Procédé Bessemer
Le procédé Bessemer est un procédé d'affinage de la fonte brute, aujourd’hui disparu, ayant servi à fabriquer de l'acier peu coûteux. Ce procédé porte le nom de son inventeur, Henry Bessemer, qui le brevette en 1855 et le perfectionne avec la Henry Bessemer and Company, société implantée à Sheffield, ville du Nord de l'Angleterre.
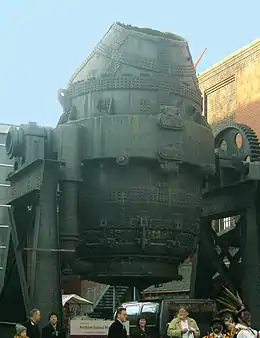
Le procédé consiste à oxyder avec de l'air les éléments chimiques indésirables contenus dans la fonte pour en obtenir du fer ou de l'acier. L'originalité du procédé consiste à exploiter la chaleur dégagée par les réactions chimiques pour maintenir la masse de métal en fusion. Après l'amélioration de Thomas (procédé Thomas ou « Bessemer basique »), le convertisseur devient un des moteurs de la révolution industrielle.
Avec la mise au point, au début du XXe siècle, de la liquéfaction des gaz, l'utilisation d'oxygène pur devient économique. Le procédé Bessemer est alors abandonné dans le milieu des années 1960 : même si l'allure générale du convertisseur est conservée, les performances et la conduite des convertisseurs modernes à l'oxygène ont peu de rapport avec celui de Bessemer[1].
Genèse du procédé
Procédés primitifs d'affinage de la fonte par l'air
Le haut fourneau étant un bas fourneau dont la combustion est attisée par un puissant courant d'air, les forgerons ont toujours essayé de convertir la fonte liquide produite par le haut fourneau en un métal proche de l'acier présent dans la loupe extraite du bas fourneau. Les Chinois, premiers utilisateurs du haut fourneau, affinaient la fonte en la brassant à l'air pendant plusieurs jours pour brûler le carbone dissous. Ce procédé appelé chǎo (chinois : 炒), ce qui signifie littéralement « saisir dans une poêle », a permis l'obtention de nombreux outils et armes en acier ou en fer[2]. Au XVIIIe siècle, les missionnaires chrétiens jésuites contribuent à faire connaître ce procédé en Europe[3].
Avec l'invention du haut fourneau au coke et du puddlage, la production de fonte et sa transformation en fer sont entrées dans l'ère industrielle. Ces procédés partagent la caractéristique d'opérer sur un matériau à l'état pâteux (comme le puddlage), ou liquide mais sans brassage métallurgique. Il en est de même pour la production d'acier, obtenue par recarburation[alpha 1] du fer puddlé. Il faut non seulement réchauffer le matériau à haute température, mais aussi le maintenir chaud pendant une longue durée. Les besoins en combustibles sont élevés, alors que la productivité reste faible[B 1].
En 1847, le maître de forges états-unien William Kelly commence une série d'expériences pour décarburer la fonte liquide par l'emploi de l'air seul. En 1851, il expose les principes de l'affinage de la fonte à l'air à quelques maîtres de forges et métallurgistes locaux. Cependant si le procédé est théoriquement capable de convertir la fonte en fer, il n'est pas breveté[alpha 2] et rien ne permet de prouver que les expériences menées ont abouti à l'obtention d'un métal convenablement décarburé[4].
Invention du procédé par Bessemer
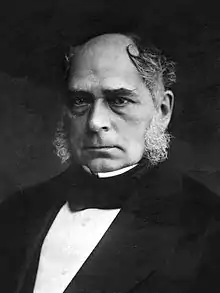
Henry Bessemer est un ingénieur et inventeur anglais fécond. Dans les débuts des années 1850, il cherche à fondre ensemble du fer et de l'acier pour obtenir un acier sans devoir marteler ou forger une masse de métal. Pour ne pas polluer le métal avec le soufre contenu dans le combustible, il doit employer un four à réverbère, dans lequel il dose de la fonte et du fer pour obtenir de l'acier. Pour atteindre les températures nécessaires[alpha 3], il provoque un courant d'air à la surface du bain de métal liquide afin d'améliorer la combustion des fumées[B 2].
Le métal obtenu est d'excellente qualité. Bessemer parvient sans difficulté[alpha 4] à convaincre l'empereur Napoléon III d'investir dans son procédé pour la fabrication d'acier à canon. Retournant à son laboratoire pour parfaire le procédé, il observe alors que, à la surface de la fonte liquide, se forment de fines plaques de fer décarburé. Ce fer, solide car sa température de fusion est supérieure à celle de la fonte, a été obtenu par la seule action de l'air « sans puddlage ou autre manipulation[B 3] ». Il réoriente alors ses recherches[alpha 5] pour mieux comprendre cette découverte[B 3].
Bessemer construit pour cette nouvelle étude un creuset de laboratoire avec une canne plongeant dans de la fonte grise en fusion pour y insuffler de l'air. Ce creuset est réchauffé par l'extérieur. Il obtient ainsi du fer liquide « sans aucune manipulation, mais non sans combustible[B 4] ».
Or Bessemer, qui connaît la nature exothermique des réactions d'affinage, veut aller plus loin :
« C'est alors qu'émergea la question de première importance : l'introduction d'air atmosphérique pourrait-elle produire suffisamment de chaleur interne pour maintenir le métal fluide jusqu'à ce qu'il soit complètement décarburé ? Cela, j'étais déterminé à l'essayer sans délai[B 4]. »
— H. Bessemer, Sir Henry Bessemer, F.R.S. An autobiography, p. 143
Il construit alors le premier convertisseur dans son laboratoire. Celui-ci consiste en un réservoir cylindrique, doté à sa base de 6 tuyères pour y insuffler l'air dans le métal en fusion. Il obtient du fer, bien que la violence de la réaction impose des précautions. En effet, au début du soufflage, la réaction est calme, le silicium s'oxydant pour former un laitier acide qui flotte sur le bain. Mais après que tout le « silicium a été calmement consumé, l'oxygène se combine alors avec le carbone, provoquant un flux croissant d'étincelles et une grande flamme blanche[B 5] » : la combustion du carbone crée en effet un grand volume de monoxyde de carbone qui brasse violemment le bain.
