Contreplaqué moulé
Le contreplaqué moulé utilise des plis façonnés en contreplaqué selon des formes courbes plutôt qu'en panneaux.
Les formes qui sont générée par moulage du contreplaqué vont de toutes les combinaisons de cylindres à courbure simple et de plans à toutes les formes composées de paraboloïdes et portions de sphère, en bref toute pièce courbe pour laquelle un moule peut être fabriqué et séparé ultérieurement du produit fini[1].
Le contreplaqué moulé a été utilisé intensivement dans la conception de différents avions monocoques en bois ; depuis les années 1910 jusqu'à la fin de la seconde Guerre Mondiale. Pendant la seconde Guerre Mondiale il a aussi été fait usage du contreplaqué moulé comme matériau de remplacement de l'aluminium, pour des parties de fuselages et s'est décliné selon différents procédés. Le contreplaqué moulé offrait certaines caractéristiques de performance meilleure que celle du métal, en raison d'un rapport rigidité/poids supérieur[2].
Le mobilier en contreplaqué moulé a d'abord été produit selon des combinaisons de portions de cylindre et de plans. Les premières productions utilisant des combinaisons de formes plus complexes sont les sièges conçus par Charles Eames et Eero Saarinen pour l'exposition de 1941, Organic Design in Home Furnishings et réalisés par la Haskelite Manufacturing Corporation[3].
Les précurseurs
Dans le mobilier
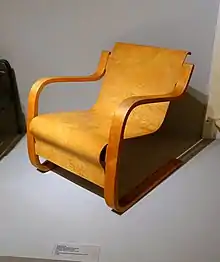
Entre 1850 et 1890, le contreplaqué moulé était dans la conception de meubles, plus courant que les panneaux selon le même matériau et la conception de mobilier était le moteur de son innovation. Une technique de moulage de meubles a été brevetée à New York en 1858 par John Henry Belter (en)[4], pour produire des dossiers de chaises. Sa technique augmentait la vitesse de fabrication et réduisait les coûts de production, car les dossiers pouvaient être fabriqués par huit à l'aide d'un seul moule[5]. Une chaise d'Isaak Cole de 1874 est considérée comme le premier meuble entièrement composé de coques en bois moulé[6] - [7]. Le contreplaqué moulé est apparu dans la production de meubles de masse après la Première Guerre mondiale. Les méthodes de production de masse et les considérations esthétiques deviendront la préoccupation d'architectes et de designers tels que Mart Stamm, Alvar Aalto, Marcel Breuer, Eero Saarinen, Charles et Ray Eames et Arne Jacobsen[7]. Le Fauteuil Paimio, conçu par Alvar Aalto et Huonekalu- ja Rakennustyötehdas (en) en 1932 pour Sanatorium de Paimio en Finlande sera fabriqué aux côtés d'autres créations de meubles d'Aalto pour la vente générale et exportés en grande quantité au Royaume-Uni et aux États-Unis, où son utilisation innovante du contreplaqué aura un impact significatif sur d'autres designers[5]. En 1932 Alvar Aalto va produire un fauteuil moulé composé, annoncé par Domus et présenté au Nordic Building Congress la même année mais qui ne sera jamais été exposé ni fabriqué. Le designer britannique Gerald Summers (en), produira deux chaises en contreplaqué multidimensionnel avec plus de succès qu'Aalto[8]. Pendant l'entre-guerre et la seconde Guerre mondiale le nouveau moteur de l'innovation dans le moulage des contreplaqués et la diffusion des adhésifs de synthèse sera l'aéronautique. Une série de sièges multi-dimensionnel sont conçus par Charles Eames et Eero Saarinen pour l'exposition de 1941, Organic Design in Home Furnishings du MoMA et sont réalisés par la Haskelite Manufacturing Corporation[3]. Par la suite Charles et Ray Eames, vont obtenir des commandes de l'armée pour des attelles de jambes en bois moulé qu'ils vont produire au sein de la Molded Plywood Division de Evans Products, ils vont aussi fabriquer des parties entières de fuselage d'avion. Au sortir de la guerre, en 1946, la technologie utilisée pour le mobilier des Eames dans leurs ateliers de Venice à Los Angeles, et dans l'usine Evans de Coos Bay en Oregon, avait atteint un tel stade de développement, que des distributeurs comme la Herman Miller Furniture Company à Zeeland, Michigan, n'ont pu dans un premier temps que se raccrocher à un train qui les avait dépassé[9] - [10] - [11] - [12] - [13].
Marine
En Angleterre, Samuel Edgar Saunders, en 1899, fait breveter[14] un matériau composite léger assimilable à du contreplaqué, le Consuta. Saunders est d'abord un constructeur de marine et Constua sera d'abord utilisé pour des navires (comme le Steam Launch Consuta de 1898[15]). Au départ, S. E. Saunders Ltd à East Cowes, île de Wight, s'est concentré sur la construction de bateaux à moteur, de canonnières, etc. Cependant, à l'aube de l'ère de l'aviation, Saunders a compris que la nature solide et légère de Consuta était idéale pour les avions. Les premières réalisation aéronautiques de Saunders consiste en les deux gondoles pour moteurs du dirigeable britannique HMA n ° 1 de 1911. Le Sopwith Bat Boat (en) de 1913 est le premier avion réalisé par Saunders. Le White and Thompson No. 3 de 1914 sera construit à 9 exemplaire. À partir de 1917, une centaine de Felixstowe F.2, basés sur le H4 vont être construit par la S. E. Saunders pour la Seaplane Experimental Station de Felixstowe (en). La technique pour les bateaux restera en usage jusque dans les années 1950[16].
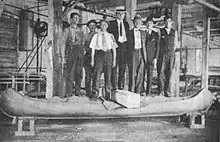
Aux États-Unis, la résistance structurelle légère des placages de bois stratifiés et moulés en une seule pièce a été expérimentée par Henry L. Haskell de Ludington, dans un canoë fabriqué d'un seul pli moulé, dès 1917. Haskell a par la suite fabriqué des pièces d'avion en contreplaqué basées sur son brevet « Aeroplane-body[17] » de 1918. La plupart des procédés de fabrication de contreplaqué moulé à destination de l'aviation aux États-Unis, tels Duramold, sont les successeurs des procédés mis en place par Haskell.
Pendant la Seconde Guerre mondiale des coques de petits bateaux et des cabines et ponts de PT boat ont été construits en contreplaqué moulé[18].
Aéronautique
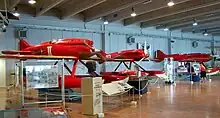
La construction contreplaqué et en contreplaqué moulé doit à partir de 1910, son essor à l'industrie aéronautique. La construction d'avion en contreplaqué monocoque se met en place dès 1912, mais longtemps ne sera pas utilisée dans une large mesure pour la fabrication d'avions commerciaux en raison de son coût excessif. Un autre inconvénient a été la difficulté d'obtenir un produit parfait en raison des processus laborieux généralement utilisés pour appliquer et coller chaque bande de bois séparément de la forme par laquelle le fuselage est habituellement construit[19]. Une structure monocoque en placage de bois moulé a été fabriquée avec succès dès 1912 sur le Deperdussin Monocoque par Louis Béchereau, et en 1916, le LWF model V de la Lowe, Willard & Fowler Engineering Company[20]. La même année le LFG Roland C.II est lancé en Allemagne par la Luft-Fahrzeug-Gesellschaft, qui sera construit à 300 exemplaires. La coque du Deperdussin Monocoque pesait 22 kg et pouvait être portée à bout de bras.
Conçu en 1920, le Loughead S-1, fut construit à un exemplaire selon une méthode innovante de construction monocoque en contreplaqué de moulage au sac que l'on doit à Jack Northrop. La technique utilise deux demi-coques en contreplaqué moulé qui sont collées ensemble autour de cerceaux en bois[21]. La construction monocoque n'est réalisée dans un premier temps que pour de petites séries[21]. Partout où une rationalisation parfaite et une qualité optimale sont requises, des fuselages monocoques en contreplaqué vont être utilisés ; pour tous les avions de course à succès compris les avions Curtis (Curtiss R3C) et le vainqueur italien de la Coupe Schneider de 1926, le Macchi M.39 ; ainsi que pour certains avions militaires réussis de Grande-Bretagne, de France[19] et d'Allemagne. Le processus développé et amélioré par Lockheed pour le Loughead S-1 va être appliqué en 1927 au Lockheed Vega, plus grand et plus célèbre, qui sera construit en 132 exemplaires[21].
