Grillage (métallurgie)
En métallurgie extractive, le grillage est une chauffe à haute température de minerais ou de produits métallurgiques intermédiaires à l'état solide. Plus précisément, le terme désigne tout procédé pyrométallurgique consistant à chauffer un minerai dans une atmosphère oxydante, de façon à en changer les propriétés physiques et la composition chimique, par des réactions solide-gaz.
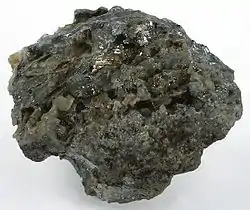
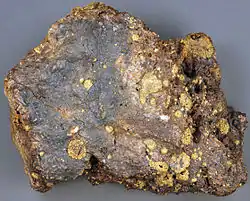
Le grillage à 500 °C provoque l'oxydation du tellure selon la réaction AuTe2(s) + O2(g) → Au(s) + TeO2 (g), l'or restant sous la forme de bulles vésiculaires[1].
Incontournables dans la métallurgie extractive des métaux, les procédés de grillage des minerais ont beaucoup évolué. Au début du XXIe siècle, les fours à réverbères et à soles multiples ne sont plus guère utilisés. Si les fours à tambours rotatifs existent encore, ils reculent devant les fours à lit fluidisé (dans la métallurgie des minerais non ferreux et des mattes) et le grillage sur chaîne (systématique dans la sidérurgie). Mais ce dernier générant un frittage en même temps que le grillage, il est plutôt qualifié de procédé d'agglomération.
Définitions
Un sens d'abord multiple
Au XVIIIe siècle, le grillage est associé au chauffage à haute température de minerais. Mais la compréhension, encore très confuse, des réactions chimiques mises en œuvre, combinée avec l'empirisme des méthodes de production, empêche alors l'établissement d'une définition précise. Ainsi, quand John Percy aborde le sujet en 1865, il commence par préciser que « ce mot […] s'applique à des procédés qui, par leur nature et leur objet, diffèrent beaucoup entre eux. »[2].
Puisque le mot ne peut alors pas être associé à un procédé ou un résultat, les auteurs évoquent une série de synonymes, en renonçant à établir une quelconque nuance : Pierre Joseph Macquer ne note pas de différence entre « grillage », « rôtissage », « calcination » et « torréfaction ». L'Encyclopédie de Diderot propose comme synonymes « calcination », « cuisson » et « rôtissage »[SF 1].
Et une acceptation moderne plus restrictive
Au XIXe siècle, l'industrie métallurgique ne peut plus se contenter d'appellations aussi approximatives, et la chimie a bien compris les enjeux liés à la métallurgie extractive. Les procédés de prétraitement des minerais sont rigoureusement identifiés. En 1878, Emmanuel-Louis Gruner définit le grillage comme une oxydation à haute température, par le moyen d'air, d'une matière minérale broyée[note 1] - [G2 1].
Si « l'agent oxydant par excellence est l'air », l'oxydation n'est pas exclusivement dépendante de son action. « On pourrait, à la rigueur, distinguer le grillage, dont l'action est due à l'influence exclusive de l'air, et le grillage dû à l'action combinée de l'air et d'un autre élément. Mais l'air, au fond, agit rarement tout à fait seul […] même dans les situations où l'air semble agir seul, l'oxydation se fait aussi d'une façon indirecte, par des oxydes ou certains acides ou sels. »[G2 3] Enfin, le grillage peut être réducteur : si l'emploi de ce terme dans ce contexte peut sembler abusif, il est néanmoins admis.
Pour autant, tous les métallurgistes constatent la proximité du grillage avec la calcination[SF 1]. Celle-ci est également une opération consistant à chauffer des manières minérales de façon à « éliminer un élément volatil, ou même simplement désagréger la matière minérale[G2 4] ». Si la confusion est fréquente en sidérurgie, c'est parce que beaucoup de minerais sont très facilement oxydables. Gruner établit ainsi qu'une calcination devrait être qualifiée de grillage dès qu'une oxydation a lieu, car « dès qu'il y a excès d'air dans l'appareil de calcination, les matières seront partiellement grillées »[G2 4].
Objectifs
L'inventaire des opérations de grillage d'un minerai fait apparaitre, indépendamment de l'appareil utilisé, trois types de réactions chimiques, combinées ou pas[SF 1] :
- la thermolyse (exemples : calcination des minerais carbonatés, déshydratation des minerais hydratés) ;
- le grillage métallurgique (exemple : retrait du soufre ou du zinc par oxydation) ;
- la suroxydation (exemple : transformation de la magnétite et hématite).
Bien entendu, dès que la chauffe commence, un séchage se produit, qui, dans le cas du grillage, se produit jusqu'à une dessiccation totale. Les gains liés à cette pratique étant évidents, il est tentant de penser que le grillage est apparu, historiquement, comme une tentative de pousser le séchage au-delà de la dessiccation afin d'en augmenter le bénéfice[SF 1].
Ainsi, hormis le cas du grillage suroxydant, un grillage entraine le retrait d'une certaine quantité de matière stérile, voire indésirable. Par conséquent, il se pratique très généralement sur les lieux même d'extraction : comme il entraîne une perte de masse qui peut atteindre 30 à 40 %, c'est autant de moins à transporter[SF 1] - [3]…
Thermolyse
La thermolyse se déroule pendant une chauffe sans réaction chimique avec un corps étranger au minerai. Elle consiste en une décomposition chimique du minerai due à la température. Dans la plupart des cas, la thermolyse des minerais est une calcination, c'est-à -dire une décarbonatation de la roche[note 2] :
La chauffe peut aussi entraîner une réaction de sublimation. Dans le cas de l'extraction du zinc, la chauffe des minerais provoque l'évaporation du zinc. C'est ainsi que, tout au long du XIXe siècle, récupération du métal s'est fait par condensation des vapeurs issues de la chauffe du minerai[4].
Déshydroxylation et déshydratation
Les réactions chimiques de déshydratation et de déshydroxylation sont généralement les premières à se produire lors de la chauffe d'un minéral. Ces réactions sont distinctes de la dessiccation, qui correspond au retrait de l'eau libre. L'objectif est cependant souvent le même : éliminer l'eau susceptible de se libérer lors des traitements postérieurs à haute température et dont le dégagement générerait des effets indésirables (explosion de vapeur, corrosion, réactions chimiques indésirables ou impossibles, etc.). De plus, le minerai sous forme anhydre est plus léger (par exemple, l'eau combinée dans la garniérite correspond à 30 % du poids à l'extraction), ce qui réduit le coût des manutentions comme des traitements[5].