La violence de la réaction est telle que pour Bessemer, ce premier convertisseur est « condamné en tant qu'outil commercial, à cause des projections de laitier, et uniquement pour cette raison[B 6] ». Il essaye un déflecteur constitué d'une plaque de fonte : celle-ci ne résiste pas à son premier essai. Il construit alors une chambre en réfractaire au-dessus du carnau pour collecter les particules incandescentes. Il ajoute sous le trou de coulée du convertisseur un réservoir tampon, servant à la fois de réceptacle de secours et de lieu de décantation si des morceaux de matériau réfractaire étaient mélangés au métal. Une fois plein, ce réservoir permet un remplissage contrôlé du moule situé sous lui[B 7].
- Four à réverbère expérimental de Bessemer. L'injection d'air (le ventilateur est visible) censée améliorer la post-combustion des fumées décarburait aussi la fonte.
- Creuset experimental de Bessemer. Ce creuset, chauffé par l'extérieur, permit à Bessemer de vérifier que l'air était capable de transformer efficacement la fonte en fer.
- Premier « convertisseur Bessemer » expérimental. La plaque en fonte dévie des projections.
- Deuxième convertisseur Bessemer expérimental. La chambre supérieure piège les étincelles et les fumées.
- Installation du convertisseur Bessemer vertical. Un réservoir tampon collecte le fer liquide avant sa coulée en lingotière.
L'annonce de Cheltenham
Le procédé inventé par Bessemer soulève beaucoup de scepticisme : il propose de souffler de l'air froid dans une masse de fonte en fusion, et estime qu'à la fin du soufflage, le métal obtenu sera plus chaud[alpha 3] qu'au début ! Le premier essai est pourtant une réussite[B 8].
Malgré ce succès, Bessemer se méfie encore de sa découverte. Cherchant un avis impartial, il sollicite discrètement George Rennie (en), président de la section mécanique de la British Association. Impressionné par l'essai que Bessemer réalise devant lui, celui-ci l'encourage à communiquer immédiatement sur son invention, sans attendre que les détails techniques soient mis au point. Rennie bouleverse l'ordre du jour du congrès de cette association renommée afin que le communiqué de Bessemer ait une publicité maximale. Le , à Cheltenham quelques heures avant de lire son papier, il surprend l'échange entre un sidérurgiste gallois, M. Budd, et son ami William Clay :
« Clay, j'aimerais que vous m'accompagniez à l'une des conférences ce matin, on s'y amusera bien »
La réplique fut : « Je suis désolé car je me suis spécialement engagé ce matin, sinon je l'aurais fait avec plaisir. »
« Oh vous devriez venir, insista M. Budd. Saviez-vous qu'un personnage arrive de Londres pour nous présenter un papier sur la fabrication de fer doux sans combustible ? Ha, ha, ha[B 9] ! »
— H. Bessemer, Sir Henry Bessemer, F.R.S. An autobiography, p. 156
Le discours a un grand retentissement et est intégralement reproduit le lendemain dans The Times. Mais Bessemer a anticipé les performances de son procédé : il l'annonce comme capable de recycler des ferrailles et d'ôter le soufre du métal (ce qui lui permettrait de transformer la fonte au coke en un excellent fer affiné au charbon de bois). Il montre des échantillons démontrant la qualité du fer obtenu. Mais le procédé est loin d'être mature :
« Je me suis permis d'apporter trop rapidement mon invention devant l'intérêt du public. Je n'aurais pas dû le faire avant que tous les détails du procédé n'aient été examinés, et j'en aurais alors fait un grand succès commercial (et non pas scientifique)[B 10]. »
— H. Bessemer, Sir Henry Bessemer, F.R.S. An autobiography, p. 164
En effet, les quelques maîtres de forge qui ont acheté le droit de fabriquer de l'acier Bessemer constatent vite que le fer obtenu est souvent inapte aux applications les plus exigeantes : son ami William Clay[alpha 6] le qualifie même de « pourri à chaud et de pourri à froid »[6]. Pour étouffer l’affaire et se donner le temps de déterminer l’origine de cette mauvaise qualité, Bessemer rachète immédiatement les droits de ses associés. Mais les constats d'échec se multiplient et l'affaire s'ébruite jusque dans la presse[B 11]. Recherchant soigneusement l'origine de la mauvaise qualité du fer obtenu avec certaines fontes, il constate que « la fonte brute britannique contient de façon abondante cet ennemi mortel, le phosphore[B 12] ».
Le fer, lorsqu’il contient plus de 3 ‰ de phosphore, devient en effet cassant[Ba 1]. Alors que le puddlage permet de déphosphorer la fonte, le procédé de Bessemer n’a aucune influence sur cet élément. Bessemer se résout à limiter son procédé à l'affinage de fontes suédoises au charbon de bois et de quelques fontes hématites anglaises, élaborées à partir de minerais sans phosphore[B 13]. Le procédé reste cependant rentable car ces fontes, achetées 7 £ la tonne, donnent un acier valant 50 à 60 £ la tonne[B 14].
La déception qui suit cette annonce ne sera pas oubliée : lorsque Bessemer exposera, quelques années après, les avantages du traitement au ferromanganèse, Thomas Brown, un métallurgiste dont l'enthousiasme pour le procédé Bessemer fut douché par la difficulté de mettre au point un revêtement réfractaire économique, affirma publiquement « qu'il pensait que M. Bessemer faisait la même erreur sur les coûts de son procédé que celle qu'il fit à Cheltenham[B 15] ».
Mise au point de la cornue Bessemer
Le convertisseur fixe mis au point par Bessemer est efficace, mais présente d'évidents inconvénients pratiques. En effet, pour éviter le bouchage des tuyères, le soufflage doit être maintenu tant que du métal est dans le convertisseur. Or les durées de remplissage et de vidange pouvant fluctuer, il n'est pas possible de garantir la durée du soufflage, et donc la température du métal liquide car l'essentiel de la chaleur est dissipé par le vent soufflé. De plus, il n'y a pas de possibilité de stopper rapidement l'opération en cas de problème sur la soufflerie ou une tuyère[B 16].
L'idée d'un convertisseur rotatif s'impose donc rapidement. Quant à sa forme caractéristique de cornue, elle est dictée par le procédé :
- les formes concaves permettent un bon maintien du revêtement réfractaire : un réacteur chimique ovoïde est un compromis entre le cylindre des convertisseurs fixes et la sphère ;
- le bec pointé de manière oblique permet de diriger les projections loin de la zone de travail. Il impose un remplissage en position inclinée[B 16] ;
- un basculement permet l'examen des tuyères[L 1]. Le fond du convertisseur est accessible, ce qui permet d'adopter un fond rapidement remplaçable en cas de problème[7] - [alpha 7].
