollway, « Production of sulphur, copper matte, etc. from pyrites (patent US 234129 A) », USPTO,
- (en) Walter MacFarlane, The principles and practice of iron and steel manufacture, Longmans, Green, and Co, , 5e éd. (lire en ligne), p. 93
- Jannettaz, Douglas et David 1920
- Southwick 2008
- Moissan et Ouvrard 1896, p. 71-73
- Pierre Blazy et El-Aid Jdid, « Pyrométallurgie et électroraffinage du cuivre - Pyrométallurgie », dans Techniques de l'ingénieur, Éditions techniques de l'ingénieur (lire en ligne) (voir dans la bibliographie).
- (en) Pierre Manhès, « Process of treating copper matte (patent US 470384 A) », USPTO,
- (en) Alejandro Alberto Bustos, « Injection phenomena and heat transfer in copper converters » [PDF],
- (en) Adalbert Lossin, « Copper », dans Ullmann's Encyclopedia of Industrial Chemistry, Wiley-VCH, (DOI 10.1002/14356007.a07_471, lire en ligne), p. 32
- (en) Hermann Wedding (trad. de l'allemand par William B. Phillips et Ernst Prochaska), Wedding's basic Bessemer process [« Basische Bessemer - oder Thomas-Process »], New York Scientific Publishing Company, , 224 p. (lire en ligne), p. 21-22 ; 30-32
- (en) W. A. Mueller, « Progressive Steps In the Metallurgy of Copper », Ohio State University, College of Engineering,
- (en) William H. Peirce et Elias A. Cappelen Smith, « Method of and converter vessel for bessemerizing copper matte (patent US 942346 A) »
- (en) Catalogue no. 1, presented by the Anaconda Copper Mining Co., foundry department, manufacturers of mining, milling, concentrating and smelting machinery, standard Publishing Co., (lire en ligne)
- (en) « Analysis of Jawbone Flats Mine Dump Samples », Western Oregon University,
- (en) Kenneth O. Bjork, Saga in Steel and Concrete, Norwegian-American Historical Association, , 504 p. (lire en ligne), p. 249-250
- (en) William Herbert Dennis, Metallurgy - 1863-1963, , 342 p. (ISBN 978-0-202-36361-5, lire en ligne), p. 66-70
- (en) « Black copper definition », Merriam-Webster,
- Metallurgie Hoboken-Overpelt, « Procédé pour extraire des métaux non-ferreux de déchets ferrés (Brevet EP 0 053 406 A1) », Office européen des brevets,
- (en) Ralph Baggaley, « Copper-refining furnace (patent US 846891 A) », USPTO,
- (en) « United Verde Copper Co. v. Peirce-Smith Converter Co. », Circuit Court of Appeals, Third Circuit.,
- (en) Clement Van de Velde, « The treatment of copper ores by the Manhès Process », Minutes of proceedings of the engineering society of New South Wales, Gustav Fischer, vol. 1, , p. 21-26 (lire en ligne)
- Mathewson 1907
- M. P. L. Burthe, « Notice sur le sélecteur Paul David », Annales des Mines, Mines ParisTech, 9e série, vol. 13, , p. 621-643 (lire en ligne)
- Olivier C. A. Bisanti, « Un siècle d'oxygène en sidérurgie », Soleil d'acier,
- (en) George Kachaniwsky et Chris Newman, Proceedings of the International Symposium on the Impact of Oxygen on the Productivity of non-ferrous metallurgical processes, vol. 2 : Proceedings of the Metallurgical Society of the Canadian Institute of Mining and Metallurgy, Pergamon Press, (ISBN 0-08-035767-9, lire en ligne), p. 25
- « Injection d'Oxygène dans les convertisseurs Cu/Ni », Air liquide,
- (en) Charles E. Baukal, Jr., Oxygen-Enhanced Combustion, (ISBN 0-8493-1695-2, lire en ligne), p. 210
- Moissan et Ouvrard 1896, p. 65
- Moissan et Ouvrard 1896, p. 69
- Moissan et Ouvrard 1896, p. 74
- (en) Arthur Philemon Coleman, The nickel industry; with special reference to the Sudbury region, Ontario, Ottawa Governement Printing Bureau, (lire en ligne), p. 143-144
