Fusion flash
La fusion flash est un procédé d'extraction pyrométallurgique de métaux non ferreux, consistant à simultanément oxyder et fondre les métaux contenus dans un minerai sulfureux, comme la chalcopyrite. Le procédé a été inventé par l'entreprise finlandaise Outokumpu et utilisé à partir de 1949 pour l'extraction du cuivre. Le procédé a été depuis adapté à l'extraction du nickel et du plomb. Au début du XXIe siècle, la fusion flash intervient dans 50 % de la production mondiale de cuivre, 30 % de la production de nickel[1] et 10 % de la production de plomb[2].
.svg.png.webp)
Histoire
Fin du XIXe siècle : premiers essais
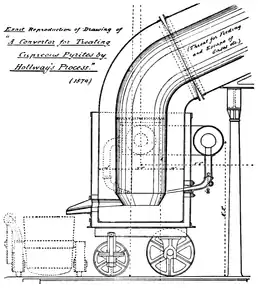
L'idée d'oxyder le soufre contenu dans les minerais sulfureux de cuivre est ancienne. Dans les années 1870, le métallurgiste anglais John Hollway expérimente la fusion et l'affinage du cuivre au moyen d'un convertisseur inspiré du procédé Bessemer. Il propose le sulfure de fer comme combustible, son oxydation générant du SO2 et un laitier de FeO. L'oxydation n'est cependant pas complète : Hollway prend garde de toujours disposer d'un excès de soufre dans le bain, afin d'éviter l'oxydation du cuivre, mais aussi des métaux plus précieux, comme le nickel, l'argent ou l'or[3].
Hollway envisage donc la production d'une matte blanche, c'est-à-dire un mélange de cuivre et de soufre. Il n'envisage pas de pousser l'affinage au-delà, en retirant tout le soufre[4]. Il entame alors une série d'expérimentations poussées dans le milieu des années 1870 à Penistone, en Angleterre[5], qui font de lui le pionnier des tentatives de fusion et d'affinage des pyrites cuivreuses en une seule étape[6]. Malgré sa persévérance, Hollway échoue à mettre au point un procédé industriellement utilisable :
« En cette année [1878], Hollway suggéra et expérimenta le principe qu'il avait relevé, posant les bases de l'affinage des pyrites et de leur conversion actuelle. L'air était soufflé au travers de pyrites de Rio Tinto dans un convertisseur Bessemer ordinaire, et l'expérience fut un succès remarquable. Mais l'appareil était cependant inadapté, et le procédé fonctionnait de manière très intermittente, et de grandes quantités de laitier était produites, qui devaient être vidangé régulièrement, pendant que la position des tuyères de ce convertisseur s'avérait insatisfaisante. […]
Dans la forme finale de l'appareil de Hollway pour la fusion des pyrites, du minerai au métal, une introduction de fondant siliceux pour l'oxyde de fer, combinée avec l'utilisation d'un réfractaire basique, avait pour but de résoudre des difficultés liées à l'attaque du revêtement réfractaire siliceux[7]. »
— Donald M. Levy, Modern copper smelting
Cependant, ne cachant rien de ses échecs, et publiant des brevets sans lendemain[note 1], Hollway communique de manière détaillée ses essais et leurs résultats. Ainsi, lorsque Pierre Manhès et Paul David mettent au point le procédé Manhès-David, leur invention bénéficie immédiatement de l'expérience constituée par les essais de Hollway. Mais leur procédé se limite à l'affinage pneumatique d'une matte préalablement fondue[5].
Première moitié du XXe siècle : recherches ponctuelles
En 1898, le métallurgiste américain Edward Dyer Peters calcule que 60 % du coût de production du cuivre correspond à la consommation de combustible. Et il n'échappe alors à aucun métallurgiste que ce combustible sert à ôter le fer et le soufre combinés avec le cuivre. Or ces éléments pourraient être eux-mêmes des combustibles utiles. En particulier, le grillage des minerais est une opération de désulfuration coûteuse en combustible[8].