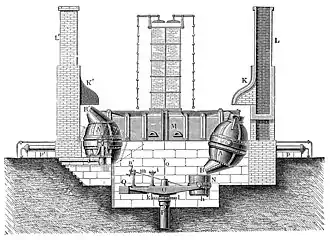
Puis Bessemer met au point l'installation de coulée, allant jusque dans les moindres détails :
- une poche permet de gérer le remplissage des lingotières. Une quenouille permet d'obstruer son trou de vidange ;
- une soufflerie silencieuse ;
- une potence hydraulique pour manutentionner les poches, et une autre, manuelle, pour la gestion des lingots. Robustes mais ne permettant pas de desservir une grande surface, ces mécanismes seront souvent abandonnés au profit de ponts roulants ;
- un poste de contrôle où sont centralisées toutes les commandes ;
- un mécanisme puissant et commandable à distance pour le basculement du convertisseur, etc[B 17].
Une usine de démonstration est édifiée à Sheffield. Après deux ans de fonctionnement, elle est rentable[B 18]. Aux maîtres de forges qui achètent le droit de fabriquer de l'acier Bessemer, en échange d'une redevance de dix shillings par tonne de métal produite, il propose les plans d'un outil parfaitement au point. Thomas Turner constate, une cinquantaine d'années après cette annonce, qu'il est « remarquable que non seulement la première conception, mais aussi les détails mécaniques du procédé sont tous issus du même esprit, et que l'invention a quitté les mains de son concepteur si aboutie qu'aucune amélioration, excepté des détails mineurs, n'a été depuis introduite[T 1] »[alpha 8].
Réactions chimiques
Déroulement d'un soufflage
Tous les essais menés par Bessemer pour maîtriser la violence de la réaction ayant échoué, il en conclut que, pour obtenir une bonne décarburation, l'air soufflé doit faire mousser le métal de manière que « la combustion du carbone par l'oxygène se déroule dans des myriades de petites bulles instables[B 19] ». Le panache de fumées et de projection s'avère finalement essentiel pour évaluer l'avancement de l'affinage. En 1895, Ledebur décrit ainsi la réaction dans un convertisseur industriel :
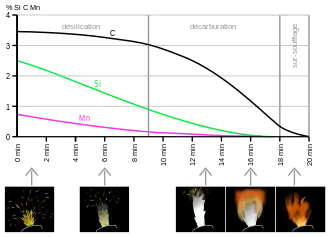
« […] les gaz qui s'échappent de prime abord sont peu éclairants ; ils ont une teinte rougeâtre due aux parcelles métalliques qu'ils entraînent, le carbone ne brûle pas encore ou, du moins sa combustion est insignifiante, l'oxydation se porte à peu près uniquement sur le silicium et le manganèse ; de nombreuses étincelles sont projetées hors de l'appareil, et on entend à l'intérieur un bruit de clapotement provenant du passage de l'air à travers la masse métallique…
Bientôt après, la combustion du carbone commence, la flamme paraît avec une couleur d'un bleu blanchâtre et sous la forme d'un cône allongé ; puis elle devient plus vivement éclairante, tandis que le nombre et la grosseur des étincelles diminuent…
À partir du moment où le carbone a commencé à brûler, le dégagement des gaz augmente, la flamme devient d'un blanc éclatant, elle atteint jusqu'à 6 m de longueur ; le clapotement du commencement se transforme en explosion retentissante provoquée par la production de grandes quantités d'oxyde de carbone dans un endroit restreint. Il se fait des projections de scories et de grenaille métallique entraînées par le mouvement rapide des gaz…
Dès le moment où la flamme devient plus vive, on distingue à sa pointe une fumée brune qui augmente d'intensité à mesure que la décarburation s'avance ; elle se compose d'oxyde de fer et d'oxyde de manganèse emportés par le courant gazeux… Cependant la carburation du métal diminue de plus en plus, […] la fumée brune augmente et enveloppe toute la pointe de la flamme, les explosions […] se calment…[L 2] »
— A. Ledebur, Manuel théorique et pratique de la métallurgie du fer, p. 507
Pour l'opérateur, il est donc facile de distinguer les différentes phases du soufflage : l'oxydation du silicium et du manganèse produisant le laitier, il s'agit d'une réaction calme. Puis la combustion du carbone produit un gaz, le monoxyde de carbone : le bain va donc être violemment agité. Ce gaz étant combustible et chaud, il s'enflamme spontanément au contact de l'air. Enfin, la combustion du fer génère des fumées rousses, caractéristiques de l'oxyde de fer : prolonger alors le soufflage n'amène qu'à gaspiller le fer affiné.
- Convertisseur Bessemer en début de soufflage en Pennsylvanie. Le panache d'étincelles et la courte flamme orange sont typiques de la combustion du silicium.
- Convertisseurs à différents stades du soufflage. Du premier-plan à l'arrière-plan : début de soufflage avec des projections jaunes de silice ; décarburation avec une grande flamme blanche-bleuâtre ; fin de soufflage avec des fumées brunâtres.
Pour apporter un peu plus de rigueur au suivi du soufflage, des procédures sont également développées. Beaucoup d'aciéries utilisent un spectroscope[L 4] - [Ba 2]. Une autre méthode consiste à tremper dans le métal une tige de fer et à évaluer la couleur du laitier qui s'est solidifié dessus : tant qu'une couleur brunâtre est décelable, le métal n'est pas complètement décarburé. À l'inverse, un laitier noir avec des points brillants est caractéristique d'un métal décarburé et en cours de sur-soufflage[Ba 3].
Bilan thermique de la réaction
Les oxydations du silicium, du manganèse, du carbone et du fer sont exothermiques. Mais il apparaît rapidement aux expérimentateurs que l'obtention d'un fer complètement affiné nécessite une fonte d'une qualité bien précise :
- le silicium est le principal contributeur thermique : la combustion de 1 % de silicium élève la température du bain de 300 °C[L 5]. C'est la teneur visée par les sidérurgistes états-uniens, alors que les Anglais utilisent généralement des fontes à 2 % de silicium[7] ;
- la combustion du manganèse et du fer est trop peu exothermique pour avoir une quelconque influence[L 6] ;
- la combustion du carbone n'est vraiment exothermique qu'aux basses températures : la combustion de 1 % de cet élément n'élève la température d'un bain à 1 500 °C que de 6 °C[L 5]. La faible contribution thermique du carbone est rapidement admise par tous, alors que Bessemer l'avait estimée fondamentale[B 20].
