Minerai de fer houiller
Le minerai de fer houiller[note 1] ou blackband est un minerai de fer présent dans des gisements de houille. Le fer est présent sous la forme de carbonate de Fe(II), la sphérosidérite (FeCO3). La houille, qui représente généralement de 10 à 25 % du poids, permet sa combustion.
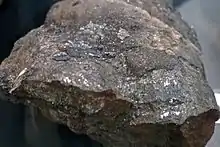
S'il est un médiocre combustible, il s'avère être un minerai de fer bien adapté aux procédés sidérurgiques. Ainsi, le blackband est à l'origine notamment du développement de la sidérurgie écossaise à partir des années 1840, puis de la Ruhr dans les années 1860. Ces gisements sont maintenant épuisés.
Aspect et composition
Ce minerai est de couleur noir mat, avec parfois des reflets bleu ardoise[4]. Sa texture est parfois schisteuse et rubannée[5]. La couleur noire domine dès que la teneur en charbon dépasse 10 %[6] :
« Ce minerai renferme de si grandes quantités de houille, et de manière si constante, qu'il est absolument noir et susceptible de s'enflammer et de continuer à brûler. La proportion de matières combustibles n'est pas inférieure à 10 %, et atteint fréquemment 25 %. Les parties qui contiennent le plus de houille brûlent seules et forment la transition entre les minerais et les houilles les plus chargées en cendres[7]. »
— A. Ledebur, Manuel théorique et pratique de la métallurgie du fer, Tome 1, p. 220
Il s'agit d'un mélange de sidérite, de kaolin (un silicate d'alumine) et de charbon[4]. Une teneur en charbon de 10 à 25 % en poids est courante[7], bien que certains auteurs fixent une fourchette entre 12 et 35 %, voire 40 %[4]. On y trouve aussi souvent d'autres métaux, jusqu'à 1 % de manganèse et 0,5 % de phosphore[8], mais certains minerais peuvent être si riches en phosphore qu'ils sont compatibles avec la production de superphosphate[9]. L'arsenic et le soufre y sont également présents, en de plus faibles concentrations, et combinés sous la forme d'arsénopyrite et de marcassite, mais aussi de galène et de sphalérite. La teneur en soufre peut atteindre 4 %[10]. Avant traitement, la teneur en fer du minerai se situe entre 25 et 40 %, la teneur moyenne étant 30 %[8]. Le trait et la cassure des meilleures variétés présentent un éclat métallique[10]. Enfin, des stériles, comme le sable, les marnes ou l'argile, peuvent être présents[4].
Formation
Les gisements de minerai de fer houiller datent du carbonifère. Ils se forment en plusieurs étapes, dans les mares et entendues d'eau douce peu profondes, qui sont propices à la formation de la houille[8]. Les mousses et autres plantes, qui contiennent l'oxyde de fer(II) acide, s'en séparent dans l'eau stagnante et le fer prend la forme d'oxyhydroxyde de fer(III)[9]. Ce composé du fer précipite et se concentre alors dans la zone racinaire des plantes. Les précipités s'accumulent progressivement, la quantité de fer dépendant beaucoup de la circulation des liquides et de leur teneur en fer. Ainsi, dans la même veine charbonneuse, on peut trouver des secteurs riches en fer et d'autres non[8].
Typologie des gisements et extraction
Les couches de minerai se confondent avec celles de charbon, se concentrant généralement au pied de la strate charbonneuse. Mais on peut aussi les trouver en partie médiane ou supérieure[9]. Dans certaines formations de houille, les dépôts de minerai atteignent jusqu'à 0,7 mètre de puissance[4]. Hors des gisements les plus importants et exploités industriellement, on le trouve disposé en rognons dans les grès[1].
Les gisements les plus importants ont été trouvés en Allemagne, à Sprockhövel, Gelsenkirchen et Dortmund-Aplerbeck[4]. Dans la mine d'Hiddinghausen, une couche d'une puissance de 1,24 m a été découverte par un tunnel[11]. Au Royaume-Uni, ce type de gisement atteignait communément des puissances aussi importantes[4].
Utilisation
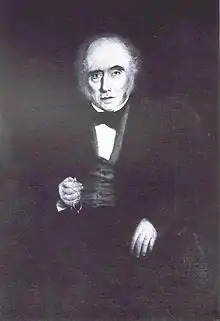
Trouvé dans des mines de charbon, cette roche s'avère un combustible médiocre qui a d'abord rejoint les stériles sur les terrils des charbonnages[9].
