Béton de ciment
Le béton de ciment, couramment appelé béton, est un mélange de ciment, de granulats, d'eau et d'adjuvants.
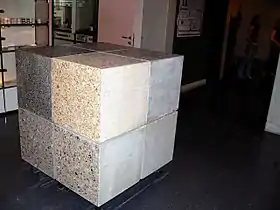
Le ciment
Le ciment se compose essentiellement de chaux, de silice, d'alumine et d'oxyde de fer combinés au silicate et aluminate de calcium. Les différents ciments résultent du mélange de clinker, de calcaire, de laitier et de cendres volantes (qui sont des composés à effet pouzzolanique, mais non considérés comme des pouzzolanes).
La fabrication du ciment se décompose en 6 étapes :
- lâextraction (de calcaire et dâargile) ;
- lâhomogĂ©nĂ©isation ;
- le séchage et le broyage ;
- la cuisson ;
- le refroidissement ;
- le broyage.
Les granulats
Un granulat est composĂ© dâun ensemble de grains minĂ©raux qui, selon sa dimension, se situe dans une famille particuliĂšre. Les granulats sont donc triĂ©s selon leur granulomĂ©trie, câest-Ă -dire selon leur diamĂštre, et peuvent donc appartenir, selon la norme NFP 18-101, Ă lâune des cinq familles suivantes :
- les fines avec un diamĂštre compris entre 0 et 0,08 mm ;
- les sables avec un diamĂštre compris entre 0 et 6,3 mm ;
- les gravillons avec un diamĂštre compris entre 2 et 31,5 mm ;
- les cailloux avec un diamĂštre compris en 20 et 80 mm ;
- les graves avec un diamĂštre compris en 6,3 et 80 mm.
Les granulats sont les principaux composants du bĂ©ton (70 % en poids). Les performances mĂ©caniques des granulats vont donc conditionner la rĂ©sistance mĂ©canique du bĂ©ton et leurs caractĂ©ristiques gĂ©omĂ©triques et esthĂ©tiques, en particulier, lâaspect des parements des ouvrages. Le choix des caractĂ©ristiques des granulats (roulĂ©s ou concassĂ©s, teintes, dimensions) est dĂ©terminĂ© par les contraintes mĂ©caniques, physico-chimiques et esthĂ©tiques du projet Ă rĂ©aliser et de mise en Ćuvre du bĂ©ton (critĂšre de maniabilitĂ©, enrobage)[1].
Différents types de granulats
Les granulats utilisĂ©s pour le bĂ©ton sont soit d'origine naturelle, soit artificiels. Leur taille variable dĂ©terminera l'utilisation du bĂ©ton (par exemple : les gros granulats pour le gros Ćuvre). La rĂ©sistance du bĂ©ton augmente avec la variĂ©tĂ© des calibres mĂ©langĂ©s.
Dans des rĂ©gions de certains pays d'Asie du Sud-Est (Inde, BangladeshâŠ) particuliĂšrement pauvres en roches, il est courant d'utiliser comme granulats des briques cuites, concassĂ©es et calibrĂ©es. Le concassage et le calibrage sont gĂ©nĂ©ralement effectuĂ©s sur place.
Parmi les granulats naturels, les plus utilisés pour le béton proviennent de roches sédimentaires siliceuses ou calcaires, de roches métamorphiques telles que les quartzites, ou de roches éruptives telles que les basaltes, les granites, les porphyres.
IndĂ©pendamment de leur origine minĂ©ralogique, on classe les granulats en deux catĂ©gories qui doivent ĂȘtre conformes Ă la norme NF EN 12620 et la NF P 18-545 (Granulats - ĂlĂ©ments de dĂ©finition, conformitĂ© et codification) :
- Les granulats alluvionnaires, dits roulés, dont la forme a été acquise par l'érosion. Ces granulats sont lavés pour éliminer les particules argileuses, nuisibles à la résistance du béton et criblés pour obtenir différentes classes de dimension. Bien qu'on puisse trouver différentes roches selon la région d'origine, les granulats utilisés pour le béton sont le plus souvent siliceux, calcaires ou silico-calcaires ;
- Les granulats de carriĂšre sont obtenus par abattage et concassage, ce qui leur donne des formes angulaires. Une phase de prĂ©-criblage est indispensable Ă l'obtention de granulats propres. DiffĂ©rentes phases de concassage aboutissent Ă l'obtention des classes granulaires souhaitĂ©es. Les granulats concassĂ©s prĂ©sentent des caractĂ©ristiques qui dĂ©pendent d'un grand nombre de paramĂštres : origine de la roche, rĂ©gularitĂ© du banc, degrĂ© de concassage⊠La sĂ©lection de ce type de granulats devra donc ĂȘtre faite avec soin et aprĂšs accord sur un Ă©chantillon.
Les granulats allĂ©gĂ©s par expansion ou frittage, trĂšs utilisĂ©s dans de nombreux pays comme la Russie ou les Ătats-Unis, n'ont pas eu en France le mĂȘme dĂ©veloppement, bien qu'ils aient des caractĂ©ristiques de rĂ©sistance, d'isolation et de poids trĂšs intĂ©ressantes. Les plus usuels sont l'argile ou le schiste expansĂ© (norme NF P 18-309) et le laitier expansĂ© (NF P 18-307). D'une masse volumique variable entre 400 et 800 kg/m3 selon le type et la granularitĂ©, ils permettent de rĂ©aliser aussi bien des bĂ©tons de structure que des bĂ©tons prĂ©sentant une bonne isolation thermique. Les gains de poids sont intĂ©ressants puisque les bĂ©tons rĂ©alisĂ©s ont une masse volumique comprise entre 1 200 et 2 000 kg/m3.
Les granulats trĂšs lĂ©gers sont d'origine vĂ©gĂ©tale et organique plutĂŽt que minĂ©rale (bois, polystyrĂšne expansĂ©). TrĂšs lĂ©gers â 20 Ă 100 kg/m3 â ils permettent de rĂ©aliser des bĂ©tons de masse volumique comprise entre 300 et 600 kg/m3. On voit donc leur intĂ©rĂȘt pour les bĂ©tons d'isolation, mais Ă©galement pour la rĂ©alisation d'Ă©lĂ©ments lĂ©gers : blocs coffrants, blocs de remplissage, dalles ou rechargements sur planchers peu rĂ©sistants. Les bĂ©tons cellulaires (bĂ©tons trĂšs lĂ©gers) dont les masses volumiques sont infĂ©rieures Ă 500 kg/m3. Ils sont utilisĂ©s dans le bĂątiment, pour rĂ©pondre aux exigences d'isolation. Lors de sa rĂ©alisation, des produits moussants lui sont incorporĂ©es crĂ©ant des porositĂ©s dans le bĂ©ton. Les bĂ©tons de fibres, plus rĂ©cents, correspondent Ă des usages trĂšs variĂ©s : dallages, Ă©lĂ©ments dĂ©coratifs, mobilier urbain.