Une teneur minimum en silicium est donc nécessaire pour que le soufflage puisse s'achever : cette nécessité précipite la disparition des hauts fourneaux à vent froid. Mais produire des fontes très riches en silicium n'a pas d’intérêt économique car cela entraîne une forte consommation de combustible au haut fourneau[L 7]. De plus, trop de silicium prolonge le soufflage et entraîne une forte consommation de fer par le laitier[7] - [alpha 9]. Cette contrainte sur la qualité de la fonte a été un frein à son affinage directement à la sortie du haut fourneau : on a donc longtemps préféré préparer au cubilot une charge de fonte liquide à partir de gueuses soigneusement choisies. Mais cet outil, outre sa consommation en combustible, est un goulot vis-à-vis du convertisseur : il est abandonné dès que l'on peut mélanger la fonte de plusieurs hauts fourneaux pour en stabiliser la composition[Ba 4].
Incapacité à déphosphorer
Bessemer avait initialement dirigé ses recherches vers l'obtention d'un acier de haute qualité pour la fabrication de canons[B 21]. Les premiers essais de son procédé ont d’ailleurs donné un fer doux de qualité satisfaisante. La recherche d’une amélioration capable d’ôter le phosphore mobilise l’énergie de Bessemer pendant plusieurs années. Mais, après la dépense de plusieurs milliers de livres sterling en expérimentations diverses[B 22], il ne trouve pas de solution pour l'éliminer[8]. Les essais d'enrichissement de l'air avec des éléments plus réactifs (avec, entre autres, le monoxyde de carbone et des hydrocarbures) pour rendre le procédé compatible avec les fontes phosphoreuses au coke, échouent tous[B 12].
Bessemer contourne cette difficulté par l'utilisation de fonte suédoise élaborée au charbon de bois, et fait adopter son procédé partout où des minerais dépourvus de phosphore sont disponibles[B 13].
Pourtant, le puddlage s’avère capable de retirer le phosphore d’une fonte moyennement phosphoreuse[P 1] - [P 2], mais les réactions qui permettent ce résultat sont mal comprises[L 8] - [Ba 5]. La solution ne sera trouvée qu'en 1877 par Thomas, avec un revêtement et un laitier à base de chaux, au lieu de silice. Bessemer avait d’ailleurs réalisé ses premières expériences avec des briques réfractaires basiques, assemblées avec de l'argile. Le revêtement siliceux adopté par la suite ne lui permet pas d’obtenir un laitier où l’oxyde de phosphore soit stable[B 23].
Rôle du manganèse et calmage
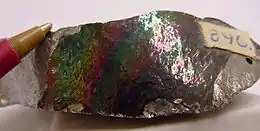
Il était bien connu depuis le brevet de Josiah Marshall Heath en 1839[alpha 10], que l'addition de manganèse améliore significativement les propriétés des aciers : quatre brevets relatifs à l'addition de manganèse pour améliorer le fer de Bessemer sont d'ailleurs déposés dans les semaines qui suivent l'annonce de Cheltenham. Parmi ces brevets, trois sont du métallurgiste anglais Robert Forester Mushet, spécialiste des alliages d'acier et de manganèse[B 24]. Sa méthode consiste à mener d'abord le soufflage jusqu'à son terme, puis à ajouter dans le convertisseur une quantité soigneusement calculée de carbone et de manganèse (généralement 10 % du poids de la charge[Ba 6]), sous la forme de ferromanganèse[8]. En effet, le ferromanganèse utilisé alors étant une fonte qui apporte beaucoup de carbone (sa teneur est de 4 % de carbone pour seulement 8 % de manganèse), l'effet du manganèse est accompagné d'une recarburation indésirable du métal.
Or le manganèse est un élément d'alliage dont l'intérêt est multiple. Tout d'abord, il supprime la fragilité à chaud due au soufre contenu dans le métal, en formant du sulfure de manganèse (MnS). Cet effet est bien connu des métallurgistes de l'époque, même s'il est encore mal expliqué[P 4]. Il n'est donc pas brevetable et ne concerne pas Bessemer, qui se limite d'ailleurs à l'affinage de fontes de qualité exemptes de cet élément.
Le manganèse réagit aussi avec l'oxygène apporté par le soufflage, qui reste dissous dans le métal. Cet élément est soit combiné avec le carbone, sous la forme de monoxyde de carbone, soit combiné avec le fer, sous la forme d'oxyde de fer. Le monoxyde de carbone, très soluble dans le fer liquide, est rejeté par le métal au moment de la solidification, et forme alors des poches de gaz, les soufflures, qui affaiblissent considérablement les pièces moulées[B 25]. L'oxyde de fer, typique des fortes teneurs en oxygène (cas de sursoufflage), forme des inclusions qui fragilisent également le fer.
Or le métal liquide issu du convertisseur contient beaucoup d'oxygène dissous. Même en évitant soigneusement tout sursoufflage, les soufflures se forment. Ces cavités sont typiques du procédé pneumatique de Bessemer et sont incompatibles avec l'obtention de lingots ou de pièces moulées de qualité. Mushet, dont le brevet a été inspiré par l'observation d'un acier Bessemer suroxydé[alpha 11], n'a pas remarqué qu'un dégagement de gaz au moment de la solidification est indissociable du nouveau procédé[9].
- Métallographie montrant des inclusions de sulfure de fer aux joints de grain, qui rendent cet acier cassant à chaud.
- Inclusions de sulfure de manganèse (taches allongées en gris clair) dans un acier traité au manganèse. Ces inclusions ne perturbent pas la cohésion des grains.
- Solidification d'acier calmé ou effervescent. La retassure centrale sur l'acier calmé est due au retrait de solidification et peut être supprimée avec une masselotte.
Pour Bessemer, qui cherche un réactif susceptible de s'associer avec l'oxygène sous une forme non gazeuse, les brevets de Mushet sont « un obstacle qui pourrait m'empêcher tout usage du manganèse dans mon procédé, dans n'importe quelle forme que ce métal puisse être[B 26] ». Il cherche alors à limiter le soufflage en le stoppant dès que la bonne teneur en carbone est atteinte. Cette méthode ne donne cependant pas de résultats satisfaisants : ce dégagement de gaz persiste, l'acier bouillonne et est qualifié de « sauvage »[P 5]. Il cherche alors, sans plus de succès[alpha 12], un autre élément capable de fixer l'oxygène dissous (de « calmer » l'acier), économique et qui ne dégrade pas la qualité du métal[B 28].