La première tentative d'utilisation du minerai de fer houiller pour la fabrication de l'acier a été faite par l'écossais David Mushet (en) (père de Robert Forester Mushet). En 1801, il réussit à produire de la fonte à l'usine de Calder Iron Works, qu'il venait de relancer avec des associés. Non seulement le minerai est adapté à la production de fonte, mais son utilisation s'avère rentable[9].
Pourtant, sa teneur en fer, assez moyenne, combinée avec la présence de nombreuses impuretés, en fait un minerai difficile à traiter[9]. Peu après, vers 1830, un autre écossais, James Beaumont Neilson, met au point une amélioration clé du haut fourneau : le vent chaud. La fusion de ce minerai est alors facilitée : l'expansion de la sidérurgie écossaise, qui passe d'une production annuelle de 37 500 tonnes en 1830 à 200 000 tonnes en 1840, s'explique par la combinaison de ces deux innovations : blackband et vent chaud[12].
Il a été ensuite découvert dans la seconde moitié du XIXe siècle dans la région de la Ruhr[9]. Des quantités importantes ont été extraites dans les mines allemandes durant les années 1860 et 1870[9]. Sa découverte a été, là aussi, le socle du développement de l'industrie sidérurgique de la Silésie (Wałbrzych), de la Westphalie (Hoerde, Aplerbeck , Hattingen[9])[4]. Il en a été de même dans le Pays de Galles[6].
Afin d'augmenter sa teneur en fer, le minerai doit être calciné, voire grillé[note 2]. Cette opération nécessaire est cependant aisée : « quoique d’une valeur intrinsèque assez faible, le blackband est néanmoins très précieux à cause de son abondance et parce qu'il est dans le voisinage d’un combustible qui peut servir à son traitement métallurgique[1] ». Le mélange intime du charbon avec le minerai est en outre un avantage :
« On ne l'emploie dans les hauts fourneaux qu'après un grillage préalable, qui est d'autant plus facile que ce minerai porte avec lui son combustible dans des quantités ordinairement suffisantes ; il arrive même quelques fois que la chaleur développée par la houille dont il est imprégné permet de calciner d'autres minerais que l'on mélange avec celui-ci[7]. »
— A. Ledebur, Manuel théorique et pratique de la métallurgie du fer, Tome 1, p. 220
Grâce à cette opération la teneur en fer du minerai cru, qui ne dépasse jamais 40 %, atteint 35 à 65 % après grillage, la valeur moyenne étant 45 %[8]. Cette opération amène une perte en poids du minerai, qui correspond à la combustion des matières organiques ainsi qu'à l'envol de certaines impuretés : près de la moitié du poids peut ainsi disparaître, ce qui amène logiquement à l'augmentation de la teneur en fer[10].
Principaux constituants de quelques minerais (en % du poids, Σ ≤ 100 %)[5] - [note 3] | |||||||||
---|---|---|---|---|---|---|---|---|---|
FeCO3 | MnCO3 | CaCO3 | MgCO3 | SiO2 | Al2O3 | S | Matières organiques | P4O10 | |
Blackband cru (30,40 % de fer) | 63 | 3,60 | 2,96 | 0,50 | 7,85 | 7,95 | 0,19 | 13,56 | tr. |
Fe2O3 | MnO2 | CaO | Argile et sable | H2SO4 | Matières organiques | H3PO4 | |||
Blackband grillé (50,37 % de fer) | 71,95 | 3,94 | 4,68 | 16,96 | 2,57 | 0 |
Pour griller ce minerai, on en constituait un tas dont les dimensions allaient, selon la teneur en charbon, de 40 à 60 mètres de long, de 6 à 11 mètres de large et d'environ 5 mètres de haut[14]. Cette opération durait à l'époque environ un mois. Ce mode opératoire a été essentiellement appliqué à proximité de la mine, le transport du minerai grillé, plus léger, étant plus économique que celui du minerai cru. Au charbon naturellement présent, on ajoutait souvent du bois pour faciliter la combustion[8]. Un tel procédé était extrêmement polluant. On l'a par la suite remplacé par des fours à griller le minerai. Depuis le milieu du XXe siècle, ce type d'opération est réalisé dans les usines d'agglomération, qui réalisent la calcination, le grillage et le frittage des minerais[note 2].
