Procédé Krupp-Renn
Le procédé Krupp-Renn est un procédé sidérurgique de réduction directe utilisé pendant les années 1930 à 1970. Fondé sur l'utilisation d'un four rotatif, il s'agit d'un des rares procédés de réduction directe ayant connu un succès technique et commercial dans le monde.
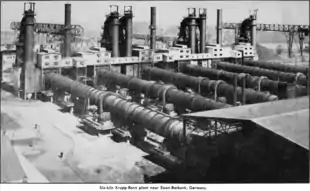
À l'instar de la majorité des procédés de réduction directe, il est une alternative aux hauts fourneaux, dont la rentabilité est pénalisée par la consommation de coke. Consommant essentiellement de la houille, le procédé Krupp-Renn a la particularité de réaliser une fusion partielle de la charge enfournée. Ainsi, il est approprié au traitement des minerais pauvres ou infusibles, car leur gangue génère un laitier protecteur et facile à séparer du fer. Il produit des nodules de minerai de fer préréduit, les Luppen, qui peuvent être facilement refondus.
Les premiers fours industriels apparaissent au cours des années 1930, dans l'Allemagne nazie puis dans l'Empire du Japon. Dans les années 1950, quelques usines neuves sont construites, notamment en Tchécoslovaquie et en Allemagne de l'Ouest. Le procédé est abandonné au début des années 1970, non sans avoir engendré quelques variantes.
Peu productif, difficile à maîtriser et pertinent uniquement avec des minerais particuliers, le procédé ne survit plus, au début du XXIe siècle, qu'au Japon où, sous une forme modernisée, il permet la production de ferronickel.
Histoire
Mise au point
Le principe de la réduction directe du minerai de fer par un brassage à haute température de poudre de minerai mélangée avec du charbon, avec un peu de calcaire pour diminuer l'acidité du minerai, a été testé dès la fin du XIXe siècle. On peut notamment relever le procédé de réduction directe de Carl Wilhelm Siemens[1], utilisé de manière épisodique aux États-Unis et au Royaume-Uni dans les années 1880. Ce procédé est fondé sur l'utilisation d'un court tambour de 3 m de diamètre et autant de long, d'axe horizontal, où sont insufflés des gaz préchauffés par deux régénérateurs[2].
L'utilisation de four tubulaire rotatif en métallurgie, inspiré de ceux utilisés en cimenterie, suscite alors de nombreuses recherches. Le procédé Basset, développé dans les années 1930, permet même de produire de la fonte en fusion[3]. Le métallurgiste allemand Friedrich Johannsen, chef du département métallurgie à l'usine Gruson et professeur à l'École des mines de Clausthal[4], s'intéresse, dans les années 1920, aux applications métallurgiques de ce type de four. Il dépose une série de brevets relatifs au retrait des métaux volatils indésirables présents dans les matières premières sidérurgiques[5].
Dans les années 1930, Johannsen commence à mettre au point la production de fer par réduction directe. La première installation est essayée de 1931 à 1933, dans l'usine Gruson à Magdebourg[6]. Les recherches se déroulent également à l'usine Krupp de Essen-Borbeck, jusqu'en 1939. Le procédé, baptisé « Krupp-Renn », fait référence à l'entreprise Krupp, qui l'a développé, et au Rennfeuer, qui désigne le bas fourneau[7]. Il est prometteur et, à partir de 1932, Krupp dépose des brevets hors d'Allemagne afin de protéger l'invention[8].
- Four de réduction directe inventé par Siemens.
- Brevet de 1927 de Johannsen sur un four de récupération d'éléments volatils.
- Premier brevet américain de Johannsen sur le procédé Krupp-Renn, déposé en 1934.
Adoption
En 1945, on recense 38 fours. Quoiqu'ils ne totalisent alors qu'une capacité de 1 Mt/an[note 1], ils sont présents partout dans le monde[10]. En Allemagne, le procédé avait été favorisé par la politique d'autarcie du régime nazi, qui privilégiait l'utilisation des minerais de fer nationaux de mauvaise qualité, plutôt que la rentabilité[11]. L'Empire du Japon bénéficie d'un transfert de technologie dans le contexte des liens entre l'Allemagne nazie et le Japon impérial. Des fours sont installés dans la sphère de coprospérité et les techniciens japonais s'approprient le procédé. À la veille de la guerre du Pacifique, les Japonais l’exploitent dans 4 aciéries[12].
Après la Seconde Guerre mondiale, toutes les installations en Allemagne, en Chine et en Corée sont démantelées[13]. Parmi celles-ci, 29 sont envoyées en URSS comme réparation de guerre[14]. Seules les installations tchécoslovaques et japonaises demeurent intactes[13].
Dans les années 1950, Krupp reconstruit quelques gros fours, notamment en Espagne, Grèce et Allemagne[10] - [13]. Tout particulièrement, les Tchécoslovaques s'en font les principaux promoteurs, en construisant 16 fours et en améliorant l'efficacité du procédé[15]. Selon la Grande Encyclopédie soviétique, plus de 65 installations industrielles (60 à 110 m de long et 3,6 à 4,6 m de diamètre) sont construites des années 1930 à 1950[6]. En 1960, 50 fours fonctionnent dans divers pays, produisant 2 Mt/an[16].
Disparition
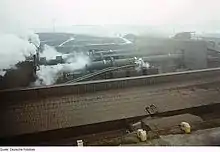
L'URSS, qui récupère 29 fours comme dommage de guerre n'en tire guère de profit. En effet, « les méthodes destructives et inappropriées de l'Armée soviétique pour démanteler les installations industrielles allemandes ont été un énorme gaspillage, et il s'est avéré difficile pour les Russes de reconstituer ces usines en Union soviétique. Les étrangers qui ont voyagé en train de Berlin à Moscou ont rapporté que chaque [mètre] de voie ferrée et d'accotement était encombré de machines allemandes, la plupart se détériorant dans la pluie et la neige[18]. » Mais la sidérurgie russe est assez peu dépendante de l'apport technologique de l'Ouest[19], et le bloc de l'Est n'entretient finalement guère cette technologie marginale que dans les pays d'Europe récemment soviétisés[20], où elle est aussi progressivement abandonnée[16].
En Allemagne de l'Ouest, les gros fours reconstruits dans les années 1950 fonctionnent une dizaine d’années avant d'être arrêtés, victimes du faible coût des ferrailles et du minerai importé[note 2]. Le procédé disparaît alors de l'Allemagne de l'Ouest, en même temps que de l'Europe de l'Ouest[13].
Au Japon, les fours évoluent eux aussi vers des outils de plus en plus gros. Mais là aussi, l'épuisement des gisements locaux de sables ferrugineux, combiné au faible coût des ferrailles et des minerais importés, amène à l'abandon progressif du procédé. Pour autant, les Japonais l'améliorent régulièrement, le faisant évoluer sous d'autres appellations et sur des productions spécialisées, comme les ferroalliages[13] ou la valorisation de sous-produits sidérurgiques[21]. Au début du XXIe siècle, il n'y a qu'au Japon que le procédé Krupp-Renn est explicitement utilisé pour la production de ferronickel[22].
En 1972, la plupart des usines tchécoslovaques, japonaises et ouest-allemandes ne fonctionnent plus : le procédé est considéré comme globalement obsolète et ne retient plus l'attention des industriels[16].