Les réactions de déshydratation et de déshydroxylation se distinguent par la nature du groupe retiré[5] : MXn · m H2O (s) → MXn (s) + m H2O (g) réaction de déshydratation correspondant au retrait de l'eau combinée dans un hydrate 2 M(OH)n (s) → MOn (s) + n H2O (g) réaction de déshydroxylation correspondant au retrait de l'hydroxyde
Ainsi, par exemple, la chauffe de la limonite (Fe2O3.3H2O) entraîne une réaction de déshydratation, pour donner un composé anhydre, l'hématite (Fe2O3) : 2 Fe2O3.3H2O (s) → 2 Fe2O3 (s) + 2 H2O (g) dès que T > 330 °C (endothermique)
Une réaction de déshydroxylation partielle est obtenue par la chauffe de l'hydroxyde de fer(III) (bernalite) qui donne de l'oxyhydroxyde de fer(III) (goethite) selon la réaction : Fe(OH)3 (s) → FeO(OH) (s) + H2O (g) dès que T > 195 °C (endothermique)
Décarbonatation
La calcination correspond à une réaction de décarbonatation. Dans le cas le plus courant et le plus connu, il s'agit de transformer le calcaire en chaux (d'où le terme « calcination » qui vient étymologiquement de cette opération). Dans la métallurgie extractive, il s'agit de chauffer de la même manière les minerais carbonatés.
La réaction est toujours endothermique (à 900 °C, elle consomme 209 kJ/mol de CaCO3). Parmi les traitements de calcination les plus courants, on peut citer[6] :
- Décarbonatation de la sidérite (FeCO3) :
2 FeCO3 (s) → 2 FeO (s) + 2 CO2 (g) dès que T > 400 °C (endothermique[note 3])
- Décarbonatation de la rhodochrosite (MnCO3) :
2 MnCO3 (s) → 2 MnO (s) + 2 CO2 (g) dès que T > 377 °C (endothermique)
- Décarbonatation de la magnésite (MgCO3) :
2 MgCO3 (s) → 2 MgO (s) + 2 CO2 (g) dès que T > 417 °C (endothermique)
La chauffe d'une seule espèce chimique peut bien sûr générer plusieurs réactions distinctes de thermolyse. Beaucoup de minéraux complexes, comme la malachite (Cu2CO3(OH)2), subissent successivement une déshydratation puis une décarbonatation[7] : 2 Cu2CO3(OH)2 (s) → 2 Cu2CO3 (s) + O2 (g) + 2 H2O (g) dès que T > 95 °C 2 Cu2CO3 (s) + O2 (g) → 4 CuO (s) + 2 CO2 (g) + 2 H2O (g) dès que T > 350 °C L'ensemble de ces deux réactions produit 150 kJ/mol de Cu2CO3(OH)2
Autres décompositions chimiques
Une réaction de désulfatation est une possibilité qui suit les mêmes principes que la calcination. Par exemple, dans le cas de la jarosite (KFe3(SO4)2(OH)6), plusieurs réactions de dissociations se succèdent ainsi[8] : Déshydroxylation : 2 KFe3(SO4)2(OH)6(s) → K2SO4⋅Fe(SO4)3(s) + 2 Fe2O3 (s) + 6 H2O (g)[note 4] pour T de 350 à 500 °C (endothermique) Dissociation : K2SO4⋅Fe(SO4)3(s) → K2SO4(s) + Fe2(SO4)3 (s) pour T d'environ 500 °C (exothermique) Désulfatation : Fe2(SO4)3(s) → Fe2O3(s) + 3 SO3(g) pour T d'environ 750 °C (endothermique) Dissociation : K2SO4(s) → K2O(s) + SO3(s) pour T d'environ 1 100 °C (endothermique)
Grillage
Le grillage proprement dit consiste en la chauffe en présence d'air. Bien sûr, la teneur en oxygène et la température sont très variables selon les réactions chimiques recherchées. On distingue plusieurs types de grillages. Le « grillage à mort » doit être distingué du « grillage partiel ». En effet, le grillage s'intégrant généralement dans un processus d'extraction de minerais complexes, le grillage peut être interrompu pour un traitement intermédiaire. Enfin, les « grillages suroxydants » sont particuliers puisqu'ils cherchent à enrichir en oxygène au lieu de retirer des éléments indésirables[9].
Grillage Ă mort
Le grillage à mort correspond au retrait de tous les composés susceptibles de réagir avec l’air chaud, pour aboutir à des états d'oxydations maximaux. Un cas typique est le retrait du soufre dans la métallurgie extractive du zinc ou du cuivre :
2 ZnS (s) + 3 O2 (g) → 2 ZnO (s) + 2 SO2 (g) dès que T > 900 °C et produisant 440 kJ/mol de ZnS
- Désulfuration de la chalcopyrite (CuFeS2)[11] :
2 CuFeS2 (s) + 4 O2 (g) → 2 FeO (s) + Cu2S (s) + 3 SO2 (g) dès que T > 700 °C et produisant 1 030 kJ/mol de CuFeS2 Cu2S (s) + 2 O2 (g) → 2 CuO (s) + SO2 (g) dès que T > 700 °C et produisant 329 kJ/mol de Cu2S
Grillage partiel
Le grillage partiel ne va pas pousser aussi loin l'oxydation du composé. Pour les fours modernes, une telle opération ne signifie aucunement un manque d'efficacité, mais s'inscrit dans tout le processus d'extraction. Typiquement, le grillage partiel correspond au retrait de la totalité d'un composant indésirable, comme l'arsenic ou l'antimoine, sans en retirer tout le soufre qui sera utile aux réactions suivantes[9].
- Le grillage de l'énargite se fait à moins de 625 °C car cette température est suffisante pour retirer tout l'arsenic présent dans le minerai, évacué sous la forme d'anhydride arsénieux gazeux (As2O3)[12] :
2 Cu3AsS4 (s) + 13 O2 (g) → 2 As4O6 (g) + 6 Cu2S (g) + 10 SO2 (g) pour 375 °C < T < 625 °C et produisant 44 kJ/mol de Cu3AsS4 Il serait tout à fait possible de pousser le grillage au-delà de cette température et de pousser l'oxydation du cuivre, avec une deuxième étape 6 Cu2S (s) + 9 O2 (g) → 6 Cu2O (s) + 6 SO2 (g) et une troisième 6 Cu2O (s) + 3 O2 (g) → 12 CuO (s). Mais ces deux dernières oxydations sont exothermiques et sont plus avantageusement réalisées dans un four de fusion flash qui exploite la chaleur dégagée par ces réactions afin de réaliser une fusion du cuivre[12]. Surtout, il ne faut pas perdre de vue que l'objectif industriel est d'oxyder l'arsenic afin de l'évacuer sur la forme de composé gazeux, et non d'oxyder le soufre qui est le carburant des réactions ultérieures de fusion. Un moyen courant de privilégier la dissociation de l'énargite par rapport à l'oxydation du soufre consiste à préchauffer l'air ou à l'enrichir en oxygène[13].
Grillage suroxydant, ou éventuellement réducteur
La particularité du grillage suroxydant est qu'il n'est pas destiné à évacuer des éléments sous forme gazeuse. L'oxyde final est plus lourd que l'oxyde de départ.
- Sulfatation du monosulfure de cuivre (ou de cobalt)[14] :
CuS(s) + 2 O2(g) → CuSO4(s) dès que T > 650 °C (exothermique)
- Transformation de la magnétite en hématite, plus réductible au haut fourneau[8] - [SF 1] :
4 Fe3O4(s) + O2(g) → 6 Fe2O3(s) dès que T > 450 °C et produisant 188 kJ/mol de Fe2O3
2 NiS(s) + 3 O2(g) → 2 NiO(s) + 2 SO2(g) pour T > 1 050 °C (exothermique)
Dans certains cas, on qualifie de « grillage réducteur », la chauffe de produits métallurgiques intermédiaires dans une ambiance réductrice. Qualifier de grillage une réaction de réduction peut sembler abusif mais, comme les éléments indésirables sont évacués à l'état gazeux, faute de terme dédié, l'emploi du mot dans ce contexte est admis[15].