Dans les années 1930, deux légendes de l'aviation, Eugene Luther Vidal et Virginius Clark (en), poursuivent des voies distinctes pour fabriquer un avion en bois lamellé-collé. Malgré l'accent mis par l'armée sur le développement et l'achat de tous les avions en métal, Vidal obtient un contrat en 1938 pour fournir un assemblage d'aile moulé à partir d'une résine thermoplastique. Pendant ce temps, Clark s'est associé à Fairchild et Haskelite pour construire le Fairchild F-46, un avion composé de tous les matériaux synthétiques qu'Haskelite a rapporté. La technologie Duramold de Clark a ensuite été acquise par Howard Hughes et utilisée sur l'hydravion HK 1 surnommé à tort le Spruce Goose. De plus en plus proche du plastique, les contreplaqués à base de résine laissent entrevoir le jour où toute la cellule d'un avion sera construite en plastique. Dans un discours à la Royal Aeronautical Society de Londres en avril 1935, de Havilland semble avoir déjà abandonné la construction en bois. Mais cinq ans plus tard il construira l'incontournable de Havilland DH.98 Mosquito, construit à 7 781 exemplaires par la Royal Air Force. La technique de construction du Mosquito a anticipé la simplicité et la solidité des structures de fuselage monobloc jamais revues avant le premier vol du Lockheed Martin X-55 ACCA près soixante an plus tard[22].
L'utilisation de contreplaqué moulé dans l'aéronautique s'arrête peu après la fin de la seconde Guerre Mondiale. Certains planeurs l'utiliseront encore.
Automobile
La construction automobile ou des bateaux en contreplaqué moulé suivent la plupart du temps les progrès enregistrés dans l'aéronautique[5].
Georges Lévy, conçoit à la fois des side-cars et des hydravions en contreplaqué - les flotteurs des hydravions réutilisant essentiellement la forme arrondie du corps du side-car[5]. À partir de 1928, la société allemande DKW utilise du contreplaqué moulé et plat pour la carrosserie de ses voitures familiales abordables (DKW F7 (en))[5].
Les colles
L'utilisation la plus courante de la colle sur les premiers avions allait à la fabrication de contreplaqué. Le contreplaqué sera premièrement utilisé premièrement dans les avions monocoques en bois, par la suites pour les revêtements extérieurs tels que les turtle decks, les bords d'attaque des ailes, les revêtements des ailes et du fuselage, les composants internes tels que les âmes de nervure et d'empennage, les âmes de longerons de voilure, les parois des réservoirs de carburant, et les surfaces intérieures telles que les marchepieds d'aile, cloisons, surfaces de cabine et tableaux de bord[20].Les avions en bois collé demeurèrent répandus jusqu'aux années 1920 et 1930, ne furent pas rares dans les années 1940 et volèrent dans une utilisation quotidienne jusque dans les années 1950 et 1960[20]. Les développements et progrès réalisés dans la fabrication du bois moulé et de tout autre bois d'ingénierie, doivent être mis en corrélation avec les avancés dans la fabrication des adhésifs. Les bois depuis les débuts de l'aéronautique étaient la plupart du temps assemblés par collage.
Les premiers adhésifs employés dans l'aviation étaient des colles dérivées de protéines naturelles (colle animale et colle d'albumine sanguine principalement, par la suite colle de caséine). Plus tard sont arrivées les colles phénoliques, et dans les années 1930, les colles urée-formaldéhyde et les colles résol (résines phénoliques à durcissement alcalin), d'abord en Allemagne[23]. Des résines acryliques (méthacrylates de méthyle) et l'acétate de cellulose ont aussi été utilisées[24]. Plus tard des colles résorcine. Ces adhésifs à base de résine ont été développés sous forme de poudres, de liquides et de papier tissu imprégné de résine disponible en feuilles de grand format[24].
L'utilisation du contreplaqué pendant la première guerre mondiale était plutôt généralisée malgré ses inconvénients. Ce n'était pas l'inflammabilité qui a agi comme facteur limitatif dans l'utilisation du contreplaqué[25]. L'inconvénient fondamental lié à la construction en bois provenait des adhésifs couramment utilisés - les colles de caséine et d'albumine sanguine — qui étaient sujets à la détérioration par l'humidité, les champignons et l'action bactérienne. Depuis les années 1930, les défenseurs des structures d'avion en bois avait souligné ce problème, alors que le métal avait commencé à remplacer le bois comme matériau dominant[26]. Le problème sera résolu avec l'avènement des colles synthétiques, notamment celles de la famille des résines urées. Au fur et à mesure que la chimie des polymères progressait dans les années 1930 et 1940, des adhésifs synthétiques plus solides et plus durables arrivèrent sur le marché; tels Kaurit, Klemmleim (basée sur Kaurit), Tego film en Allemagne, Plybond aux États-Unis Beetle Cement (basée sur Kaurit) et Aerolite en Angleterre[27], quelquefois développées par les constructeurs d'avion eux-mêmes, et qui commencèrent à supplanter les colles naturelles dans la fabrication d'avions en bois[20]. Résistantes à l'humidité et à la pourriture, elles se prêteront à la conception de contreplaqués qui feront rattraper au bois son retard sur le métal[26]. Le contreplaqué mêlé à des adhésifs de résine améliorés va offrir aux concepteurs et aux constructeurs d'avions un matériau qui ne se fend pas, a une bonne stabilité dimensionnelle, une résistance répartie, et une facilité de mise en œuvre pour être plié, cintré et formé[25].
Des appellations erronées, telles que « plastic plywood » et « plastic planes », ont été donné de manière abusive à des structures de contreplaqué moulé qui étaient en fait fabriquées à partir de placages de bois collés avec un adhésif en résine synthétique. En poids, ces structures étaient probablement composées d'environ 80 % de bois et de 20 % de résine adhésive. À l'exception des variations de forme, le produit était essentiellement le même que le contreplaqué pressé à plat[28].
Les colles phénoliques ou urée-formaldéhydes sont dites thermodurcissables, c'est-à-dire qu'il faut leur appliquer chaleur et pression pour obtenir leur durcissement. Le NACCA, ancêtre de la NASA est un observateur silencieux des progrès réalisés par les structures en contreplaqué moulé. En 1942 elle tente de résoudre un problème de cure des résine thermodurcissables entre deux couches de bois. Parce que le bois et la résine sont mauvais conducteurs de chaleur, il faut plusieurs heures pour élever le centre du matériau à la température de durcissement. Anticipativement la NACCA prévoit que le problème pourrait être résolu en exposant l'assemblage à un champ électrique à haute fréquence, leur appliquer à grande échelle ce que cinq ans plus tard on appellera micro-onde. Le problème sera finalement résolu par autoclave[22] - [29].
En Angleterre, en 1934, Norman de Bruyne conçut le Snark, avion expérimental (en) monoplan à quatre places; pour tester des structures d'aile et de fuselage à revêtement travaillant en contreplaqué de faible poids liées à la bakélite. de Bruyne développa aussi une forme pionnière de plastique renforcé de fibres , adapté à la fabrication d'avions, un stratifié de mèches de lin et de papier imbibé de résine phénolique liquide et durci sous pression qu'il appela Gordon Aerolite. Mais la contribution la plus remarquable de Bruyne à l'aéronautique, fut un adhésif urée-formaldéhyde, l'Aerolite, qui sera commercialisé par la société qu'il fonde, Aero Research Limited. Aerolite rentrera dans la fabrication des contreplaqués des planeurs Airspeed Horsa (notamment fabriqué par Harris Lebus, un fabricant et grossiste de meubles basé dans l'East End de Londres) et le de Havilland DH.98 Mosquito.