Procédé
Principes généraux
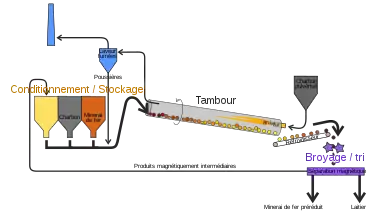
Le procédé Krupp-Renn est un procédé de réduction directe dont le réacteur est un long four tubulaire identique à celui utilisé dans les cimenteries. Dans les dernières unités construites, celui-ci mesure environ 4,5 m de diamètre et 110 m de long[10]. Le four rotatif est incliné d’environ 2,5 % ; sa pente et sa vitesse de rotation influent sur la durée de séjour du produit[23].
Le minerai de fer est premièrement broyé pour atteindre une granulométrie inférieure à 6 mm[10]. Il est ensuite introduit à l’amont du four, mélangé avec un peu de combustible (généralement de la houille)[23]. Au bout de 6 à 8 heures[24], il ressort du four à l’extrémité opposée, sous la forme d’un minerai de fer préréduit à 1 000 °C. Le fer récupéré atteint 94 % à 97,5 % du fer initialement présent dans le minerai[23].
La chaleur est apportée par un brûleur situé à l’extrémité inférieure du four, qui fonctionne donc comme un réacteur à contre-courant. Le combustible consiste en un charbon finement pulvérisé, dont la combustion à haute température génère en outre le gaz réducteur, essentiellement du CO. Une fois le four chaud, l’essentiel du combustible peut être apporté par le mélange minerai-houille[23].
Les fumées qui sortent par l’extrémité supérieure du four atteignent 850 à 900 °C. Elles sont donc refroidies et débarrassées de leur poussière par une injection d’eau avant d’être évacuées à la cheminée[23].
Le procédé est efficace dans la production de ferronickel à cause de la proximité chimique des deux éléments. En effet, les oxydes de fer et de nickel sont, à 800 °C, facilement réduits par le carbone[note 3] alors que les autres oxydes constituant la gangue du minerai sont peu ou pas réduits. Notamment, l'oxyde de fer(II) (ou la wustite), qui est l'oxyde de fer stable à 800 °C, présente une réductibilité proche de celle de l'oxyde de nickel(II) : il n'est donc pas possible de réduire l'un sans l'autre[25].
Particularités du procédé
La température maximale dans le four rotatif, comprise entre 1 230 et 1 260 °C, est beaucoup plus élevée que les 1 000 à 1 050 °C strictement nécessaires à la réduction des oxydes de fer. L'objectif est d'amener la gangue du minerai à l'état pâteux[23]. Le fer réduit peut alors s'agglomérer en nodules métalliques 3 à 8 mm, les Luppen[9]. Si la gangue est très infusible, la température doit être augmentée, jusqu'à 1 400 °C pour une charge basique[24] : la maîtrise de la viscosité à chaud de la gangue est un point clé[10]. Parmi les procédés de réduction directe par tambour rotatif, il se distingue donc par les hautes températures mises en œuvre :
![]() | |||||
1 | 2 | 3 | 4 | 5 | |
Consistance du produit obtenu | solide | pâteux | solide (clinker) liquide (fonte) | ||
---|---|---|---|---|---|
Température maxi (°C) | 600-900 | 900-1100 | 1200-1300 | 1400-1500 | |
Réduction (% de O2 retiré du Fe2O3) | 12 % | 20-70 | >90 | 100 | |
Exemples de procédés | Lurgi (de) | Highveld Udy Larco Elkem |
RN SL/RN Krupp |
Krupp-Renn | Basset |
La gestion de l’injection de charbon pulvérisé à la sortie du four est une autre particularité du procédé. Les évolutions postérieures du procédé autorisent la possibilité de couper cette alimentation en charbon, et de ne fonctionner qu’avec le charbon (ou du poussier de coke[27]) introduit avec le minerai[23]. Dans ce cas, seul l'air de combustion est injecté à la sortie du four. Le rendement thermique, qui pénalise les fours tournants vis-à-vis des fours à cuve comme les hauts fourneaux, est ainsi amélioré car l'air absorbe une partie de la chaleur des Luppen. Mais l'oxygène de cet air ré-oxyde partiellement le produit[15]. Ainsi, même si le fer peut être complètement réduit dans le four, les Luppen sont toujours altérés par le contact de l'air à la fin ou après la sortie du four[7].
L’ensemble est déchargé chaud du four. Il est alors refroidi violemment, puis broyé. Le fer est séparé du laitier par un tri électromagnétique. Les fines magnétiquement intermédiaires représentent 5 à 15 % de la charge enfournée[24]. La fusion partielle de la charge augmente la densité des préréduits, mais implique aussi une coûteuse consommation d'énergie[23].
Comportement de la charge pendant la traversée du four
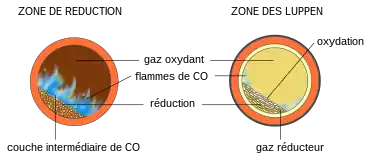
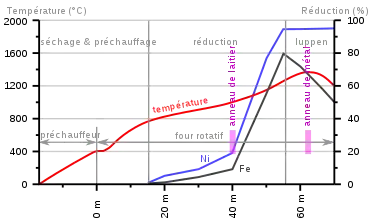
On distingue 3 zones dans le four[23] - [24] - [28] :
- la zone amont, dite de préchauffage, où le minerai est chauffé jusqu’à 800 °C par les fumées chaudes remontant dans le four. Tant que la température reste inférieure à 900-1 000 °C, la réduction du minerai est minime et le charbon rejette ses matières les plus volatiles ;
- le milieu du four, dite zone de réduction, où le charbon se combine avec les oxydes de fer pour former du monoxyde de carbone. Ce monoxyde de carbone s'échappe de la charge et forme une couche gazeuse qui protège la charge de l'air oxydant circulant au-dessus. Puis ce gaz excédentaire brûle, chauffant les parois du four qui restituent ensuite, grâce au mouvement de rotation, la chaleur à la charge. La température monte progressivement à 800 - 1 200 °C. Les oxydes de fer se transforment progressivement en fer métallique, ou en ferronickel. Le métal obtenu se présente sous la forme de particules d'éponge métallique qui restent finement dispersées dans la gangue pulvérulente ;
- à la fin du four, la réduction est complète. Seule une faible quantité de CO est produite : la charge n'est plus protégée de l'oxydation par l'air soufflé à la base du four. Une réoxydation violente mais superficielle du fer se produit donc. La rotation ramène une partie du fer oxydé au cœur de la charge, ou elle est de nouveau réduite par le charbon résiduel. Le reste se mélange aux stériles pour former une scorie visqueuse et immiscible avec le métal produit. Cette réaction très exothermique va permettre la fusion du fer et du nickel non oxydé, qui s’agglomèrent sous la forme de nodules, les Luppen.
Le contrôle de la température, en relation avec le comportement physico-chimique du minerai, est un point critique. Une température excessive ou une granulométrie inadaptée génèrent des anneaux de matières frittées qui garnissent les parois du four. Généralement, un anneau de laitier, c'est-à-dire de scories pauvres en fer, se constitue aux deux tiers de la longueur du four. De même, un anneau métallique a tendance à se former à une dizaine de mètres de la sortie. Ces anneaux perturbent l'écoulement des matières et du gaz et réduisent le volume utile du four… quand ils ne l'obstruent pas complètement. Cette formation d'anneaux contrecarre la résurrection du procédé, notamment en Chine où, au début du XXIe siècle, les industriels ont renoncé à l'adopter après avoir constaté la criticité et la difficulté de gérer ce paramètre[28].