On peut aussi relever une utilisation historique du blackband manganésifère du North Staffordshire, qui a été très apprécié comme garnissage des fours de puddlage[15].
Notes et références
- (de) Cet article est partiellement ou en totalité issu de l’article de Wikipédia en allemand intitulé « Kohleneisenstein » (voir la liste des auteurs).
Notes
- Autres appellations : fer carbonaté terreux, fer carbonaté lithoïde[1], minerai de fer charbonneux[2], fer carbonaté bitumeux[3]
- Par ordre de températures croissantes : la calcination réalise, entre autres, une décarbonatation ; le grillage une oxydation (dans le blackband, la décarbonatation de la sidérite aboutit à sa transformation en hématite, forme la plus oxydée du fer : les deux phénomènes sont donc indissociables) ; le frittage qui donne une structure poreuse et solide (par fusion partielle).
- Dans son « Traité de métallurgie », Percy communique plus de 80 analyses de minerais de fer houiller originaires de Grande-Bretagne. Ils sont généralement moins riches que celui listé ici puisque leur teneur en fer après grillage se situe entre 25 et 40 %[13].
Références
- Jacques Corbion (préf. Yvon Lamy), Le savoir… fer — Glossaire du haut fourneau : Le langage… (savoureux, parfois) des hommes du fer et de la zone fonte, du mineur au… cokier d'hier et d'aujourd'hui, , 5e éd. [détail des éditions] (lire en ligne), § Sidérose
- (en) Magdeleine Moureau et Gerald Brace, Dictionnaire du pétrole et autres sources d'énergie : anglais-français, français-anglais, Paris, Éditions Technip, (ISBN 978-2-7108-0911-1, lire en ligne), p. 54, § Blackband
- Marcellin Berthelot et al., La Grande Encyclopédie, inventaire raisonné des sciences, des lettres, et des arts, Paris, H. Lamirault & Cie, 1885-1902 (lire sur Wikisource), § Calcination
- (de) « Kohleneisenstein », eLexikon
- Emmanuel-Louis Grüner et Charles-Romain Lan, État présent de la métallurgie en Angleterre, t. 1, Paris, Dunod éditeur, (lire en ligne), p. 200-201
- (de) « Eisen (Brauneisenstein, Spateisen-, Thoneisen- und Kohleneisenstein) », eLexikon
- Adolf Ledebur (trad. Barbary de Langlade revu et annoté par F. Valton), Manuel théorique et pratique de la métallurgie du fer, Tome I et Tome II, t. 1, Librairie polytechnique Baudry et Cie éditeur, [détail des éditions], p. 220-221
- (de) Tilo Cramm, Der Bergbau zwischen Dortmund-Syburg und Schwerte, Förderverein Bergbauhistorischer Stätten Ruhrrevier e.V.,, , p. 75
- (de) Ludwig Beck, Die Geschichte des Eisens in technischer und kulturgeschichtlicher Beziehung, F. Vieweg und sohn, (OCLC 27288504, lire en ligne), p. 322, 802, 835
- (de) Charles-Edouard Jullien et Carl Hartmann, Theoretisch-praktisches Handbuch der Eisenhüttenkunde umfassend die Roheisen-, die Gusswaren-, die Stabeisen-, die Stahl-, und die Weissblechfabrikation., Verlag von August Schnée, (ASIN B0052IZWEE, lire en ligne), p. 54–55
- (de) Gustav Adolf WĂĽstenfeld, Schlebuscher Revier : Bergbau in Wetter, Gustav Adolf WĂĽstenfeld-Verlag, , 64 p. (ISBN 3-922014-05-4), p. 12
- (en) Thomas Turner (dir.), The Metallurgy of Iron : By Thomas Turner… : Being one of a series of treatises on metallurgy written by associates of the Royal school of mines, C. Griffin & company, limited, coll. « Griffin's metallurgical series », , 3e éd., 463 p. (ISBN 1-177-69287-2 et 978-1177692878, lire en ligne), p. 22
- J. Percy (trad. traduction supervisée par l'auteur), Traité complet de métallurgie, t. 2, Paris, Librairie polytechnique de Noblet et Baudry éditeur, (lire en ligne), p. 352 - 362
- (de) Bruno Kerl, Grundriss der EisenhĂĽttenkunde, Leipzig, Verlag von Arthur Felix, , p. 66
- Turner 1908, p. 66