- Grillage du NiO (lui-même issu du grillage oxydant du NiS, voir plus haut) en nickel métal, dans une atmosphère réductrice obtenue par combustion partielle de kérosène (H2C)[15] :
2 H2C(l) + O2(g) → 2 CO(g) + 2 H2(g) pour T > 1 000 °C et 2 CO(g) + NiO(s) → 2 Ni(s) + 2 CO2(g) pour T > 1 000 °C
Altération physique

Le grillage est utile pour modifier la nature des minerais rocheux. En effet, ceux-ci sont compact et les gaz (ou les liquides) y pénètrent difficilement, ce qui ralentit leur traitement ultérieur. Ils peuvent être également durs, ce qui rend coûteux leur concassage et leur broyage. Dans ce cas, le grillage a pour objectif de rendre les minerais poreux et désagrégeables[SF 1] - [G2 1].
Bien entendu, cet intérêt est inexistant dans le cas des minerais pulvérulents. Ces minerais sont grillés par des procédés qui tirent parti de leur nature pulvérulente (cas des réacteurs à lit fluidisé), ou sont traités par des grillages agglomérants dont la haute température génère un frittage (grillage sur chaine en usine d'agglomération)[SF 1].
L'effet de la chaleur sur les minéraux est connu depuis le néolithique, pendant lequel les foyers sont utilisés pour venir à bout des pierres dures. La pratique se généralise pendant l'âge du bronze ancien avec le dépilage par le feu, qui utilise la dilatation thermique pour fracturer les roches exposée au feu. Cette technique primitive perdure au cours de l'histoire elle est citée dans la Bible[note 5] et détaillée pendant la Renaissance. Elle est efficace sur les roches dures, comme les quartz et les basaltes. Combinée avec les transformations chimiques dues à la chaleur et à l'oxygène, elle est d'un emploi général dès que le combustible est abondant[16].
Procédés
Grillage en tas
Très semblable à la fabrication de charbon de bois en meule, la méthode consiste à mélanger du minerai avec du combustible, et à mettre le feu à l'ensemble. Étant donné les pertes thermiques, le procédé n'est adapté qu'aux minerais qui contiennent naturellement du combustible. Le minerai de fer houiller est celui qui se prête mieux à cette opération. Ce procédé primitif disparaît lorsque les derniers gisements de ce type sont épuisés, à la fin du XIXe siècle[G2 5]. Il est alors rarement recommandé :
« On calcine en tas libres, sans se préoccuper des pertes de chaleur, la plupart des minerais qui contiennent en eux-mêmes l'élément combustible. […] La consommation en combustible est […] le double de la consommation des fours à cuve. Aussi ne devrait-on jamais calciner en tas les minerais non bitumeux[G2 5]. »
— E.-L. Gruner, Traité de métallurgie
Pour griller en tas, on étale au préalable une couche de combustible sur une aire plane (ou, plus rarement, divisée en stalles cases ou fosses[G2 6]), sur laquelle on constitue le tas de minerai à griller. Si le minerai contient une quantité insuffisante de combustible, on ajoute une petite strate de houille ou d'un autre combustible bon marché, généralement du bois. Sur le sol, on arrange verticalement les blocs de minerai les plus grossiers, de manière à créer des carnaux pour l'arrivée de l'air. Le tas est recouvert d'une couche de minerai fin qui en se comportant comme une couverture étanche, va modérer le tirage[note 6]. Mais quelle que soit la science avec laquelle l'aérage du tas est préparé, la combustion est irrégulière : « On ne peut, en effet, jamais régler le feu d'une façon uniforme car l'opération dépend entièrement de l'état de l'atmosphère[G2 5]. » Le résultat est que le grillage est généralement plus poussé que nécessaire[G2 5] - [G2 8], mais il reste impossible d'effectuer en une seule opération un grillage complet d'un minerai par la méthode des tas, le centre étant toujours moins grillé que les bords à cause d'une arrivée d'air insuffisante. Ainsi, avec cette méthode, le grillage désulfurant des minerais et des mattes cuivreuses doit être recommencé jusqu'à dix fois pour être complet[G2 9].
Les tas eux-mêmes ont généralement la forme de pyramides tronquées à base carrée, ou de prisme triangulaire. La longueur est variable, la base fait de 5 à 10 mètres, et la hauteur varie de 1 à 4 mètres selon la nature du minerai[G2 5]. Les plus gros tas atteignent 40 à 60 mètres de long, de 6 à 11 mètres de large et environ 5 mètres de haut[17], leur grillage durant de un mois[3] à deux-trois mois et parfois davantage[G2 8].
Les minerais de fer riches en soufre (pyrites), ou les minerais sulfurés de cuivre (chalcopyrites) peuvent également être grillés en tas car l'oxydation du soufre est suffisamment exothermique pour s'entretenir toute seule. Mais générant une pollution insupportable quelle que soit l'époque, cette méthode n'a été pratiquée qu'à petite échelle et dans des endroits déserts (comme l'ouest des États-Unis dans la première moitié du XIXe siècle)[G2 10]. Ainsi, le grillage en tas a toujours été critiqué à cause de la pollution qu'il génère :
« Le grillage en tas libre est l'enfance de l'art. On perd non seulement beaucoup de chaleur, mais encore à peu près complètement, les éléments volatils, le soufre, l'arsenic, etc. Outre cela, ce mode de grillage cause de graves dommages aux propriétés voisines. En tous cas, c'est une source d'ennuis pour les habitants des environs. On ne peut échapper au paiement de sérieuses indemnités[G2 11]. »
— E.-L. Gruner, Traité de métallurgie
Enfin, le grillage en tas est impossible aux matériaux qui se ramollissent en chauffant, « sinon il en résulterait un prompt empâtement qui arrêterait le tirage »[G2 12].
- Grillage du minerai de cuivre en stalle, une variante améliorée du grillage en tas.
Four à réverbère
Le four à réverbère est particulièrement adapté au grillage de matières pulvérulentes, qui se feraient entraîner par le courant de gaz si elles étaient traités dans un four à cuve[G2 13], et aussi parce que leur perméabilité est insuffisante[G2 12]. Mais si la méthode a dominé à la fin du XIXe siècle, elle était déjà démodée au début du XXe siècle. En effet, le contact entre l'atmosphère chaude et oxydante étant relativement faible, le grillage y est lent et incomplet, même si la charge est régulièrement retournée[SF 1].
