Extraction du zinc
La mĂ©tallurgie extractive du zinc est lâensemble des opĂ©rations permettant la fabrication de zinc mĂ©tallique Ă partir du minerai, ou plus rarement Ă partir de dĂ©chets mĂ©tallurgiques, d'aciĂ©ries notamment.
Le minerai (généralement la blende) est préalablement traité par flottation afin de séparer, le sulfure de sa gangue (silicate, carbonate etc). On obtient un concentré de sulfure de zinc et de sulfure de plomb.
Il existe alors deux voies de traitements :
- la pyrométallurgique ;
- lâhydromĂ©tallurgique suivi dâune opĂ©ration dâĂ©lectromĂ©tallurgie.
Données économiques
En 2002, la production mondiale de « zinc-métal » a été de 9502 kT.
La production de métal à partir du minerai représente environ 70 % de la production, 30 % provenant du recyclage.
Histoire de la production du zinc
Au commencement l'Inde
D'aprÚs l'archéologue Paul Cradock[1] - [2], les Indiens avaient inventé au XIIe siÚcle un procédé d'extraction du zinc. Ce procédé, exploité à Zawar jusqu'au XVIIIe siÚcle, a été décrit par des lettrés dans divers ouvrages comme le Rasaratnassamuchchaya (XIVe siÚcle). Basé sur la condensation de la vapeur de zinc, il présente des similitudes avec les procédés industriels modernes.
Le minerai (sulfure de zinc, aujourd'hui appelé blende) était « grillé » pour obtenir de l'oxyde de zinc (voir le paragraphe Grillage du sulfure). L'oxyde ainsi obtenu, mélangé avec diverses matiÚres organiques (source de carbone) et de la dolomie, était placé dans un creuset de terre de forme allongé. Ce pot était appelé aubergine. Une baguette de bois était plantée dans le mélange afin de créer un conduit par lequel circulera le gaz pendant la chauffe. Le creuset était fermé par un couvercle muni en son centre d'un long conduit servant de condenseur.
Plusieurs aubergines étaient placées dans un four, le condenseur dirigé vers le bas. La charge ainsi constituée était chauffée par un feu qui brûlait au-dessus. La chaleur résultant du feu provoquait la vaporisation du zinc. Celui-ci se condensait dans les conduits des condenseurs situés dans la partie basse du dispositif (donc plus froide).
La Chine au XVIe siĂšcle...
Bien qu'il existe diverses hypothÚses, la production de zinc en Chine est avérée au XVIe siÚcle ; le procédé étant décrit dans le livre Tien-kong-kai-ou datant du XVIIe siÚcle.
à l'inverse du procédé indien, les chinois utilisent la smithsonite (carbonate de zinc de formule ZnCO3, souvent appelé calamine). Ce minerai, mélangé avec du charbon de bois, était placé dans un pot fermé par une plaque de fer et chauffé, le zinc condensé étant collecté dans un creuset placé au-dessus du mélange. La circulation du gaz était assurée par un tube sortant du pot.
L'Europe au XIXe siĂšcle
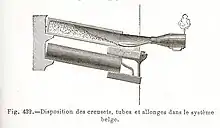
Plusieurs méthodes ont été expérimentées au XVIIIe siÚcle pour extraire le zinc de ses divers minerais.
- En 1742, le chimiste suédois Anton von Swab distilla du zinc à partir de la calamine
- En 1744 le mĂȘme Anton von Swab en distille Ă partir de la blende.
- De façon indĂ©pendante, Andreas Sigismund Marggraf rĂ©duisit de la calamine en 1746 et dĂ©montra que le zinc pouvait ĂȘtre extrait de la blende.
- C'est William Champion (1709-1789) qui fera, Ă partir de la calamine, la premiĂšre tentative industrielle de production de zinc Ă l'aide d'un condenseur ressemblant aux condenseurs indiens. Il installa son usine en 1743 Ă Bristol en Angleterre. Son procĂ©dĂ© Ă©tait basĂ© sur des creusets verticaux prolongĂ©s dans le bas de condenseurs trempant dans de l'eau pour les refroidir. Il fallait soixante dix heures pour produire 400 kg de zinc. La production annuelle de l'usine est estimĂ©e Ă environ 200 tonnes par an. Le procĂ©dĂ© consommait beaucoup dâĂ©nergie.