L'utilisation d'un haut fourneau pour la fusion des pyrites en cuivre est testée dès 1878. Le coke amorce la combustion du soufre contenu dans le minerai. Grâce à l'excellent rendement du haut fourneau[note 2], une réduction de 40 % des dépenses en combustible est envisageable. De plus, il devient possible d'éviter les étapes de broyage et de grillage du minerai, qui comptent alors entre 17 % et 50 % du coût de transformation du minerai en cuivre. Mais la fusion au haut fourneau a aussi ses inconvénients. Le four n'est efficace qu'avec des minerais suffisamment riches, et de nature rocheuse ; or les gisements de ce type sont quasiment tous épuisés dans les années 1930. Ces fours sont également difficiles à conduire et produisent une matte de qualité médiocre[8] - [note 3].
L'utilisation d'un four à réverbère permet aussi la fusion et l'affinage simultanés des pyrites. En 1878, le métallurgiste américain Henry L. Bridgman en brevette le principe[10]. Il propose d'oxyder un minerai sulfureux finement pulvérisé. Bien que les procédés d'enrichissement qui commencent à se développer, comme la flottation par moussage, facilitent la production d'un tel minerai, l'idée n'est pas concrétisée. En outre, le mauvais rendement des fours à réverbères fait que l'ensemble du procédé ne permet qu'une réduction de 5 % des besoins en combustible[8]. En 1915, des chercheurs de l'Anaconda Copper brevettent l'utilisation d'un régénérateur Siemens pour en améliorer le rendement thermique[11]. Mais rien ne permet d'établir que leur invention, comme celle, similaire, brevetée en 1932 par Horace Freeman[12] ait été concrétisée[8].
À l'opposé de ces brevets, certains chercheurs tenant la théorie de l'oxydation des pyrites comme acquise, se concentrent sur la réalisation pratique. Dans les années 1930, Frederick Laist and J. P. Cooper, toujours de l'Anaconda Copper, prouvent que récupérer la chaleur dégagée par l'oxydation des pyrites lors de leur grillage sur sole tournante peut économiser jusqu'à 60 % du combustible nécessaire à l'opération. En 1935, en Union Soviétique, un four similaire est évalué puis abandonné à cause de la mauvaise tenue des réfractaires et du colmatage du four par les particules fondues. En 1937, la Société française des mines de Bor essaie un four-cuve vertical, mais abandonne face aux difficultés techniques, et surtout à cause de la Seconde Guerre mondiale[8].
Enfin, en 1936, Telfer E. Norman, un métallurgiste travaillant pour le compte d'Inco, publie une revue d'ensemble sur la problématique de la fusion des pyrites sans combustible. Il démontre que la chaleur dégagée par l'oxydation des pyrites ne peut pas suffire à la fusion : trop de chaleur est consommée par le réchauffage de l'azote de l'air utilisé pour oxyder les pyrites. Par contre, dans une atmosphère contenant plus de 40 % d'oxygène, la fusion d'un minerai sulfureux très concentré devient théoriquement possible. Comme, à cette époque, les techniques cryogéniques de production d'oxygène pur sont devenues tout à fait envisageables pour des applications industrielles, il n'existe aucun blocage théorique ou technologique pour la mise au point d'un procédé de fusion autogène des pryrites[8] :
« À condition qu'un four adapté puisse être mis au point et s'avère être un outil [industriellement] satisfaisant, le paramètre qui devient le plus important serait les coûts relatifs du combustible et de l'oxygène[13]. »
— J. Newton & C. L. Wilson, Metallurgy of Copper
L'arrivée de la Seconde Guerre mondiale suspendra pourtant toutes les recherches.
Outokumpu
En 1936, une petite entreprise finlandaise, Outokumpu, fondée en 1914 près de la ville éponyme pour exploiter un gisement de cuivre local, met en service un four à arc électrique pour la fusion du minerai en matte. Ce four est alors le plus gros du monde pour cet usage. Mais, en 1944, l'Armistice de Moscou amène à l'annexion par l'Union Soviétique de la Carélie, et donc des deux barrages hydroélectriques de Enso-Vallinkoski et de Lesogorsk/Rouhiala (ru), privant du même coup la Finlande du tiers de sa capacité de production d'électricité. Cet événement, combiné avec la démobilisation et le paiement des indemnités de guerre (61 % des exportations du pays en 1945), met sous pression l'industrie finlandaise. Alors que l'entreprise Outokumpu consomme 3 % de l'électricité du pays, le prix de cette énergie quintuple entre 1946 et 1948[8].