Les colles dans les processus de moulage de contreplaqué à partir de 1941 aux États-Unis seront couramment fournies par American Cyanamid, Bakelite Company, Carbide & Carbon Chemicals, Casein Co . of America, Catalin, duPont, etc.[30]
Contreplaqué moulé vs aluminium formé
La découverte des colles de synthèse coïncide avec le moment où le métal a commencé à remplacer le bois comme matériau dominant pour la fabrication d'avions; et les militaires Britanniques, par exemple, au début de la Seconde Guerre mondiale, considéraient les avions en bois comme fragiles et lents sur la base des 40 dernières années d'histoire de l'aéronautique[20]. L'aluminium n'a été utilisé pour les cellules qu'après la découverte du durcissement par précipitation par Alfred Wilm, en 1903 qui a débouché sur le Duralium en 1909; et dans les années 1920, certains designers, tel Hugo Junkers, Claudius Dornier et Adolf Rohrbach, ont expérimenté des avions en aluminium. Les charges de pression accrues exercées sur le fuselage ont conduit au développement de revêtement travaillant (stressed skin panels) fabriqués à partir de matériaux à haute résistance, premièrement l'aluminium[31]. Mais en 1917 il était difficile d'obtenir de l'aluminium dont on puisse compter sur une structure et une résistance uniformes ; au stade du développement, l'aluminium a par exemple été systématiquement écarté pour tous les composants structurels de l'hydravion Curtiss NC, au profit de l'épicéa et de l'acajou amer[32].
Toutefois l'aluminium ne sera jamais un matériau parfait. À l'époque où a été construit le de Havilland DH.98 Mosquito, l'un des facteurs qui réduisaient les performances haut de gamme sur les avions à revêtement métallique était un phénomène connu sous le nom de « tin canning », l'ondulation du métal entre le rivets, causés par l'élasticité native de fines feuilles de métal léger pour avions. Cela affectait particulièrement l'extrados très incurvé de l'aile, altérant la portance et augmentant sensiblement les résistance parasites. Le contreplaqué, correctement renforcé, ne présentait pas ce phénomène[26].
L'aluminium sujet au flambage devait être de plus renforcé par un grand nombre de raidisseurs et de renfort rivetés[24]. Considérant la faible densité du contreplaqué, il était possible d'utiliser des revêtement quatre ou cinq fois plus épais que les revêtements tout métal normaux sans pénalité de poids ; ces revêtements épais sont extrêmement rigides et stables contre le flambage ; l'élasticité du contreplaqué permettait une contrainte presque jusqu'au point de rupture sans déformation[24].
Ce qui est intéressant dans la nouvelle approche de l'industrie aéronautique à l'entrée de la guerre, c'est que l'on envisage de concevoir des pièces séparées en contreplaqué moulé en remplacement des mêmes pièces en aluminium. Précédemment le moulage du contreplaqué visait surtout à produire des avions monocoques en bois. En 1941, on avance que les pièces d'avion moulées en contreplaqué — on parle encore de fuselages entiers (le H-4 emblématique de Hughes Aircraft), mais aussi les emplanture d'aile et les carénages — offrent sur le métal des caractéristiques de performance supérieures, en raison d'un rapport rigidité/poids plus élevé; et des surfaces lisses, débarrassées des rivets, et des ondulations qui sont le propre du métal et qui sont un obstacle au flux d'air[2] - [21] - [1].
A côté de l'offre de contreplaqué moulé, Fletcher Aviation a proposé de grandes feuilles souples de contreplaqué de bouleau liées à la résine , composées de deux plis de 1/8 et 1/16 de pouces d'épaisseur. Ces feuilles désignées Plasti-Ply ont été utilisées comme revêtement travaillant. Utilisé par le Fletcher FBT-2 le procédé appelé Plyweld était conçu pour éliminer les inconvénients liés à une grande matrice et à l'équipement de four spécial nécessaire au moulage dans les autres procédés en vigueur. Les pièces en contreplaqué étaient collées entre elles sous vide à l'aide d'un adhésif de type urée-formaldéhyde qui était acheté sous forme de poudre. Mélangé avec de l'eau avant l'application, il polymérisait ou durcissait pour former une forte adhérence imperméable. Cette partie de la fabrication pouvait être facilement sous-traité à l'industrie du meuble[33].
Avions monocoque en bois emblématiques
Le Deperdussin Monocoque
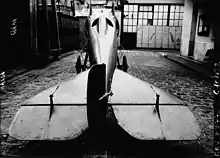
Deux Deperdussin Monocoque sont exposés au douzième Salon belge de l'automobile à Bruxelles de 1913, décrits dans L'Expansion belge de cette manière[34]: Le fuselage des monocoques constitue la partie caractéristique des appareils Deperdussin. La poutre quadrangulaire habituelle y fait place à une coque véritable d'une seule venue en bois contreplaqué à plusieurs épaisseurs. Pour obtenir cette coque, on colle successivement trois épaisseurs de lattes minces en tulipier - bois se prêtant au mieux à ce genre de travail et d'une bonne résistance - sur des gabarits démontables formant moule. Lorsque le collage est terminé, on a obtenu une carapace composée d'une quantité de pièces à contrefil, c'est-à-dire présentant les meilleures garanties d'indéformabilité. Il n'y a plus qu'à la revêtir extérieurement et intérieurement d'une toile soigneusement collée et enduite (vernie) et l'on obtient ainsi un bloc homogène, joignant la robustesse à la légèreté. Tout ce travail exige une main d'œuvre habile et soignée. Lors du montage des organes sur la coque, celle-ci est entretoisée par les tôles de fixation du moteur, les barres de compression des ailes, et les armatures de la nacelle et de l'empennage. Les ailes à très faible courbure et peu épaisses sont établies de façon à résister aux plus rudes efforts. Les longerons de voilure sont construits partie hickory, partie frêne, et l'âme en sapin. Les assemblages sont soignés à l'extrême. L'entoilage est en lin extra fort enduit d'émaillite, etc.[34]. Les Établissements Deperdussin comprennent trois groupes: l'usine de la rue des Entrepreneurs à Paris, l'usine de Juvisy sur Orge et l'aérodrome de la Champagne. L'usine de Paris travaillait en série, et à côté des ouvriers spéciaux; une sorte d'élite d'ouvriers était regroupée, qui travaillent directement sous les ordres de Louis Béchereau. C'est de l'usine de la rue des Entrepreneurs qu'est sorti le monocoque type Coupe Gordon Bennett en 1912, venu après le type militaire monoplace biplace et triplace[34]. Le monocoque Deperdussin est vainqueur de la Coupe Gordon-Bennett en 1912 à Clearing (Chicago) piloté par Jules Védrines, et en 1913 à Reims piloté par Maurice Prévost. La première Guerre Mondiale interrompra cette série de victoire qui seront continuées en 1920 par le Nieuport-Delage NiD.29, avec Joseph Sadi-Lecointe au pilotage. Ce dernier avion dont le développement avait commencé en 1917, reprenait la structure monocoque en contreplaqué moulé du Deperdussin. 300 exemplaires de ce prototypes furent construits pour l’Aviation militaire française[35].
LFG - Roland C.II
La société aéronautique Roland a fait breveter le Wickelrumpf (fuselage à enroulement) , semi-monocoque dont le procédé a ensuite été autorisé par Pfalz-Flugzeugwerke pour la construction d'avions de combat. Le Wickelrumpf impliquait l'utilisation de bandes de placage enroulées autour d'un simple châssis en bois. La coque était renforcée de tissu, formant un fuselage très profilé et robuste. Tout ce processus était une première tentative de construction monocoque. Cependant, la technique Wickelrumpf sur le LFG Roland C.II de 1916 utilisait deux longerons pour le cadre, une caractéristique que les vrais avions monocoques n'ont pas[36]. Le LFG Roland D.VI construit à la fin de 1917 a une coque construite selon la technique de bordage à franc-bord, apparue comme un moyen de faire face aux pénuries de contreplaqué subies par l'Allemagne en raison du blocus naval allié.