Finalement, avec la mise au point de ferromanganèses plus riches, il devient possible de combiner les avantages d'un soufflage partiel avec l'utilisation du manganèse. Bessemer, qui estime que le brevet de Mushet n'a pas de rapport avec le « calmage », utilise alors publiquement le ferromanganèse[alpha 13]. L'acier obtenu est enfin d'excellente qualité, malléable à chaud et tenace à froid[8] - [B 28], sans dégrader pour autant la compétitivité du procédé. Le silicium, meilleur désoxydant que le manganèse, peut être aussi utilisé[alpha 14], pour empêcher la formation de soufflures dans les aciers moulés[Ba 7]. Mais une addition importante de silicium peut s'avérer néfaste s'il n'y a pas assez d'oxygène pour l'oxyder complètement, le silicium libre étant un élément d'alliage incompatible avec le forgeage[alpha 15] - [L 10].
Expansion du procédé
Bessemer s'emploie à démontrer qu'à sa découverte correspond une invention économiquement viable. Les déconvenues des premiers maîtres de forges ayant adopté son procédé lui ont clairement montré les limites de son convertisseur, à réfractaire siliceux. Il consacre deux années à identifier les limites de son procédé et à en améliorer chaque détail[B 30].
Il va recenser les minerais anglais sans phosphore, et faire en sorte que la fonte et le fer élaborés selon ses recommandations soient distingués des autres productions[alpha 16] - [B 31]. Il rachète les licences de ceux qui avaient investi dans son procédé et qui avaient échoué, faute de minerai convenable[B 12]. Quant à lui, il se cantonne à l'affinage de fonte suédoise importée, laissant à ses licenciés la possibilité de transformer le minerai local en fer[B 13]. Ceux-ci participent activement à la mise au point du procédé, comme le suédois Göransson qui, grâce à une subvention de 50 000 couronnes suédoises allouée par l'Académie royale des sciences de Suède pour mettre au point le procédé, devient le premier entrepreneur à utiliser industriellement le procédé Bessemer[10].
L'acier Bessemer supplante le fer puddlé et ses dérivés
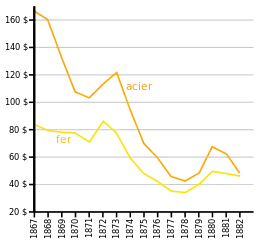
Jusqu'alors, l'acier, obtenu par la cémentation de fer, restait un matériau complexe à fabriquer. On l'obtenait en chauffant du fer produit par puddlage en contact avec du charbon de bois, pendant 6 semaines[B 1]. Si la lenteur du puddlage comme de la cémentation garantissent la qualité du métal, le coût des combustibles pénalise sa diffusion. L'acier naturel comme l'acier au creuset partagent ce handicap : l'amélioration du procédé par Benjamin Huntsman ne concerne en effet que la qualité du métal produit. Quel que soit le procédé, la production reste aussi tributaire de la disponibilité du charbon de bois. Un tel matériau est donc coûteux : 50 à 60 £ la long ton[B 1] (soit environ 3 390 à 4 070 £ en 2008[11]).
Avec le convertisseur de Bessemer, l'utilisation nécessaire de ferromanganèse à la fin du soufflage recarbure le fer. L'obtention d'un fer malléable est donc difficile mais, avec un peu de rigueur, cette recarburation devient une opportunité pour transformer le fer en acier[T 1]. En effet, si « le procédé n'est pas adapté à la production de fer doux, il devient, avec quelques modifications, capable de produire de l'acier de bonne qualité, avec une grande étendue de composition et de solidité[Ba 8] ».
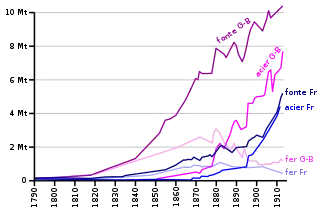
En outre, avec l'aide du colonel Eardley Wilmot, Bessemer insiste sur la qualité du fer coulé qui, contrairement au fer puddlé, ne dépend pas du cinglage puisqu'il est exempt de laitier. Désireux de prouver que son matériau est adapté aux exigences militaires les plus contraignantes, Bessemer propose même que les royalties versées par l'arsenal de Woolwich ne soient exigibles que si le procédé est nettement plus compétitif que les fours à réverbère employés jusqu'alors[B 32]. Il explique au War Office que son procédé est 10 fois moins cher et produit des lingots homogènes de 5 tonnes au lieu de 25 kilos[B 33]. Pourtant, échaudé par les échecs de quelques maîtres de forges, le successeur de Wilmot n'adoptera pas son procédé. Bessemer insiste en forgeant les premiers canons en acier, aux caractéristiques très supérieures aux canons en fer[B 34] - [alpha 17].
Ces essais ne sont pas isolés et les avantages de l'acier Bessemer sont largement admis par l'ensemble des métallurgistes. L'industrialisation de ce métal est en route. Dès le début des années 1860, les métallurgistes français Gruner et Lan affirment sans détour qu'« il est bien évident pour nous que l'acier puddlé, ainsi que le fer puddlé aciéreux (fer à grains), ont fait leur temps. Ils vont céder le pas à l'acier Bessemer, comme ils ont remplacé eux-mêmes l'ancien acier de forge et l'acier cémenté plus ou moins corroyé[12]. »
L'acier : un produit performant mais exigeant
La supériorité de l'acier sur le fer a été démontrée à de nombreuses reprises : en jouant à la fois sur la teneur en carbone et sur les traitements thermiques, le métallurgiste peut obtenir un matériau plus dur, plus résistant tout en restant suffisamment ductile. En 1856, Mushet pose un rail en acier qui, après six ans, apparaît comme neuf là où des rails en fer ne dépassaient pas 3 mois. Quelques années après, Bessemer démontre que la durée de vie d'un rail en acier atteint 20 fois celle d'un rail en fer[T 2].
Mais Bessemer constate que les traitements thermiques de l'acier sont inconnus des industriels. La maîtrise de la teneur en carbone exige également un évident savoir-faire, même s'il est « bien connu que la soudure de grandes masses de fer puddlé engendre plus de risques et d'aléas dans son résultat que n'importe quelle étape du procédé Bessemer[B 35] ».