Mais, dès 1945, anticipant la forte contrainte qui s'esquisse sur cette source d'énergie, l'entreprise se lance dans l'étude au développement d'un procédé plus économe en énergie. En seulement trois mois, l'équipe de quatre ingénieurs missionnée pour résoudre le problème propose une alternative. Ses calculs montrent qu'en oxydant le minerai concentré avec de l'air, puis en récupérant la chaleur des fumées afin de préchauffer l'air oxydant, il devient possible de réaliser la fusion presque sans apport de combustible. En , soit moins de deux ans après le début des études, l'ancêtre des fours de fusion flash est opérationnel. Un modèle industriel est construit à partir de septembre[note 4], qui est fonctionne trois mois après. En 1949, le procédé est opérationnel dans l'usine de Harjavalta, même si le four électrique d'avant-guerre assure encore un tiers de la production d'Outokumpu jusqu'en 1953[8].
Inco
Au lendemain de la Seconde Guerre mondiale, le géant mondial du nickel, le canadien Inco[note 5] reprend les recherches là où Norman les avait arrêtées. Disposant d'électricité en abondance grâce à l'exploitation des Chutes du Niagara, et s'associant avec le français Air liquide, plus petit mais plus agressif[note 6] que son concurrent Linde, Inco reprend le développement d'un four de fusion flash utilisant un enrichissement en oxygène. Le prototype démarre en (donc un mois avant celui d'Outokumpu), le premier modèle industriel n'étant opérationnel que le [8]. Comme son équivalent d'Outokumpu, il s'agit d'une évolution directe du four à réverbère[14].
Bien que le four flash d'Inco ne se soucie pas d'économiser l'énergie comme celui d'Outokumpu, il s'avère thermiquement plus efficace. En effet, les échangeurs de chaleur choisis par Outokumpu sont moins perfectionnés que les technologies cryogéniques utilisées par Inco. Ils sont aussi sont plus fragiles et d'un moins bon rendement[8].
L'absence d'azote dans l'air de combustion génère des fumées très riches en SO2 (environ 50 %), ce qui simplifie considérablement leur traitement. Ainsi, en 1952, le premier four industriel d'Inco est associé à une unité de traitement de taille standard, alors qu'elle retire dix fois plus de soufre que n'importe quelle autre unité équivalente dans le monde[14].
Fours flash
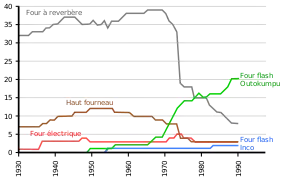
Four flash d'Outokumpu
Bien que moins efficace que celui d'Inco, le four d'Outokumpu s'est imposé à ses détriments. En effet, l'entreprise finlandaise a adopté une stratégie de vente de ses brevets et d'exportation de son savoir-faire qui a permis la diffusion rapide de sa technologie. À l'inverse, Inco n'a utilisé la fusion flash que pour maintenir son quasi-monopole sur la production du nickel[8].
Le four d'Outokumpu est constitué d'un cylindre vertical, le réacteur, au sommet duquel pénètrent le minerai concentré sec et pulvérisé, et l'air, éventuellement mélangé avec de l'oxygène, du combustible ou d'un fondant siliceux. Porté instantanément à haute température, le concentré s'oxyde et fond au cours de sa chute dans le réacteur. Il arrive alors dans la chambre de décantation, ou settler, où se séparent la matte et le laitier. Les fumées s'échappent de l'autre extrémité de la chambre par un carnau vertical, l'uptake, qui les amènent vers un récupérateur de chaleur. À Harjavalta, un concentré à 23 % de cuivre donne ainsi une matte à 64 % de cuivre et des fumées entre 11 et 14 % de SO2. En 1996, le plus grand four flash de ce type, à San Manuel, produisait 1,2 Mtonnes/an de matte et aurait même pu atteindre 2 Mtonnes/an avec quelques modifications. Comparé à un four à réverbère, la production est 4 fois plus élevée à surface égale, et la consommation en énergie est divisée par 2[15].
À l'origine, le préchauffage de l'air à une température de 200 à 800 °C permettait d'atteindre un fonctionnement autogène[16]. En 1971, Outokumpu adopte l'enrichissement en oxygène dans son usine d'Harjavalta[1]. Cette amélioration amène le four d'Outokumpu au même niveau d'efficacité énergétique que celui d'Inco[8]. Au début du XXIe siècle, l'enrichissement en oxygène, à des teneurs comprises entre 30 et 90 %, a quasiment partout remplacé la récupération de chaleur[16].
En 1978, le four flash de Głogów, en Pologne parvient pour la première fois à réaliser une fusion flash suffisamment oxydante pour produire du blister, c'est-à-dire un cuivre impur, au lieu de matte : l'étape affinage de la matte, réalisée par le procédé Manhès-David dans un convertisseur Peirce-Smith, devient alors inutile. En 1988, la fonderie d'Olympic Dam, en Australie, adopte également ce procédé. Au début du XXIe siècle, la fusion flash du minerai en blister n'est opérationnelle que dans ces deux usines[1].
Ce four a été également employé pour la production de plomb et valoriser les déchets de jarosite[16]. Un de ses inconvénients principaux est son incapacité à fondre des déchets cuivreux[E 1].
Au début du XXIe siècle, un four gros flash d'Outokumpu mesure typiquement, à l'intérieur, 20 m de long, 7 m de large et 2 m de haut. Son intérieur est tapissé de briques réfractaires en magnésite-chrome, refroidies par water jacket (en). Un tel four transforme quotidiennement 3 000 tonnes de concentrés en 1 500 tonnes de matte et autant de laitier, en utilisant un air enrichi à 50-80% d'oxygène. Il peut produire pendant plus de 8 ans sans réparation majeure de son revêtement interne réfractaire[E 2].
Four flash d’Inco
.svg.png.webp)
Le four d'Inco consiste à introduire par des tuyères latérales le minerai concentré pulvérisé et mélangé à des fondants. Porté par l'oxygène, le minerai pénètre dans la chambre de combustion où il s'allume instantanément. Les fumées s'évacuent à travers une cheminée centrale. En 1996, à l'usine de Copper Cliff, un four Inco produit une matte à 45 % de cuivre-nickel, un laitier à 0,75 % de Cu-Ni, et une fumée à 75 % de SO2[15].
Le fonctionnement avec de l'oxygène pur génère des fumées très riches en SO2 (55 à 75 % de SO2, contre 1 % pour un four à réverbère[E 3]), ce qui facilite leur retraitement : l'unité de traitement des fumées est 10 fois plus petite que celle d'un four à réverbère de capacité identique. En outre, la récupération de chaleur est plus facile à cause du faible volume des fumées[note 7] - [14].
En 2011, la fusion flash assure trois quarts de la production du nickel extrait des minerais sulfureux (les minerais de nickel de type saprolite sont eux fondus au four électrique). On dénombre 9 fours de fusion flash dédiés à la production de nickel : 7 fours de type Outotec assurant 70 % de la fusion flash de nickel, et 2 fours de type Inco produisant les 30 % restants[17].
Au début du XXIe siècle, un four gros flash d'Inco mesure typiquement, à l'intérieur, 22 m de long, 5,5 m de large et 5 m de haut. Son intérieur est tapissé de briques réfractaires en magnésite-chrome, refroidies par water jacket (en). Un tel four transforme quotidiennement 1 800 tonnes de concentrés en 1 000 tonnes de matte et 1 200 tonnes de laitier, en consommant 450 tonnes d'oxygène pur. Il peut produire pendant 5 à 6 ans sans réparation majeure de son revêtement interne réfractaire[E 4].
Four flash Kivcet
.svg.png.webp)
Directement dérivé du four d'Outokumpu[16], le four Kivcet a été développé en 1967 par l'institut soviétique VNIITSVETMET à Öskemen, au Kazakhstan, sous la direction du professeur A. P. Sychev. En 1985, la première unité industrielle a été installée dans le combinat de production de plomb et de zinc d'Öskemen, maintenant Kazzinc (en)[18]. Dans sa première version, la chambre de réaction était située au centre du four, et les particules y étaient animées d'un mouvement cyclonique. Les matières en fusion étaient alors projetées contre la paroi, ruisselant dessus. Mais le PbO corrodant le revêtement réfractaire, cette disposition a été abandonnée pour aboutir à la conception actuelle, où la chambre de réaction est dissociée du four à arc électrique[2].
La chambre de combustion est un four flash classique, utilisant de l'oxygène pur. L'oxydation des sulfures est suffisamment exothermique pour provoquer leur fusion. Mais avant d'atteindre le fond de la chambre de décantation, les oxydes fondus traversent une couche de coke à plus 1 200 °C qui, à de telles températures, brûle en dégageant un gaz très réducteur, le monoxyde de carbone. Ainsi, les oxydes fondus subissent, dans le bain, une réduction jusqu'à atteindre leur état métallique. Cette réduction, ainsi que la séparation par décantation entre le métal et le laitier, est parachevée dans le four électrique, dont les électrodes maintiennent les matières en fusion[2].
En 2004, le procédé Kivcet représente 10 % des capacités de production mondiale de plomb (estimées à 3,54 Mtonnes/an)[2]. Le procédé est également employé pour la production du cuivre[16].
Le procédé
Principe
L'objectif principal d'un four flash est d'amener à la fusion le minerai concentré, contenant typiquement 30 à 40 % de cuivre[E 5], ou de 12 à 20 % de nickel[17]. La température qui y est atteinte, 1 250 °C, permet d'avoir une matte et un laitier en fusion, et suffisamment fluides pour se dissocier par décantation[E 5].
Le minerai concentré doit être finement pulvérisé (taille d'environ 100 μm) et sec pour s'enflammer. Les concentrés issus de la flottation par moussage ont typiquement cette taille[E 5].
Les produits issus de la fusion flash sont[E 5] :
- la matte en fusion. Dans le cas de la métallurgie extractive du cuivre, la teneur en cuivre atteint typiquement 65 %, ou 40 % de nickel dans le cas de l'extraction du nickel ;
- le laitier. Sa teneur en silice permet de stabiliser l'oxyde de fer FeO sous la forme de fayalite Fe2SiO4. Il contient 1 à 2 % de cuivre ou de nickel ;
- la fumée. Il contient, suivant le niveau d'enrichissement en oxygène, de 30 à 70 % de SO2. Le four d'Inco, qui fonctionne à l'oxygène pur, génère une fumée à 75% de SO2.
Les procédés dans les fours d'Outokumpu et d'Inco sont très proches. La comparaison de leurs avantages et inconvénients respectifs est fréquente. On peut attribuer le succès des fours d'Outokumpu à la stratégie de l'entreprise, mais aussi à leur simplicité (un seul brûleur), ainsi qu'à la plus grande distance entre brûleur et sortie des fumées qui favorise les échanges thermiques. La récupération d'énergie du four d'Outokumpu est plus pertinente que celle des fours Inco, qui fabriquent de la vapeur en grande quantité à laquelle il faut trouver une utilité. Mais la configuration horizontale des fours d'Inco favorise la décantation du laitier, qui restitue ainsi à la matte la quasi-totalité du cuivre et du nickel[E 6].
Réactions chimiques
Un four de fusion flash réalise simultanément un grillage (c'est-à-dire une oxydation du minerai qui reste à l'état solide), une fusion, et un affinage de la matte en cuivre[17].
- Métallurgie extractive du cuivre :
Dans le cas de la fusion de la chalcopyrite (de formule brute CuFeS2), la réaction principale est : 2 CuFeS2 (s) + O2 (g) → Cu2S. FeS (l) + FeO (l) + SO2 (g) produisant 450 kJ/mol de CuFeS2[E 7]
- Métallurgie extractive du nickel :
Dans le cas de la fusion de la pentlandite (de formule brute (Fe,Ni)9S8), la réaction principale est : (Fe,Ni)9S8 (s) + O2 (g) → NiS (l) + FeO (l) + SO2 (g) produisant 1 200 kJ/mol de (Fe,Ni)9S8[17]
- Métallurgie extractive du plomb :
Dans le cas de la fusion de la galène (de formule brute PbS), les réactions qui dominent sont : PbS (s) + O2 (g) → Pb (l) + SO2 (g) produisant 219 kJ/mol de PbS Pb (l) + O2 (g) → PbO (l) + SO2 (g) produisant 298 kJ/mol de PbS PbS (l) + 2 PbO (l) → 3 Pb (l) + SO2 (g) produisant 61 kJ/mol de PbS
Lorsque le rapport O2/PbS est correctement choisi, une partie importante de la galène PbS est oxydée jusqu'au plomb métallique. Mais le laitier contient entre 30 et 40 % de litharge (PbO), ce qui est non négligeable, même si la quantité de laitier est assez faible (une tonne de laitier par tonne de concentré)[19]. Pour ne pas être perdue avec le laitier, la litharge doit être réduite par le CO. Cette réduction étant impossible dans le milieu oxydant nécessaire à la fusion flash, elle se fait dans le four électrique connexe, qui communique avec le four flash par un siphon : C (s) + CO2 (g) → 2 CO (g) consommant 165,4 kJ/mol de CO PbO (s) + CO (g) → Pb (l) + CO2 (g) produisant 95,8 kJ/mol de PbO Le bilan thermique de ces deux réactions est déficitaire : il est alors nécessaire d'apporter de la chaleur par un four électrique[2].
- Réactions connexes :
La pyrite et la pyrrhotite (de formules brutes FeS2 et Fe8S9) présentes dans les minerais sulfurés, sont grillées et fondues suivant des réactions très exothermiques : Fe8S9 (s) + O2 (g) → FeO (l) + 2 SO2 (g) produisant 700 kJ/mol de FeS2[20] Fe8S9 (s) + 13 O2 (g) → 8 FeO (l) + 9 SO2 (g) produisant 2 500 kJ/mol de Fe8S9[17]
L'oxyde de fer FeO, produit par les réactions précédentes, est un élément du laitier. Aux températures présentes dans le four, il se combine avec la silice (SiO2), qui va lui servir de fondant[note 8] : 2 FeO + SiO2 → Fe2SiO4 si T > 1 208 °C, produisant 20 kJ/mol de FeO[E 7]
Les premières réactions de grillage sont suffisamment exothermiques pour fondre le minerai concentré. Il arrive cependant que des brûleurs additionnels soient ajoutés, pour limiter la consommation d'oxygène, ou pour fondre des déchets cuivreux qui ne sont pas combinés avec du soufre[E 9]. Si l'oxydation du fer en FeO est exothermique, la transformation du FeO résultant en Fe2SiO4 implique l'apport de silice, enfournée froide. Le bilan général est désavantageux car la chaleur dégagée par les réactions chimique ne compense pas celle nécessaire à la chauffe de la silice : on évite ainsi de traiter des minerais concentrés riches en fer, et n'enfourne que la quantité de silice strictement nécessaire. Typiquement, on limite la quantité de silice en visant un rapport SiO2/Fe compris entre 0,7 et 1[E 10].
Évolutions actuelles et à venir
La fusion flash est souvent citée comme une innovation de rupture, une des plus marquantes du XXe siècle[8]. Procédé autogène, elle remplace à la fois les fours à réverbère, caractérisés par leur médiocre rendement thermique, et les fours de grillage, qui n'exploitent pas la chaleur dégagée par l'opération. Par ailleurs, la fumée de ces fours est un mélange de la fumée de combustion avec celle de la réaction d'oxydation. Leur fumée est donc moins riche en soufre et la désulfuration est plus difficile : 98,5 % du soufre émis par les fours flash est récupéré alors que la récupération n'atteint que 40 % pour les fours à réverbère. Les fours à réverbère relâchent 1 926 kg de CO2 et 963 kg de soufre par tonne de cuivre, alors que les émissions des fours flash sont, respectivement 46 kg et 23 kg[24].
Le principal inconvénient de la fusion flash consiste en son atmosphère très oxydante, qui oxyde les métaux que l'on souhaite récupérer. Le laitier est plus riche en oxydes de nickel, cuivre, plomb, etc. et il est avantageux de le réchauffer dans un four électrique où, mélangé avec des agents réducteurs comme le coke, il sera réduit afin de rejeter les métaux intéressants du laitier vers le métal. Cette étape complémentaire permet aussi de parfaire la décantation du laitier. Sans ce traitement du laitier, dans la métallurgie du nickel, la récupération du nickel est de 95 % (contre 98 % dans un four électrique), du cuivre, de 80 à 93 %, du cobalt, de 26 à 70 %[17]. Le four flash d'Inco peut cependant produire des laitiers moins riches en cuivre, évitant ainsi l'étape de décantation du laitier dans un four électrique[E 6].
Pour autant, dans la métallurgie extractive du cuivre, certaines fonderies poussent l'oxydation jusqu'à brûler tout le soufre contenu dans la matte, afin de supprimer son affinage dans un convertisseur Peirce-Smith (procédé Manhès-David)[E 1].
Notes et références
Notes
- Brevets anglais no 1131 du 21 mars 1878, no 4549 du 9 novembre 1878, etc.[3].
- Pour comparaison, au début du XXe siècle, le rendement thermique d'un haut fourneau atteint 70 %, contre 25 % sur les fours à réverbère équipés de régénérateurs tels que ceux utilisés pour le procédé Martin-Siemens[9].
- Outre le grand nombre de réactions physico-chimiques simultanées qui sont caractéristiques du haut fourneau, il faut noter que le haut fourneau est, fondamentalement, un four de réduction-fusion et qui est délicat d'en faire un four d'oxydation-fusion. La combustion du coke produit du monoxyde de carbone, un gaz très réducteur, alors que l'objectif est d'oxyder au maximum le soufre et le fer pour économiser le combustible.
- Ce four a coûté 30 millions de Dollars américains de 2010, soit 12 % des revenus d'Outokumpu[8].
- En 1945, Inco réalise un chiffre d'affaires de 1 480 millions de Dollars américains de 2010, avec 1 480 millions de bénéfice. La même année, le chiffre d'affaires d'Outokumpu atteint 105,3 millions de Dollars américains de 2010, avec 15,3 millions de bénéfice. Inco fourni alors 90 % du marché occidental du nickel, Outokumpu, 1 à 2 % du marché occidental du cuivre[8].
- L'oxygène vendu par Air Liquide s'avère finalement coûter la moitié du charbon que consommerait un four à réverbère de capacité identique[14].
- Inco montre qu'avec la chaleur récupérée dans une tonne d'azote présente dans les fumées, il est possible de fondre une tonne de minerai[1].
- Le point de fusion du FeO est de 1 377 °C. Si le FeO ne se combine pas immédiatement avec la silice pour former de la fayalite (Fe2SiO4)[21], dont le point de fusion est de 1 208 °C, son oxydation continue et il se transforme alors en Fe3O4. Or le point de fusion du Fe3O4 est de 1 597 °C ! Le Fe3O4 s'agglomère alors en une masse solide qui empêche le soufflage et ne peut être évacuée du four[22], si ce n'est par l'utilisation de fondants réducteurs, comme le spiegeleisen[23].
Une autre raison pour combiner le FeO avec le SiO2 vient du fait qu'un laitier riche en oxydes de fer peut oxyder le Cu2S suivant la réaction : FeO(laitier) + Cu2S(matte) → FeS(matte) + Cu2O(laitier) Une telle réaction est indésirable car elle fait migrer le cuivre de la matte vers le laitier. Pour cette raison, les métallurgistes évitent de produire des mattes à plus de 60 % de cuivre, même si les avantages de traiter une matte riche sont évidents[E 8].
Références
- (en) Marc E. Schlesinger, Matthew J. King, Kathryn C. Sole et William G. I. Davenport, Extractive Metallurgy of Copper, Elsevier, , 5e éd., 455 p. (ISBN 978-0-08-096789-9, lire en ligne)
- p. 87
- p. 74-75 ; 78-79 ; 82
- p. 403-405
- p. 92-97
- p. 73
- p. 101
- p. 5
- p. 68
- p. 77
- p. 85
- Autres références
- [PDF](en) « Outokumpu Flash Smelting », Outokumpu
- (en) H. Y. Sohn et M. Olivas-Martinez, Treatise on Process Metallurgy, vol. 3, Elsevier, , 1745 p. (ISBN 978-0-08-100000-7, lire en ligne), A, p. 686-688
- (en) John Hollway, « Production of sulphur, copper matte, etc. from pyrites (patent US 234129 A) »
- « Métallurgie : bessemérisation du cuivre », Bulletin de la Société de l'Industrie Minérale, 3e série, t. XV, , p. 560-573 (lire en ligne)
- (en) Larry M. Southwick, « William Peirce and E.A. Cappelen Smith and Their Amazing Copper Converting Machine », JOM, The Mineral, Metals & Materials Society (TMS), vol. 60, no 10, (lire en ligne)
- (en) Edward Dyer Peters, Modern copper smelting, The Engineering and Mining Journal, , 7e éd. (lire en ligne), p. 528
- (en) Donald M. Levy, Modern copper smelting, C. Griffin & company, limited, (lire en ligne), p. 192-193
- (en) Janne M. Korhonen et Liisa Välikangas, « Constraints and Ingenuity: The Case of Outokumpu and the Development of Flash Smelting in the Copper Industry » [PDF]
- (en) Thomas Turner (dir.), The Metallurgy of Iron : By Thomas Turner… : Being one of a series of treatises on metallurgy written by associates of the Royal school of mines, C. Griffin & company, limited, coll. « Griffin's metallurgical series », , 3e éd., 463 p. (ISBN 1-177-69287-2 et 978-1177692878, lire en ligne), p. 384
- (en) Henry L. Bridgman, « Process of reducing ores (patent US 578912 A) »
- (en) John H. Klepinger, Milo W. Krejci et Charles R. Kuzell, « Process of smelting ores (patent US 1164653 A) »
- (en) Horace Freeman, « Process of smelting finely divided sulphide ores (patent US 1888164 A) »
- (en) Joseph Newton et Curtis L. Wilson, Metallurgy of Copper, John Wiley & Sons, (lire en ligne), p. 161
- (en) Paul E. Queneau et Samuel W. Marcuson, « Oxygen Pyrometallurgy at Copper Cliff—A Half Century of Progress », The Minerals, Metals & Materials Society, (lire en ligne)
- Pierre Blazy et El-Aid Jdid, « Pyrométallurgie et électroraffinage du cuivre - Pyrométallurgie », dans Techniques de l'ingénieur, Éditions techniques de l'ingénieur (lire en ligne)
- [PDF]Document de référence sur les meilleures techniques disponibles : Industrie des métaux non ferreux, Direction régionale de l'environnement, de l'aménagement et du logement, , 778 p. (lire en ligne), p. 100-102
- (en) Frank K. Krundwell, Michael S. Moats, Venkoba Ramachandran, Timothy G. Robinson et William G. Davenport, Extractive Metallurgy of Nickel, Cobalt and Platinum Group Metals, Elsevier, , 610 p. (ISBN 978-0-08-096809-4, lire en ligne), p. 215 - 225
- (en) « The KIVCET Smelting Process »,
- (en) William G. I. Davenport et Eric H. Partelpoeg, Flash Smelting : Analysis, Control and Optimization, Pergamon Press, (ISBN 0-08-034925-0), p. 295
- Davenport et Partelpoeg 1987, p. 8
- (en) Heinrich Oscar Hofman, Metallurgy of copper, MacGraw Hill Book Company, (lire en ligne), p. 323
- Krundwell et al. 2011, p. 127
- Hofman 1914, p. 342
- (en) Nenad M Stojanović, Marko Kimi Milić et Darko M Milošević, Implementation of modern technologies in metallurgy in the function of protection of the environment and natural ressources, (ISBN 978-86-7747-486-7, lire en ligne [PDF])