La fusion du laitier consomme de l'énergie mais permet de maîtriser le comportement de la charge dans le four. De fait, un minimum de 800 à 1 000 kg de laitier par tonne de fer est requis pour ne pas obtenir des Luppen trop gros[29]. Le laitier limite aussi la ségrégation du charbon qui, beaucoup moins dense que le minerai, resterait en surface du mélange. Puis, à chaud, il devient une pâte qui protège le métal de l'oxydation. Enfin, à froid, sa vitrification simplifie autant le traitement des Luppen que le nettoyage du four lors des arrêts de maintenance[27].
Performances avec des minerais pauvres
À l’instar de la plupart des procédés de réduction directe, le procédé Krupp-Renn est adapté à la production de minerai de fer préréduit à partir de minerais très siliceux, donc acides (indice de basicité CaO/SiO2 de 0,1 à 0,4[30]), qui génèrent un laitier pâteux dès 1 200 °C. De plus, l'acidité du laitier le rend vitreux, donc facile à concasser et à séparer du fer[15]. Plus marginalement, le procédé est aussi parfaitement adapté au traitement des minerais riches en dioxyde de titane. En effet, cet oxyde rendant le laitier particulièrement infusible et visqueux, les minerais qui en contiennent sont incompatibles avec les hauts fourneaux, qui doivent évacuer toute leur production sous la forme liquide[23]. Les minerais de prédilection du procédé sont ainsi ceux qui perdraient leur intérêt économique s'il fallait les amender avec des additifs basiques, typiquement ceux qui sont peu riches en fer (entre 35 et 51 %) et dont la gangue doit être neutralisée[7].
Intégré dans un complexe sidérurgique traditionnel, le procédé est une alternative aux procédés d'enrichissement ou à l'usine d'agglomération[24]. En effet, il peut retirer les stériles et les éléments indésirables, comme le zinc, plomb ou étain. Dans un haut fourneau, ces éléments subissent un cycle continuel de vaporisation-condensation qui le sature progressivement. Avec le procédé Krupp-Renn, la haute température des fumées évite leur condensation dans le four avant leur récupération dans les installations de dépoussiérage[30]. Ainsi, le procédé est un moyen de valoriser des sous-produits ou d'extraire certains métaux. Les Luppen sont ensuite refondues au haut fourneau, voire au cubilot ou au four Martin-Siemens, car il ne s'agit alors que de fondre une charge préréduite et riche en fer[24].
Le procédé s'est avéré adapté aux traitements de minerais riches en oxydes de nickel, de vanadium, etc.[10]. Une autre utilisation de ce procédé est ainsi la production de ferronickel[30]. Dans ce cas, les minerais saprolitiques, pauvres et très basiques (à cause de leur teneur en magnésie[31]), sont tout aussi infusibles que les minerais très acides, et le procédé reste pertinent[12].
Comme la plupart des procédés de réduction directe, il est aussi possible d’utiliser à peu près n’importe quel combustible solide. Il faut 240 à 300 kg de houille pour traiter une tonne de minerai de fer contenant 30 à 40 % de fer. En retenant une consommation de 300 kg/t de minerai à 30 %, la consommation de houille est de 800 kg par tonne de fer, à laquelle il faut ajouter la fusion des Luppen au haut fourneau, qui consomme 300 kg de coke. Quand elle est faite entièrement au haut fourneau, la fusion de ce même minerai aboutit à une consommation totale de combustible identique… mais il s'agit exclusivement de coke, un combustible bien plus coûteux que la houille[24].
Par contre, le fonctionnement avec des laitiers contenant souvent plus de 60 % de silice, donc acides, est incompatible avec la désulfuration du métal, qui nécessite des laitiers très basiques[32]. Ainsi, 30 % du soufre apporté par les combustibles se retrouve dans le fer[10] et un coûteux traitement postérieur est alors nécessaire pour l'éliminer[23] - [note 4].
Productivité
Selon les minerais et la taille de l'installation, la production quotidienne d'un four est de 250 à 800 tonnes de minerai de fer préréduit[6]. Les plus gros fours, qui atteignent 5 m de diamètre et 110 m de long, peuvent traiter 950 à 1 000 tonnes de minerai par jour, combustible non compris. Lorsqu'elle est bien conduite, une installation tourne environ 300 jours par an. La durée de vie du réfractaire interne est de 7 à 8 mois dans la partie la plus exposée du four, et 2 ans ailleurs. Ainsi, en 1960, un gros four Krupp-Renn alimenté en minerai pauvre produit 100 kt/an de fer[30], alors qu'un haut fourneau moderne de la même époque produit 10 fois plus de fonte[34].
Une des difficultés majeures, commune à tous les procédés de réduction directe par four rotatif, consiste en la formation locale d'un anneau de fer et de scories, frittés ensemble, un garni qui obstrue progressivement le four. La compréhension du mécanisme de formation de ce garni est complexe car elle fait intervenir la minéralogie, mais aussi la chimie du procédé (quelques éléments en quantité infimes suffisent à faire croître progressivement l'anneau et ainsi empoisonner progressivement le four) et la préparation du minerai (granulométrie, humidité…). Pour y remédier, augmenter l'apport d'air de combustion, voire interrompre la charge du four, est un moyen efficace de refondre ces anneaux[24]. Sinon, il faut corriger la granulométrie du minerai enfourné[35] ou corriger la chimie du mélange minéral enfourné[36].
En 1958, une usine complète construite par Krupp, pouvant produire 420 000 t/an de minerai de fer préréduit (soit une batterie de 6 fours), est estimée 90 millions de Deutsche Mark[30] - [29], ou 21,4 millions de dollars[37]. L'usine construite en 1956-1957 à Salzgitter-Watenstedt, bien intégrée dans un site sidérurgique existant, n'a cependant coûté que 33 millions de Deutsche Mark[11]. À cette époque, les coûts d'investissement et de fonctionnement d'une installation Krupp-Renn en font une alternative viable au procédé de référence, le haut fourneau : l’investissement initial ramené à la tonne produite est presque 2 fois inférieur, mais les frais de fonctionnement sont presque 2,5 fois plus élevés[37].
Le laitier, une silice vitrifiée, s'avère facile à valoriser comme additif dans les revêtements de chaussée ou dans le béton[32]. Toutefois, le procédé ne génère pas de gaz valorisable comme celui issu des hauts fourneaux, ce qui pénalise sa rentabilité dans la plupart des contextes[24], mais aussi résout la question de sa valorisation[9].