Béton et recyclage
Le béton est un matériau qui permet le réemploi de certains déchets industriels ou domestiques :
- fumée de silice : résidus de filtration des fumées de fours à arc ;
- laitier de haut-fourneau : résidus de fabrication de la fonte et de l'acier servant à la fabrication de certains ciments ;
- sulfonates : composés chimiques issus de l'industrie papetiÚre utilisés sous forme de plastifiant ;
- polyphénols : composés chimiques issus de l'industrie pétroliÚre utilisés sous forme de plastifiants ;
- farines animales : produit issus du traitement des carcasses animales utilisés par brûlage pour la fabrication du ciment ;
- cendres : utilisation des résidus de brûlage des centrales à charbons sous forme de filer.
Dans le secteur du bĂątiment et des travaux publics (BTP), les gravats de bĂ©ton provenant des chantiers de dĂ©molition/dĂ©construction sont thĂ©oriquement eux-mĂȘmes recyclables. Les armatures envoyĂ©es Ă la ferraille sont refondues en four Ă©lectrique, tandis que les granulats recyclĂ©s peuvent remplacer en partie les granulats naturels. En France (pour 2015), la production annuelle de dĂ©chets du BTP Ă©tait d'environ 260 millions de t/an dont 20 millions de t/an de dĂ©chets de bĂ©ton (dont 80 % finissent en fond de couche routiĂšre). Le projet RecybĂ©ton[2] lancĂ© en 2012 avec un soutien financier (5 millions d'euros pour 2012-2016) de l'Ademe, du ministĂšre de l'Ăcologie et de l'ANR, parallĂšlement Ă Ecoreb (Eco-construction par le recyclage du bĂ©ton) regroupe 47 partenaires souhaitant promouvoir le recyclage du bĂ©ton (« y compris la fraction fine »[2]) en granulats, via des Ă©tudes de caractĂ©risations, l'amĂ©lioration des procĂ©dĂ©s de sĂ©paration mĂ©caniques et optiques, la construction de plateformes de tri « au plus prĂšs des sites de production, tels les cimenteries ou les producteurs de granulats », une adaptation de la lĂ©gislation qui en 2014 via la norme NF EN 206-1/CN (publiĂ©e en dĂ©cembre 2014) impose un maximum de 20 % de substitution de gravillons naturels par des gravillons recyclĂ©s dans du bĂ©ton[3]. Le projet RecybĂ©ton sâappuyait sur trois chantiers expĂ©rimentaux (un parking fait avec 100 % de bĂ©ton recyclĂ©, une passerelle ferroviaire faite avec 20 % de granulats recyclĂ©s et un bĂątiment d'archive dont le bĂ©ton contient 30 % de sable recyclĂ© et de 50 % de gravillon recyclĂ©). Une des conditions Ă respecter est de bien Ă©liminer les restes de plĂątre ou d'autres substances susceptibles d'affecter la qualitĂ© du futur bĂ©ton. Les ouvrages en bĂ©ton peuvent aussi ĂȘtre « Ă©coconçus » de maniĂšre Ă faciliter le recyclage futur du bĂ©ton et diminuer sa forte empreinte carbone. Selon le groupe Lafarge, la fabrication de ciment « reprĂ©sente quelques [sic] 5 % des Ă©missions mondiales de CO2. 60 % proviennent du processus de « dĂ©carbonatation » et 40 % de la combustion de combustibles fossiles »[4].
Granulométrie
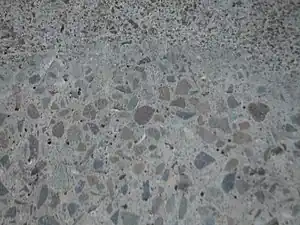
Si un bĂ©ton classique est constituĂ© d'Ă©lĂ©ments de granulomĂ©trie dĂ©croissante, en commençant par les granulats (NF EN 12620 - spĂ©cification pour les granulats destinĂ©s Ă ĂȘtre incorporĂ©s dans les bĂ©tons), le spectre granulomĂ©trique se poursuit avec la poudre de ciment puis parfois avec un matĂ©riau de granulomĂ©trie encore plus fin comme une fumĂ©e de silice (rĂ©cupĂ©rĂ©e au niveau des filtres Ă©lectrostatiques dans l'industrie de l'acier). L'obtention d'un spectre granulomĂ©trique continu et Ă©tendu vers les faibles granulomĂ©tries permet d'amĂ©liorer la compacitĂ©, donc les performances mĂ©caniques. L'eau a un double rĂŽle d'hydratation de la poudre de ciment et de facilitation de la mise en Ćuvre (ouvrabilitĂ©). Un bĂ©ton contient donc une part importante d'eau libre, ce qui conduit Ă une utilisation non optimale de la poudre de ciment. En ajoutant un plastifiant (appelĂ© aussi rĂ©ducteur d'eau), la quantitĂ© d'eau utilisĂ©e dĂ©croĂźt et les performances mĂ©caniques du matĂ©riau sont amĂ©liorĂ©es (BHP : bĂ©ton hautes performances).
Les résistances mécaniques en compression obtenues classiquement sur éprouvettes cylindriques normalisées, sont de l'ordre de :
- BFC : bétonnage fabriqué sur chantier : 25 à 35 MPa (méga Pascal), peut parfois atteindre 50 MPa ;
- BPE : bĂ©ton prĂȘt Ă l'emploi, bĂ©tonnage soignĂ© en usine (prĂ©fabrication) : 16 Ă 60 MPa ;
- BHP : béton hautes performances : jusqu'à 80 MPa ;
- BUHP : béton ultra hautes performances, en laboratoire : 120 MPa.
- BFUHP : béton fibré à ultra hautes performances : supérieur à 150 MPa.
La rĂ©sistance en traction est moindre avec des valeurs de l'ordre 2,1 Ă 2,7 MPa pour un bĂ©ton de type BFC. La conductivitĂ© thermique couramment utilisĂ©e est de 1,75 W·mâ1·Kâ1, Ă mi-chemin entre les matĂ©riaux mĂ©talliques et le bois.
Les adjuvants
Un adjuvant est un produit incorporĂ© au moment du malaxage du bĂ©ton, Ă une dose infĂ©rieure ou Ă©gale Ă 5 % en masse de la teneur en ciment du bĂ©ton pour modifier les propriĂ©tĂ©s du mĂ©lange Ă lâĂ©tat frais et/ou durci.
En avril 1998, lâAssociation Française de Normalisation (AFNOR) publie la norme NF EN 934-2 qui dĂ©finit les catĂ©gories gĂ©nĂ©rales propres aux adjuvants. Ces catĂ©gories sont au nombre de 3 selon leurs caractĂ©ristiques gĂ©nĂ©rales :
- la prise et le durcissement (accélérateurs de prise, accélérateurs de durcissement, retardateurs de prise) ;
- lâouvrabilitĂ© (plastifiants, superplastifiants) ;
- certaines propriĂ©tĂ©s particuliĂšres (entraineurs dâair, gĂ©nĂ©rateurs de gaz, hydrofuges de masse).
Lâajout dâun adjuvant dĂ©pend donc des caractĂ©ristiques que lâon souhaite obtenir dans le bĂ©ton utilisĂ©.