Le de Havilland Mosquito
La cellule du de Havilland Albatross de 1937 est moulé d'un seul tenant autour de sa structure[37].
Un moule positif est utilisé pour le de Havilland DH.98 Mosquito de 1941, deux demi-coques sont assemblées en une seule, chaque demi-coque est constituée de deux couches de contreplaqué moulé autour d'une âme de balsa[38] - [39]. D'autres sources renseignent des moules négatifs, premièrement dans des moules négatifs en bois fermés; des outils en béton dans les années suivantes[20].
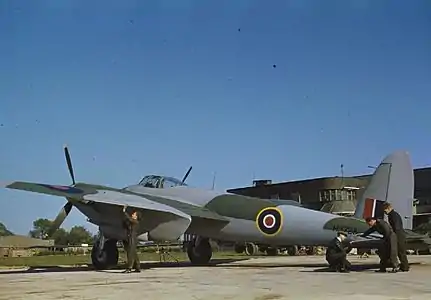
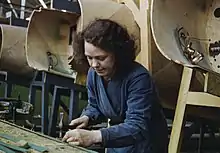
.jpg.webp)
Au début de la Seconde Guerre mondiale, alors que les usines métallurgiques étaient insuffisantes pour alimenter le front intérieur, les industries du bois demeuraient disponibles. Après le décompte des résultats de la débâcle anglaise en France, furent définis les types d'avions dont l'Angleterre aurait désormais besoin. Il fut déterminé que le programme de bombardiers lourds et de chasseurs absorberait la majeure partie du métal de l'Empire britannique alloué aux avions. Il y aurait cependant besoin d'un « in-fielder », un avion qui pourrait être modifié pour faire un peu de tout[26]. Cet avion devrait être produit en quantité, et sans bouleverser le calendrier d'approvisionnement et de main-d'œuvre du programme des chasseurs et de bombardiers. De Havilland Aircraft Company fournit le miracle, sous la forme du de Havilland DH.98 Mosquito ; qui s'avéra remarquable[40]. Le bois était le grand matériau inexploité, et les menuisiers étaient le principal bassin de main-d'œuvre non drainé et qui pouvait s'appliquer à tout l'Empire britannique; Le Canada, l'Inde, l'Australie et la Nouvelle-Zélande pourraient tous produire des cellules Mosquito complètes[26].
Le fuselage du Mosquito est fait de placage standard de chaque côté d'un noyau de balsa. Le fuselage comprenait une peau intérieure en contreplaqué à 3 plis collée à une ossature en bois lamellé-collé. Le bois de balsa, agissant comme un matériau sandwich, a ensuite été collé en place pour remplir les espaces entre les peaux. La peau extérieure à 3 plis a ensuite été collée sur le dessus pour compléter le sandwich[41]. Étant donné que le balsa n'a virtuellement aucune résistance structurelle propre, le placage de bois, généralement de l'épicéa, du bouleau ou de l'acajou, supporte les tensions. Le balsa stabilise simplement les plis, en les espaçant, transformant l'ensemble de la section en un seul longeron caisson[26]. Cette construction a préfiguré les conceptions populaires à noyau en nid d'abeille/faces en aluminium et les composites des années ultérieures[20].
L'aile est une structure monobloc entièrement en porte-à-faux, constituée de deux longerons caissons. Ceux-ci consistent en des semelles en épicéa sur une âme en bouleau. L'intrados de l'aile est une simple feuille de contreplaqué, collée et vissée sur les membrures. La surface supérieure, cependant, est une double peau de contreplaqué, séparée par des entretoises en bois dur qui transforment toute la surface supérieure porteuse de contraintes en une série de longerons caisson de voilure pour une grande résistance et rigidité absolue[26].
Le De Havilland Hornet[39] de 1944 et le de Havilland Vampire[42] de 1946 sont de même conception. Les prises d'air du Vampire avaient une conception multi-courbure incroyablement compliquée, qui n'a été possible que grâce à la capacité de pouvoir produire des stratifiés en bois collés[41].
Le Loughead S-1
_(17733144163).jpg.webp)
Le fuselage du Loughead S-1 fut construit selon une méthode innovante de construction monocoque que l'on doit à Jack Northrop. La forme arrondie du fuselage a été produite en deux moitiés réalisées dans un grand moule en béton. Trois couches constituées de fines bandes d'épicéa enduites de colle de caséine ont été posées, la direction du fil de chacune des couches étant à angle droit avec la précédente. Un couvercle a alors été boulonné sur le moule, et une vessie ou baudruche en caoutchouc laissée à l'intérieur a été gonflée à haute pression pour fusionner la coque en bois. Vingt-quatre heures plus tard, la demi-coque lisse était prête à être jointe à une autre pour créer le fuselage ; les moitiés étaient réunies autour de cadres elliptique en stratifié d'épicéa pour créer le fuselage monocoque[43] - [21].
Un brevet est déposé le 12 aout 1919 par Malcolm Loughead pour Allan Haines Loughead, Anthony Stadlman et Jack Northrop[44]:
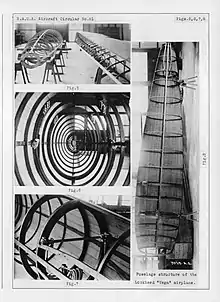
La méthode employée pour le Loughead S-1 rendant impossible de soumettre l'ensemble d'une grande unité de contreplaqué à une pression efficace en une seule fois — car l'adhésif utilisé pour assembler les premières bandes avait fait prise avant qu'il soit possible de terminer l'application des bandes ou pièces formant la dernière couche — le processus de fabrication des demi-coques incurvées s'est fait par unité de couches séparées. Le travail en plusieurs étapes consistait d'abord à assembler à la colle les couches de plaquage incurvées séparément sur le moule; elles étaient en plus marouflées par une couche de tissu fin ou de papier de soie. La couche terminée pouvait ensuite être retirée en tant qu'unité prête à l'emploi. Deux ou plusieurs couches dont les fils étaient croisés, étaient alors placées sur le moule, un adhésif entre les couches, et toute la surface était soumise à une pression avant que l'adhésif n'ait fait prise[45].
Des photos montrent la coque extrêmement légère du S-1 encore ouverte, soutenue à bout de bras par deux hommes. La coque avait un rapport résistance-poids exceptionnel.
En 1926, utilisant désormais l'orthographe phonétique de leur nom, les frères Loughead fondent la Lockheed Aircraft Company qui ouvre une usine à Hollywood, en Californie, pour commencer la production d'un monoplan monomoteur à aile haute cantilever, le Lockheed Vega, construit selon la même technique[43]. Le moule utilisé pour le Vega sera utilisé aussi pour produire les Air Express, Explorer, Sirius, Orion et Altair. Cette série est interrompue par les premiers exemplaires de Vega et Sirius en métal, en février 1932. Le métal est introduit par le nouvel actionnaire de Lockheed, la Detroit Aircraft Corporation de Edward S. Evans. La crise de 1929 étant passée par là, l'entreprise ferme la même année[39].
Les procédés
A côté des fuselages monocoques en bois, nombreuses autres petites pièces en stratifié moulé furent fabriquées en utilisant des matrices métalliques assorties, des vessies de pression à l'intérieur de matrices femelles, des vide sous sacs sur des outils mâles et, plus tard, des autoclaves. Ces types de structure en stratifié de bois moulé ont été les précurseurs des structures semi-monocoque en métal et en composite liée en autoclave d'aujourd'hui[20].
Dans l'entre-deux guerre, l'attention des défenseur de la construction en bois, se porta sur les méthodes de moulage de contreplaqué, sous pression de fluide, qui formeraient des revêtements de poids acceptable, et qui seraient sécurisées contre le froissement et le flambage auxquels les métaux étaient soumis[46]. Le contreplaqué pourrait être façonnées en courbes composées, disponibles jusque là uniquement grâce à l'utilisation de métaux légers estampés et martelés[26]. De telles peaux en contreplaqué, variables d'une partie de surface à une autre en fonction des exigences de résistance, devraient former une coque à haute efficacité tant aérodynamique que structurelle et ne nécessiteraient que des éléments de charpente légers pour la supporter. Ces procédé de moulage étaient en 1941 encore au stade expérimental mais un développement rapide était attendu[46].