- Johan Ruberg (1751-1807) Ă partir de 1798 en SilĂ©sie amĂ©liore le procĂ©dĂ© par des creusets horizontaux, permettant un chargement et un dĂ©chargement sans refroidir l'installation, c'est-Ă -dire en amĂ©liorant nettement le rendement Ă©nergĂ©tique. Ce procĂ©dĂ© a inspirĂ© de nombreuses usines en Europe et notamment en Belgique dans la rĂ©gion de LiĂšge oĂč Jean-Jacques Daniel Dony (1759-1819) crĂ©a une premiĂšre usine en 1805 puis en 1810 dans le faubourg Saint-LĂ©onard de LiĂšge. Dony y a encore modifiĂ© le principe des creusets horizontaux. La Belgique Ă©tant alors sous domination française, NapolĂ©on Ier lui a accordĂ© la concession du gisement belge le plus riche en zinc (Moresnet/La Calamine). Ces usines belges sont Ă l'origine de la SociĂ©tĂ© des Mines et Fonderie de la Vieille Montagne (créée en 1837) qui devint rapidement leader dans la production de zinc.
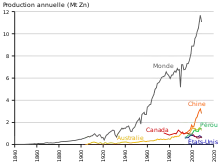
Production nord-américaine
Elle ne démarra qu'en 1850 en utilisant le procédé de Dony. La mine de Red Dog, exploitée depuis 1989, est actuellement la plus grande mine à ciel ouvert de zinc d'Amérique du Nord.
Dans le monde
En 1907, la production Ă©tait de 737 500 tonnes, dont 31 % provenait des Ătats-Unis, 31 % d'Allemagne, 21 % de Belgique.
Extraction miniĂšre
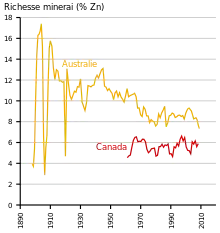
Comme beaucoup de mĂ©taux non ferreux, la teneur en mĂ©tal des minerais n'a jamais cessĂ© de baisser. Les minerais de zinc sont souvent associĂ©s Ă la prĂ©sence de plomb et d'argent et, dans ce cas, ils sont extraits ensemble. Le zinc peut Ă©galement ĂȘtre trouvĂ© associĂ© avec du cuivre, comme dans la grande mine de minerais pauvres d'Antamina, au PĂ©rou[3].
Extraction par pyrométallurgie
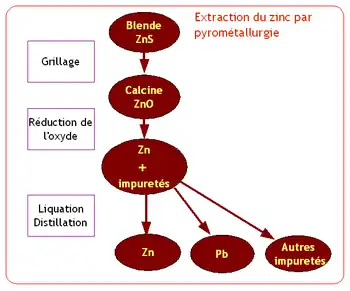
Le procédé pyrométallurgique est constitué des opérations suivantes :
- grillage du sulfure pour obtenir un oxyde de zinc,
- rĂ©duction de lâoxyde
- affinage par liquation et distillation
Grillage du sulfure
Le grillage a pour but de transformer le sulfure en oxyde. Lâobtention de lâoxyde de zinc ZnO est rĂ©alisĂ©e Ă une tempĂ©rature comprise entre 910 °C et 980 °C. Lâoxyde obtenu est appelĂ© « calcine »[4].
La réaction est exothermique.
RĂ©duction de lâoxyde
Pour rĂ©duire lâoxyde de zinc, il faut le chauffer Ă une tempĂ©rature supĂ©rieure Ă la tempĂ©rature de vaporisation du zinc (907 °C). Tous ces procĂ©dĂ©s sont basĂ©s sur le chauffage de lâoxyde pour obtenir le zinc sous forme gazeuse, par rĂ©action carbothermique. Le zinc est rĂ©cupĂ©rĂ© par condensation de ce gaz.