La rĂ©action chimique qui permet au bĂ©ton de ciment de « faire prise » est assez lente : au bout de sept jours, la rĂ©sistance mĂ©canique Ă la compression atteint Ă peine 75 % de la rĂ©sistance finale. La vitesse de durcissement du bĂ©ton peut cependant ĂȘtre affectĂ©e par la nature du ciment utilisĂ©, par la tempĂ©rature du matĂ©riau lors de son durcissement, par la quantitĂ© d'eau utilisĂ©e, par la finesse de la mouture du ciment, ou par la prĂ©sence de dĂ©chets organiques. La valeur prise comme rĂ©fĂ©rence dans les calculs de rĂ©sistance est celle obtenue Ă 28 jours, Ă©quivalent Ă 80 % de la rĂ©sistance finale. Ăgalement, en prĂ©sence d'eau, la rĂ©sistance continuera d'augmenter, trĂšs lĂ©gĂšrement mĂȘme aprĂšs 28 jours.
Il est possible de modifier la vitesse de prise en incorporant au bĂ©ton frais des adjuvants ou des additifs, ou en utilisant un ciment prompt ou Ă prise rapide. D'autres types d'adjuvants permettent de modifier certaines propriĂ©tĂ©s physico-chimiques des bĂ©tons. Par exemple, la fluiditĂ© du bĂ©ton peut ĂȘtre augmentĂ©e pour faciliter sa mise en Ćuvre en utilisant des « plastifiants », le rendre hydrofuge par l'adjonction d'un liquide hydrofuge ou d'une rĂ©sine polymĂšre, ou maĂźtriser la quantitĂ© d'air incluse avec un « entraĂźneur d'air ». DiffĂ©rents modĂšles (thĂ©orie de la percolation, modĂšle des empilements granulaires pour les bĂ©tons de haute performance) permettent d'expliquer les rĂ©actions physiques et chimiques de la « prise ».
La rĂ©sistance elle-mĂȘme du bĂ©ton pourra ĂȘtre amĂ©liorĂ©e par l'usage d'adjuvant de type super plastifiant qui par amĂ©lioration de l'ouvrabilitĂ© du bĂ©ton permet de rĂ©duire la quantitĂ© d'eau de gĂąchage et donc la porositĂ© rĂ©sultante et par dĂ©floculation du ciment amĂ©liore la rĂ©action de prise. L'usage de produits de type fumĂ©e de silice remplissant une double fonction de filer et de liant permet Ă©galement d'augmenter la compacitĂ© et la rĂ©sistance.
Eau de gĂąchage
Importance du rapport eau/ciment
Les dosages de l'eau et du ciment sont deux facteurs importants. En effet, l'ouvrabilité et la résistance sont grandement affectés par ces deux paramÚtres. Plus le rapport eau/ciment est grand, plus l'ouvrabilité sera grande. En effet, plus il y a d'eau, plus le béton aura tendance à remplir aisément les formes. Le rapport des masses E/C « moyen » est normalement fixé à 0,55. C'est ce rapport qui est le plus souvent utilisé, car le béton obtenu dispose d'une assez bonne ouvrabilité, tout en ayant une bonne résistance.
Le phénomÚne de ressuage est dû à un rapport eau sur ciment trop élevé. Il se manifeste par l'apparition d'une flaque au-dessus du béton frais. Au niveau des granulats, on observe la présence d'eau à l'interface entre les granulats et la pùte de ciment. La résistance en est réduite, car l'eau s'évapore et il y a des vides entre le granulat et la pùte.
Formulation
Le choix des proportions de chacun des constituants d'un bĂ©ton afin d'obtenir les propriĂ©tĂ©s mĂ©caniques et de mise en Ćuvre souhaitĂ©es s'appelle la formulation. Plusieurs mĂ©thodes de formulations existent, dont notamment :
- la méthode Baron ;
- la méthode Bolomey ;
- la méthode de Féret ;
- la méthode de Faury ;
- la méthode Dreux-Gorisse.
La formulation d'un bĂ©ton doit intĂ©grer avant tout les exigences de la norme NF EN 206/CN, laquelle, en fonction de l'environnement dans lequel sera mis en place le bĂ©ton, sera plus ou moins contraignante vis-Ă -vis de la quantitĂ© minimale de ciment Ă insĂ©rer dans la formule ainsi que la quantitĂ© d'eau maximum tolĂ©rĂ©e dans la formule. De mĂȘme, Ă chaque environnement donnĂ©, une rĂ©sistance garantie Ă 28 jours sur Ă©prouvettes sera exigĂ©e aux producteurs, pouvant justifier des dosages de ciments plus ou moins supĂ©rieurs Ă la recommandation de la norme, et basĂ©e sur l'expĂ©rience propre Ă chaque entreprise, laquelle Ă©tant dĂ©pendante de ses matiĂšres premiĂšres dont la masse volumique peut varier, notamment celle des granulats. D'autres exigences de la norme NF EN 206/CN imposent l'emploi de ciment particuliers en raison de milieux plus ou moins agressifs, ainsi que l'addition d'adjuvants confĂ©rant des propriĂ©tĂ©s diffĂ©rentes Ă la pĂąte de ciment que ce soit le dĂ©lai de mise en Ćuvre, la plasticitĂ©, la quantitĂ© d'air occlus, etc.
Classification
Le bĂ©ton utilisĂ© dans le bĂątiment, ainsi que dans les travaux publics comprend plusieurs catĂ©gories. En gĂ©nĂ©ral le bĂ©ton peut ĂȘtre classĂ© en trois groupes (norme NF EN 206/CN articles 3.1.4.1 Ă 3.1.4.3), selon sa masse volumique Ï :
- bĂ©ton lĂ©ger : Ï entre 800 et 2 000 kg/m3 ;
- bĂ©ton normal : Ï entre 2 000 et 2 600 kg/m3 ;
- bĂ©ton lourd : Ï > 2 600 kg/m3 ;
Les bĂ©tons courants peuvent aussi ĂȘtre classĂ©s en fonction de la nature de leurs liants :
- béton de ciment ;
- béton asphalte.
Lorsque des fibres (métalliques, synthétiques ou minérales) sont ajoutées, on distingue : les bétons renforcés de fibre (BRF) qui sont des bétons « classiques » qui contiennent des macrofibres (diamÚtre ~1 mm) dans proportion volumique allant de 0,5 % à 2 % ; et les bétons fibrés à ultra hautes performances (BFUHP). Ce sont des bétons (BUHP) qui contiennent des microfibres (diamÚtre > 50 ”m), ou un mélange de macrofibres et de microfibres. Utilisés depuis le milieu des années 1990 dans le génie civil et parfois la réhabilitation d'ouvrages anciens, en milieu littoral notamment[5].
Le bĂ©ton peut varier en fonction de la nature des granulats, des adjuvants, des colorants, des traitements de surface et peut ainsi sâadapter aux exigences de chaque rĂ©alisation, par ses performances et par son aspect.
- Les bĂ©tons courants sont les plus utilisĂ©s, aussi bien dans le bĂątiment qu'en travaux publics. Ils prĂ©sentent une masse volumique de 2 300 kg/m3 environ. Ils peuvent ĂȘtre armĂ©s ou non, et lorsqu'ils sont trĂšs sollicitĂ©s en flexion, ĂȘtre prĂ©contraints.
- Les bétons lourds, dont les masses volumiques peuvent atteindre 6 000 kg/m3 sont utilisés dans le domaine du nucléaire pour réaliser les blindages des protections biologiques contre les rayons gamma de haute énergie et trÚs pénétrants.
- Les bĂ©tons de granulats lĂ©gers, dont la rĂ©sistance peut ĂȘtre Ă©levĂ©e, sont employĂ©s dans le bĂątiment, pour les plates-formes offshore ou les ponts.