Usines construites
Nombre de fours | Emplacement | Propriétaire à la mise en service |
Diamètre interne (m) | Longueur (m) | Capacité (tminerai/j) | Date mise en service | Date d’arrêt | Remarques |
---|---|---|---|---|---|---|---|---|
1 | Magdebourg (Allemagne) | F. Krupp | 0,7 (externe ou interne inconnu) | 8 | 2,5[9] | 1931[6] | 1933[6] | Premier four expérimental[39] - [32]. |
1 | Rheinhausen (Allemagne) | F. Krupp | 0,9 | 14 | 6 | NC | 1939[7] | Prototype A évolué pour explorer la faisabilité d'une variante du procédé Krupp-Renn, le procédé Krupp-Eisenschwamm[40]. |
1 | Essen-Borbeck (Allemagne) | F. Krupp | 3,6 | 50 | 275-300 | 1935 | 1945 | Démonstrateur industriel. Capacité de 250–280 t/j selon les Soviétiques[38]. Transféré en Union soviétique en 1945. |
2 | Frankenstein (Silésie) Ząbkowice Śląskie (Pologne) | F. Krupp Zakłady Górniczo-Hutnicze „Szklary” | 3,6 | 50 | 2 × 250-280[38] 2 × 275-300 | 1935 et 1941 1950-1953[41] | 1945 1982[41] | Transférés en Union Soviétique en 1945 puis reconstruits à l'identique[note 6] par les Polonais. Traitement de garniérite (9 % de fer, 61 % de SiO2 et 0,73 % de nickel). |
4 4 | Anshan (Mandchoukouo) | Aciéries Shōwa Anshan I&S | 3,6 | 60 | 4 × 60[42] 8 × 300 | 1939[43] 1948[44] | 1945[45] NC | 6 fours supplémentaires commandés mais jamais installés à cause de la guerre. Transférés en Union soviétique après la guerre[45]. Reconstruits à l'identique en 1948[44] avec 4 fours supplémentaires. Minerai contenant 35-36 % de Fe et 40-48 % de SiO2. |
4[note 7] 2 1 | Seishin (Corée[note 8]) | Mitsubishi Shoji Kaisha | 3,6 | 60 | 4 × 300 | 1939[48] 1945-1954 avant 1964 | 1945[45] NC | Transférés en Union soviétique après la guerre[45]. 7 fours en 1964. Magnétite contenant 55-60 % de Fe, ou limonite contenant 46-52 % de Fe. |
2[note 9] | Kuji (Japon) | Kawasaki Dockyard | 1,8[49] 1,8[49] | 25[49] 15[49] | 20 (est[note 9].) | 1939[50] | entre 1964[38] et 1967[13] | Petits fours de séchage reconvertis[50]. Fours arrêtés en 1945 et redémarrés en 1949[13]. |
4 | Ōeyama (Japon) | Nihon Yakin Kogyo | 3,6 | 70 | 500-600 | 1940-1942 | 1945 | Minerai de fer contenant du nickel. |
1 2 | Nanao (Japon) | Iwaki Cement Co[42] | 3,45 3,45 | 88[note 10] 73 | 3 × 70,7[42] | 1940[49] | NC | Fours de cimenterie modifiés. Minerai contenant 26 % de Fe, 24-29 % de SiO2, 0,6 % de Ni, 1,4 % de Cr. En service en 1964 selon les sources soviétiques. |
1 | Onishi (Japon) | Nippon Nickel Co[42] | 2,8[42] | 50[42] | 60[42] | vers 1940[42] | NC | Les Luppen contiennent 1,3 % de Ni et 0,6 % de Cr[42]. |
2 | Hirai (Japon) | Riken Industrial Corp.[note 11] - [42] | 2,3[42] | 38[42] | 2 × 36[42] | vers 1940[42] | NC | Mélange de minerais limonitiques locaux et importés. Les Luppen contiennent 1,7 % de Ni et 2,1 % de Cr[42]. |
2 | Fushun (Mandchoukouo) | Aciéries Shōwa | 3,0[42] | 60[42] | 2 × 60[42] | vers 1940[42] | NC | Magnétite[42]. |
2 | Kuji (Japon) | Kawasaki Dockyard | 3,6 | 60 | 2 × 300 | 1941[51] | 1967[13] | Fours arrêtés en 1945 et redémarrés en 1957-59[13]. Minerai contenant 34-35 % de Fe et 5-8 % de TiO2. |
1 2 | Králův Dvůr (Tchécoslovaquie) | Králodvorských železárnách Hrudkovny Praha[52] | 3,6 | 60 | 3 × 300-325 | 1943[note 12] vers 1955[52] | vers 1966[53] | Minerai contenant 30-35 % de Fe et 24 % de SiO2 (pélosidérite + chamosite + hématite). |
3 | Salzgitter-Watenstedt (Allemagne) | F. Krupp | 4,2 | 70 | 3 × 500 | 1943-1945[note 13] | 1950 | Donné comme réparations de guerre en 1950. Minerai contenant 25-30 % de Fe. |
2[54] | Ōeyama (Japon) | Nihon Yakin Kogyo | 3,6 | 70 | 500-600 | 1952[55] | en service (2014)[22] | Saprolite riche en nickel (>2,5 % Ni) importée de Nouvelle-Calédonie[54]. Le procédé original a été fortement modifié et les Luppen contiennent 18-22 % de Ni[55]. |
2 | Unterwellenborn (RDA) | VEB Maxhütte Unterwellenborn | 3,6 | 60 | 2 × 300 - 400 | 1953 | 1968[56] | Chamosite et limonite siliceuse[15]. Mélange contenant contenant 33 % de fer, 10,5 % de Al2O3 et 27 % de SiO2. En 1957, projet de construction d'un 3e four, jamais concrétisé[38] - [56]. |
1 2[note 14] | Avilés (Espagne) | Siderúrgica Asturiana, S. A. | 3,6 4,6[note 14] | 60 70[note 14] | 250-275 NC | 1954 vers 1960 | 1971[57] | Hématite contenant 30-40 % de Fe et 20-30 % de SiO2. |
3 | Mníšek (Tchécoslovaquie) | Kovohutě Mníšek | 3,6 | 60 | 3 × 300-350 | vers 1954[58] | 1967[53] | Minerai contenant 30-35 % de Fe et 24 % de SiO2 (pélosidérite + chamosite + hématite). |
10 | Ejpovice (Tchécoslovaquie) | RND Ejpovice[59] | 3,6 | 60 | 10 × 300-350 | 1956[58] | 1966[58] | Sur la période, 2,827 Mt de Luppen à 82-83 % de fer ont été produits[58], à partir de minerai contenant 30-35 % de Fe et 24 % de SiO2 (pélosidérite + chamosite + hématite). |
1[note 15] | Lárymna (Grèce) | Hellenic Company of Chemical Products & Fertilizers Ltd. | 4,2 | 90 | 400 | 1956 | 1963[60] | Minerai contenant 35 % de Fe et 1,5-1,75 % de Ni, les Luppen contiennent 4 % de nickel. Échec technique : adoption du procédé LM en 1963, puis Larco en 1966 afin de déporter la fusion du préréduit dans un four électrique[60]. |
2 2 | Salzgitter-Watenstedt (RFA) | Rennanlage Salzgitter-Ruhr GbR. | 4,2 4,6 | 95 110 | 2 000 | 1956 1957 et 1960 | 1963[11] | Minerai siliceux du Harz contenant 28-34 % de Fe. |
2 1 | Sabinów k. Częstochowy (Pologne) | Zakłady Górniczo-Hutnicze „Sabinów” | 3,6 4,2 | 60 70 | 340 et 360[27] 460[27] | 1958[61] | 1971[62] | Sidérite contenant 31-33 % de Fe[27] et 25 % de SiO2. L'écart de productivité entre les deux premiers fours vient de leur inclinaison (respectivement 2 et 3°)[27]. |
1[63] | Minnesota (États-Unis) | South Western Engineering | 2,7 | 53,4 | NC | 1959 | vers 1962[7] | Usine pilote construite sous licence Krupp pour évaluer la valorisation du gisement de Mesabi Range : 12 000 t de minerai y ont été transformées en 5 000 t de Luppen. Minerai contenant 47 % de Fe et 18 % de Ti2O2. |
6 | Essen-Borbeck (RFA) | F. Krupp | 4,6 | 110 | 4 200 | 1959-1960 | 1963[64] | Mélange à 35 % de Fe constitué de minerais importés et de crasses limonitiques. |
1 1[65] | Novotroïtsk (URSS) | Combinat Métallurgique d'Orsk-Khalilovo | 3,6 | 60 | 2 × 250-300[65] | 1960[66] 1963-1973[65] | NC | Limonite d'Ackerman (Khabarninsky) contenant 32-45 % de Fe, 1,26 % de Cr et 0,52 % de Ni, ou limonite d'Orsk-Khalilovo contenant 18 % de Fe, 0,6-1,16 % de Cr. Gangue de SiO2 et Al2O3. Chaque four produit 55–60 t/j de Luppen contenant 1,2-2,3 % de Ni et 0,4-0,9 % de Cr.