À partir de 1940 les techniques mise en œuvre sont souvent désignées spécifiquement, comme les procédés Duramold, Vidal (Eugene Luther Vidal), Aeromold (Timm Aircraft (en)) ou « vacuum-bag processes ». D'autres termes parfois utilisés pour décrire la technique sont « bag-molding », « autoclave molding », « tank molding ». L'expression la plus inclusive serait peut-être « fluid-pressure molding »[28] - [30]. La procédure fondamentale est la même pour tous les procédés d'usage courant. En principe, la technique consiste à attacher temporairement par des agrafes, du ruban adhésif, des clips ou tout autre moyen, des couches superposées de bandes ou de feuilles de placages collés à un moule de la forme souhaitée, et de les mouler en une structure unitaire par l'application de chaleur et pression du liquide à travers un sac ou une couverture souple et imperméable[47].
La fabrication de contreplaqué moulé au sac, de qualité avion ou bateau. nécessite l'utilisation d'équipements considérables. Des moyens d'alimentation en fluide sous pression et en chaleur doivent être prévus. Normalement, un autoclave ou un réservoir sous pression cylindrique de 3 à 12 pieds de diamètre et de 10 à 60 pieds de longueur, qui résistera à une pression de travail interne de 30 à 120 livres par pouce carré, est utilisé[30].
La chaleur peut être fournie de manière plus économique par la vapeur, soit directement, soit indirectement en chauffant de l'eau ou de l'air, d'où la nécessité d'une chaudière ou d'un approvisionnement adéquat en vapeur à partir d'une conduite de vapeur existante. Lorsque l'air est utilisé pour un mélange vapeur-air, ou pour fournir une pression sur l'eau chaude, ou comme moyen de chauffage-pression combiné, un compresseur et un récepteur sont nécessaires. Une pompe à vide peut être utilisée pour induire une pression d'air ou pour vérifier l'étanchéité du sac au-dessus d'un assemblage. Le vide seul produit une pression insuffisante pour la plupart des opérations de moulage avec sac et n'est donc utilisé que pour les opérations de placage à courbure simple, dans les travaux de meubles, et n'est pas recommandé pour le contreplaqué d'avion . Toute opération impliquant l'utilisation de placage suppose l'utilisation de certains des outils usuels pour l'ébarbage du placage, tels que scie, sécateur, toupie, ainsi qu'un étaleur de colle et des râteliers de conditionnement de placage[30].
Dans certaines opérations de moulage de sacs, un contrôle minutieux de la teneur en humidité du placage tout au long du processus est souhaitable. Un équipement de climatisation adéquat est alors une exigence supplémentaire. Le formage de n'importe quel morceau de contreplaqué moulé avec sac nécessite un moule ou matrice d'un certain type, classés comme mâles ou femelles . Les matériaux de moulage courants sont le bois (massif ou contreplaqué), le métal (acier, fonte ou alliages à basse température), les matières plastiques et les ciments. Le choix des matériaux du moule dépendra en grande partie de la forme de la pièce à mouler, de la quantité souhaitée, de la disponibilité, des avantages et inconvénients des' matériaux considérés.
La plupart des opérations de moulage de sacs nécessitent des sacs en caoutchouc naturel ou synthétique spécialement composé, prpoposé par DuPont, Firestone, Goodyear, Goodrich, Tyer Rubber et Voit (en)[30].
Aero
Le bois densifié Aero (un contreplaqué collé au Tego film d'abord développée par Theodor Goldschmidt AG à Essen en Allemagne) a été utilisé dans la fabrication d'hélices pour des avions tels que l'Avro Lancaster, le Handley Page Halifax, le Supermarine Spitfire et le Hawker Typhoon[41].
Haskelite

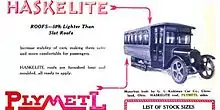
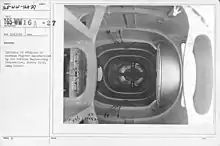
La résistance structurelle légère des placages de bois stratifiés et moulés en une seule pièce a été prouvée par Henry L. Haskell de Ludington dès 1917. De 1917 à environ 1934, la Haskell Boat Company de Ludington, Michigan, construisit un seul modèle de canoé de type Ojibwé en contreplaqué moulé de 17 pieds d'environ , invention que l'on doit à Henry L. Haskell et J.W. Beiger; Dès 1903, Haskell développe un procédé pour extraire l'albumine du sang d'abattoir, à partir duquel ils produit un adhésif imperméable bon marché, appelé « black albumin glue »; à partir duquel Haskell produit un contreplaqué à trois plis, avec les deux faces extérieures de placage de bouleau de 1⁄16 pouces et une couche centrale de séquoia de 1⁄16 pouces. Les trois couches étaient assemblées à la colle d'albumine noire soluble dans l'eau ; une pile de feuilles était pressée à 200 psi et chauffée à plus de 220 degrés Fahrenheit, ce qui a lié la colle et les couches de manière permanente. Une feuille mesurait environ 5 x 20 pieds. Pour faire connaître son produit, Haskell a fait fabriquer des « cartes de visite » à partir de ce contreplaqué qui disaient « Stronger than steel per unit of weight - Boil Me, Bake Me, Soak Me, Break Me - They make me into Haskell Canoes»[48] - [49] [50].Pour fabriquer un canoë, une seule feuille de contreplaqué était découpée en forme de « papillon », puis bouillie dans l'eau pendant 3 heures. Pendant qu'elle était chaude et humide, la feuille de contreplaqué était placée sur un moule mâle et avec des béliers hydrauliques, était pliée en forme de canoë. Des longerons internes en chêne puis des plats-bords en acajou en forme de L et trois bancs en acajou complétaient la structure[48]. La deuxième usine, Haskelite Manufacturing Corporation de Grand Rapids, a cessé de fabriquer des canoës en 1918 et a fabriqué du contreplaqué exclusivement pour le gouvernement américain et ses alliés pendant la Première Guerre mondiale.
Les feuilles fabriquées de cette manière ont finalement reçu le nom commercial de « Haskelite » d'après l'inventeur[51] [50].
Le contreplaqué a reçu des noms de marque en fonction de ses caractéristiques[52]. Plymetl avait des faces métalliques et était utilisé dans la construction de coffres à vêtements hermétiques pour stocker des fourrures et des vêtements coûteux[53]. Plymold était un contreplaqué à base de plastique qui pouvait être moulé, et Phemaloid était un panneau résistant au feu[54].
Haskelite a été utilisé pour les pièces d'avion, en particulier les fuselages et les ailes[55] à commencer par le triplan Curtiss 18T de 1918[56]. Le contreplaqué de Haskell a également été utilisé pour la construction d'avions expérimentaux et commerciaux[57], y compris un avion expérimental Johnson Twin-60 (en) de 1927 avec 85% de contreplaqué Haskelite dans ses ailes, ses sièges, son tableau de bord et ses pièces de fuselage[58].
Pendant la Première Guerre mondiale, l'entreprise a produit plus de 5 000 000 pieds carrés (464 515,2 m2) de contreplaqué destiné à être utilisé dans les avions[59] - [60] [61]. En 1927, la société a fabriqué des pièces de carrosserie d'avion pour l'avion monomoteur Spirit of St. Louis de Charles Linbergh.
Duramold
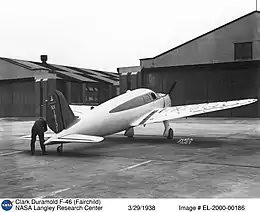

Le procédé qui suit s'appelle Duramold. Il est développé conjointement par la Haskelite Manufacturing sous le nom de Plymold et la Fairchild Engine and Aircraft Corporation sous le nom de Duramold[62] - [63]. Le premier avion commercial à succès sur lequel il a été utilisé était le Fairchild F-46 de 1937[64].