Le grillage au four à réverbère consiste à étendre sur la sole d'un four une couche de 8 à 10 cm d'épaisseur et la brasser (à la main au XIXe siècle, puis automatiquement au début du XXe siècle, comme dans le four Edwards). Comme seule la couche supérieure est soumise au grillage oxydant, un pelletage à main ou un râblage mécanique est nécessaire, mais cela reste souvent insuffisant pour réaliser un grillage rapide et complet. De plus, les gaz qui résultent du grillage (gaz sulfureux, oxydes de zinc, etc.) ne sont pas chassés vigoureusement du lit de matière et ont tendance à rester dans les espaces entre les grains (par adsorption), ce qui pénalise la progression de l'oxydation[SF 1]. Pour autant, ce phénomène est beaucoup moins pénalisant dans les fours à réverbère que dans les autres procédés (four à cuve, grillage en stalle ou en tas, etc.) puisque les gaz quittent plus rapidement la charge. Par sa flexibilité, le four à réverbère, qui permet un réglage de la température indépendant du degré d'oxydation, est un outil apprécié pour la désulfuration des minerais[G2 14].
Les fours à réverbère présentent tout de même l'inconvénient d'un mauvais rendement thermique[G2 15]. Pour l'améliorer et faciliter l'accès à la charge, la sole des fours de grillage est longue et étroite. Au XIXe siècle, celle-ci mesure au moins 10 mètres de long pour au plus 2 mètres de large. On y distingue deux zones : celle de chauffe, à proximité du pont de feu (ou autel), et celle du laboratoire, où la matière se réchauffe lentement, qui est 15 à 20 fois plus étendue. Les matières sont poussées le long de la sole, de la cheminée vers le foyer. Pour faciliter leur mouvement, la sole est donc parfois inclinée, ou est conçue pour un écoulement en cascade (four à tablettes). Pour avoir un grillage oxydant, on augmente les arrivées d'air. L'air froid, plus dense, circule sous les fumées, au contact de la charge qu'il oxyde. Mais si on compte traiter les fumées (par exemple pour en récupérer le soufre), l'excès d'air doit être limité[G2 13]. Dans ce cas, le retournement fréquent du produit étalé sur la sole doit se faire de manière mécanisée, sinon l'accès à la charge entraîne des entrées d'air récurrentes. Beaucoup de systèmes ont été proposés, des four à tablettes inclinées dans lequel la charge tombe en cascade (fours de Hasenclever (de)) aux fours dotés de systèmes de râblage mécaniques[G2 16].
À l'instar de la plupart des procédés de grillage, le frittage doit être évité afin de permettre une manutention facile des matières. Mais pour le grillage des minerais de plomb, il est fréquent que le frittage, voire la fusion, soient réalisés dans le même four[G2 17] - [note 7]
- Four à réverbère utilisé en 1883 pour le grillage de minerai de plomb. Il est alors qualifié de conception moderne.
- Four à réverbère utilisé pour le grillage du minerai d'argent, commercialisé en 1897 par l'Anaconda Mining Company.
- Four à réverbère à sole inclinée de 18° (four Ferraris), utilisé pour la calcination des calamines menues au début du XXe siècle.
- Four à réverbère à soles multiples (four à tablettes), utilisé à la fin du XIXe siècle pour le grillage de minerai de plomb sulfureux. La charge passe successivement de la sole supérieure à la sole inférieure, circulant dans le sens inverse des fumées.
- Vue en coupe du système de râbles tournantes du four Edwards, tel qu'utilisé en 1921.
Four Ă cuve
Les fours à cuve ont un excellent rendement à cause de leur fonctionnement à contre-courant (les gaz chauds montent et les matières froides descendent). Ce rendement croit avec la taille, notamment avec la hauteur, du four : au début du XiXe siècle, les fours à cuve mesurent de 5 à 10 mètres de haut[G2 19]. Mais ils ne sont compatibles qu'avec une matière perméable à haute température : si elle devient friable, on doit limiter leur hauteur et donc leur rendement. Si le minerai est fin ou colmatant, le fonctionnement est impossible[G2 20].
Les fours de grillage à cuves peuvent être distingués selon le type de combustion qui y est réalisé : les fours à combustible solide, ceux à combustible gazeux et ceux à fumée oxydante ou à air chaud[G2 5] :
- les combustibles solides riches en éléments volatils, comme le bois et la houille, subissent une carbonisation qui absorbe la chaleur : ils sont peu adaptés au grillage. La combustion est plus difficile, car gênée par la proximité avec la matière à griller, qui est froide. Par ailleurs, les gaz dégagés sont souvent réducteurs (comme le monoxyde de carbone et l'hydrogène) et vont réduire la charge au lieu de l'oxyder. Ces gaz ont aussi l'inconvénient d'être combustibles et vont brûler généralement en partie haute, hors des zones où se déroule le grillage. Enfin, les cendres polluent la charge en se mélangeant avec elle. Avec des combustibles plus énergétiques, comme le coke, on risque chauffer excessivement la charge, provoquant un frittage, voire une fusion partielle de la charge, pouvant mener à un engorgement ou un blocage[G2 21] - [G1 1] ;
- les combustibles gazeux (et aussi liquides, mais les exemples industriels sont rares) ont l'avantage d'être aisés à manipuler et à brûler. On peut avantageusement valoriser des gaz pauvres, comme le gaz de haut fourneau. Même dans ce cas, ils permettent de meilleures productivité que les combustibles solides[G2 22] ;
- l'emploi de l'air chaud, obtenu par un échangeur ou un four de type cowper présente les avantages de se libérer de toutes les contraintes induites par le combustible, mais un réchauffeur d'air est une installation supplémentaire dont le coût est difficilement amorti[G2 23].
On distingue également les fours par leur conception. Dans les « fours à grilles », la charge est supportée par une grille horizontale qui laisse passer l'air. La chauffe est plus homogène que dans les « fours à ouvreaux », où les orifices latéraux servent à la fois à l'évacuation des charges et à l'amenée de l'air. Les fours à ouvreaux sont d'une conception plus simple, mais il est parfois nécessaire de multiplier les orifices jusqu'à mi-cuve pour assurer une bonne arrivée des gaz, sans pour autant garantir l'efficacité des réactions au centre de la cuve[G1 2] - [note 8].
Équilibrer les réactions entre le centre de la cuve (où la chaleur se concentre mais où les gaz accèdent difficilement) et la périphérie (où les charges sont bien ventilées mais refroidies par les parois) est possible par une modification des formes du four. Certains fours sont ainsi elliptiques pour éviter l'apparition d'une zone centrale trop chaude. Plus simplement, on peut adopter une forme évasée qui favorise l'écoulement dans l'axe du four. En partie haute, la forme évasée ralentit aussi les vitesses, favorisant la restitution de la chaleur des gaz à la charge fraîchement enfournée. La partie basse des fours à ouvreaux étant souvent encombrée en son centre par une masse de matière inerte, on réalise un rétrécissement de la cuve, voire un cône central, pour mieux retirer les matières[G1 3].
- Four Ă griller le minerai de fer Ă Saint-Pierre-d'Allevard.
- Four à chauffe latérale utilisé en 1860 pour le grillage du minerai de zinc. La production des fumées oxydantes se fait à côté de la cuve.
- Four à ouvreaux du suédois Westmann. Du gaz de haut fourneau et de l'air sont introduits à des endroits distincts, la combustion se déroule en partie basse.