Ătude de la composition
Il nâexiste pas de mĂ©thode de composition du bĂ©ton qui soit universellement reconnue comme Ă©tant la meilleure. La composition du bĂ©ton est toujours le rĂ©sultat dâun compromis entre diverses exigences souvent contradictoires. De nombreuses mĂ©thodes de composition du bĂ©ton plus ou moins compliquĂ©es et ingĂ©nieuses ont Ă©tĂ© Ă©laborĂ©es. Une Ă©tude de composition de bĂ©ton doit toujours ĂȘtre contrĂŽlĂ©e expĂ©rimentalement ; une Ă©tude effectuĂ©e en laboratoire doit gĂ©nĂ©ralement ĂȘtre adaptĂ©e ultĂ©rieurement aux conditions rĂ©elles du chantier.
Une mĂ©thode de composition du bĂ©ton pourra ĂȘtre considĂ©rĂ©e comme satisfaisante si elle permet de rĂ©aliser un bĂ©ton rĂ©pondant aux exigences suivantes : Le bĂ©ton doit prĂ©senter, aprĂšs durcissement, une certaine rĂ©sistance Ă la compression. Le bĂ©ton frais doit pouvoir facilement ĂȘtre mis en Ćuvre avec les moyens et mĂ©thodes utilisĂ©s sur le chantier. Le bĂ©ton doit prĂ©senter un faible retrait (source de fissurations internes et externes : phĂ©nomĂšne de « faĂŻençage ») et un fluage peu important. Le coĂ»t du bĂ©ton doit rester le plus bas possible. Dans le passĂ©, pour la composition du bĂ©ton, on prescrivait des proportions thĂ©oriques de ciment, dâagrĂ©gat fin et dâagrĂ©gat grossier. Mais lâĂ©laboration des ciments ayant fait des progrĂšs considĂ©rables, de nombreux chercheurs ont exprimĂ© des formules en rapport avec les qualitĂ©s recherchĂ©es :
- minimum de vides internes, déterminant une résistance élevée ;
- bonne étanchéité améliorant la durabilité ;
- résistance chimique ;
- rĂ©sistance aux agents extĂ©rieurs tels que le gel, lâabrasion, la dessiccation.
Sur les petits chantiers, oĂč le bĂ©ton est fabriquĂ© artisanalement, le dosage « standard » est de 350 kg de ciment par mÂł de bĂ©ton. La composition de 1 m3 de bĂ©ton « standard » est donc de :
- 350 kg de ciment ;
- 680 kg de sable (granulométrie de 1 à 5 mm) ;
- 1 175 kg de gravier (granulométrie de 6 à 15 mm).
soit des proportions proches de 1-2-3, c'est-à -dire deux volumes de sable (350 à 2 kg) et trois volumes de graviers (350 à 3 kg) pour un volume de ciment. C'est la fameuse rÚgle du 1-2-3 qui va de la granulométrie la plus fine (le ciment) à la plus grosse (le gravier).
Quand c'est un « paveur », (mĂ©lange dĂ©jĂ fait de sable et de gravier), qui est utilisĂ©, la formule 1,2,3 devient alors une pelle de ciment pour 5 pelles de paveur. La quantitĂ© dâeau de gĂąchage varie trop souvent au grĂ© du savoir-faire du maçon, la nature de ciment, lâhumiditĂ© du granulat passant aprĂšs la consistance du bĂ©ton Ă obtenir. Le bĂ©ton peut varier en fonction de la nature des granulats, des adjuvants, des colorants, des traitements de surface, et peut ainsi sâadapter aux exigences de chaque rĂ©alisation, par ses performances et par son aspect. La composition dâun bĂ©ton et le dosage de ses constituants sont fortement influencĂ©s par lâemploi auquel est destinĂ© le bĂ©ton et par les moyens de mise en Ćuvre utilisĂ©s.
Essai de gĂąchage
BĂ©ton frais : mesure Î (contrĂŽle des dosages effectifs) mesure plasticitĂ© (contrĂŽle de la consistance) mesure teneur en air (contrĂŽle des vides). Fabrication Ă©prouvette (contrĂŽle de ÎČ moyen). BĂ©ton durci : mesure Î, mesure ÎČ cube, Ă©volution sclĂ©romĂštre, Ă©volution essai gel, permĂ©abilitĂ©, essais spĂ©ciauxâŠ
Correction des dosages ou de la formulation
En fonction des observations, des mesures faites lors de lâessai de gĂąchage et des rĂ©sistances mĂ©caniques obtenues, il sera nĂ©cessaire dâeffectuer des corrections.
- Consistance : Lors de lâessai de gĂąchage, il est recommandĂ© de ne pas ajouter tout de suite la quantitĂ© dâeau totale E prĂ©vue, mais dâajouter seulement 95 % de E, de mesurer la consistance, puis dâajouter de lâeau jusquâĂ obtention de la consistance prescrite.
- Dosage en ciment : Si le dosage en ciment effectivement rĂ©alisĂ© est incorrect, on devra le corriger. Sâil faut rajouter (ou enlever) un poids ÎC de ciment pour obtenir le dosage dĂ©sirĂ©, on devra enlever (ou rajouter) un volume absolu Ă©quivalent de sable, soit un poids ÎC Ă©gal Ă : Si ÎC est important, il faudra aussi corriger la quantitĂ© dâeau.
- RĂ©sistances mĂ©caniques : Si les rĂ©sistances mĂ©caniques sont insuffisantes, il faudra avoir recours Ă lâune ou Ă plusieurs des possibilitĂ©s suivantes :
- augmenter le dosage en ciment (au-delĂ de 400 kg/m3, une augmentation de dosage en ciment nâa plus quâune trĂšs faible influence sur lâaccroissement de rĂ©sistance) ;
- diminuer le dosage en eau sans changer la granulométrie des granulats ;
- rĂ©duire la quantitĂ© dâeau et corriger la granulomĂ©trie des granulats ;
- utiliser un autre type de granulats ;
- utiliser un adjuvant et rĂ©duire la quantitĂ© dâeau ;
- utiliser un ciment Ă durcissement plus rapide.
Il faut dans tous les cas veiller Ă ce que la consistance du bĂ©ton permette une mise en Ćuvre correcte.
Utilisations du béton de ciment
Bloc de béton aggloméré
Le bloc de béton aggloméré a été inventé par François Coignet. Sa premiÚre utilisation a été faite pour la maison de François Coignet en 1853. L'église Sainte-Marguerite du Vésinet, réalisée en 1855 par l'architecte Louis-Auguste Boileau suivant le procédé Coignet de construction de béton aggloméré imitant la pierre, fut le premier bùtiment public non industriel réalisé en béton en France. Cette église fut trÚs critiquée lors de sa réalisation en raison de sa morphologie mais aussi du procédé Coignet qui a provoqué trÚs rapidement des marbrures noires sur les murs (en raison de présence de mùchefer dans le béton). C'est un matériau imitant la pierre.
