Mobilier en contreplaqué moulé
Le contreplaqué moulé trouve des applications dans le mobilier en contreplaqué moulé.
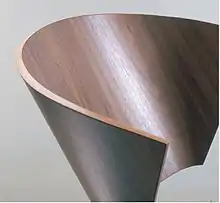
Le contreplaqué moulé est un produit bidimensionnel ou tridimensionnel composé de plusieurs couches de placage qui sont collées ensemble à l'aide d'un adhésif, de chaleur et de pression dans un outil de pressage. Les couches de placage alternativement sont disposées selon un angle de 90 degrés selon le sens du fil. Le contreplaqué moulé est utilisé pour les composants de meubles tels que les chaises, les dossiers et les coques de siège.
Si les couches de placage sont disposées dans le même sens de fil , il s'agit de bois lamellé-collé moulé. Il est utilisé pour les accoudoirs et les cadres de chaise. Une fois les pièces pressées, elles sont finies à la machine.
Une particularité est la possibilité de produire différentes variantes de contour à partir des matrices. En raison de sa haute robustesse et de son faible poids, le contreplaqué moulé est particulièrement adapté à la décoration intérieure, aux sièges, aux lattes de lit, aux planches à roulettes et à la construction de véhicules .
Histoire du contreplaqué moulé dans le mobilier
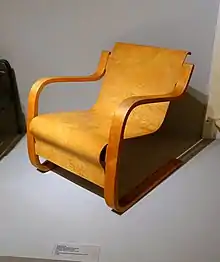
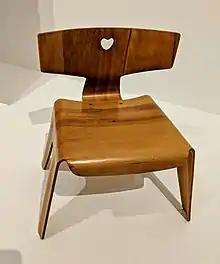
%252C_zeeland_(MI)_1946_ca.jpg.webp)
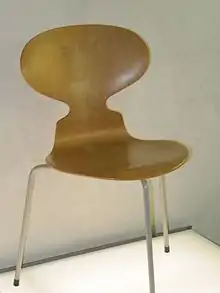
Entre 1850 et 1890, le contreplaqué moulé était dans la conception de meubles, plus courant que les panneaux selon le même matériau et la conception de mobilier était le moteur de son innovation. Une technique de moulage de meubles a été brevetée à New York en 1858 par John Henry Belter (en)[patent 1], pour produire des dossiers de chaises. Sa technique augmentait la vitesse de fabrication et réduisait les coûts de production, car les dossiers pouvaient être fabriqués par huit à l'aide d'un seul moule[3]. Une chaise d'Isaak Cole de 1874 est considérée comme le premier meuble entièrement composé de coques en bois moulé[patent 2] - [4].
Dès 1830, le designer de meubles Michael Thonet expérimente le collage de couches de placage selon des déformations bidimensionnelles; il a arrêté ces tentatives et a développé le procédé du bois cintré pour produire des composants en bois formé en trois dimensions à partir de bois massif.
Le contreplaqué moulé est apparu dans la production de meubles de masse après la Première Guerre mondiale. Les méthodes de production de masse et les considérations esthétiques deviendront la préoccupation d'architectes et de designers tels que Mart Stamm, Alvar Aalto, Marcel Breuer, Eero Saarinen, Charles et Ray Eames et Arne Jacobsen[4].
Le Fauteuil Paimio, conçu par Alvar Aalto et Huonekalu- ja Rakennustyötehdas (en) en 1932 pour Sanatorium de Paimio en Finlande sera fabriqué aux côtés d'autres créations de meubles d'Aalto pour la vente générale et exportés en grande quantité au Royaume-Uni et aux États-Unis, où son utilisation innovante du contreplaqué aura un impact significatif sur d'autres designers[3]. Aalto va produire un fauteuil moulé composé, annoncé par Domus en 1932 et présenté au Nordic Building Congress la même année mais qui ne sera jamais été exposé ni fabriqué, probablement parce que le processus prenait du temps et criblé de difficultés techniques. Le designer et fabricant de meubles britannique Gerald Summers (en), dont certains meubles en contreplaqué étaient vendus dans les grands magasins américains dans les années 1930, a produit deux chaises en contreplaqué multidimensionnel, apparemment avec plus de succès[5].