- Four Ă grille pour le grillage du minerai de zinc Ă Monteponi (it)
- Four du suédois Gjers, dont le cône et le rétrécissement à la base facilitent l'extraction des matières.
Four Ă soles multiples
Les premiers fours à sole tournante n'étaient équipés que d'une seule sole. D'après Gruner, ils semblent être tous inspirés de celui de l'inventeur écossais William Brunton[G2 24], qui en brevette le principe le [18]. Ils ont été mis au point et utilisés dans les Cornouailles pour le grillage de minerai d'étain (cassitérite) à gangue d'arsénopyrite. Jusqu'à leur abandon, en 1950, au profit de procédés de flottation par moussage, ils s'y sont révélés efficaces[19]. En 1860, Parkes invente le four à soles multiples, qui est ensuite régulièrement amélioré par ses concurrents[20].
Les fours à soles multiples modernes mesurent de 2 à 8 m de diamètre, et disposent de 3 à 16 soles. Des râbles posées de biais retournent le produit et le déplacent radialement sur la sole, afin de l'évacuer sur la sole inférieure. Ces fours, bien adaptés aux grillages exothermiques, ont été la technologie dominante pour le grillage des pyrites jusque dans les années 1960. À cette époque, ils ont été brutalement dépassés par les fours à lit fluidisé, qui permettent des productions plus élevées et une meilleure maîtrise de l'oxydation. Mais comme les fours à soles multiples permettent des grillages lents faisant intervenir de faibles quantités de gaz, ils restent encore utilisés, au début du XXIe siècle, pour le grillage de la molybdénite (grillage exothermique du MoS2 en MoO3 à 630 °C), ainsi que des laitiers contenant du vanadium ou du tungstène (grillages généralement endothermiques)[21].
- Four de Brunton.
- Plan d'un four de Herreshoff[note 9] utilisé pour le grillage de chalcopyrite.
- Fours de MacDougal, pour le grillage de chalcopyrite Ă l'usine de Washoe de l'Anaconda Copper en 1920.
- Plan d'un four de MacDougal de la Tooele Smelter.
Four Ă tambour rotatif
Le principe du four rotatif est ancien. En tant que four de grillage, il apparait en mars 1867 dans le Nevada, pour le grillage des sulfures argentifères. Ce premier modèle, conçu par William Bruckner[note 10], consiste en un court four d'axe horizontal, qui marque ses contemporains par ses performances économiques et sa capacité à traiter les minerais les plus complexes[22]. Les modèles commercialisés par la suite sont capables de traiter des lots de 2 tonnes de minerai en 5 heures. Aussi efficace qu'économe en personnel, il est encore, à cette époque, considéré comme d'une conception plus exigeante que les technologies alternatives[G2 25].
Le succès de Bruckner inspire les inventeurs américains, qui reprennent le principe du four tambour en l'améliorant. John White tente d'en faire un four continu en l'inclinant : les minerais sulfurées entrent d'un côté et sortent de l'autre, les gaz circulant à contre-courant. Mais les fumées entrainent les fines de minerai, qui doivent être grillées par un feu auxiliaire situé dans le carnau[24]. C'est John Howell qui, vers 1870, finalise la mise au point du four de White en l'allongeant et en associant ces deux foyers. Le four de grillage continu White-Howell est enfin au point et surclasse alors le four de Bruckner[22], tandis que Philip Argall propose un four original à quatre cylindres, mais dont le seul intérêt réside dans la faible puissance nécessaire à sa rotation[25].
À la même époque, le four Smidth est mis au point pour le grillage du minerai de fer. Il est lui aussi plus élancé que le four Bruckner : il est long de 8 m contre 4 m, et d'un diamètre de 1,2 m contre 1,7 m)[SF 2]. Le four Smidth, comme ses équivalents, évolue et s'avère apte au fonctionnement en continu. Dans les années 1960, les fours Smidth utilisés en sidérurgie atteignent 100 m de long pour 4 à 6 m de diamètre, et grillent plus de 700 tonnes/jour de poussières de haut fourneau. Ils utilisent le gaz de haut fourneau, peuvent retirer le zinc contenu dans les poussières et réalisent un bouletage du minerai fin[SF 3].
Au début du XXIe siècle, ces fours sont courants dans les procédés non métallurgiques, voire systématiques dans le cas de la production du ciment. Mais dans la métallurgie extractive, ils ont reculé face aux autres procédés adaptés au traitement de minerais fins. Pour le grillage des minerais de fer, ils y sont abandonnés dans les années 1970 au profit des procédés sur chaîne, capables de plus fortes productions et réalisant une oxydation plus poussée[SF 4]. Dans les procédés non sidérurgiques relatifs aux minerais fins, comme le grillage exothermique des minerais sulfureux ou la déshydratation (endothermique) de l'ilménite et des roches phosphatées, ils ont été remplacés par les fours à lits fluidisés[26]. À cause de leur rendement thermique défavorable (pour la production de chaux, ils consomment 5 020 à 5 440 MJ/tonne contre 3 350 MJ/tonne pour un four à cuve), leur emploi ne se justifie que dans des cas très précis[6], comme les matériaux de granulométrie dispersée ou qui se dégradent pendant l'opération[27].
- Four tambour de Bruckner, fabriqué par les Chicago Iron Works en 1905, et utilisé dans le Montana pour le grillage de minerais de cuivre.
- Four tambour de Bruckner
- Four tambour Howell-White, fabriqué par l'Anaconda Copper en 1897, et utilisé pour le grillage désulfurant de minerais d'argent.
- Four tambour d'Argall constitué de 4 tubes satellites, à Cripple Creek en 1902. D'une capacité de 45 à 50 t/24h, ils réduisent la teneur en soufre du minerai d'or de 2 à 0,10 %. Un moteur de 1 CV entraîne l'ensemble.
Four à lit fluidisé
En 1867, Carl August Stetefeldt (en) brevette un four qui fonctionne sur la chute libre de minerai fin dans un courant ascendant de fumées chaudes et oxydantes. Ce four, qui préfigure les fours à lit fluidisé, est critiqué car il n'est efficace que si la granulométrie est maîtrisée[G2 26]. Mais il est un succès aux États-Unis où il sert au grillage du minerai d'argent[28]. Quelques années après, Florian Joseph Gerstenhöfer lui ajoute une série de barreaux disposés en chicane, qui ralentissent la chute pour augmenter la durée du grillage[G2 27] - [SF 5].
- Four de grillage de Stetefeldt, fonctionnant sur la chute libre de minerais fins.
- Four de grillage de Gerstenhöfer, ou four à cascade, utilisé pour le grillage de la blende.
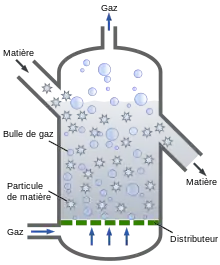
En 1950, la société allemande Lurgi (de) met en service le premier four de grillage à lit fluidisé. La technologie se répand rapidement. Le procédé se révèle efficace pour le grillage des pyrites, des blendes, des minerais d'or, des mattes de cuivre, pour le grillage pour la pyrohydrolyse des chlorures de nickel, etc.[14]. Le procédé a l'avantage d'être continu et fermé. Outre les avantages écologiques, il est facile de garantir une production de fumée constante en qualité comme en quantité, afin d'en récupérer la chaleur sensible et le soufre. Ainsi, au XXIe siècle, la technologie est encore parfaitement moderne et même recommandée en tant que meilleure technique disponible par la Commission européenne[29].