Le produit est fondu au haut fourneau[67]. |
2 1 | St. Egidien (RDA) | VEB St. Egidien | 4,2 | 90[note 16] | NC | décembre 1960[17] 1974[68] | 1990[17] | Prévus pour le traitement de silicates de nickel hydratés[69]. 4 fours initialement prévus, le 3e a été ajouté vers 1974[68]. Minerai contenant 11 % de Fe et 0,84 % de Ni, les Luppen contiennent 5,8 % de Ni. |
3 | Zębiec k. Iłży (Pologne)[27] | Zakłady Górniczo-Hutnicze „Zębiec”[27] | 4,2[27] | 95[27] | 580[27] | 1965[61] | 1970[70] | Sable ferrugineux[27] contenant 15 % de Fe. |
Héritage
Évolution
Au vu de ses performances, le procédé a semblé une base de développement pertinente pour des variantes plus efficaces. Vers 1940, les Japonais ont notamment construit plusieurs petits fours de réduction opérant à plus basse température : un à Tsukiji (1,8 m × 60 m), deux à Hachinohe (2 fours de 2,8 m × 50 m) et trois à Takasago (2 fours de 1,83 m × 27 m et 1 four de 1,25 m × 17 m). Mais, ne produisant pas de Luppen, ils ne peuvent pas être assimilés au procédé Krupp-Renn[42].
Bien que la réduction directe dans un four rotatif ait fait l’objet d'un grand nombre de développements, le descendant logique du procédé Krupp-Renn est le « procédé Krupp-CODIR »[71]. Développé dans les années 1970, il reprend les principes généraux du Krupp-Renn avec une réduction à plus basse température, typiquement entre 950 et 1 050 °C, qui permet d’économiser du combustible mais qui est insuffisante pour obtenir une fusion partielle de la charge. L'ajout d'additifs correcteurs basiques (généralement du calcaire ou de la dolomie) mélangés avec le minerai permet le retrait du soufre apporté par le charbon, bien que la thermolyse de ces additifs soit très endothermique[23]. Ce procédé a été adopté par 3 usines : en 1973 par la Dunswart Iron & Steel Works en Afrique du Sud, en 1989 par la Sunflag Iron and Steel et en 1993 par la Goldstar Steel & Alloy, en Inde. Si l'application industrielle s'est bien concrétisée, ce procédé échoue cependant à s'imposer comme a pu le faire son prédécesseur[72].
Enfin, il existe beaucoup de procédés de réduction directe postérieurs au Krupp-Renn et fondés sur un four tubulaire rotatif. Au début du XXIe siècle, leur production cumulée représente entre 1 et 2 %[73] de la production mondiale d'acier[74]. La technologie reste donc assez confidentielle : en 1935 et 1960, la production issue du procédé Krupp-Renn (respectivement 1 et 2 millions de tonnes) correspondait à un peu moins de 1 % de la production mondiale d'acier[10] - [16].
Traitement de sous-produit ferreux
Spécialisé dans la valorisation de minerais pauvres, le procédé Krupp-Renn a servi logiquement de base de développement à des procédés de recyclage de sous-produits ferreux. En 1957, Krupp essaie à Stürzelberg[note 17] un four traitant les pyrites grillées afin d'en extraire le fer (sous la forme de Luppen) et le zinc (vaporisé dans les fumées). Ce procédé est donc un hybride entre le procédé Waelz et le Krupp-Renn, raison pour laquelle il a été appelé « procédé Krupp-Waelz » (ou encore « Renn-Waelz »[4]). Limité à un unique démonstrateur de 2,75 m × 40 m capable de traiter 70 à 80 t/jour, ses essais n'ont pas eu de suite[75].
La filiation technique entre le Krupp-Renn et les procédés japonais de production de réduction directe est souvent évoquée. Dans les années 1960, partageant le constat de la difficile maîtrise du colmatage du four, les sidérurgistes japonais développent leurs variantes à basse température du procédé Krupp-Renn[12]. La Kawasaki Steel met en service dans l'usine de Chiba (1968) ainsi que celle de Mizushima (1975), un four de réduction directe dont la caractéristique la plus visible consiste en une unité de bouletage des sous-produits sidérurgiques du site (boues et poussières issues de l'épuration des gaz de convertisseur et de haut fourneau). Le « procédé Kawasaki » intègre également d'autres évolutions, comme la combustion de pétrole au lieu de charbon pulvérisé[note 18] et l'utilisation de poudre de coke au lieu du charbon en mélange avec le minerai… Quasiment identique au procédé Kawasaki (il dispose d'une unité de bouletage plus élaborée), le « procédé Koho » a été adopté par Nippon Steel, qui démarre une installation de ce type en 1971 à l'usine de Muroran[21].
Le procédé Ōeyama
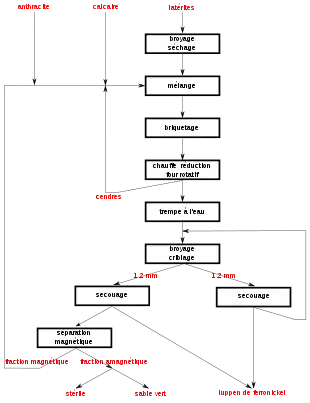
La production de ferronickel à partir de latérites s'inscrit dans un contexte bien plus favorable au procédé Krupp-Renn que la sidérurgie. En effet, les minerais latéritiques sous la forme de saprolite sont pauvres, très basiques et contiennent du fer. Les volumes de production sont modérés et la chimie du nickel se prête remarquablement bien à la réduction au four rotatif. Le procédé est donc séduisant mais, quel que soit le métal extrait, maîtriser toutes les transformations physiques et chimiques dans un unique réacteur est un réel défi[76]. L'échec de l'usine Larco à Lárymna, en Grèce, illustre le risque que représente son adoption : ce n'est que lors du passage à l'étape industrielle que le minerai s'est avéré incompatible avec le procédé Krupp-Renn[60].
Par conséquent, réaliser une réduction à plus basse température, suivie d'une fusion au four électrique permet, moyennant un investissement plus élevé, de dédier un outil à chaque étape afin de gagner en simplicité et en efficacité. Mise au point en 1950 en Nouvelle-Calédonie dans l'usine de Doniambo, cette combinaison s'est avérée rentable et surtout, plus robuste[28]. De grands tambours rotatifs (5 m de diamètre et 100 m, voire 185 m, de long) sont utilisés pour produire une poudre sèche de concentré de minerai de nickel. Cette poudre contient 1,5 à 3 % de nickel. Elle sort à 800–900 °C du tambour pour être immédiatement fondue dans des fours électriques. On se contente d'effectuer une réduction partielle dans les tambours : un quart du nickel en sort la forme métallique, le reste est encore oxydé. Seulement 5 % de fer est réduit en métal, et il reste du charbon imbrûlé qui servira de combustible lors de l'étape ultérieure de fusion au four électrique. Cette filière bien éprouvée (appelée aussi procédé RKEF, pour Rotary Kiln–Electric Furnace) s'est imposée : au début du XXIe siècle, elle assure la quasi-totalité du traitement des latérites nickélifères[76].