Béton armé
.jpg.webp)
Le ciment armé a été inventé par Joseph Monier qui en a déposé les brevets dÚs 1870. On peut citer aussi les barques de Lambot (1848) en ciment armé de 5 à 6 cm d'épaisseur et dont deux exemplaires existent toujours. On se reportera pour plus de précision au livre Joseph Monier et la naissance du ciment armé paru aux éditions du Linteau (Paris, 2001). C'est ensuite en 1886 que François Hennebique va étudier et améliorer l'invention de Joseph Monier pour ensuite l'utiliser pour la construction en 1899 du premier pont civil en béton armé de France, le pont Camille-de-Hogues à Chùtellerault.
De façon intrinsĂšque, le bĂ©ton de ciment possĂšde une bonne rĂ©sistance Ă la compression, mais une faible rĂ©sistance Ă la traction. Aussi est-il nĂ©cessaire, lorsqu'un ouvrage en bĂ©ton est prĂ©vu pour subir des sollicitations en traction ou en flexion (par exemple un plancher, un pont, une poutreâŠ), d'y incorporer des armatures en acier destinĂ©es Ă s'opposer aux efforts de traction et Ă les reprendre. Les armatures mises en Ćuvre peuvent ĂȘtre soit en acier doux (l'acier doux est gĂ©nĂ©ralement lisse, il n'est plus guĂšre utilisĂ© aujourd'hui en bĂ©ton armĂ© que dans la confection des boucles de manutention prĂ©scellĂ©es pour son aptitude aux pliages-dĂ©pliages successifs sans perte de rĂ©sistance) soit en acier haute-adhĂ©rence (aciers HA anciennement dĂ©nommĂ©s TOR) dont les caractĂ©ristiques mĂ©caniques sont de l'ordre du double de celles des aciers doux.
Béton précontraint
Le béton possÚde des propriétés mécaniques intéressantes en compression alors que la résistance en traction est limitée (environ 1/10e de la résistance à la compression). Lorsque les sollicitations deviennent trÚs importantes, l'alourdissement de la section de béton armé devient prohibitif (en général au-delà de 25 m de portée pour une poutre). C'est ainsi qu'il devient intéressant de créer une compression initiale suffisante pour que le béton reste entiÚrement comprimé sous les sollicitations ; ainsi toute la section du béton participe à la résistance : c'est le principe du béton « précontraint ».
Le bĂ©ton « prĂ©contraint » est une technique mise au point par EugĂšne Freyssinet en 1928 et testĂ©e sur des poteaux prĂ©fabriquĂ©s destinĂ©s au support de cĂąbles Ă©lectriques. UltĂ©rieurement, le champ d'application du bĂ©ton prĂ©contraint s'est considĂ©rablement Ă©largi. Le bĂ©ton prĂ©contraint convient aussi bien Ă des petites dalles prĂ©fabriquĂ©es qu'Ă des ouvrages de trĂšs grandes portĂ©es (100 mĂštres ou plus). Lorsque le bĂ©ton prĂ©contraint subit des sollicitations de signe opposĂ© Ă la prĂ©contrainte, le bĂ©ton se dĂ©comprime ; les variations de tension dans les armatures sont quasiment nĂ©gligeables compte tenu de la forte inertie de la section de bĂ©ton rapportĂ©e Ă celles des aciers. En pratique, les rĂšglements modernes (BPEL, Eurocodes) autorisent de lĂ©gĂšres dĂ©compressions du bĂ©ton sensiblement dans la limite de sa rĂ©sistance en traction. Ceci pose problĂšme dans certains domaines comme celui des enceintes primaires en bĂ©ton prĂ©contraint des rĂ©acteurs nuclĂ©aires par exemple, oĂč des dĂ©formations diffĂ©rĂ©es anormales du bĂ©ton ont Ă©tĂ© constatĂ©es Ă partir des annĂ©es 1980-1990 ; anomalies « que les modĂšles de calcul rĂ©glementaires ne prenaient pas en compte d'une façon satisfaisante » ont Ă©tĂ© constatĂ©es[6]. Ces anomalies ont, en France, justifiĂ© une vaste Ă©tude sur ces bĂ©tons par EDF, avec des modĂ©lisations du « comportement rĂ©el en fluage des enceintes dĂ©jĂ construites »[6].
Les aciers utilisés pour la mise en compression du béton sont des cùbles (à torons) ou des barres de trÚs haute résistance à la rupture. Selon que cette tension appliquée aux armatures est effectuée avant la prise complÚte du béton ou postérieurement à celle-ci, on distingue la précontrainte par « pré-tension » et la précontrainte par « post-tension ».
- Dans la « pré-tension », le plus souvent utilisée en préfabrication, les armatures (souvent des cùbles) sont mises en tension avant la prise du béton. Elles sont ensuite relùchées, mettant ainsi le béton en compression par simple effet d'adhérence, le diamÚtre des cùbles augmentant légÚrement lorsque la tension appliquée est relùchée (cfr. coefficient de Poisson). Elle est trÚs souvent réalisée en usine, avec des machines spécifiques. Les prédalles ou les poutrelles préfabriquées sont réalisées avec cette technique. Elle ne permet pas d'atteindre des valeurs de précontrainte aussi élevées qu'en post-tension.
- La « post-tension » consiste Ă disposer les cĂąbles de prĂ©contrainte dans des gaines incorporĂ©es au bĂ©ton. AprĂšs la prise du bĂ©ton, les cĂąbles sont tendus au moyen de vĂ©rins de maniĂšre Ă comprimer l'ouvrage au repos. Cette technique, relativement complexe, est gĂ©nĂ©ralement rĂ©servĂ©e aux grands ouvrages (ponts) puisqu'elle nĂ©cessite la mise en Ćuvre d'encombrantes « piĂšces d'about » (dispositifs mis en place de part et d'autre de l'ouvrage et permettant la mise en tension des cĂąbles).
L'équilibre des efforts est obtenu par un tracé judicieux des cùbles de précontrainte sur l'ensemble de la poutre ou de l'élément concerné de telle sorte que les sections de béton restent (quasiment) entiÚrement comprimées sous l'effet des différentes actions. Par exemple, au milieu d'une poutre isostatique, à vide, la précontrainte sera conçue de telle sorte que la contrainte du béton soit maximale en fibre inférieure et minimale en fibre supérieure (dans ces conditions, une contre-flÚche peut apparaßtre à vide). Une fois la poutre soumise à sa charge maximale, la précontrainte en fibre inférieure sera presque annulée par la tension de charge, alors que dans la partie supérieure la compression sera largement plus importante que dans une poutre en béton armé classique.
Autres techniques de renforcement
On peut amĂ©liorer la rĂ©sistance mĂ©canique (post-fissuration) du bĂ©ton de diffĂ©rentes maniĂšres, notamment en y incorporant des fibres (0,5 Ă 2 % en volume). L'incorporation de celles-ci dans le bĂ©ton rend ce dernier davantage ductile (moins fragile). DiffĂ©rents types de fibre (mĂ©talliques, en polypropylĂšne, en verreâŠ) peuvent ĂȘtre utilisĂ©s avec des propriĂ©tĂ©s spĂ©cifiques. C'est surtout le rapport entre la longueur et le diamĂštre des fibres (Ă©lancement) qui aura une influence sur les performances finales du bĂ©ton fibrĂ©. On obtient ainsi un « bĂ©ton fibrĂ© », souvent mis en Ćuvre par projection (tunnels) ou couramment utilisĂ© pour les dallages industriels par exemple.