Le principe du lit fluidisé est avantageux pour améliorer les échanges thermiques solide-gaz, et notamment, dans le cas des sulfures, pour éliminer le SO2 en maintenant une basse pression partielle de SO2 autour des particules. Si les réactions présentent une exothermicité élevée, il peut fonctionner de façon autogène. Sinon, le combustible (charbon pulvérisé, fuel) est injecté dans le réacteur avec le minerai broyé ou avec l'air. La conduite du four demande une bonne maîtrise de la thermique et de la granulométrie pour éviter la prise en masse du minerai, problème auquel ces fours sont parfois confrontés[6].
Grillage sur chaîne ou grille
En 1897, le premier procédé de grillage sur des barreaux à travers lesquels les gaz étaient aspirés, pour brûler une charge minérale contenant un combustible, est breveté par Thomas Huntington et Ferdinand Heberlein (de). Ce grillage de blende se fait dans des cuves fixes, et la température est soigneusement contrôlée pour éviter le frittage de la charge[note 11]. À partir de cela, Wolfgang Job développe l'agglomération de fines de minerais ou, plutôt, de poussières de gaz de haut fourneau. Mais c’est au début du XXe siècle, entre 1907 et 1911, qu'Arthur Smith Dwight et Richard Lewis Lloyd inventent la « chaîne droite continue » pour griller des minerais sulfurés, ou agglomérer des fines ou poussières de minerais de fer, voire des résidus d’usines sidérurgiques[SF 1] - [31].
Le fonctionnement en dépression est une innovation majeure. Cet avantage, combiné avec le fait que le procédé est continu, assure la popularité du procédé Dwight-Lloyd :
« Non seulement ce procédé a baissé les coûts et amélioré l'opération dans tous les sens métallurgiques du terme, mais les conditions d'exploitation peuvent être de très loin meilleures, du point de vue de l'hygiène, à n'importe quel autre procédé équivalent[32]. »
— A. Hamilton & R. Meeker, Lead poisoning in the smelting and refining of lead
- Pot Huntington-Heberlein utilisé en 1914 pour le grillage de blende. Le pot photographié ici fonctionne avec un flux d'air ascendant[30].
- Principe de fonctionnement du procédé Dwight-Lloyd.
Bien que de nombreuses tentatives furent faites pour élaborer d’autres technologies, supposées être moins coûteuses pour des capacités de production limitées (procédés Greenawalt, AIB, GHH, etc.) la chaîne droite continue est devenue rapidement le seul type de machine utilisée pour l’agglomération sur grille des minerais de fer[31].
Dans le cas du grillage des matières sulfureuses, les fumées aspirées sous la chaîne sont renvoyées, après dépoussiérage, au-dessus, de manière à fonctionner en circuit fermé. Ce recyclage des fumées pénalise l'oxydation, mais il permet d'enrichir les fumées en SO2 afin de faciliter leur traitement[33]. Cette technique commence à être employée en sidérurgie, où elle permet de limiter les émissions polluantes d'une usine d'agglomération de minerai de fer de 25 %[34].
Cornues, fours Ă moufle, fours clos
Lorsque l'on veut éviter le contact avec la flamme, ou traiter au mieux les fumées, on dissocie l'enceinte où se produit la combustion de celle où est traitée le minerai. Les fours à moufle[note 12] et les creusets ont ainsi été utilisés. Ces fours sont fréquents lorsque les gaz ont de la valeur, comme dans certains grillages des minerais de zinc où le métal est justement récupéré à l'état d'oxyde gazeux. Par contre, bien qu'on les qualifie fréquemment de four de grillage, l'oxydation par l'air est quasiment absente, la transformation de la matière recherchée se limitant à la sublimation[4].
- Four à creusets penchés, ou « four belge », utilisé pour l'évaporation-condensation du zinc, tel qu'utilisé à la Vieille-Montagne vers 1840.
- Détail d'un creuset de four belge, avec son allonge renflée où se produit la condensation du zinc.
- Four à creusets verticaux, ou « four anglais », utilisé pour l'évaporation-condensation du zinc à la fin du XIXe siècle.
- Four à moufles, ou « four silésien », utilisé pour l'évaporation-condensation du zinc à la fin du XIXe siècle.
On peut arriver à des fours complètement clos, comme les cornues, pour récupérer la totalité des gaz émis lors de la chauffe. Lorsqu'il s'agit de séparer le plomb du zinc, on rencontre fréquemment, au début du XXe siècle, la cornue inventée par Adolf von Faber du Faur : la chauffe permet l'évaporation complète du zinc, qui est récupéré par condensation, le plomb étant ensuite coulé par basculement de la cornue[35] - [36].
- Cornue de Faber du Faur, utilisée au début du XXe siècle.
- Four Faber du Faur en chauffe, en 1914. Devant le bec de la cornue, on a fixé un pot dans lequel se condense le zinc vaporisé.
Four annulaire
En 1858, Friedrich Hoffmann brevète un four annulaire destiné à la cuisson des briques et des tuiles. Très populaire et atteignant des dimensions considérables, ce four s'est avéré efficace dans l'opération de grillage. Le four Hoffmann est un anneau divisé en compartiments fixes, et le feu progresse d'un compartiment à l'autre. L'air entre en un point de l'anneau, parcourt les 2/3 de la circonférence en s'échauffant au contact des matières déjà grillées et réagit avec le compartiment chargé en combustible. Les fumées chaudes générées par la combustion continuent leur chemin, restituant leur chaleur aux compartiments suivants qui sont chargés en matière non grillée, avant de s'échapper par la cheminée centrale[G1 4].
Pour la calcination des minerais carbonatés de fer et de zinc, le four Hoffmann permet une économie de combustible allant jusqu'à 50% par rapport aux fours à cuve à combustible solide. Mais, plus optimisé pour la chauffe que pour l'oxydation, ce four est resté, en tant que four de grillage, assez marginal. Pour cet usage, quelques modifications mineures sont nécessaires car la décarbonatation du calcaire ou des minerais génère un tassement de la charge. Un vide se forme alors entre la voûte et la charge, et les gaz empruntent ce vide au lieu de circuler au sein de la charge. On crée donc des diaphragmes obstruant le tiers supérieur de la voûte, afin de contraindre les gaz à passer au travers de la charge[G1 4].
- Grand four ovale de Hoffman, près de Zehdenick.
- Plan simplifié d'un petit four circulaire de Hoffman.
Impact environnemental
Le grillage produit de grandes quantités de fumées, composées de vapeurs acides transportant des poussières d'oxydes et de sulfures de plomb, d'antimoine, d'arsenic, d'argent[G2 28]… Aux États-Unis, au début du XXe siècle, les industriels américains qualifiaient alors de smoke farming l'activité des agriculteurs consistant à leur intenter des procès, en leur imputant la responsabilité des pluies acides dues au traitement des minerais et des mattes de cuivre riches en soufre[note 13]. Le traitement des fumées n'est alors guère pratiqué : « Plutôt que de subir un tel racket, les fondeurs trouvaient plus économique de, soit acheter les fermes voisines, soit les cultiver eux-mêmes, ou de les louer en se couvrant par une clause relative aux fumées. »[38].