En effet, la mise en œuvre de l'acier réclame des compétences rares à l'époque :
« Les maîtres de forges avaient l'habitude de produire des barres de fer à partir de n'importe quelle qualité de fonte brute, et ils ne pouvaient pas comprendre que du bon acier ne pouvait être fait qu'à partir d'une qualité bien précise de fonte.[…] Ils utilisaient de la fonte hématite de qualité inférieure, ou réalisaient des mélanges de fontes phosphoreuses pour en baisser le coût.[…]
L'adoption de mon procédé à la fabrication de rails ne risquait guère de lui porter préjudice[…]. Mais lorsqu'il fut question de réaliser des tôles pour chaudières ou pour bateaux[alpha 18], le maître de forge inexpérimenté, avec ses ouvriers inexpérimentés, commencèrent à réaliser que l'acier demandé exigeait un bon niveau de qualité pour certains usages, et qu'il fallait former les ouvriers pour produire les différentes nuances d'acier demandées. Il n'est alors pas étonnant, dans un tel contexte, que l'acier Bessemer ait eu la réputation d'être peu fiable. Des centaines d'ouvriers n'avaient jamais travaillé une tôle d'acier de leur vie, et ignoraient tout de son traitement particulier[B 36]. »
— H. Bessemer, Sir Henry Bessemer, F.R.S. An autobiography, p. 193-194
Toutes ces incertitudes font que Gustave Eiffel construit sa tour en fer puddlé en 1889 alors que la supériorité de l'acier avait été généralement admise. Si elle avait été achevée, la tour de Watkin, d'architecture identique mais construite en acier, aurait dominé de 46 mètres le monument parisien[14].
- Premier lingot de métal obtenu par Bessemer. Celui-ci démontre qu'il s'agit de fer en l'entaillant avec une hache.
- Essai d'emboutissage profond sur un acier Bessemer pour chaudière. L’absence d'inclusion, et donc d'amorces pour des déchirures, garantit la sécurité à haute pression.
Déclin du procédé
L'amélioration de Thomas
À cause de son incapacité à déphosphorer, le convertisseur de Bessemer reste une invention marginale dans la plupart des pays. Bessemer va rechercher activement, mais sans succès, une méthode pour adapter le convertisseur à la déphosphoration[8].
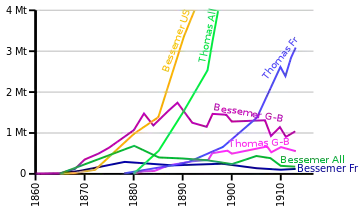
Le revêtement mis au point par Thomas, consistant en de la dolomie cuite avec du goudron, ne semble pas révolutionner le procédé. Pourtant, la conduite du soufflage est différente : l'oxydation du phosphore étant très exothermique, il n'est plus nécessaire d'élaborer des fontes riches en silicium. La basicité du laitier favorise aussi la production de silice mais gêne celle de l'oxyde de manganèse[15]. Mais il n'est plus possible d'interrompre l'élaboration au moment où la décarburation du métal devient suffisante car l'oxydation du phosphore ne se produit que tout à la fin du soufflage[L 11].
Le laitier de déphosphoration étant en outre un excellent engrais, la conduite du convertisseur est optimisée pour en garantir la qualité[16].
C'est surtout la rareté des minerais non phosphoreux, presque inexistants en France et en Allemagne, et minoritaires en Grande-Bretagne, qui marginalise le procédé Bessemer en Europe. Dans quatre pays les plus industrialisés (Allemagne, États-Unis, France et Grande-Bretagne), la proportion d'acier Thomas, proche de zéro en 1880, correspond à 62 % de la production Bessemer et Thomas en 1913[17], sachant que la production états-unienne connaît une croissance spectaculaire (3 380 kt en 1880 et 33 500 kt en 1913) sans utiliser le procédé Thomas[18].
Évolutions et disparition
Le procédé Bessemer ne va donc survivre que là où ne sont produites que des fontes sans phosphore. Il se maintient en Suède, où l'utilisation de convertisseurs fixes positionnés en sortie de haut fourneau s'est brièvement développée[Ba 9]. Les États-Unis n'adopteront jamais le procédé Thomas[18], la fonte phosphoreuse y étant affinée par le procédé Martin-Siemens[T 3].
Si la miniaturisation ou l'amélioration de la tenue du fond du convertisseur inspirent beaucoup de brevets, ces améliorations de l'outil restent marginales, autant par leur aspect novateur que par leur généralisation[L 12]. En revanche, la recherche sur le procédé lui-même va amener des idées plus radicales. Une idée consiste à utiliser un air de soufflage préchauffé. Le principe, simple en apparence et généralisé aux hauts fourneaux, n'est pourtant breveté qu'en 1935[19] et ne débouche sur aucune application pratique. Ce procédé, qui ne se justifie que pour l'affinage de fontes à la fois pauvres en phosphore et en silicium, est d'un intérêt marginal[15]. Mais surtout, il est proposé au moment où l’intérêt économique du recyclage des ferrailles et les contraintes de qualité métallurgiques marginalisent le convertisseur Bessemer et ses dérivés.
L'intérêt d'enrichir de l'air de soufflage avec de l'oxygène est évident et n'échappe pas à Bessemer. L'affinage devient à la fois plus rapide et plus exothermique, ce qui permet de recycler des ferrailles avec le convertisseur[20]. L'addition d'oxygène est donc essayée dès que celui-ci devient disponible à faible coût, grâce aux procédés de liquéfaction de l'air développés par Carl von Linde et Georges Claude. En 1925, à Oberhausen, un convertisseur Thomas fonctionne avec de l'air enrichi. En 1930, la première grande installation de liquéfaction de l'air permet à la Maximilianshütte à Sulzbach-Rosenberg de généraliser l'addition d'oxygène[21] - [B 37]. Après la guerre, le procédé est essayé plus largement en Europe. Celui-ci permet de doper la production des aciéries à un moment où il faut alimenter les usines construites grâce au plan Marshall.