Cependant, au début du XXIe siècle, la fonderie de Nihon Yakin Kogyo à Ōeyama, au Japon, continue d'utiliser le procédé Krupp-Renn pour la production de ferronickel de qualité intermédiaire (23 % de nickel), appelé parfois fonte brute de nickel. Avec une production mensuelle de 1 000 tonnes de Luppen[77] pour une capacité de production de 13 kt/an, elle fonctionne à pleine capacité[54]. Elle est la seule usine du monde à conserver ce procédé[77]. C'est aussi la seule usine à utiliser un procédé de réduction directe pour l'extraction du nickel à partir de latérites. Le procédé, considérablement modernisé, est revendiqué comme le « procédé Ōeyama »[78].
Le procédé Ōeyama se distingue de procédé Krupp-Renn par l'emploi de calcaire, et le briquetage du minerai avant son enfournement. Il conserve ses avantages, qui sont la concentration de toutes les réactions pyrométallurgiques dans un unique réacteur, et l'utilisation de charbon standard (c'est-à-dire non cokéfiable), qui couvre 90 % des besoins énergétiques du procédé. La consommation de charbon n'est que de 140 kg par tonne de latérite sèche[note 19], et la qualité du ferronickel obtenu est compatible avec une utilisation directe par la sidérurgie. Quoique marginal, le procédé Krupp-Renn reste ainsi un procédé moderne et performant pour la fabrication de fonte brute de nickel. Dans ce contexte, face au procédé RKEF et au couple « usine d'agglomération-haut fourneau », il reste une alternative systématiquement étudiée[28].
- L'usine d'Ōeyama (Japon) de Nihon Yakin Kogyo en 2012. C'est la dernière usine à employer le procédé Krupp-Renn dans l'extraction du nickel.
Notes et références
Notes
- Johannsen arrive, lui, à une capacité cumulée construite, en 1945, de 3,2 Mt/an[9].
- En 1962, le minerai importé de la mine de Kiruna (nord de la Suède) titre 63,69 points de fer contre 53,80 points pour le minerai de la Ruhr. De 1959 à 1960, les importations de minerai en Allemagne passent de 20 à 33,7 millions de tonnes annuelles[11].
- Cette proximité chimique entre fer et nickel se traduit par un réactivité carbothermique semblable. Mais avoir des densités proches est tout aussi important afin d'éviter la ségrégation des matières brassées dans le four.
- Le soufre a une forte affinité pour le fer. Or il est également un élément d’alliage généralement indésirable, qui fragilise le fer à chaud comme à froid. Son élimination ne peut se faire qu’en milieu fortement basique (donc en présence de chaux, sinon de magnésie), alors que le procédé Krupp-Renn nécessite un laitier acide afin d'obtenir une bonne viscosité[33]. Pour autant, la capacité du procédé à évacuer les indésirables par les fumées fait du procédé un bon candidat dans le traitement des pyrites, car il peut ôter de grandes quantités de soufre par les fumées sans que le laitier soit pollué par cet élément[10].
- Bien que l'exhaustivité de cette liste ne puisse être affirmée, elle est assez cohérente avec les 65 fours industriels dénombrés par la Grande Encyclopédie soviétique dans les années 1970[6].
- Une source isolée évoque la reconstruction de 3 fours, au lieu de 2[41].
- Certaines sources indiquent 4 fours construits avant 1945 (sources soviétiques et japonaises), alors que d'autres en recensent 6 (Barrett, etc.). Akira Kudo qui date précisément le début de chaque campagne de 4 fours, semble le mieux renseigné[46].
- La CIA recense, en 1971, deux usines sidérurgiques nord-coréennes exploitant le procédé Krupp-Renn : l'usine de Kimch'aek, dotée de 6 fours avant 1960 et complétés par 2 fours supplémentaires vers 1970 et l'usine sidérurgique de Posan où 4 fours sont construits de 1969 à 1971. Par contre, aucun four n'est identifié à Seishin[47].
- Les caractéristiques de ces fours diffèrent selon les sources : Barrett identifie un four de 1 m de diamètre et 8 m de long mis en service avant 1945[42], les Soviétiques recensent 2 fours de 1,1 m de diamètre et 25 m de long encore en service en 1964[38] et Akira Kudo indique 2 fours de 1,8 m de diamètre et de longueurs 15 et 25 m produisant 8 t/j de fer, soit une consommation de minerai d'une vingtaine de tonnes quotidiennes. Ses informations ont été retenues[49].
- Les sources soviétiques donnent des fours de 3 m de diamètre, un de 92,3 m de long et 2 de 3 m de diamètre et 73,5 m de long[38].
- Il est difficile de préciser en quoi le four de Hirai, géré par un institut de recherche, ait été exploité de manière stable avec le procédé Krupp-Renn, même si Barett le comptabilise comme tel, ainsi que les petits fours de Fushun et d'Onishi[42].
- La CECA attribue la mise en service du 1er four à Thyssen en 1943[30], alors que les soviétiques présentent les 3 fours comme postérieurs à 1945[38]. La version de la CECA est généralement retenue[52].
- Un article du Der Spiegel reporte cependant une utilisation d'installations de réduction directe dès 1937 sur ce site, par la Reichswerke Hermann Göring de Watenstedt[11].
- En 1960, la CECA évoque un four de diamètre 3,6 m et de longueur 60 m, plus un autre en projet de 4,2 m × 70 m[30]. En 1963, l'UNIDO recense deux fours en service : 3,6 m × 40 m et 4,2 m × 90 m[15]. Enfin, en 1964, les sources soviétiques évoquent 2 fours de 4,6 m × 70 m, qui s'ajoutent au four de 1954[38]. C'est cette dernière information qui a été retenue.
- Un 2e four, de 4,6 m × 110 m, a été également construit[38], mais le procédé Krupp-Renn avait été abandonné avant sa mise en service[60].
- En 1960, la CECA donne une longueur de 100 m à ces deux fours. Les autres sources soviétiques étant cohérentes avec 90 m, elles ont été privilégiées.
- Ce four à Stürzelberg ne doit pas être confondu avec le « procédé Stürzelberg », un four tournant et basculant de réduction-fusion inventé dans la même ville[30].
- Les hydrocarbures, quoique plus coûteux, sont plus faciles à brûler et enrichissent le gaz réducteur en hydrogène[23].
- Cette consommation de 140 kg/t de charbon peut être comparée aux 240 kg de coke et 200 kg de charbon qu'un bon haut fourneau moderne consomme pour produire une tonne de fonte à partir de minerais de fer riches[79].
Références
- (en) Alexander Lyman Holley, Siemens' direct process of making wrought iron from ore, in a rotating gas furnace, , 21 p..
- (en) William Henry Greenwood, Steel and Iron : Comprising the practice and theory of the several methods pursued in their manufacture, and of their treatment in the rolling mills, the forge, and the foundry, , 546 p. (ISBN 1-110-38645-1, lire en ligne), p. 213-217.