Procédé en creuset vertical
Un mĂ©lange de calcine, fine de charbon et d'un liant est aprĂšs cokĂ©faction placĂ© dans un creuset de carbure de silicium dâune dizaine de mĂštres de haut et dâune section rectangulaire dâenviron 2 m par 0,3 m. Le creuset est alimentĂ© en continu par le haut et il est chauffĂ© Ă une tempĂ©rature comprise entre 1 280 °C et 1 320 °C. Lâoxyde de zinc se rĂ©duit au contact du carbone en zinc mĂ©tallique, selon la formule :
Ă lâissue de la rĂ©action, le zinc est gazeux et encore mĂ©langĂ© Ă du monoxyde de carbone gazeux. Ă partir de ce mĂ©lange rĂ©cupĂ©rĂ© en haut du creuset, le zinc est condensĂ© Ă lâaide dâune turbine.
Procédé en creuset horizontal
Le creuset est en terre rĂ©fractaire et dâune capacitĂ© relativement rĂ©duite. Il est constituĂ© dâune chambre dans laquelle sera placĂ© un mĂ©lange calcine, charbon (en excĂšs). Elle est prolongĂ©e par un condenseur qui servira Ă condenser les vapeurs de zinc et dâune allonge qui collectera les gaz et en particulier le monoxyde de carbone qui sera brĂ»lĂ© Ă la sortie.
Compte tenu de la faible capacité des creusets, ils sont associés en batterie. Les creusets sont chauffés pendant une durée de un à deux jours à 1 200 °C. Le rendement de ce procédé est relativement faible en comparaison des autres procédés.
Procédé Imperial smelting
Ce procĂ©dĂ© est utilisĂ© quand on veut extraire dâautres mĂ©taux (cuivre, or, antimoine, bismuth, argent) prĂ©sents dans le minerai. Le procĂ©dĂ© comporte des similitudes avec celui de lâextraction de la fonte dans un haut-fourneau. On mĂ©lange dans le four de la calcine et du coke. Ce mĂ©lange sâĂ©coule de haut en bas. La combustion du coke en bas du four produit du monoxyde de carbone. Ce gaz rĂ©ducteur monte et rĂ©duit lâoxyde de zinc en zinc mĂ©tal.
Le zinc se gazĂ©ifie et est collectĂ© en haut du dispositif, tandis que le plomb liquide sâĂ©coule avec un laitier contenant divers oxydes : SiO, Al2O3, CaO, SO2. En s'Ă©coulant, le plomb emmĂšne dâautres Ă©lĂ©ments mĂ©talliques qui peuvent ĂȘtre valorisĂ©s.
Le mélange gazeux capté en haut du four contient environ 8 % de zinc, 25 % de monoxyde de carbone et 11 % de dioxyde de carbone.
Le gaz traverse une pulvérisation de gouttelettes de plomb en fusion à une température de 550 °C. On récupérera 1 tonne de zinc pour 400 tonnes de plomb. à la sortie du condenseur, le mélange plomb-zinc est traité par liquation (le zinc liquide flottant sur le plomb) afin de séparer le plomb du zinc, qui contient encore 1,5 % de plomb.
Affinage : liquation, distillation
Le zinc obtenu lors des opĂ©rations prĂ©cĂ©dentes contient encore du plomb et dâautres impuretĂ©s (fer, cadmium dans des proportions de lâordre de 0,1 %). Pour augmenter le titre en zinc du mĂ©tal, il est affinĂ© par deux opĂ©rations : la liquation et la distillation.
La liquation est basĂ©e sur une diffĂ©rence de miscibilitĂ© entre le plomb et le zinc Ă une tempĂ©rature comprise entre 430 °C et 440 °C. De mĂȘme, la solubilitĂ© du fer dĂ©croĂźt fortement lorsque lâon refroidit le mĂ©lange fer- zinc.