Pendant l'entre-guerre et la Seconde Guerre mondiale le nouveau moteur de l'innovation dans le moulage des contreplaqués et la diffusion des adhésifs de synthèse sera l'aéronautique. En 1931, la société Gebrüder Thonet lance le modèle S43, la première chaise cantilever en tube d'acier, dans laquelle le designer Mart Stam utilise des pièces en contreplaqué moulé de forme tridimensionnelle pour l'assise et le dossier afin de rendre la chaise très confortable sans rembourrage et lui donner une apparence de légèreté.
Une série de sièges multi-dimensionnel sont conçus par Charles Eames et Eero Saarinen pour l'exposition de 1941, Organic Design in Home Furnishings du MoMA, et sont réalisés par la Haskelite Manufacturing Corporation[6]. Il fut envisagé que La Heywood-Wakefield Company et la Haskelite Manufacturing Corporation devaient produire en série les chaises, mais l'entrée en guerre des États-Unis (après l'attaque de Pearl Harbor le 7 décembre 1941) a annulé ce programme[7] - [8].
Par la suite Charles et Ray Eames, vont obtenir des commandes de l'armée pour des attelles de jambes en bois moulé qu'ils vont fabriquer au sein d'une première entité, la Plyformed Wood Company dissoute en juillet 1943, tous les produits des Eames (Eames Process), compris l'attelle de jambe, sont fabriqué à partir de cette date par la division du contreplaqué moulé d'Evans Products, la «Molded Plywood Division »[9]. Evans Product développa, soutint le développement des processus de fabrication et même construit l'outillage réel qui fabriqua les attelles[10] et au sortir de la guerre le premier mobilier de Eames. En 1946, la technologie utilisée pour le mobilier des Eames dans leurs ateliers de Venice à Los Angeles, et dans l'usine de Evans Product à Coos Bay en Oregon, avait atteint un tel stade de développement, que des distributeurs comme la Herman Miller Furniture Company à Zeeland, Michigan, se sont dans un premier temps raccroché à un train qui les avait dépassé[11] - [12] - [13] - [14] - [15]. Les Eames ont par la suite développé la Collection de meubles en contreplaqué pour la société Herman Miller.
En 1952, Arne Jacobsen présenta une chaise au nom inhabituel « Ant », qui connut plus tard un grand succès. Des millions de « classiques » issus de ces modèles sont encore produits et vendus aujourd'hui.
Termes
Contreplaqué moulé
Terme désignant des pièces moulées composées d'au moins trois placages minces collés les uns aux autres, qui sont tournés de 90 degrés dans le sens du fil. Les couches de cette manières sont calées et le procédé évite le gonflement (en) et le rétrécissement (de) pour une résistance acrue. Les propriétés sont utilisées pour les pièces moulées telles que les sièges, les dossiers et les coques de chaises . Les qualités de placage peuvent être assemblées pour des pièces en contreplaqué moulé apparentes ou tapissées . Les couches intérieures sont fabriquées à partir de placages écorcés moins coûteux. Les couches supérieures peuvent être choisies parmi les placages déroulés, les placages tranchés de bois précieux ou les panneaux stratifiés .
Contreplaqué lamellé moulé

Le bois lamellé moulé fait référence à des pièces moulées dans lesquelles le fil court dans le même sens. Afin d'augmenter la résistance à la flexion et de réduire les comportements de gonflement et de retrait, le bois lamellé moulé est scellé avec quelques placages transversaux pour certaines applications. Le bois lamellé moulé est utilisé pour les bâtis de chaises, les parties latérales en porte-à-faux et les accoudoirs . Les assemblages peuvent être pressés ensemble à l'aide de gousset en bois lamellé (triangle) L'épaisseur des pièces moulées peut être modifiée en utilisant des placages intérieurs rectifiés . La résistance à la traction est nettement supérieure à celle du contreplaqué moulé.
Fabrication
Le processus de fabrication est divisé en trois étapes. Tout d'abord, le placage pelé est produit, puis le contreplaqué moulé ou les ébauches de bois lamellé moulé sont pressées à partir de celui-ci, qui sont ensuite traitées. À la fin, il y a des meubles ou des éléments d'intérieur prêts à installer.