- Jacques Corbion (préf. Yvon Lamy), Le savoir… fer — Glossaire du haut-fourneau : Le langage… (savoureux, parfois) des hommes du fer et de la zone fonte, du mineur au… cokier d'hier et d'aujourd'hui, , 5e éd. [détail des éditions] (lire en ligne [PDF]), § Procédé Basset.
- (de) Paul Funke, « Friedrich Johannsen : Nachruf », Jahrbuch 1988 der Braunschweigischen Wissenschaftlichen Gesellschaft, Göttingen, Erich Goltze KG, , p. 253-254 (DOI 10.24355/dbbs.084-201309201345-0, lire en ligne).
- Friedrich Johannsen, « Liste de brevets de Friedrich Johannsen », sur worldwide.espacenet.com, Office européen des brevets (consulté le ).
- (en) E. N. Iarkho, The Great Soviet Encyclopedia, 1970-1979, 3e éd. (lire en ligne), « Krupp-Renn Process ».
- (en) Feasability of the Krupp-Renn process for treating lean iron ores of the Mesabi Range, U.S. Department of Commerce, (lire en ligne), p. 4-5.
- (en) Brevet US 2900248 "Direct smelting process in rotary kilns", Friedrich Johannsen, 1959.
- (en) Friedrich Johannsen, « The Krupp Renn Process », dans Study on iron and steel industry and report on meeting of experts held in Bogota and sponsored by the Economic Commission for Latin America and technical assistance administration, vol. II, Organisation des Nations unies, (lire en ligne [PDF]), p. 192-200.
- (en) W. H. Voskuil et H. E. Risser, Economics Aspects of Direct Reduction of Iron Ore in Illinois, Urbana (Illinois), Division of the Illinois Geological Survey, (lire en ligne [PDF]).
- (de) « Gesang der Erzengel », Der Spiegel, no 29, , p. 31-32 (lire en ligne).
- (en) Akira Kudo, Japanese-German Business Relations : Co-operation and Rivalry in the Interwar, Routledge, , 286 p. (ISBN 0-415-14971-1, 0-203-01851-6 et 0-203-11623-2, lire en ligne), p. 89-108.
- Kudo 1998, p. 108.
- (en) Antony C. Sutton, Lend Lease (USA USSR Loan) & Major Jordan's Diaries Ultimate Collection, Stanford, Calif., Hoover institution press, , 482 p. (ISBN 0-8179-1131-6, lire en ligne), p. 125.
- (en) J. Mach et B. Verner, « Czechoslovak Experience with the Krupp-Renn Process », UNIDO, .
- (ru) В. Князев, А. Гиммельфарб et А. Неменов, Бескоксовая металлургия железа [« Métallurgie du fer sans coke »], Moscou, , 272 p., « Производство крицы », p. 143.
- (en) « History of St. Egidien » (consulté le ).
- Sutton 1973, p. 19
- Sutton 1973, p. 403.
- Sutton 1973, p. 21.
- (en) Amit Chatterjee, Sponge Iron Production By Direct Reduction Of Iron Oxide, PHI Learning Private Limited, , 376 p. (ISBN 978-81-203-3644-5, lire en ligne), p. 123-125.
- (en) Elisabeth Torsner, « Nickel and nickel alloys in stainless steel melting » [PDF], .
- (en) « Process technology followed for sponge iron » [PDF], Environment Compliance Assistance Centre (ECAC).
- (de) Friedrich Johannsen, « Das Krupp-Rennverfahren », Stahl und Eisen, no 38, , p. 969-978 (lire en ligne [PDF]).
- Krundwell et al. Davenport, p. 51.
- (en) Jörg Grzella, Peter Sturm, Joachim Krüger, Markus A. Reuter, Carina Kögler et Thomas Probst, « Metallurgical Furnaces » [PDF], John Wiley & Sons, , p. 7.
- (pl) Bogusław Barczyk, « Rozwój technologii przeróbki, wzbogacania i uzdatniania krajowych rud żelaza », Zeszyty naukowe politechniki śląskiej, seria Górnictwo no 27, , p. 275-307 (lire en ligne [PDF]).
- (en) Mingjun Rao, Guanghui Li, Tao Jiang, Jun Luo, Yuanbo Zhang et Xiaohui Fan, « Carbothermic Reduction of Nickeliferous Laterite Oresfor Nickel Pig Iron Production in China: A Review », The Minerals, Metals & Materials Society, vol. 65, no 11, , p. 1573-1583 (DOI 10.1007/s11837-013-0760-7, lire en ligne).
- (en) D. Fastje, « The Krupp-renn process », dans The production of iron-rich "iron-coke" for blast furnace operation, CIA, (lire en ligne [PDF]).
- Kegel, Willems, Decker, Gouzou, Poos, Jacques Astier, Folié et Palazzi, Procédé de réduction directe des minerais de fer, Communauté Européenne du Charbon et de l'Acier, , 130 p. (lire en ligne [PDF]).
- Brevet WO 2008029009 Procédé de traitement métallurgique d'un minerai de nickel et de cobalt latéritique, et procédé de préparation de concentrés intermédiaires ou de produits commerciaux de nickel et/ou de cobalt l'utilisant, Jérôme Agin, Yves Le Quesne et Bertrand Berthomieu, 2006.
- (de) Heinz Lehmkühler, « Die Verarbeitung eisenarmer saurer Erze nach dem Krupp-Rennverfahren in der Großversuchsanlage der Firma Fried. Krupp A.-G. », Stahl und Eisen, no 48, , p. 1281-1288 (lire en ligne [PDF]).
- (en) James Orlan Hood Jr., Investigations of several variables in the Dwight Lloyd McWane ironmaking process (Thèse de Master), Université du Missouri, (OCLC 860913751, lire en ligne), p. 14.
- (de) Joseph Schlink, Gemeinfassliche Darstellung des Eisenhüttenwesens, Dusseldorf, Stahleisen mbH, 1970/71, 17e éd. (ISBN 978-3-514-00001-8 et 3-514-00001-8, OCLC 252035201), p. 101.
- Kudo 1998, p. 103.
- (en) Anjali Singh et Prabhas Jain, « A study on the accretion formation in DRI kilns and possible ways for its reduction », Journal of Mechanical and Civil Engineering, vol. 12, no 6, , p. 98-103 (ISSN 2320-334X, e-ISSN 2278-1684, DOI 10.9790/1684-126598103, lire en ligne [PDF]).
- (en) H. A. Havemann, « Direct Iron Ore Reduction for Asia », Indian Construction News, , p. 269 (lire en ligne [PDF]).
- (ru) Внедоменное получение железа за рубежом [« Production de fer en loupe par des fours rotatifs (procédé Krupp-Renn) du livre Production étrangère de fer sans haut fourneau »], Moscou, А.Н. Похвиснева, , « Получение кричного железа во вращающихся печах (крично-рудный процесс) », p. 176–240.
- (ru) В. С. Абрамов, « Прямое получение железа по способу Круппа » [« Bulletin de l'Institut d'Information Central du Commissariat du Peuple de l'URSS »], Бюллетень Центрального института информации Народного коммисариата чёрной металлургии СССР, no 41, , p. 16-24.
- Kegel et al. 1960, p. 53-55.
- (pl) Marek Furmankiewicz et Krzysztof Krzyżanowski, « Podziemme relikty kopalni niklu w Szklarach » [« Reliques souterraines de la mine de nickel de Szklary »] [PDF], Wrocław, P.P. Zagożdżona i M. Madziarza, , p. 55.