Pour les applications architecturales ou quand la corrosion des armatures est potentiellement dangereuse, les ciments Ă renfort fibre de verre, dits « CCV » (composites ciment-verre), sont utilisĂ©s depuis la fin des annĂ©es 1970. Ils allient une matrice riche en ciment et des fibres de verre alcali rĂ©sistantes (3 Ă 6 % en masse totale du mĂ©lange humide) et peuvent ĂȘtre prĂ©fabriquĂ©s en produits minces, donc lĂ©gers[7] - [8].
Avantages et inconvénients du béton armé de fibres
Fibres métalliques :
+ : La ductilité, augmentant la résistance aux chocs et à la fatigue, diminution des fissures de retrait.
- : Demande plus de granulats fins et donc plus dâeau de gĂąchage (sauf en cas d'usage d'un super-plastifiant), les fibres qui apparaissent en surface peuvent rouiller ou endommager les pneus, utilisation proscrite pour des bĂ©ton apparents (fibres visibles).
Fibres synthétiques :
+ : Diminution des fissures de retrait, diminution du retrait plastique, diminution de la ségrégation.
- : Diminution de la plasticité du mélange (idem que pour fibres métalliques), utilisation proscrite pour des béton apparents (fibres visibles).
Autres utilisations
Lâinvention du premier « bateau-ciment » par le Français Joseph Lambot remonte Ă 1848. Dans les annĂ©es 1970, aux Ătats-Unis, a lieu la premiĂšre compĂ©tition de canoĂ«s en bĂ©ton. Depuis, prĂšs de 200 universitĂ©s amĂ©ricaines participent chaque annĂ©e Ă lâĂ©vĂ©nement, et ce type de compĂ©tition sâest exportĂ© dans de nombreux pays tels que la France depuis 2000, le Canada, lâAllemagne, le Japon ou encore lâAfrique du Sud.
CaractĂ©ristiques dâun bĂ©ton colloĂŻdal
Le bĂ©ton colloĂŻdal a Ă©tĂ© conçu pour ĂȘtre dĂ©versĂ© sous eau avec des procĂ©dĂ©s conventionnels. Les particules de ciment adhĂ©rent fortement aux granulats: on dit que ce bĂ©ton « colle ». Le bĂ©ton colloĂŻdal frais a une plasticitĂ© diffĂ©rente de celle dâun bĂ©ton ordinaire: il ne se dĂ©sagrĂšge pas et nâest pas dĂ©lavĂ© lors de sa mise en place sous eau.
Pratique industrielle
Fabrication
Le bĂ©ton peut ĂȘtre confectionnĂ© dans une bĂ©tonniĂšre mobile (Ă©lectrique ou thermique) pour les petites quantitĂ©s. Mais il est aussi fabriquĂ© dans des centrales Ă bĂ©ton ou dans des usines de prĂ©fabrication qui utilisent directement le matĂ©riau produit en fabriquant des Ă©lĂ©ments en bĂ©ton. Si nous sommes en prĂ©sence dâun chantier qui demande de grandes quantitĂ©s, une centrale mobile est parfois installĂ©e directement sur le chantier; ce qui permet dâaugmenter le dĂ©bit de livraison au chantier. De plus, cela nĂ©cessite moins de camions malaxeurs (couramment appelĂ©s camions-toupie) pour le transport du bĂ©ton Ă©tant donnĂ© que la distance parcourue est plus courte. Cependant, elle nĂ©cessite une grue sur le chantier.
Il existe deux types de mĂ©thodes pour fabriquer le bĂ©ton prĂȘt Ă l'emploi (BPE) : (Dry-Batch) et le (PrĂ©-Mix). Le Dry-batch consiste Ă mĂ©langer les agrĂ©gats et adjuvants chargĂ©s par convoyeurs directement dans le camion-toupie. Cette mĂ©thode nĂ©cessite que la bĂ©tonniĂšre malaxe pendant 5 minutes. Le PrĂ©-Mix consiste Ă mĂ©langer les agrĂ©gats et adjuvants dans un malaxeur dans lâusine pour ensuite le dĂ©verser dans le camion-toupie qui est prĂȘte Ă faire sa livraison. Attention, il faut livrer le bĂ©ton sur le chantier avant qu'il n'ait commencĂ© Ă prendre.
Caractéristiques du béton léger.
Masse volumique < Ă 2 000 kg/m3 ; Granulats Ă structure poreuse ; RĂ©sistance au feu ; Faible coefficient de dilatation thermique (par rapport au bĂ©ton normal) ; Module dâĂ©lasticitĂ© plus faible (par rapport au bĂ©ton normal)
Acheminement
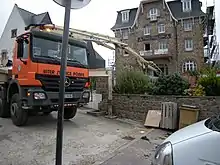
Le mode, la durĂ©e et les conditions de lâacheminement du bĂ©ton sont des Ă©lĂ©ments dĂ©terminants dans sa formulation. Ils ont chacun une influence particuliĂšre sur sa manĆuvrabilitĂ© et sa qualitĂ©. Le bĂ©ton se transporte soit par des moyens manuels (seau, brouetteâŠ), soit, pour de grandes quantitĂ©s, par des moyens mĂ©caniques. Dans ce cas, il est gĂ©nĂ©ralement transportĂ© depuis la centrale Ă bĂ©ton par camions malaxeurs appelĂ©s « toupies » dont la capacitĂ© est de 4 m3 maximum pour un camion 4 x 2 ou 4 x 4, 6 m3 maximum pour un camion 6 x 4, 8 m3 maximum pour un camion 8 x 4, et 10 m3 pour un camion semi-remorque 2-essieux de 38 tonnes. Au QuĂ©bec les capacitĂ©s varient : 5 m3 pour un camion 10 roues, 7 Ă 8 m3 pour un camion 12 roues, 10 m3 pour un semi-remorque 2-essieux, et 13 m3 pour un semi-remorque 3-essieux. Une fois sur le chantier, il est transvasĂ© soit dans des bennes Ă bĂ©ton (350 litres Ă 3 m3 et Ă volant ou Ă manchette) qui sont levĂ©es Ă la grue pour ĂȘtre ensuite vidĂ©es dans le coffrage, soit dans une pompe Ă bĂ©ton qui est accouplĂ©e Ă un mĂąt de distribution du bĂ©ton. Certaines toupies sont aussi Ă©quipĂ©es dâun tapis convoyeur (standard, tĂ©lescopique, avec une goulotte rotative en bout de tapis), pouvant aller jusquâĂ 17 m.