Le durcissement des normes environnementales a condamné les installations les plus sommaires, qui n'ont d'ailleurs jamais été acceptées, mêmes quand elles se limitaient à l'échelle artisanale. Historiquement, en l'absence de système moderne d'aspiration des fumées, les meilleures pratiques ont consisté à :
- limiter la quantité de fumées en réduisant l'air nécessaire au grillage… un excès d'air impliquant également une consommation inutile de combustible ;
- maîtriser la quantité de fumées en limitant les entrées d'air parasites, des fumées abondantes et diluées étant plus difficiles à traiter ;
- condenser les fumées, en les faisant cheminer dans de longs carneaux ;
- obtenir un dépoussiérage statique, par des pièges à poussières dans les carneaux ;
- prévoir une très haute cheminée (d'au moins 60 m de haut, si ce n'est le triple), qui augmente le tirage et disperse les polluants.
La généralisation des ventilateurs de dépoussiérage permet d'installer des systèmes bien plus performants :
- le lavage des fumées [G2 28];
- la filtration avec des filtres à manches et des électrofiltres[38].
Notes et références
Notes
- Lorsque la matière se présente en gros fragments, il nomme l'opération « cémentation oxydante » ou « rôtissage »[G2 1]. Cette distinction est tombée en désuétude lorsque le broyage s'est généralisé, car il permet des réactions à la fois plus rapides et plus faciles à contrôler, et lorsque des procédés plus efficaces que ceux fondés sur des réactions solides-gaz ont été mis au point[G2 2].
- Étymologiquement, la calcination est la transformation du calcaire en chaux par chauffage dans un four à chaux.
- La décarbonatation de la sidérite (FeCO3) en wustite (FeO) est généralement suivie d'une oxydation en hématite (Fe2O3). La réaction globale est alors : 4 FeCO3 (s) + O2 (g) → 2 Fe2O3 (s) + 4 CO2 (g) produisant 63 kJ/mol de FeCO3[SF 1]
- Cette équation n'est pas équilibrée. Elle est en effet supposée produire de l'hématite (Fe2O3), oxyde de fer le plus courant et le plus stable à T < 500 °C. Si on admet que l'oxyde de fer produit est un mélange de wustite (FeO) et de fer pur, la réaction s'équilibre naturellement : 2 KFe3(SO4)2(OH)6(s) → K2SO4⋅Fe(SO4)3(s) + Fe5O2 (s) + 6 H2O (g)
- On relève des exemples dans le livre de Job, ainsi que dans le livre de Jérémie 23,29 : « Ma parole n'est-elle pas comme un feu et comme un marteau qui brise le roc ? »[16]
- Cette couche, nommée la « couverte » par Gruner, peut être gérée de manière à rester froide durant l'opération. Les fumées s'y condensent alors, et il devient possible d'y récupérer une fraction du soufre, de l'arsenic ou du mercure qui sinon seraient dispersés dans l'atmosphère. Au XIXe siècle la récupération de ces produits se justifie que par leur valeur à la vente. En effet, les quantités récupérées, de l'ordre de quelques pourcents des quantités ôtées par le grillage, ne réduisent pas la pollution de manière mesurable[G2 7].
- Le grillage des minerais sulfureux de plomb est complexe. Si l'oxydation est trop vigoureuse, il se forme du sulfate de plomb(II) (PbSO4), qui est infusible et difficilement oxydable. On le réduit alors en le mélangeant avec une matière carbonée (coke, houille, etc.) : PbSO4 (s) + C (s) → PbO (s) + SO2 (g) + CO2 (g). Cette méthode consistant à alterner les chauffes oxydantes et réductrices permet aussi de se débarrasser de l'arsenic et du zinc présents dans le minerai[G2 18].
- Le fait que les réactions soient moins vigoureuses au centre de la cuve qu'à proximité des parois n'est pas forcément un inconvénient dans le cas du grillage. En effet, si l'écoulement était strictement homogène, la température serait plus élevée au centre que sur les parois. Or, contrairement au haut fourneau, le grillage doit éviter le frittage et la fusion des matières, il existe une température maximale à ne pas atteindre[G1 3]
- Les fours à soles multiples d'Herreshoff, MacDougal sont très semblables. Les différences se limitent à des dispositions constructives. Par exemple, le four de Herreshoff est identique à celui d"Evans-Klepetko, sauf que les bras et la cuve sont refroidis à l'air au lieu de l'eau[20].
- William Bruckner, en réalité Wilhelm H. Bruekner, est un ingénieur allemand, formé à la chimie à Göttingen, et à l'extraction minière à Freiberg. Il émigre de la Saxe vers le Pérou et la Bolivie, où il reste 8 ans, avant d'arriver en 1868 aux États-Unis, âgé de 28 ans. Il s'installe à Georgetown pendant le boum en argent du Colorado, au sein d'une communauté allemande d'experts en métallurgie extractive. Remarquable chercheur, il est à l'origine du développement des fours rotatifs en métallurgie[22]. Il meurt cependant à 52 ans dans une relative pauvreté, son sens des affaires étant très inférieur à ses compétences techniques et scientifiques[23].
- Le pot Huntington-Heberlein mis au point en 1897 fonctionne généralement en soufflant l'air de combustion du bas vers le haut. Mais en 1910, Huntington et Heberlein brevettent l'intérêt d'inverser le sens des gaz, en les aspirant au fond[30].
- L'orthographe « mouffle » avec deux « f » est équivalente, mais ne semble plus guère usitée.
- Pendant l'hiver 1904-1905, les dégâts dus aux émissions de dioxyde de soufre décident les fermiers de la vallée de Salt Lake de s'associer pour porter plainte devant l'United States District Court of Utah. Le jugement rendu interdit à toutes les fonderies locales traitant un minerai contenant plus de 10 % de soufre « de rejeter le-dit soufre dans l'atmosphère, que ce soit sous forme d'acide ou autre, et de ne plus rejeter d'arsenic, sous quelque forme que ce soit », entrainant ainsi la fermeture immédiate des 3 fonderies de cuivre concernées[37].