En traitant le zinc issu des opĂ©rations prĂ©cĂ©dentes dans un four Ă rĂ©verbĂšre Ă une tempĂ©rature comprise entre 430 °C et 440 °C pendant un Ă deux jours, on sĂ©pare le zinc qui contient encore 0,9 % de plomb de ce qui sâappelle la ââmatte de zincââ contenant du plomb, 5 Ă 6 % de zinc et un composĂ© ferreux de composition FeZn13.
Pour obtenir un zinc pur, il faut passer par une opĂ©ration de distillation fractionnĂ©e qui permet de sĂ©parer les diffĂ©rents constituants mĂ©talliques en jouant sur leurs tempĂ©ratures de fusion. Pour cela, on chauffe le mĂ©lange de mĂ©taux pour le rendre gazeux. Ă lâaide de diverses colonnes de distillation, on sĂ©pare les mĂ©taux en les condensant.
Extraction par hydro-électrométallurgie
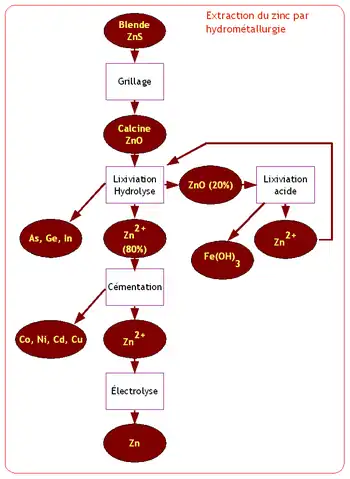
Le procédé hydrométallurgique est composé des opérations suivantes :
Lixiviation
Par cette opĂ©ration, on traite soit de la calcine issu de lâopĂ©ration de grillage, soit directement le sulfure de zinc, ce dernier procĂ©dĂ© Ă©tant plus rĂ©cent que le traitement de lâoxyde de zinc.
Le but de la lixiviation est de mettre en solution le zinc sous forme de lâion Zn2+ en obtenant la transformation soit du sulfure de zinc issu directement du minerai, soit lâoxyde de zinc (calcine) issu du grillage en sulfate de zinc (ZnSO2+).
Traitement du sulfure de zinc
Le sulfure est traitĂ© par action de lâacide sulfurique en milieu oxydant pour obtenir du sulfate de zinc et du soufre sous forme solide. La rĂ©action avec lâacide sulfurique en prĂ©sence de oxygĂšne est lente. On utilise comme oxydant lâion Fe3+.
La réaction globale est la suivante :
Lixiviation hydrolyse
On place la calcine en prĂ©sence dâune solution trĂšs diluĂ©e dâacide sulfurique. Cette opĂ©ration permet la mise en solution de 80 % du zinc sous forme de sulfate de zinc. On Ă©limine certaines impuretĂ©s mĂ©talliques : arsenic, germanium et indium en injectant des ions ferreux (Fe2+) qui prĂ©cipitent en hydroxyde de fer (Fe(OH)3) en entraĂźnant ces composĂ©s.
On sĂ©pare par dĂ©cantation la solution dâions zinc qui sera traitĂ©e par cĂ©mentation puis Ă©lectrolysĂ©e. Les boues contenant encore 20 % du zinc sous forme dâoxyde sont traitĂ©es par ââlixiviation acideââ.
Lixiviation acide
La mise en solution des 20 % de zinc restant est obtenue en utilisant de lâacide sulfurique concentrĂ©. Le fer et le cuivre sont Ă©galement solubilisĂ©s.
La solution décante pour séparer les éléments solubilisés des déchets solides résiduels du minerai et de certains éléments insolubles.
On extrait le fer de la solution contenant le zinc en le prĂ©cipitant sous forme dâhydroxyde ferrique (Fe(OH)3). La solution de zinc ainsi obtenue sera rĂ©introduite dans lâopĂ©ration de lixiviation hydrolyse.