Le bĂ©ton peut aussi ĂȘtre projetĂ© Ă lâaide dâun compresseur pneumatique, cette technique est trĂšs utilisĂ©e pour rĂ©parer des ouvrages en bĂ©ton. Le temps de prise du bĂ©ton commence Ă partir du mĂ©lange et malaxage, Ă sa fabrication. Le transport entame donc ce temps et doit ĂȘtre le plus rapide possible pour prĂ©server un maximum de manĆuvrabilitĂ© du bĂ©ton pendant sa mise en place. En gĂ©nĂ©ral la durĂ©e moyenne pour le transport et la mise en Ćuvre du bĂ©ton est de deux heures, au-delĂ de cette durĂ©e, les centrales Ă bĂ©ton ne garantissent plus la qualitĂ© car le bĂ©ton a dĂ©jĂ commencĂ© Ă faire prise. La tempĂ©rature lors du transport est aussi importante. La rapiditĂ© de prise du bĂ©ton est fortement influencĂ©e par la tempĂ©rature ambiante. Lors du malaxage il est ainsi possible dâutiliser de lâeau froide par trĂšs grosses chaleurs et de lâeau chaude par temps froid. Certain camions sont Ă©galement calorifugĂ©s
Mise en Ćuvre
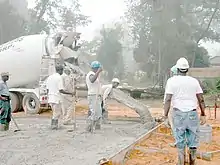
Les propriĂ©tĂ©s rhĂ©ologiques du bĂ©ton Ă lâĂ©tat frais peuvent permettre de distinguer diffĂ©rents types de bĂ©ton :
- bĂ©ton vibrĂ© : nĂ©cessite une vibration (aiguille vibrante, banche vibranteâŠ) pour une bonne mise en place dans le coffrage ; chasser les "vides" et resserrer le matĂ©riau autour des armatures ;
- bĂ©ton compactĂ© au rouleau (BCR) : bĂ©ton trĂšs raide qui est mis en place Ă lâaide dâun rouleau compresseur (utilisĂ© principalement pour les chaussĂ©es, les pistes dâatterrissage ou les barrages[9]) ;
- béton projeté : béton raide mis en place par projection sur une surface verticale ou en surplomb (il existe deux techniques : la projection par voie humide et la projection par voie sÚche) ;
- béton tapissé : concerne tous les types de béton du plus sec au plus fluide qui est acheminé à l'aide d'un tapis convoyeur à béton ;
- bĂ©ton pompĂ© : bĂ©ton fluide qui peut ĂȘtre acheminĂ© sur plusieurs centaines de mĂštres Ă lâaide dâune pompe Ă bĂ©ton ;
- bĂ©ton auto-plaçant et bĂ©ton auto-nivelant : bĂ©tons trĂšs fluides qui ne nĂ©cessitent pas de vibration, la compaction sâeffectuant par le seul effet gravitaire.
De façon courante, le bĂ©ton est coulĂ© dans un coffrage (moule Ă bĂ©ton). Pendant son malaxage, son transport et sa mise en Ćuvre, le bĂ©ton est brassĂ© et de lâair reste emprisonnĂ© en lui. Il faut donc enfoncer des aiguilles vibrantes dans le bĂ©ton pour faire remonter ces bulles dâair en surface. La vibration a aussi pour effet de couler plus facilement le bĂ©ton dans le coffrage, de rĂ©partir ses agrĂ©gats et son liant autour des armatures et sur les faces et les angles qui seront visibles, de le rendre homogĂšne mĂ©caniquement et esthĂ©tiquement. Le bĂ©ton est coulĂ© par couches dâenviron 30 cm pour la simple raison quâun vibreur courant fait 30 cm de haut. Lorsque lâon enfonce un vibreur dans le bĂ©ton, il faut atteindre la couche infĂ©rieure pour la marier avec la derniĂšre couche sans poches jointives. La cure du bĂ©ton est importante au dĂ©but de sa prise. Elle consiste Ă maintenir le bĂ©ton dans un environnement propice Ă sa prise. Il faut Ă©viter toute Ă©vaporation de lâeau contenue dans le bĂ©ton (par temps chaud et/ou venteux), ce qui empĂȘcherait la rĂ©action chimique de prise de se faire et mettrait donc en cause la rĂ©sistance du bĂ©ton.
Il faut aussi Ă©viter les chocs thermiques. La rĂ©action exothermique du bĂ©ton, Ă©ventuellement ajoutĂ©e Ă une forte chaleur ambiante fait que le bĂ©ton pourrait « s'autocuire ». Ă lâinverse il faut protĂ©ger le bĂ©ton du froid ambiant pour que la rĂ©action chimique du bĂ©ton sâamorce et quâelle sâentretienne pendant un laps de temps minimum (jusquâĂ 48 heures pour les bĂ©tons Ă prise lente). Dans le cas de grands froids, les coffrages sont isolĂ©s (laine de verre ou tentes chauffĂ©es) et doivent rester en place jusquâĂ ce que le bĂ©ton ait fait sa prise.
Propriétés des bétons projetés.
- Grande résistance due à un faible rapport E/C et à un degré de compactage élevé.
- Bonne adhérence.
- Bonne résistance aux acides et à l'usure.
- Perméabilité faible.
- Retrait faible, principalement par la méthode sÚche.
- Mélange trÚs homogÚne par la méthode humide,
Finitions
Le bĂ©ton peut avoir diffĂ©rentes finitions, traitements mĂ©caniques et chimiques de surface qui font apparaĂźtre les granulats : brossĂ©, dĂ©sactivĂ© (dĂ©nudĂ© par un dĂ©sactivateur), sciĂ©, poli, poncĂ©, sablĂ©, flammĂ©, bouchardĂ©[10]âŠ
Vieillissement
Selon sa composition (alcali-rĂ©action ou rĂ©action sulfatique interne), ses additifs et selon les conditions de sa prĂ©paration (tempĂ©rature notamment) ou de son coulage ou selon les contraintes quâil a subies (attaques chimiques, sĂ©ismes, vibrations, chocs thermiques, etc.), le bĂ©ton vieillit plus ou moins bien. De nombreux tests et Ă©tudes portent sur la durabilitĂ© des bĂ©tons. En particulier, la caractĂ©risation des matĂ©riaux par acoustique ultrasonore permet de dĂ©tecter des changements structuraux du matĂ©riau.
Un des maux qui affectent frĂ©quemment le bĂ©ton est la carbonatation. Il sâagit dâune rĂ©action chimique, entre le gaz carbonique de lâatmosphĂšre (CO2) et le ciment du bĂ©ton, qui provoque une baisse de l'alcalinitĂ© du bĂ©ton en le rendant moins basique, le pH passe ainsi de 12 Ă environ 9 ce qui n'est plus suffisant pour protĂ©ger les aciers. Lorsque lâacier enrobĂ© nâest plus protĂ©gĂ© par la barriĂšre basique du bĂ©ton, il se corrode, gonfle, et fait Ă©clater le bĂ©ton d'enrobage, les armatures ne sont alors plus protĂ©gĂ©es et la rĂ©sistance mĂ©canique est compromise.
Contact avec lâeau potable
Dans un chĂąteau d'eau ou un rĂ©servoir dâeau potable, les bĂ©tons sont soumis Ă des contraintes non rencontrĂ©es habituellement sur des bĂątiments. Le bĂ©ton seul (sans adjuvant) est normalement apte au contact avec lâeau potable. Pour respecter les exigences de la norme EN 206/CN et obtenir les caractĂ©ristiques physico-chimiques requises pour un rĂ©servoir (rĂ©sistance mĂ©canique et chimique, porositĂ©, durabilitĂ©, etc.), lâutilisation dâadjuvants est devenue indispensable (il sâagit de molĂ©cules ou de polymĂšres Ă propriĂ©tĂ© antigel, de plastifiants, de rĂ©sine, de fumĂ©es de silice, dâhydrofuge, etc.). Pour Ă©viter que ces produits se diffusent plus tard dans lâeau, ces adjuvants doivent ĂȘtre certifiĂ©s aptes pour contact avec lâeau potable.