Références
- Emmanuel-Louis Grüner, Traité de métallurgie — métallurgie générale, t. 1, agent et appareils métallurgiques, principe de la combustion, Dunod, (lire en ligne), partie I
- p. 233
- p. 228-229
- p. 230-233
- p. 233-239
- Emmanuel-Louis Grüner, Traité de métallurgie — métallurgie générale, t. 2, procédés métallurgiques, chauffage et fusion, grillage, affinage et réduction, Dunod, (lire en ligne), partie I
- p. 81
- p. 138-140
- p. 82
- p. 17
- p. 18
- p. 89-93
- p. 93-94
- p. 85
- p. 87-88
- p. 85-82 ; 94
- p. 84
- p. 83
- p. 31 ; 100 ; 106-107
- p. 115
- p. 32
- p. 120-121 ; 128-132
- p. 109
- p. 113-114
- p. 21-23
- p. 29-30 ; 95
- p. 18-21
- p. 26-29
- p. 23
- p. 133
- p. 134-137
- p. 122-123
- p. 123-128
- p. 117-119
- Jacques Corbion (préf. Yvon Lamy), Le Savoir… fer — Glossaire du haut fourneau : Le langage… (savoureux, parfois) des hommes du fer et de la zone fonte, du mineur au… cokier d'hier et d'aujourd'hui, 5, [détail des éditions] (lire en ligne)
- § Grillage
- § Four rotatoire
- § Four Smidth
- § Agglomération Smidth
- § Four de grillage
- Autres références
- (en) Mike D. Adams, Gold Ore Processing : Project Development and Operations, Amsterdam, Elsevier, (ISBN 978-0-444-63658-4, lire en ligne), p. 919
- J. Percy (trad. traduction supervisée par l'auteur), Traité complet de métallurgie, t. 1, Paris, Librairie polytechnique de Noblet et Baudry éditeur, (lire en ligne), p. 31
- (de) Tilo Cramm, Der Bergbau zwischen Dortmund-Syburg und Schwerte, Förderverein Bergbauhistorischer Stätten Ruhrrevier e.V.,, , p. 75
- Arthur Jean Baptiste Théodore Édouard Lodin de Lépinay, Métallurgie du zinc, Dunod, , p. 192-202
- [PDF](en) Chiranjib Kumar Gupta, Chemical Metallurgy : Principles and Practice, Weinheim, WILEY-VCH Verlag GmbH & Co. KGaA, , 811 p. (ISBN 3-527-30376-6, lire en ligne), p. 343-345
- Pierre Blazy et El-Aid Jdid, « Métallurgie extractive - Pyrométallurgie », dans Techniques de l'ingénieur, Éditions techniques de l'ingénieur, (lire en ligne)
- [PDF](en) M. K. Seguin, « Thermogravimetric and differential thermal analysis of malachite and azurite in inert atmospheres and in air », Canadian Mineralogist, vol. 13,‎ , p. 127-132 (lire en ligne)
- [PDF](en) Mária Földvári, « Handbook of thermogravimetric system of minerals and its use in geological practice », Occasional Papers of the Geological Institute of Hungary,, Geological Institute of Hungary, vol. 213,‎ (ISBN 978-963-671-288-4, lire en ligne)
- [PDF](en) « Copper », Outotec,
- [PDF]« Document de référence sur les meilleures techniques disponibles : Transformation des métaux ferreux », Commission européenne, , p. 608
- D. Bourgarit et B. Mille, « La transformation en métal de minerais de cuivre à base de sulfures : et pourquoi pas dès le Chalcolithique ? », Revue d'Archéométrie, vol. 25, no 1,‎ , p. 145-155 (lire en ligne)
- (en) Rafael Padilla-Duran, Alvaro Aracena et Maria Cristina Ruiz-Paredes, « Reaction Mechanism and Kinetics of Enargite Oxidation at Roasting », Metallurgical and Materials Transactions B: Process Metallurgy and Materials Processing Science,‎ (ISSN 1073-5615, lire en ligne)
- (en) Åke Holmström, L. Hedström, K. Lundholm, M. Andersson et L. Nevatalo, « Partial roasting of copper concentrate with stabilisation of arsenic and mercury », Outotec,
- (en) « Roasting plants », Outotec,
- (en) Frank K. Krundwell, Michael S. Moats, Venkoba Ramachandran, Timothy G. Robinson et William G. Davenport, Extractive Metallurgy of Nickel, Cobalt and Platinum Group Metals, Elsevier, , 610 p. (ISBN 978-0-08-096809-4, lire en ligne), p. 109-116
- (en) G. Weisgerber et L. Willies, « The use of fire in prehistoric and ancient mining: firesetting », Paléorient, CNRS, vol. 26, no 2,‎ , p. 131-149 (lire en ligne)
- (de) Bruno Kerl, Grundriss der EisenhĂĽttenkunde, Leipzig, Verlag von Arthur Felix, , p. 66
- (en) Stephen Hughes, The Archaeology of an Early Railway System : The Brecon Forest Tramroads, Royal Commission on the Ancient and Historical Monuments of Wales, , 367 p. (ISBN 1-871184-05-3, lire en ligne), p. 116
- [PDF](en) Phil Newman, The Archaeology of Mining and Quarrying in England : A Research Framework for the Archaeology of the Extractive Industries in England, National Association of Mining History Organisations, (ISBN 978-1-871827-41-5, lire en ligne), p. 210
- (en) Donald M. Levy, Modern copper smelting, C. Griffin & company, limited, (lire en ligne), p. 73-76
- [PDF](en) Jörg Grzella, Peter Sturm, Joachim Krüger, Markus A. Reuter, Carina Kögler et Thomas Probst, « Metallurgical Furnaces », John Wiley & Sons, , p. 6-10
- [PDF](en) Robert L. Spude, « The Ingenious Community: Georgetown, Colorado, and the Evolution of Western American Silver Milling and Metallurgy, 1864-1896 », Mining History Journal,‎ , p. 112-118 (lire en ligne)
- Spude 2003, p. 127
- (en) Charles Howard Aaron, Leaching Gold and Silver Ores. The Plattner And Kiss Processes : A Practical Treatise (lire en ligne)
- (en) L. D. Michaud, « Mechanical types of furnces used in metal industry »,
- Grzella et al., p. 4 ; 6
- Gupta 2003, p. 348
- (en) Guido KĂĽstel, Roasting of gold and silver ores : and the extraction of their respective metals without quicksilver, Dewey & Co., , 162 p., p. 99-102
- (en) « Roasting », Outotec,
- (en) Thomas Huntington et Ferdinand Heberlein, « Process of recovering zinc and other volatile metals (patent US 1069085 A) »,
- Jacques Astier, « Agglomération des minerais de fer », dans Techniques de l'ingénieur, Éditions techniques de l'ingénieur, (lire en ligne)
- (en) Alice Hamilton et Royal Meeker, « Lead poisoning in the smelting and refining of lead », Bulletin of the U.S. Bureau of Labor Statictics, Washington government printing office,‎ , p. 31 (lire en ligne)
- Pierre Blazy et El-Aid Jdid, « Pyrométallurgie et électroraffinage du cuivre - Pyrométallurgie », dans Techniques de l'ingénieur, Éditions techniques de l'ingénieur, (lire en ligne)
- [PDF]« Démonstration industrielle d'un procédé innovant de recirculation sélective des fumées à l’agglomération de minerai de fer », ADEME
- (en) William Gowland, The metallurgy of the non-ferrous metals, Charles Griffin and Co, (lire en ligne), p. 181-182
- Hamilton et Meeker 1914, p. 44-45
- [PDF](en) Leonard J. Arrington et Gary B. Hansen, The richest hole on earth : The history of the Bingham copper mine, King Hendricks, (lire en ligne), p. 19
- (en) William Herbert Dennis, Metallurgy - 1863-1963, , 342 p. (ISBN 978-0-202-36361-5, lire en ligne), p. 66-70