Production de placage
Le bois de hêtre est utilisé en Europe. Il est disponible en grande quantité à partir de forêts gérées durablement. Le bois de bouleau est souvent utilisé dans le nord et l'est de l'Europe. L'érable noir est utilisé en Amérique du Nord . En raison de la la dormance de l'arbre, le bois du tronc n'est récolté qu'en hiver et doit ensuite être arrosé dans la zone de stockage ou stocké sous eau . Pour produire du placage, les bois ronds sont cuits à la vapeur dans des puits à vapeur à 85 degrés Celsius. Ce qui rend le bois souple . L'étape suivante consiste en le sciage transversal des bois ronds et l'écorçage. Les longueurs des sections de tronc dépendent des dimensions de placage requises pour les commandes. Dans la machine à dérouler, le couteau à dérouler est guidé contre la section de bûche rotative à haute pression. Une bande de placage cohésive est créée, qui est coupée à la largeur requise. Des placages avec des épaisseurs de 0,6 mm jusqu'à 2,3 mm sont générés. Les placages encore humides subissent le processus de séchage. Immédiatement après, le placage déroulé est automatiquement trié selon ses qualités optiques. Une distinction est faite entre les placages à usage apparent et ceux présentant des nœuds et des craquelures, qui serviront de remplissage dans les pièces moulées.
Moulage par compression
Une fois le placage préparé pour une commande, un outil de pressage est installé dans une presse. Les outils de pressage peuvent être construits en deux parties (pour les sièges, les dossiers et les coques ) ou en plusieurs parties, par exemple les moulures en forme de U où une pression est également requise sur le côté . Le pressage commence par le collage des placages sur des rouleaux encolleurs. Une résine d'urée avec un durcisseur est utilisée comme colle, qui durcit de manière duroplastique lors du pressage. Un paquet dit de placage est ensuite placé dans l'outil de presse, qui est chauffé à 100 degrés Celsius. La presse est arrêtée. La pression de pressage est d'environ 25 N/cm². Le temps de pressage dépend de l'épaisseur des pièces moulées. Plus la pièce moulée est épaisse, plus elle est longuement pressée . Les coques ont besoin d'environ 5 minutes, les parties latérales plus épaisses parfois 20 minutes. Une exception est le collage à haute fréquence, dans lequel le joint de colle est chauffé par un champ de condensateur, ce qui réduit considérablement le temps de pressage . Ce procédé est donc adapté aux pièces moulées très épaisses. Le placage étant un produit naturel, certaines limites doivent être respectées lors de la déformation. Le plus petit rayon dépend de l'épaisseur du placage utilisé et est de 12 mm pour un angle de 90 degrés. Un effilement des pièces moulées est possible. La possibilité de déformation tridimensionnelle n'est guère limitée pour les pièces de remplissage. Pour les bois apparents, de légères déformations jusqu'à l'apparition de fissures ou de compression du placage sont possibles. Ce qui peut être déformé avec du carton solide peut également être fabriqué à partir de contreplaqué moulé, car les deux se comportent de manière similaire. Ces limites peuvent être dépassées en utilisant des facettes 3D spéciales, qui sont cependant plus complexes à produire et sont donc associées à des coûts supplémentaires.
Montage
Les ébauches de contreplaqué moulé déformées en trois dimensions pour les sièges, les coques et les dossiers sont fraisées avec des fraiseuses CNC multi-axes et percées si nécessaire. La variété des variantes est ici très élevée, car seuls de nouveaux programmes de fraisage sont écrits pour d'autres contours. Après avoir poncé les bords et installé le matériel de montage, ils sont prêts pour la peinture.
Les ébauches de contreplaqué façonnées pour les cadres et les composants des chaises sont coupées, poncées et traitées par ordinateur avec des fraiseuses CNC à réglage automatique. Des techniques d'assemblage spéciales telles que des assemblages à vis, à goujon, à entures multiples, à languette ou à fente et tenon peuvent être utilisées pour produire des composants prêts à installer ou des cadres complets .