L'azote dissous reste cependant un élément fragilisant pour le fer : l'oxygène pur est donc essayé dès les années 1920. Mais souffler avec un air contenant plus de 40 % d'oxygène présente des difficultés considérables. La réaction de l'oxygène pur avec la fonte mène à des températures de 2 500 °C à 2 700 °C : dans ces conditions, sans utilisation de tuyères refroidies, le fond d'un convertisseur est détruit en quelques heures[22]. L'oxygène est alors dilué dans des gaz dont le craquage à haute température[alpha 19] est endothermique : le dioxyde de carbone est essayé à Domnarvet en Suède en 1947-1949[23], la vapeur d'eau est essayée vers 1950 en France et en Allemagne, puis adoptée dans le Pays de Galles en 1958[alpha 20]. Finalement, la mise au point de tuyères en cuivre, refroidies par une injection périphérique d'hydrocarbures dont le craquage est suffisamment endothermique pour éviter la fusion du cuivre, va achever l'évolution du convertisseur. Mais les procédés développés (LWS, OBM, Q-BOP…) ont alors atteint un niveau de productivité et de complexité[alpha 21] sans aucun rapport avec le convertisseur développé par Bessemer[22].
Notes et références
Notes
- La carburation est l'enrichissement en carbone d'une fonte ou d'un acier. La « recarburation » consiste à réenrichir un acier en carbone après une étape de décarburation.
- Kelly ne revendiquera la paternité de l'affinage à l'air que le 30 septembre 1856, soit 6 semaines après la communication de Bessemer. Le commissaire américain chargé de statuer sur la contestation donnera raison à Kelly[4]. L'attribution de la paternité à Kelly reste très discutable, des considérations autant patriotiques qu'économiques ayant probablement influencé la décision[4] - [5].
- Le liquidus d'une fonte à 6 % C est de l'ordre de 1 150 °C, et passe à 1 500 °C lorsqu'on approche la composition du fer pur.
- Le père d'Henry Bessemer, Anthony Bessemer, est un Français ayant émigré en Angleterre pendant la Révolution française et est membre de l'Académie des sciences. Apprécié en France, son fils Henry s'est vu proposer deux fois la légion d'honneur, mais l'Angleterre y a apposé à chaque fois un veto.
- Bessemer constatera par la suite que s'il avait persévéré dans le développement de son four à réverbère, il aurait peut-être inventé le four Siemens-Martin. Mais, bien que le brevet de Bessemer du 10 janvier 1855 ait été déposé 10 ans avant celui Martin, Bessemer n'intentera aucune contestation d'antériorité.
- William Clay, propriétaire de la Mersey Steel and Iron Co à Liverpool, a été un des pionniers de l'utilisation industrielle du procédé Bessemer.
- Alors que le garnissage réfractaire de la cornue peut durer de 10 000 à 20 000 coulées, le fond ne tient parfois que de 20 à 25 soufflages. Il est donc démontable et certaines aciéries savent le remplacer en une vingtaine de minutes[7].
- Plus d'un siècle après l'invention, ce constat n'a pas changé. La seule amélioration sensible apportée aux convertisseurs modernes consiste en un trou de vidange latéral, distinct du bec de la cornue.
- D'après Ledebur, la combustion de 1 % de phosphore élève la température de 183 °C. C'est un des avantages du convertisseur Thomas qui utilise un carburant plus économique que le silicium[L 7].
- Le brevet de Heath concernait l'addition de manganèse métallique dans l'élaboration de l'acier au creuset. Cette matière étant chère, il conseille alors à ses licenciés d'utiliser de l'oxyde de manganèse. Cette innovation est un succès, mais plus personne ne lui paiera alors une redevance sur son premier procédé. Après 9 ans de procédure, la Chambre des lords lui reconnaît la paternité de l'utilisation de manganèse oxydé, alors qu'il est déjà mort ruiné[P 3].
- Mushet obtient ce métal de Thomas Brown[9], qui réalise des essais sans la licence ni l'expérience de Bessemer[B 15].
- Les recherches de Bessemer permettent d'identifier la franklinite, qui s'avère un bon désoxydant : le zinc de ce minerai se vaporisant au-delà de 907 °C, il ne reste plus que du manganèse et du fer. Mais là encore, c'est le manganèse qui désoxyde l'acier[B 27].
- Mushet n'intentera aucune procédure. Apprenant qu'il vieillit ruiné, Bessemer lui verse, à titre personnel et pendant 25 ans, une confortable pension annuelle de 300 £[B 29].
- Bessemer brevette le 1er février 1861 l'addition de silicium métallique, dosé à 0,045 % du poids de l'acier liquide[P 6].
- Un fer contenant 1 % de silicium se casse de manière fragile vers 600 °C[L 9].
- Chaque lingot ou gueuse sans phosphore est marqué de la lettre « B ». Bessemer prend donc le risque de distinguer son produit, malgré sa mauvaise réputation initiale.
- L'arsenal restera campé sur son refus, se méfiant de la qualité variable du métal produit. Les chapitres XII à XVI de l'autobiographie de Bessemer prouvent à quel point « nul n'est prophète en son pays »…
- L'utilisation d'un métal performant pour les chaudières et les bateaux est intéressante car elle permet de diminuer l'épaisseur des tôles. Dans le cas d'une chaudière, des parois minces améliorent le transfert de chaleur. Mais il s'agit là d'applications sensibles où un défaut métallurgique est rédhibitoire. En outre la tenue à la corrosion est essentielle et ne peut être jugée que dans la durée[13].
- La décomposition thermique de la vapeur commence vers 900 °C pour être totale à 2 500 °C. Celle du dioxyde de carbone commence dès 700 °C.
- Il s'agit du procédé VLN, adopté notamment à Ebbw Vale[24].