Cémentation
Le but de la cĂ©mentation de la solution issue de lâopĂ©ration de lixiviation hydrolyse est de retirer les Ă©lĂ©ments : cobalt, nickel, cadmium et cuivre. Ces Ă©lĂ©ments ayant Ă©tĂ© solubilisĂ©s sous forme dâions.
Le principe est de mettre en contact lâion mĂ©tal (exemple Cu2+) avec un mĂ©tal ayant un pouvoir rĂ©ducteur plus important (moins Ă©lectronĂ©gatif). On utilise ici de la poudre de zinc fine.
On a une réaction du type :
LâopĂ©ration se fait par plusieurs cĂ©mentations successives. La difficultĂ© dâextraire les Ă©lĂ©ments suit lâordre suivant par difficultĂ© croissante : Cuivre, Cadmium, Nickel, Cobalt. On joue en particulier sur la tempĂ©rature (entre 45 °C et 65 °C pour le cadmium, 75 °C et 95 °C pour le cobalt).
Les liquides et les solides sont séparés par filtration.
Ălectrolyse
LâĂ©lectrolyse est effectuĂ©e en faisant passer un courant Ă©lectrique entre deux Ă©lectrodes dans la solution de sulfate de zinc obtenue Ă lâissue de lâopĂ©ration de cĂ©mentation.
Elle met en jeu les réactions suivantes :
- Cathode en aluminium :
et
- anode en plomb :
La réaction globale est :
Lâinstallation est constituĂ©e de cellules comportant chacune jusquâĂ quatre-vingt six cathodes (sur des installations dites Superjumbo). Pour une installation de cette taille, cela reprĂ©sente une surface de 3,2 m2 d Ă©lectrode. Le zinc est rĂ©cupĂ©rĂ© par action mĂ©canique sur les cathodes.
LâĂ©lectrolyte est Ă une tempĂ©rature de 30 Ă 40 °C. La tension dâĂ©quilibre thĂ©orique est de 2,022 V. Compte tenu des diffĂ©rents phĂ©nomĂšnes physiques, de la gĂ©omĂ©trie de lâinstallation, les tensions rĂ©elles sont de 3,2 Ă 3,7 V pour des intensitĂ©s variant de 400 Ă 700 A/m2. La consommation Ă©lectrique est de 2 950 Ă 3 500 kWh/t de zinc produit.
Voir aussi
Articles connexes
Bibliographie
- Fathi Habashi, Discovering the 8th metal, publiĂ© par lâ International Zinc Association (http://www.zincworld.org/ ), consultable sur (PDF)
- Pierre Routhier, Voyage au monde du métal : inventions et aventures, Paris, Belin, coll. « Regards sur la science », , 159 p. (ISBN 978-2-7011-2403-2, OCLC 1040412308), « Un métal volatil capturé en Asie : le zinc », p. 100 à 105.
- Michel Darcy, MĂ©tallurgie du zinc, M2770, , Ă©ditions Techniques de lâingĂ©nieur.
- Jean Philibert, Alain Vignes, Yves BrĂ©chet, Pierre Combrade, MĂ©tallurgie, du minerai au matĂ©riau, Chapitre 14 : lâĂ©laboration du zinc, page 225 Ă 232, Ădition Dunod, 2e Ă©dition, 2002 (ISBN 2-10-006313-8).
Notes et références
- Cf. P. T. Craddock (dir.), I. C. Freestone, L. K. Gurjar, A. P. Middleton et L. Willies, 2000 years of zinc and brass, Londres, British Museum, (rĂ©impr. 1998, ed. rev.), 258 p. (ISBN 978-0-86159-124-4 et 0-86159-124-0), « Zinc in classical antiquity », p. 1â3.
- Cf. P. T. Craddock et al. Ibid., pp. 35â46.
- (en) Gavin M. Mudd, « The âLimits to Growthâ and âFiniteâ Mineral Resources : Re-visiting the Assumptions and Drinking From That Half-Capacity Glass », , p. 5
- La valorisation de l'acide sulfurique produit a amené certaines entreprises à quitter le zinc pour se lancer dans d'autres productions (par exemple, Prayon et les superphosphates).