- (en) Hiram W. Hixon, Notes on lead and copper smelting and copper converting, Hill Publishing Company, (lire en ligne), p. 102-110
- (en) Leonard J. Arrington et Gary B. Hansen, The Richest Hole on Earth : The history of the Bingham copper mine, King Hendricks, (lire en ligne [PDF]), p. 19
- « Document de référence sur les meilleures techniques disponibles : Transformation des métaux ferreux » [PDF], Commission européenne,
- Pierre Blazy et El-Aid Jdid, « Cuivre : ressources, procédés et produits », dans Techniques de l'ingénieur, Éditions techniques de l'ingénieur (lire en ligne), § Pyrométallurgie
- (en) U.S. Congress, Office of Technology Assessment (préf. John H. Gibbons), Copper : Technology & Competitiveness, (lire en ligne), chap. 8 (« Environmental Aspects of Copper Production »)
- (en) Copper : Technology and competitiveness, Congress of the United States, (lire en ligne [PDF]), chap. 6 (« Copper Production Technology »), p. 104
- Weiss 1894, p. 8
- (en) Harry Foster Bain et Thomas Thornton Read, Ores and Industry in South America, Arno Press, , 381 p., p. 217
- (en) Frederick Hobart, « Gold and Silver », The Engineering and Mining Journal, Hill Publishing Company, vol. 101, no 2, , p. 47 (lire en ligne)
- Douglas 1920, p. 558
- (en) Gavin M. Mudd, « The “Limits to Growth” and ‘Finite’ Mineral Resources : Re-visiting the Assumptions and Drinking From That Half-Capacity Glass », Auckland, New Zealand, 4th International Conference on Sustainability Engineering & Science: Transitions to Sustainability, , p. 5
- (en) Daniel Lederman et William F. Maloney, Natural Resources, Neither Curse nor Destiny, World Bank Publications, (ISBN 0-8213-6545-2 et 978-0-8213-6545-8, lire en ligne), p. 190
- (en) Lindsay Newland Bowker et David M. Chambers, « The risk, public liability, & economics of tailings storage facility failures », , p. 5
- Éric Drezet, « Épuisement des ressources naturelles », EcoInfo (CNRS),
- Éric Drezet, « L’énergie des métaux », EcoInfo (CNRS),
Voir aussi
Bibliographie
- (en) Donald M. Levy, Modern Copper Smelting, C. Griffin & company, limited, (lire en ligne)
- (en) Marc E. Schlesinger, Matthew J. King, Kathryn C. Sole et William G. I. Davenport, Extractive Metallurgy of Copper, Elsevier, , 5e éd., 455 p. (ISBN 978-0-08-096789-9, lire en ligne)
- Paul Louis Weiss, Le Cuivre : Origine - Gisements - Propriétés - Métallurgie - Applications - Alliages, J.-B. Baillière et fils, , 344 p. (ASIN B0019TU3SK, lire en ligne)
- (prénom inconnu) Douglas, « L'aluminium et les produits nouveaux obtenus par le moyen de l'électricité », Bulletin de la Société de l'Industrie Minérale, 3e série, t. XV, , p. 558-560 (lire en ligne)
- Paul Jannettaz, (prénom inconnu) Douglas et Paul David, « La bessemérisation des mattes cuivreuses », Bulletin de la Société de l'Industrie Minérale, 3e série, t. XV, , p. 560-573 (lire en ligne)
- (en) Larry M. Southwick, « William Peirce and E.A. Cappelen Smith and Their Amazing Copper Converting Machine », JOM, The Mineral, Metals & Materials Society (TMS), vol. 60, no 10, (lire en ligne)
- Pierre Blazy et El-Aid Jdid, « Pyrométallurgie et électroraffinage du cuivre - Pyrométallurgie », dans Techniques de l'ingénieur, Éditions techniques de l'ingénieur, (lire en ligne)
- (en) E. P. Mathewson, « Relative Elimination of Iron, Sulphur and Arsenic in Bessemerizing Copper-Mattes », Transactions of the American Institute of Mining Engineers, , p. 154-161 (lire en ligne)
- Henri Moissan et Léon Victor René Ouvrard, Le Nickel, Gauthier-Villars et fils, Masson et Cie, (lire en ligne)