Lâeau potable, en Ă©tant lĂ©gĂšrement acide ou trĂšs faiblement minĂ©ralisĂ©e, est agressive pour le bĂ©ton des parois. Lâeau dissout progressivement la chaux du ciment, cela entraĂźne une augmentation de la porositĂ© du bĂ©ton et une lĂ©gĂšre Ă©lĂ©vation du pH de lâeau, sans consĂ©quence majeure sur la qualitĂ© de lâeau. En revanche, en devenant poreuse, la surface de bĂ©ton peut alors favoriser le dĂ©veloppement dâun biofilm. Des rĂ©sines Ă©tanches, certifiĂ©es aptes au contact alimentaire et eau potable, peuvent alors ĂȘtre utilisĂ©es. Les joints des canalisations peuvent aussi parfois relarguer dans lâeau des nutriments dâorigine organique pouvant stimuler la croissance de certaines bactĂ©ries.
« Certains matĂ©riaux de revĂȘtement interne de grosses conduites ou de rĂ©servoirs relargueront pour leur part des polymĂšres ou des adjuvants, ou des solvants ce qui se traduira par l'apparition de saveurs dĂ©sagrĂ©ables[11] - [12]. »
Autres causes de dégradation
En France, des documents spécifiques, recommandations et fascicules de documentation, synthétisent des principes de prévention pour des problématiques de durabilité en complétant les normes européennes. Il s'agit :
- recommandations pour la prévention des désordres dus à l'alcali-réaction[13] ;
- recommandations pour la durabilité des bétons durcis soumis au gel[13] ;
- définitions et classifications des environnements chimiquement agressifs, recommandations pour la formulation des bétons (FD P 18-011)[14]
- recommandations pour la prévention des désordres liés aux réactions sulfatiques internes[15].
Corrosion des armatures
Elle se manifeste pour le béton armé par des taches de rouille à la surface du béton, mais aussi par de la délamination. L'acier des armatures se transforme en oxyde de fer, ce qui augmente le volume des armatures et provoque la dégradation du béton qui enrobe ces armatures.
Alcali silica réaction
Si les granulats utilisés contiennent de la silice mal cristallisée, on peut observer une réaction alcali granulats qui se manifeste par un gonflement au niveau microscopique qui peut entraßner des dégradations au niveau macroscopique.
Recyclage
.jpg.webp)
Le bĂ©ton peut ĂȘtre recyclĂ© lors des chantiers de dĂ©molition : il est alors concassĂ©, la ferraille en Ă©tant extraite par aimantation. Il peut ĂȘtre utilisĂ© essentiellement dans la confection de remblais[16]. Les gravillons obtenus peuvent ĂȘtre aussi rĂ©incorporĂ©s dans du bĂ©ton neuf dans des proportions variables (maximum de 5 % en France, tolĂ©rances plus Ă©levĂ©es dans dâautres pays)[16]. Si cette proportion est trop importante, le bĂ©ton rĂ©sultant est moins solide[16].
Aspect
Le bĂ©ton peut ĂȘtre teintĂ© dans la masse en y incorporant des pigments naturels ou des oxydes mĂ©talliques. Il peut aussi ĂȘtre traitĂ© Ă l'aide d'adjuvants pour ĂȘtre rendu hydrofuge (il devient alors Ă©tanche, empĂȘchant les remontĂ©es capillaires). L'ajout de diffĂ©rents matĂ©riaux (fibres textiles, copeaux de bois, matiĂšres plastiquesâŠ) permet de modifier ses propriĂ©tĂ©s physiques. Son parement pouvant ĂȘtre lissĂ© ou travaillĂ©, le bĂ©ton de ciment est parfois laissĂ© apparent (« brut de dĂ©coffrage ») pour son aspect minimaliste, brut et moderne. Le bĂ©ton utilisĂ© en revĂȘtement de grandes surfaces (esplanades, places publiquesâŠ) est souvent dĂ©sactivĂ© : on procĂšde en pulvĂ©risant, Ă la surface du bĂ©ton fraĂźchement posĂ©, un produit dĂ©sactivant qui neutralise sa prise. Un rinçage Ă haute pression permet alors, aprĂšs Ă©limination de la laitance, de faire apparaĂźtre, en surface, les divers gravillons constitutifs.
MoulĂ© ou « banchĂ© » (c'est-Ă -dire coulĂ© dans une banche : un moule dĂ©montable mis en place sur le chantier et dĂ©montĂ© aprĂšs la prise), le bĂ©ton peut prendre toutes les formes. Cette technique a permis aux architectes de construire des bĂątiments avec des formes courbes. Elle permet aussi de rĂ©aliser les tunnels. En technique routiĂšre, le bĂ©ton extrudĂ©, mis en Ćuvre Ă l'aide de coffrages glissants, permet de rĂ©aliser des murets de sĂ©curitĂ©, des bordures et des dispositifs de retenue sur des linĂ©aires importants.
Données techniques
Empreinte carbone
Le ciment employĂ© dans le bĂ©ton contribue maintenant pour 5 pour cent de la production annuelle mondiale de CO2 anthropique. D'ici 2050, l'utilisation du bĂ©ton atteindra quatre fois le niveau d'utilisation de 1990. Le problĂšme semble donc vouloir empirer. La raison pour laquelle le bĂ©ton a une grande empreinte carbone dans son ensemble tient aux quantitĂ©s Ă©normes de bĂ©ton utilisĂ©es. Le remplacement hypothĂ©tique du bĂ©ton par de l'acier par exemple ne ferait qu'accroitre le problĂšme, la fabrication de l'acier produisant Ă©galement beaucoup de CO2. La rĂšgle empirique est que pour chaque tonne de ciment produit, une tonne de CO2 est produite. Les fours Ă ciment modernes sont maintenant plus efficaces et produisent environ 800 kg de CO2 par tonne - mais c'est encore une grosse Ă©mission. La production de bĂ©ton est responsable d'une telle quantitĂ© de CO2 parce que le ciment Portland ne nĂ©cessite pas seulement des quantitĂ©s importantes d'Ă©nergie pour atteindre des tempĂ©ratures de rĂ©action allant jusqu'Ă 1 500 °C, mais aussi parce que la rĂ©action principale du ciment est la dĂ©composition du carbonate de calcium, en oxyde de calcium et en CO2. Sur ces 800 kg de CO2 produits, environ 530 kg sont libĂ©rĂ©s par la rĂ©action de dĂ©composition calcaire elle-mĂȘme. Plusieurs façons de rĂ©duire l'impact environnemental du bĂ©ton font actuellement l'objet d'Ă©tudes[17] :
L'une d'elles est la possibilitĂ© de produire des variĂ©tĂ©s ultra-rĂ©sistantes de bĂ©ton - et donc moins de bĂ©ton serait nĂ©cessaire pour faire le mĂȘme travail ; Obtenir un bĂ©ton haute-rĂ©sistance est un jeu d'Ă©quilibre particulier. Trop de pores remplis d'eau n'ayant pas rĂ©agi, affaiblissent la structure finale du bĂ©ton, mais une certaine quantitĂ© d'eau est nĂ©cessaire pour maintenir l'ouvrabilitĂ© du mĂ©lange. Cependant, ce seuil d'ouvrabilitĂ© peut ĂȘtre abaissĂ© en utilisant des additifs appelĂ©s plastifiants. La rĂ©sistance finale est obtenue par une rĂ©duction d'eau maximale, qui nