Carl Wilhelm Siemens
Carl Wilhelm Siemens ( à Lenthe, royaume de Hanovre - , Grande-Bretagne) est un ingénieur britannique originaire du royaume de Hanovre, frère de Werner von Siemens, inventeur et créateur de procédés pour la fabrication de l'acier.
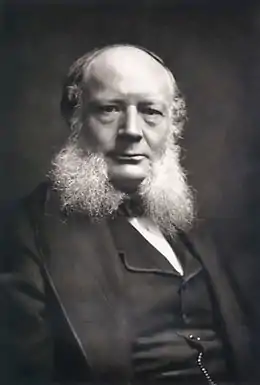
Naissance | |
---|---|
Décès | |
Sépulture | |
Nationalité |
Allemand puis anglais |
Formation | |
Activités | |
Père |
Christian Ferdinand Siemens (d) |
Fratrie |
Membre de | |
---|---|
Distinctions |
Il émigre en Angleterre en 1844. Par la suite, il dirige la branche anglaise de la société de Siemens & Halske, Siemens Brothers. Il obtient la nationalité britannique en 1859 et est fait chevalier en 1883.
Il est célèbre pour le développement du four à sole avec réchauffage des gaz, appelé « four Siemens », qu'il fait breveter en 1856. Ce four révolutionnaire est utilisé par Pierre-Émile Martin par la suite pour l'affinage de la fonte brute en acier : le procédé Martin-Siemens mis ainsi au point associe les deux inventeurs. Il est aussi l'un des pionniers de l'utilisation de l'énergie électrique et l'une des plus importantes personnalités de Grande-Bretagne dans le domaine de la science et de l'ingénierie.
Autres inventions
Régénérateur Siemens
Le régénérateur Siemens, fondé sur l'accumulation de chaleur, a été très populaire, et son usage a été étendu bien au-delà du four Martin-Siemens.
Il a été notamment utilisé au début du XXe siècle pour améliorer l'efficacité des « fours belges » d'extraction du zinc. Dans ce type d'application, il apporte des économies d'énergie, mais ne révolutionne pas le métier comme dans la sidérurgie. En effet, les températures y sont plus basses (la blende se décompose vers 900 °C et le zinc se vaporise à 907 °C, alors que le fer fond à 1 535 °C), ce qui diminue l'intérêt d'un système complexe de récupération d'énergie. Par ailleurs, les oscillations de températures, inhérentes au système Siemens, dégradent l'efficacité du four et la tenue des réfractaires. La nécessité d'avoir une température homogène dans un four de grande taille amène aussi à multiplier les brûleurs, complexifiant d'autant l'exploitation du four[1].
- Coupe transversale d'un four belge à régénérateur Siemens, utilisé à Auby. Les creusets inférieurs sont beaucoup plus chauffés que ceux du dessus.
- Coupe transversale d'un four belge à régénérateur Siemens, utilisé à Birkengang . La flamme est gérée dans une chambre intermédiaire entre régénérateurs et laboratoire.
- Coupes latérale et transversale d'un four belge à régénérateur Siemens utilisé à Monteponi (it). Les flammes sont réparties, mais l'équipartition des gaz et des fumées est difficile.
Procédés de réduction directe
Un des premiers fours de réduction directe imaginé par Siemens consiste en deux cornues parallèles en fonte, dont les extrémités, en argile, débouchent sur un four à réverbère de fusion. Les cornues chauffent le minerai mélangé avec du charbon de bois, le minerai de fer préréduit chaud tombe ensuite dans le four où il est élaboré à la composition chimique désirée. En 1890, soit 21 ans après la proposition de Siemens, en énumérant les nombreuses difficultés techniques liées à la mise au point d'un tel procédé, le métallurgiste américain Henry Marion Howe (en) s'étonne que « de nos jours, on se demande comment un homme aussi génial et expérimenté que Siemens ait pu croire à un tel projet […]. La folie d'aujourd'hui est plus sage que la foi d'hier »[H 1].
Un autre procédé de réduction directe, fondé encore sur l'utilisation d'un four à réverbère, a été le four en cascade. Il s'agit d'un four à réverbère à 2 laboratoires. Le laboratoire amont chauffe le minerai de fer, qui est amené manuellement dans le laboratoire aval où il est mélangé avec un agent réducteur (charbon, coke, etc.). Le procédé est abandonné par Siemens qui lui admet son mauvais rendement en fer (perdu en grande partie par le laitier) et « une certaine quantité de travail manuel et d'expertise »… euphémisme quand on relève les similitudes de ce procédé avec le puddlage[H 2]!
Plus séduisant car pensé comme un procédé continu, le four continu de réduction directe, fondé encore sur l'utilisation d'un four à réverbère, n'a pas connu plus de succès. Le système de chauffe y est d'un côté, le minerai mélangé au charbon est chargé à l'autre extrémité. Le laitier coule continuellement par un trou, le métal est vidangé à intervalles réguliers[H 2]. L'estimant inapte à déphosphorer de manière économique[note 1] - [H 4]. Howe qualifie ce four de « moins prometteur qu'original[H 2] ».
Enfin, Siemens, en abandonnant le four à réverbère pour un tambour rotatif, abouti à un procédé plus efficace[H 5]. Le réacteur consiste en un tambour de 3 m de diamètre et autant de long, d'axe horizontal, où sont insufflés des gaz préchauffés par deux régénérateurs. Le minerai de fer, ou les déchets métalliques à recycler, y sont mélangés avec du charbon (une tonne consommée par tonne de fer produite) et de la chaux. Le résultat est un fer quasiment dépourvu de soufre et de phosphore. Ce procédé, qui ne sera utilisé, et de manière épisodique, qu'aux États-Unis et au Royaume-Uni, dans les années 1880[2], est un des ancêtres des procédés modernes de production de minerai de fer préréduit avec du charbon dans un four rotatif[3].
- Four primitif de réduction directe consistant deux cornues parallèles alimentant le laboratoire d'un four à réverbère.
- Four de réduction directe en cascade : le four supérieur chauffe le minerai, l'inférieur assure sa réduction.
- Four continu de réduction directe (le système de chauffe est à gauche, le chargement se fait par la droite).
- Four de réduction directe inventé par Siemens, fondé sur le principe d'un tambour rotatif.
Cycle de Siemens
En 1857, Siemens brevette une technique de refroidissement des gaz en trois étapes[4].
Thermomètre électrique
En tant que membre du comité de circumnavigation qui doit préparer l'expédition océanographique du HMS Challenger, Siemens est chargé en 1871 de mettre au point un thermomètre électrique pour mesurer la température de l'Océan à différentes profondeurs[5].
Bibliographie
- (de) Wolfgang König: Sir William Siemens. 1823–1888. Eine Biographie, München: Beck 2020 (ISBN 978-3-406-75133-2).
- (de) Julius Pagel, « Siemens, Karl Wilhelm », dans Allgemeine Deutsche Biographie (ADB), vol. 34, Leipzig, Duncker & Humblot, , p. 213 f
- (de) Wilhelm Rothert: Allgemeine Hannoversche Biografie. Band 2: Im Alten Königreich Hannover 1814–1866. Sponholtz, Hannover 1914, S. 445–462. (Werner von Siemens und seine Brüder)
- (de) Frank Wittendorfer, « Siemens, Carl Wilhelm », dans Neue Deutsche Biographie (NDB), vol. 24, Berlin, Duncker & Humblot, pas encore publié, p. 372–374 (original numérisé).
- (de) Zukunft gestalten. Die Siemens-Unternehmer 1847–2018. Hrsg. vom Siemens Historical Institute. Hamburg 2018 (ISBN 978-3-86774-602-1).
Articles connexes
Liens externes
- Ressource relative Ă la recherche :
- Ressource relative aux beaux-arts :
- Notices dans des dictionnaires ou encyclopédies généralistes :
Notes et références
Notes
- La déphosphoration consiste à oxyder le phosphore en pentoxyde de phosphore P2O5. Cela impose une activité élevée en oxygène, ce qui est impossible tant qu'il y a du carbone car celui-ci absorbe l'oxygène… pour former du monoxyde de carbone CO, qui est un gaz réducteur[H 3].
Références
- Arthur Jean Baptiste Théodore Édouard Lodin de Lépinay, Métallurgie du zinc, Dunod, , p. 487-512.
- (en) William Henry Greenwood, Steel and Iron : Comprising the practice and theory of the several methods pursued in their manufacture, and of their treatment in the rolling mills, the forge, and the foundry, , 546 p. (ISBN 1-110-38645-1, lire en ligne), p. 213-217
- (en) Alexander Lyman Holley, Siemens' direct process of making wrought iron from ore, in a rotating gas furnace, , 21 p.
- (en) The Siemens cycle, sur le site kryolab.fysik.lu.se
- Frédéric Aitken et Jean-Numa Foulc, Des profondeurs océaniques au laboratoire. 2, A la découverte des mesures physiques du H.M.S. Challenger en relation avec la circulation océanique, Londres, ISTE, , 236 p. (ISBN 978-1-78405-465-6 et 1-78405-465-8, OCLC 1088557853, présentation en ligne, lire en ligne), chap. 1
- (en) Henry Marion Howe, The metallurgy of steel, vol. 1, The scientific publishing company, (lire en ligne [PDF]), p. 79-80
- p. 283
- p. 288
- p. 265-267
- p. 265-266
- p. 285-288