Surfaces
Les surfaces de contreplaqué et de bois de placage stratifié peuvent être conçues de différentes manières en pressant des couches supérieures de placages tranchés de bois précieux tels que le chêne, l'érable, le cerisier, le frêne, le noyer et d'autres bois. Les films mélaminés colorés offrent d'autres possibilités de design ; Films décors, impressions numériques et stratifiés décoratifs (HPL/ CPL) et bien sûr lasures et vernis, transparents ou opaques . Des systèmes de peinture modernes à base d'eau sont utilisés à cet effet.
Les caractéristiques
Le contreplaqué moulé et le bois lamellé moulé sont très résistants par rapport à d'autres matériaux à base de bois tels que les panneaux de fibres à densité moyenne ou les panneaux de particules. Cela leur donne un large éventail d'utilisations.
Force
Selon le type de bois, la résistance à la traction est de 110-135 N/cm². Elle implique que des chaises cantilever en stratifié moulé pour la haute résilience et le comportement de balancement agréable.
Résistance à la compression
La résistance à la compression des essences de bois utilisées pour le bois moulé est comprise entre 50 et 62 N/cm². Il garantit des meubles durables qui peuvent également résister à des contraintes extrêmes, telles que celles rencontrées par ex. dans les écoles.
Résistance aux intempéries
Le bois de hêtre n'est en effet pas adapté à une utilisation en extérieur car il est très rapidement décomposé par les champignons lignivores. Mais par un changement chimique ou thermique, il est possible de rendre le contreplaqué moulé et le bois lamellé moulé résistant aux intempéries.
Faible inflammabilité
La faible inflammabilité du bois moulé est obtenue grâce à l'introduction de sels dans le processus de fabrication. C'est un aspect important, en particulier lorsqu'il s'agit de design d'intérieur et lorsqu'il est utilisé pour les sièges dans les trains.
Notes
Références
- (de) Cet article est partiellement ou en totalité issu de l’article de Wikipédia en allemand intitulé « Formsperrholz » (voir la liste des auteurs).
- « Child'chair », sur www.metmuseum.org (consulté le )
- « Collection | Milwaukee Art Museum », sur collection.mam.org (consulté le )
- (en) « V&A · A short history of plywood in ten-ish objects », sur Victoria and Albert Museum (consulté le )
- « Material-Archiv », sur materialarchiv.ch (consulté le )
- (en) Pat Kirkham, Charles and Ray Eames: Designers of the Twentieth Century, MIT Press, (ISBN 978-0-262-61139-8, lire en ligne)
- (en) Eliot Noyes, Organic Design in Home Furnishings, New-York City, Museum of Modern Art, (lire en ligne [PDF])
- Eero Internet Archive, Eero Saarinen : shaping the future, New Haven : Yale University Press ; New York : in association with the Finnish Cultural Institute in New York ; Helsinki : The Museum of Finnish Architecture ; Washington, D.C. : The National Building Museum ; New Haven : Yale University School of Architecture, (ISBN 978-0-300-11282-5, 978-0-9724881-2-9 et 978-0-300-12237-4, lire en ligne)
- (en-US) « Designed To Serve | Cooper Hewitt, Smithsonian Design Museum », sur www.cooperhewitt.org, (consulté le )
- (en-US) « MOLDED PLYWOOD GROUP », sur Eames Office (consulté le )
- (en-US) « Molded Plywood Leg Splint », sur Eames Office (consulté le )
- (en) Cherie Fehrman et Kenneth Fehrman, Interior Design Innovators 1910-1960, Fehrman Books, (ISBN 978-0-9842001-0-8, lire en ligne)
- (en) Ralph Caplan, The Design of Herman Miller, Whitney Library of Design, (ISBN 978-0-8230-7141-8, lire en ligne)
- (en) Design Review, Whitney Library of Design., (ISBN 978-0-8230-7157-9, lire en ligne)
- (en) Cherie Fehrman et Kenneth Fehrman, Postwar Interior Design, 1945-1960, Van Nostrand Reinhold, (ISBN 978-0-442-22617-6, lire en ligne)
- (en) The Timberman, M. Freeman Publications, (lire en ligne)