Duramold est un procédé de matériau composite développé par Virginius E. Clark (en) . Les plis de bouleau sont imprégnés de résine phénolique et laminés ensemble dans un moule à chaud (137,8 °C) et sous pression. Le Duramold est conçu pour être utilisé comme matériau structurel léger[65].
Le moule peut être coulé mais est généralement fabriqué à partir de tôle lisse, généralement en feuille de duralumin 1/8 pouce et est rendue parfaitement lisse sur sa surface intérieure critique de sorte que le moulage soit lisse sur la surface extérieure. Pression et chaleur sont appliquées de tous les côtés en plaçant l'ensemble du moule, son contenu et son couvercle dans un réservoir autoclave pour laquelle de la vapeur à 100 livres de pression et une température de 300 °F est admise. Les placages varient de 1/48 à 1/20 pouces d'épaisseur Il est possible de mouler des coques ou des coques partielles et d'appliquer des renforts internes tels que des nervures[25].
Le Duramold pesait environ un tiers du poids des alliages d'aluminium utilisés à l'époque tout en étant plus résistant et un fuselage entier pouvait être transformé en deux moitiés puis scellé mécaniquement[66].
Le Fairchild AT-21 Gunner, (NX/NC19131) est fabriqué à l'aide du procédé Duramold[67]. Plusieurs avions ont utilisé du Duramold dans certaines parties de leur structure, mais le plus gros avion fabriqué avec le procédé est le Hughes H-4 Hercules conçu par Howard Hughes et Glenn Odekirk, qui a été presque entièrement construit avec du Duramold dans de très grandes sections[68]. Hughes Aircraft avait acheté les droits du procédé pour cette utilisation[69]. Le Hughes H-4 Hercules, un hydravion à coque le plus grand avion en bois jamais construit ; commencé en 1940, terminé en 1947, baptisé « Spruce Goose » par ses critiques (« L'oie en sapin »), demeure l'un des plus grands avions au monde derrière le Stratolaunch, l'Antonov 225 et l'Airbus A380.
Duply
Contreplaqué de bouleau assemblé à l'acétate de cellulose par Harry Atwood (en). Un seul avion construit, l'airmobile de 1937[22]. A inspiré Eugene Luther Vidal pour la conception du Vidal Weldwood.
« Duply » était un mot-valise dérivé de « DuPont », dont les laboratoires ont été le site de la première expérimentation, et de « plywood » . Atwood possédait toujours Atwood Carolina, une entreprise de fabrication d'avions d'avant-guerre. Son biographe déclare que lui et Vidal rivalisaient pour être connus sous le nom de "Henry Ford de l'aviation" et Atwood a estimé qu'il avait été escroqué de son brevet par Vidal, qui, selon lui, l'a acheté pour 10 000 $ en 1939, puis n'a payé qu'un an de royalties avant de déposer un brevet sous son propre nom avec de légères modifications dans le processus. Les processus d'Atwood et celui de Vidal se ressemblaient superficiellement mais utilisaient des méthodes de liaison différentes[70].
Vidal Weldwood
Vidal Weldwood a été développé et breveté par Eugene Luther Vidal[71], il servit pour l'Aircraft Research BT-11 (en). Il fut ensuite employé sous licence par de nombreux fabricants.
Dans le processus Vidal développé par Aircraft Research Corporation allié à United States Plywood Corporation, une procédure similaire est utilisée que dans Duramold mais des moules internes sont utilisés. Des nervures de renforcement et d'autres pièces de renforcement sont signalées comme étant moulées en place, et une pression de fluide liquide ou gazeuse est utilisée. Après les placages de bois et les raidisseurs ainsi que le liant plastique soient en place l'ensemble est recouvert d'une couverture en caoutchouc et soumis à la chaleur et à la pression dans un réservoir autoclave[25].
Le procédé Vidal peut être utilisé en fabriquant un moule mâle aux proportions intérieures exactes de la partie de l'avion spécifiée. Le bois est un matériau de prédilection pour ce moule. Les placages, éventuellement découpés sur une matrice de découpe selon le modèle plat souhaité, sont suspendus au-dessus du moule mâle après avoir été plongés dans la solution de résine et laissés sécher. Une fois que le plastique et le placage sont sur le moule mâle, l'ensemble est mis dans un sac en caoutchouc. Ce sac élimine les frais d'un moule femelle. Au fur et à mesure que l'air en est extrait, les plis du sac se resserrent autour des placages; les placages glissent en position sans que beaucoup de contraintes sur les fibres ne soient créées. Le sac et son contenu sont insérés dans un grand réservoir en acier dans lequel la vapeur accumule la chaleur et la pression requises pendant la durée nécessaire. L'épicéa, l'acajou africain et d'autres bois sont traités de cette manière. Des fuselages renforcés, des ailes, des ascenseurs, des volets, des ailerons, des stabilisateurs, des dérives verticales, des flotteurs, des commandes diverses, des trappes de soute à bombes et des nacelles ont été réalisés de cette manière. Les fuselages sont sans couture. Les ailes seraient 40 % plus légères que celles en métal. La United States Plywood a des droits sur le procédé Vidal en dehors des domaines aéronautiques, dont les droits aéronautiques sont gérés par Aircraft Research[24].
Aeromold
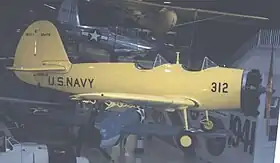
Aeromold est un procédé breveté par Timm Aircraft (en), employé pour le Timm N2T Tutor.
L'entreprise a développé un matériau "plastique" composé de résine et de bois similaire au procédé Duramold. Le procédé Duramold a été suivi par le procédé Weldwood de Eugene Luther Vidal et plus tard le procédé Aeromold. Le processus Aeromold diffère en ce qu'il est cuit à une basse température de 37,8 °C lors de la coupe et du formage, et à 82,2 °C pour fusionner les sections après l'ajout des résines.
Les matériaux seraient confinés au contreplaqué d'épicéa 1/24 pouces dans des solutions de résine phénolique épaisses et certaines spéciales. La coque est formée sur un moule en bois et se compose de plis et de couches de résine phénolique. La coque est transféré dans un moule en métal et une pression de 50 livre par pouce carré est appliquée pendant une période de 2 heures pour forcer la résine dans les pores du bois, puis elle est transférée dans un gabarit d'assemblage où elle est appliqué sur les éléments de raidissement après que chaque joint a été saturé de résine. Les assemblages encore sur gabarits sont tournés dans un four et cuits pendant plusieurs heures[25].
Plyweld
Plyweld a été développé par Fletcher Aviation, notamment utilisé pour le Fletcher FBT-2[33].
L'avion Fletcher n'est pas un avion moulé. Il est fabriqué selon un procédé conçu pour éliminer les inconvénients liés à une grande matrice et à l'équipement de four spécial nécessaire au moulage. Les pièces en contreplaqué sont collées entre elles sous vide à l'aide d'un adhésif de type urée-formaldéhyde qui est acheté sous forme de poudre. Mélangé avec de l'eau avant l'application, il polymérise ou durcit pour former une forte adhérence imperméable[33].
Plasti-ply se conçoit comme un revêtement qui se compose de deux feuilles de placage de bois collées ensemble avec un adhésif résineux. La direction du grain de chaque stratification est posée à un angle de 25° à l'axe longitudinal de la feuille, ce qui se traduit par une résistance maximale dans la direction de l'axe longitudinal, et une flexibilité maximale dans la direction perpendiculaire. Ce qui correspond aux conditions requises pour les revêtements d'aile par exemple: une résistance maximale est requise dans le sens de l'envergure et une flexibilité maximale dans le sens de la corde. Pour le fuselage, une résistance maximale est requise dans le sens longitudinal et une flexibilité maximale dans le sens transversal. La flexibilité de Plasti-ply est extrêmement grande et permet une flexion même autour du petit rayon de un bord d'attaque sans préformage. Il est ainsi possible d'appliquer la peau d'une aile complète comme une unité. Un sac à vide en caoutchouc fournit la pression nécessaire pour coller la peau aux nervures et aux longerons. Un simple gabarit localise les nervures et les longerons de l'aile pendant qu'ils sont collés ensemble pour former un cadre sur lequel la peau est appliquée. Un gabarit similaire pour le fuselage localise les cloisons pour l'assemblage du revêtement des cloisons. Cette partie de la fabrication peut être facilement sous-traité à l'industrie du meuble[33].
Duraloïd
En 1942, Robert J Nebesar a développé et breveté un processus de moulage de contreplaqué[72] dans lequel du contreplaqué moulé sera lié à la bakélite. Le processus a été commercialisé sous le nom commercial « Duraloïd ». Le Bennett BTC-1 Executive de Bennett Aircraft Company, était un avion américain entièrement construit en « Duraloïd ». Durant la Seconde Guerre mondiale, la firme Globe Aircraft Corporation (en), qui succéda à Bennett Aircraft Company, a produit des panneaux d'avion en Duraloïd.
Bellanca process
Dans le procédé Bellanca, le moulage se fait sous pression mécanique appliquée en serrant les tôles après quoi elles sont enduites de résine entre des formes qui constituent en fait des moules. La procédure se comprend comme impliquant l'application de la résine employée dans une solution aqueuse à laquelle est ajouté un accélérateur qui confère à la résine phénolique des propriétés de prise à froid et accélère le durcissement lorsque la chaleur est appliquée ultérieurement. Les ingrédients spéciaux développés par American Catalin Corporation ont des propriétés telles que le durcissement peut être effectué à une température inhabituellement basse pour un matériau phénolique de 140 °F[25].
Plyformed
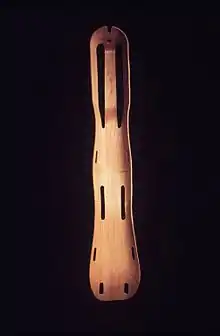
Charles et Ray Eames, ont formé une entreprise appelée Plyformed Wood Company pour produire des attelles de jambes en contreplaqué en grand nombre, après avoir obtenu un contrat de l'US Navy en novembre 1942; Plyform ou Plyformed étant le nom adopté du nouveau matériau moulé[73]. L'entreprise fut reprise par la Evans Products Company, pour former la Molded Plywood Division ; Charles Eames responsable des travaux de recherche et développement. Un brevet de fabrication fut produit par Eames[74]. L'entreprise commença à construire diverses pièces d'avion en contreplaqué moulé pour la Marine des États-Unis, des queues de stabilisateur d'avion, de fuselage et d'autres pièces d'avion pour des fabricants tels que Vultee Aircraft[75]. En 1943, commande du concepteur de planeurs Hawley Bowlus de General Airborne Transport Co., ils fabriquèrent également un fuselage d'avion, une queue de stabilisateur d'avion et d'autres pièces pour le General Airborne Transport XCG-16, y compris le siège du pilote, objet qui leur était un peu plus familier[76].
L'expérience acquise grâce à la production à grande échelle des attelles a été très utiles aux Eames pour leurs aventures d'après-guerre dans les objets en contreplaqué produits en série[77].
Les sièges proposés par le duo Eames-Saarinen pour le concours « Organic Design » du MoMA avaient fait usage de Haskelite. Hors des maquettes proposées par le duo, un moule en fonte avait été fabriqué et la coque en contreplaqué de la chaise finale avait été collée dans ce moule par Haskelite Corporation. Il fut envisagé que la Heywood-Wakefield Company et la Haskelite Manufacturing Corporation devaient produire en série les chaises, mais l'entrée en guerre des États-Unis (après l'attaque de Pearl Harbor le 7 décembre 1941) a annulé ce programme[78] - [79].
Le rachat de la Haskelite Manufacturing Corporation par Evans Products dans les années fin 1956, suggère peut-être une collaboration ancienne entre les deux sociétés[80].
D'autre fabricants d'avions ont employé le contreplaqué, comme la Morrow Aircraft Corporation (en)[33]. Plxwave a utilisé des structures géodésiques en longerons de contreplaqué lamellés collés[33].
Références
- (en) Forest Products Laboratory (U.S.), Wood Aircraft Inspection and Fabrication: War Department, Army Air Forces. Navy Department, Bureau of Aeronautics. Department of Commerce, Civil Aeronautics Administration, U.S. Government Printing Office, (lire en ligne)
- (en) Report, U.S. Department of Agriculture, Forest Service, Forest Products Laboratory, (lire en ligne)
- (en) Eliot Noyes, Organic Design in Home Furnishings, New-York City, Museum of Modern Art, (lire en ligne [PDF])
- Belter 1858
- (en) « V&A · A short history of plywood in ten-ish objects », sur Victoria and Albert Museum (consulté le )
- Cole 1874
- « Material-Archiv », sur materialarchiv.ch (consulté le )
- (en) Pat Kirkham, Charles and Ray Eames: Designers of the Twentieth Century, MIT Press, (ISBN 978-0-262-61139-8, lire en ligne)
- (en) Cherie Fehrman et Kenneth Fehrman, Interior Design Innovators 1910-1960, Fehrman Books, (ISBN 978-0-9842001-0-8, lire en ligne)
- (en) Ralph Caplan, The Design of Herman Miller, Whitney Library of Design, (ISBN 978-0-8230-7141-8, lire en ligne)
- (en) Design Review, Whitney Library of Design., (ISBN 978-0-8230-7157-9, lire en ligne)
- (en) Cherie Fehrman et Kenneth Fehrman, Postwar Interior Design, 1945-1960, Van Nostrand Reinhold, (ISBN 978-0-442-22617-6, lire en ligne)
- (en) The Timberman, M. Freeman Publications, (lire en ligne)
- Saunders 1899
- « Steam Launch Consuta - 1898 fast river launch for umpiring duties », sur www.consuta.org.uk (consulté le )
- (en) « Consuta home page », sur www.consuta.org.uk (consulté le )
- Haskell 1920-06-29.
- (en) Bonnier Corporation, Popular Science, Bonnier Corporation, (lire en ligne)
- (en) « Kockheed "vega" airplane : a commercial cabin monoplane », Aircraft Circular::National Advisory comitee for aeronautics, (lire en ligne, consulté le )
- Alphonsus V. Pocius, David A. Dillard et Manoj Kumar Chaudhury, Adhesion science and engineering, Elsevier, (ISBN 978-0-444-51140-9, 0-444-51140-7 et 0-08-052598-9, OCLC 162129877, lire en ligne)
- (en) United States Federal Aviation Administration, Pilot's Handbook of Aeronautical Knowledge, Aviation Supplies & Academics, Incorporated, (ISBN 978-1-56027-750-7, lire en ligne)
- (en) NASA's Contributions to Aeronautics, Volume 2, Flight Environment ..., NASA/SP-2010-570-Vol 2, 2010, *, (ISBN 978-0-16-084636-6, lire en ligne)
- (en) Sara Witter Connor, Wisconsin's Flying Trees in World War II: A Victory for American Forest Products and Allied Aviation, Arcadia Publishing, (ISBN 978-1-62584-910-6, lire en ligne)
- (en) Flying Magazine, (lire en ligne)
- (en) United States Army Air Forces, Technical data digest. U.S.Army Air corps : Confidential Documents, (lire en ligne)
- (en) Bonnier Corporation, Popular Science, Bonnier Corporation, (lire en ligne)
- (en) " "Plastes (pseud.), Plastics in Industry, Chapman & Hall Limited, (lire en ligne)
- Bruce G. Heebink et Forest Products Laboratory (U.S.), « Fluid-pressure molding of plywood », sur ir.library.oregonstate.edu (consulté le )
- VON HIPPEL, Arthur R. et DIETZ, Albert George Henry. Curing of resin-wood combinations by high-frequency heating. 1942.