- Outre une productivité multipliée par 10, ces nouveaux convertisseurs sont dotés d'une récupération des fumées avant que celles-ci ne s'enflamment au contact de l'air, d'une automatisation imposée par la présence d'oxygène pur et de monoxyde de carbone, etc.[1]
Références
- (en) Henry Bessemer, Sir Henry Bessemer, F.R.S. An autobiography, (voir dans la bibliographie)
- p. 138
- p. 138-139
- p. 142
- p. 143
- p. 143-144
- p. 144
- p. 146-147
- p. 152
- p. 156
- p. 164
- p. 170
- p. 172
- p. 178-180
- p. 174
- p. 291
- p. 148
- p. 149-151
- p. 334
- p. 145
- p. 157
- p. 136
- p. 171-172
- p. 171
- p. 263
- p. 268 - 269
- p. 286
- p. 272-273
- p. 287-289
- p. 293-295
- p. 192
- p. 179
- p. 188
- p. 189
- p. 227-228
- p. 232
- p. 193-194
- p. 55
- Adolf Ledebur, Manuel théorique et pratique de la métallurgie du fer, (voir dans la bibliographie)
- p. 478
- p. 507
- p. 508
- p. 509
- p. 472
- p. 471
- p. 473
- p. 388
- p. 182
- p. 419
- p. 513
- p. 483-491
- (en) Hilary Bauerman, F.G.S, A treatise of the Metallurgy of Iron, (voir dans la bibliographie)
- p. 33
- p. 452-454
- p. 454
- p. 455
- p. 329
- p. 443
- p. 445
- p. 434-435
- p. 436
- (en) Thomas Turner, The Metallurgy of Iron : By Thomas Turner…, (voir dans la bibliographie)
- p. 42
- p. 43
- p. 49
- John Percy (trad. traduction supervisée par l'auteur), Traité complet de métallurgie, t. 4, Paris, Librairie polytechnique de Noblet et Baudry éditeur, (lire en ligne)
- Tome 4, p. 35
- Tome 4, p. 254
- Tome 4, p. 282 - 286
- Tome 2, p. 230
- Tome 1, p. 134
- Tome 4, p. 251
- Autres références
- Olivier C. A. Bisanti, « Un siècle d'oxygène en sidérurgie », Soleil d'acier, (consulté le )
- (en) Robert Hartwell, Markets, Technology and the Structure of Enterprise in the Development of the Eleventh Century Chinese Iron and Steel Industry, Journal of Economic History 26, , p. 53-54
- François Chaubet, La mondialisation culturelle, Paris, Presses universitaires de France, mars 2013 (première édition), février 2018 (deuxième édition), 128 p. (ISBN 978-2-13-080163-4), p. 21
- (en) Philip W. Bishop, The Beginnings of Cheap Steel, Project Gutenberg's, coll. « Contributions from The Museum of History and Technology », (lire en ligne), p. 27-47
- (en) John H. Lienhard, « No. 762: Kelly's converter », The Engines of Our Ingenuity, 1988-1997 (lire en ligne)
- (en) Charlotte Erickson, British industrialists : steel and hosiery 1850-1950, Cambridge University Press, (1re éd. 1959) (ISBN 0-566-05141-9), p. 141-142
- (en) Bradley Stoughton, Ph.B., B.S., The metallurgy of iron and steel, New York, McGraw-Hill Book Company, , 509 p. (lire en ligne), p. 95, 101, 112
- (en) Ralph Anstis, Man of Iron, Man of Steel : Lives of David and Robert Mushet, Albion House, , 216 p. (ISBN 0-9511371-4-X), p. 140, 147
- (en) Robert Forester Mushet, The Bessemer-Mushet process or Manufacture of cheap steel, (lire en ligne)
- (sv) « Göran Fredrik Göransson », sur Riksarkivet
- Lawrence H. Officer & Samuel H. Williamson, « Purchasing Power of British Pounds from 1264 to Present »,
- Emmanuel-Louis Grüner et Charles-Romain Lan, État présent de la métallurgie en Angleterre, Paris, Dunod éditeur, (lire en ligne), p. 825
- (en) William Tulloch Jeans, The Creators of the Age of Steel, , 356 p. (ISBN 1-4179-5381-0 et 978-1417953813, lire en ligne), p. 95-96
- François Landon, La Tour Eiffel, Paris, Ramsay, , 160 p. (ISBN 2-85956-303-2), p. 136
- (en) G. Reginald Bashforth, The manufature of iron and steel, vol. 2 : Steel production, Londres, Chapman & Hall Ltd, , 461 p. (lire en ligne), p. 41 ; 55
- Louis Colombier, Métallurgie du fer, Dunod, , 2e éd., p. 191
- Alexis Aron, « Les conséquences économiques de l'invention de Sidney Gilchrist Thomas (allocution) », La revue de métallurgie, no 12, , p. 18-22
- (en) The journal of the Iron and Steel Institute, vol. XCI, Londres, , 711 p. (lire en ligne), « Statistics », p. 655-657
- « Brevet du convertisseur à air chaud », Office Européen des Brevets
- (en) F. Wallner et E. Fritz, « Fifty years of oxygen-converter steelmaking », Revue de Métallurgie, no 10, , p. 825-837
- P. Leroy et E. Devernay, « Essais de soufflage au convertisseur Thomas ... l'air enrichi ... l'oxygène », La revue de métallurgie,
- Leroy et al., « Soufflage d'oxygène pur par le procédé LWS », La revue de métallurgie,
- Kalling et al., « Emploi d'oxygène-acide carbonique au lieu d'air pour le soufflage final dans le procédé Thomas », La revue de métallurgie,
- (en) Robert Protheroe-Jone, Welsch steel, , 60 p. (ISBN 0-7200-0424-1, lire en ligne), p. 50
Voir aussi
Bibliographie
- (en) Henry Bessemer, Sir Henry Bessemer, F.R.S. An autobiography, (lire en ligne)
- Adolf Ledebur (trad. Barbary de Langlade revu et annoté par F. Valton), Manuel théorique et pratique de la métallurgie du fer, Tome I et Tome II, Librairie polytechnique Baudry et Cie éditeur, (Tome 1 et Tome 2 à)
- (en) Hilary Bauerman, F.G.S (ill. J. B. Jordan), A treatise of the Metallurgy of Iron, Londres, Crosby Lockwood and Son, coll. « Weale's scientific & technical series / Mining and metallurgy », , 6e éd. (1re éd. 1868) (lire en ligne)
- (en) Philip W. Bishop, The Beginnings of Cheap Steel, Project Gutenberg's, coll. « Contributions from The Museum of History and Technology », (lire en ligne), p. 27-47
- (en) Thomas Turner (dir.), The metallurgy of iron : By Thomas Turner... : Being one of a series of treatises on metallurgy written by associates of the Royal school of mines, C. Griffin & company, limited, coll. « Griffin's metallurgical series », , 3e éd., 463 p. (ISBN 1-177-69287-2 et 978-1177692878, lire en ligne)
- (en) Robert Forester Mushet, The Bessemer-Mushet process or Manufacture of cheap steel, (lire en ligne)
- (en) Bradley Stoughton, Ph.B., B.S., The metallurgy of iron and steel, New York, McGraw-Hill Book Company, , 509 p. (lire en ligne), p. 95, 101, 112