- (en) Edward P. Barrett, « Sponge iron and direct-iron processes », Bulletin, Bureau of Mines, no 519, , p. 10 (lire en ligne [PDF]).
- Kudo 1998, p. 93.
- (en) « History of Ansteel » (consulté le ).
- Kudo 1998, p. 107.
- Kudo 1998, p. 96-106.
- (en) « North Korea: the status of the iron and steel industry » [PDF], CIA, (consulté le ).
- Kudo 1998, p. 102 et 106.
- (en) Akira Kudō, « The Transfer of Leading-edge Technology to Japan : The Krupp-Renn Process », Japanese Yearbook on Business History, no 11, , p. 15 (lire en ligne [PDF]).
- Kudo 1998, p. 96.
- Kudō 1994, p. 14.
- (cs) Jitka Kuncová, « Hrudkovenské potvory », Králodvors Kýzpravodaj, no 5, , p. 5 (lire en ligne).
- (cs) Džurný Jakub, « Mníšek pod Brdy », (consulté le ).
- (en) Ashok D. Dalvi, W. Gordon Bacon et Robert C. Osborne, The Past and the Future of Nickel Laterites, Inco Limited, (lire en ligne [PDF]).
- (en) Haruo Arai, « Ferro-Nickel Smelting at Oheyama Nickel Co., Ltd », Journal of the Mining and Metallurgical Institute of Japan, vol. 97, , p. 792-795 (DOI 10.2473/shigentosozai1953.97.1122_792, lire en ligne).
- (de) Albert Gieseler, « Maximilianshütte », Mannheim, (consulté le ).
- (es) Benito Del Pozo, « El primer fracaso del INI en Asturias: SIASA (1942–1971) », Revista de Historia Económica / Journal of Iberian and Latin American Economic History, vol. 9, no 3, , p. 533-540 (DOI 10.1017/S0212610900003050, lire en ligne).
- (cs) Vratislav Řehoř et Jiří Grygárek, « Historie těžby chudých Fe rud v Barrandienu po 2. světové válce » [PDF], (consulté le ).
- (cs) « RND Ejpovice », (consulté le ).
- (he) Emmanouil Zevgolis, « Η Σύγχρονη Ιστορία της Μεταλλουργίας του Ελληνικού Σιδηρονικελίου » [« The Contemporary History of the Greek Ferronickel Industry »], Mining and Metallurgical Chronicles, (lire en ligne).
- (pl) Teofil Lijewski, Uprzemysłowienie Polski 1945-1975 : przemiany strukturalne i przestrzenne, Varsovie, Państ. Wydaw. Naukowe, (lire en ligne), p. 130.
- (pl) « Huta Stara B - Archiwum » (consulté le ).
- (en) M. J. Kennard, « Krupp-Renn direct reduction process », Mining Congress Journal, vol. 47, no 1, , p. 34-37.
- (de) « „Bergeborbeck“ – Versionsunterschied » (consulté le ).
- Князев, Гиммельфарб et Неменов 1972, p. 143-146.
- (ru) A. I. Gimmel’farb et G. I. Chasovitin, « Production of bloomery iron in rotary furnaces and experiences with its use in blast furnaces », Stal, no 8, , p. 691-694 (lire en ligne).
- (en) Charles Eric Denike Clifford, The Uralian Iron and Steel Industry, University of British Columbia, (lire en ligne [PDF]), p. 143-148.
- (de) « Zum Nickelsilikaterzbergbau bei Callenberg » (consulté le ).
- (en) « The history of St. Egidien ».
- (pl) « ZGM Zębiec, SA » (consulté le ).
- (en) Marko Kekkonen et Lauri E Holappa, Comparison of different coal based direct reduction processes, Université de technologie d'Helsinki, (ISBN 951-22-5134-5, ISSN 1455-2329), p. 9.
- Chatterjee 2010, p. 185.
- (en) « 2019 World direct reduction statistics » [PDF], Midrex, .
- (en) « 2020 World Steel in Figures » [PDF], Worldsteel Association, (consulté le ), p. 25.
- (en) « The Krupp-Renn Process », Prospectus of the Krupp company, Essen, Krupp, et (en) S. Henkel, « titre non communiqué », Stahl und Eisen, vol. 78, nos 1, 4, cités par Production étrangère de fer sans haut fourneau, Moscou, 1964.
- (en) Frank K. Krundwell, Michael S. Moats, Venkoba Ramachandran, Timothy G. Robinson et William G. Davenport, Extractive Metallurgy of Nickel, Cobalt and Platinum Group Metals, Elsevier, , 610 p. (ISBN 978-0-08-096809-4, lire en ligne), p. 51-53 ; 59 ; 62-64.
- (en) Shigenobu Yamasaki, Masato Noda et Noboru Tachino, « Production of Ferro-Nickel and Environmental Measures at YAKIN Oheyama Co., Ltd. », Journal of The Mining and Materials Processing Institute of Japan (MMIJ), (DOI 10.2473/journalofmmij.123.689, lire en ligne).
- (en) Matsumori Watanabe, Sadao Ono, Haruo Arai et Tetsuya Toyomi, « Direct reduction of garnierite ore for production of ferro-nickel with a rotary kiln at Nippon Yakin Kogyo Co., Ltd., Oheyama Works », International Journal of Mineral Processing, vol. 19, , p. 173-187 (DOI 10.1016/0301-7516(87)90039-1, lire en ligne).
- (en) Best Available Techniques (BAT) Reference Document for Iron and Steel Production, Direction régionale de l'environnement, de l'aménagement et du logement, , 597 p. (lire en ligne [PDF]), p. 291-293 ; 338-345.
Voir aussi
Bibliographie
- (de) Friedrich Johannsen, « Das Krupp-Rennverfahren », Stahl und Eisen, no 38, , p. 969-978 (lire en ligne [PDF])
- (en) E. N. Iarkho, The Great Soviet Encyclopedia, 1970-1979, 3e éd. (lire en ligne), « Krupp-Renn Process »
- (en) Feasability of the Krupp-Renn process for treating lean iron ores of the Mesabi Range, U.S. Department of Commerce, (lire en ligne), p. 4-5
- (en) « Process technology followed for sponge iron » [PDF], Environment Compliance Assistance Centre (ECAC)
- Kegel, Willems, Decker, Gouzou, Poos, Jacques Astier, Folié et Palazzi, Procédé de réduction directe des minerais de fer, Communauté Européenne du Charbon et de l'Acier, , 130 p. (lire en ligne [PDF])
- (en) Akira Kudo, Japanese-German Business Relations : Co-operation and Rivalry in the Interwar, Routledge, , 286 p. (ISBN 0-415-14971-1, 0-203-01851-6 et 0-203-11623-2, lire en ligne), p. 89-108
- (en) Edward P. Barrett, « Sponge iron and direct-iron processes », Bulletin, Bureau of Mines, no 519, , p. 10 (lire en ligne [PDF])
- (en) Akira Kudō, « The Transfer of Leading-edge Technology to Japan : The Krupp-Renn Process », Japanese Yearbook on Business History, no 11, , p. 15 (lire en ligne [PDF])
- (en) J. Mach et B. Verner, « Czechoslovak Experience with the Krupp-Renn Process », UNIDO,
- (ru) Внедоменное получение железа за рубежом [« Production de fer en loupe par des fours rotatifs (procédé Krupp-Renn) du livre Production étrangère de fer sans haut fourneau »], Moscou, А.Н. Похвиснева, , « Получение кричного железа во вращающихся печах (крично-рудный процесс) », p. 176–240