- Forest Products Laboratory (U.S.) et Bruce G. Heebink, « Bag-molding of plywood », sur ir.library.oregonstate.edu (consulté le )
- (en) « Introduction to Aerospace Materials | ScienceDirect », sur www.sciencedirect.com (consulté le )
- (en) « Design and Construction of the NC Flying Boats », sur U.S. Naval Institute, (consulté le )
- (en) Aero Digest, Aeronautical Digest Publishing Corporation, (lire en ligne)
- W.Finolds, Le monocoque Deperdussin : Champion de la vitesse!, L'Expansion belge, (lire en ligne)
- « Nieuport-Delage NiD.29 - Description », sur Techno-Science.net (consulté le )
- (en-US) Medicman11, « LFG Roland C.II », sur Plane-Encyclopedia, (consulté le )
- A30yoyo, DH-91 Albatross fuselage moulding, (lire en ligne)
- « Manufacturing Process of de Havilland Mosquito in 1944 » (consulté le )
- (en) Graham M. Simons, Lockheed TriStar: The Most Technologically Advanced Commercial Jet of Its Time, Air World, (ISBN 978-1-5267-5885-9, lire en ligne)
- Forest Products Mission et Forest Products Laboratory (U.S.), « The use of wood for aircraft in the United Kingdom : Report of the Forest Products Mission », sur ir.library.oregonstate.edu (consulté le )
- (en) Phillipe Cognard, Handbook of Adhesives and Sealants: Basic Concepts and High Tech Bonding, Elsevier, (ISBN 978-0-08-053409-1, lire en ligne)
- « de Havilland D.H.100 Vampire III », sur www-archives.ingeniumcanada.org (consulté le )
- « Wooden Wonders: Early Lockheed Aircraft | SFO Museum », sur www.sfomuseum.org (consulté le )
- Loughead 1922
- Loughead Malcolm, Process of manufacturing curved forms of plywood or fibrous compositions, (lire en ligne)
- Carlile P. Winslow, United States, University of Wisconsin et Forest Products Laboratory (U.S.), Forest products and defense, U.S. Dept. of Agriculture, Forest Service, Forest Products Laboratory, coll. « [Report] ;R1250FU », (lire en ligne)
- Bruce G. Heebink, « Fluid-pressure molding of plywood : Technical Report », sur ir.library.oregonstate.edu (consulté le )
- « Haskell Boat Company | Wooden Canoe Museum », sur woodencanoemuseum.org (consulté le )
- McCloud, Tom. À Haskell Goes Home: The Restoration of a Haskell Molded Plywood Canoe. Wooden Canoe Issue 179, October 2013.
- Motor Boat 1920, p. 38.
- Motor Body 1919, p. 54.
- Hardwood Record 1920, p. 30.
- Chicago Tribune, November 9, 1923
- Marine Engineering 1933, p. 208-213.
- Dunbar 1955, p. 439.
- (en) Gordon G. Beld, The Early Days of Aviation in Grand Rapids, Arcadia Publishing, (ISBN 978-1-61423-805-8, lire en ligne)
- Daily News, August 1, 1939
- « New Johnson Twin 60 adopts Haskelite », Aero-Digest, vol. 10, , p. 2 (lire en ligne, consulté le )
- June 26, 1993, Daily News
- Daily News, September 3, 1965
- Beld 2012, p. 99.
- « 15 July 1943 », The Ludington Daily News, , p. 3 (lire en ligne, consulté le )
- (en) « New Process Developed by Chicago Firm », Chicago Tribune, , p. 25 (lire en ligne)
- Daily News, July 15, 1943
- United Service and Royal Aero Club (Great Britain), Royal Aero Club of the United Kingdom, United Service and Royal Aero Club, Flight International, volume 42
- Chicago Tribune, January 22, 1939
- Frank Woodring et Suanne Woodring, Fairchild Aircraft
- Parker, Dana T. Building Victory: Aircraft Manufacturing in the Los Angeles Area in World War II, pp. 49-58, Cypress, CA, 2013. (ISBN 978-0-9897906-0-4).
- « Plastic Airplane Industry is near », Lansing State Journal, Lansing, Michigan, (lire en ligne)
- Howard Mansfield, Skylark : the life, lies, and inventions of Harry Atwood, University Press of New England, (ISBN 0-87451-891-1 et 978-0-87451-891-7, OCLC 39706864, lire en ligne)
- Vidal 1942
- Nebesar 1945-02-27.
- (en) « Wartime Plyformed Molded Leg Splint by Charles Eames », sur Eames.com (consulté le )
- Eames 1946-02-26.
- (en-US) « Airplane Stabilizer Tail », sur Eames Office (consulté le )
- (en-US) « The Pilot Seat », sur Eames Office (consulté le )
- (en) Pat Kirkham, Charles and Ray Eames: Designers of the Twentieth Century, MIT Press, (ISBN 978-0-262-61139-8, lire en ligne)
- Eero Internet Archive, Eero Saarinen : shaping the future, New Haven : Yale University Press ; New York : in association with the Finnish Cultural Institute in New York ; Helsinki : The Museum of Finnish Architecture ; Washington, D.C. : The National Building Museum ; New Haven : Yale University School of Architecture, (ISBN 978-0-300-11282-5, 978-0-9724881-2-9 et 978-0-300-12237-4, lire en ligne)
- (en-US) « Designed To Serve | Cooper Hewitt, Smithsonian Design Museum », sur www.cooperhewitt.org, (consulté le )
- « Clipped From Corvallis Gazette-Times », Corvallis Gazette-Times, , p. 10 (lire en ligne, consulté le )
Brevets
- John Henry Belter, Improvement in the method of manufacturing furniture, (lire en ligne)
- Isaak Cole, Improvement in chairs, (lire en ligne)
- Samuel edgar saunders, (lire en ligne)
- Henry L. Haskell, Aeroplane-body, (lire en ligne)
- Malcolm Loughead, Process of manufacturing curved forms of plywood or fibrous compositions, (lire en ligne)
- Eugene L. Vidal et Laurence J. Marhoefer, Method of forming veneer structures, (lire en ligne)
- Robert J. Nebesar, Molding, shaping, and uniting apparatus, (lire en ligne)
- Eames Charles, Method of making laminated articles, (lire en ligne)
- Verhey William, Method of making plywood shells, (lire en ligne)
- Monroe M. Teague, Fluid pressure veneer press, (lire en ligne)
Bibliographie
- Gordon G. Beld, The Early Days of Aviation in Grand Rapids, Charleston, South Carolina, Arcadia Publishing, (ISBN 978-1-61423-805-8, OCLC 945368042, lire en ligne)
- Willis Frederick Dunbar, Michigan Through the Centuries, Detroit, Michigan, Lewis Historical Publishing Company, (lire en ligne)
- « Veneer Enters Vast New Field », Hardwood Record, vol. 49, , p. 29+ (lire en ligne)
- Joseph Nathan Kane, Famous First Facts and Records, New York City, The H. W. Wilson Company, (lire en ligne), p. 70
- « Titre inconnu », Marine Engineering and Shipping Age, vol. 38, , p. 208–213 (lire en ligne)
- « Haskelite, a Plywood for Boat Construction », Motor Boat, vol. 17, , p. 38 (lire en ligne)
- « Why Haskelite flat panels are once and for all flat » (publicité), The Vehicle Monthly, vol. 55, , p. 54–55 (lire en ligne)
- « Veneers and Plywood », S.H. Smith, vol. 24, , p. 19 (lire en ligne)
- (en) Forest Products Laboratory (U.S.), Wood Aircraft Inspection and Fabrication: War Department, Army Air Forces. Navy Department, Bureau of Aeronautics. Department of Commerce, Civil Aeronautics Administration, U.S. Government Printing Office, (lire en ligne)
- Forest Products Laboratory (U S. );United States Army-Navy-Civil Committee on Aircraft Design Criteria ;United States Aeronautical Board, « Wood aircraft inspection and fabrication », sur library.si.edu, (consulté le )
- Thomas D. Perry, « Aircraft Plywood and Adhesives », Journal of the Aeronautical Sciences, vol. 8, no 5, , p. 204–216 (DOI 10.2514/8.10684, lire en ligne, consulté le )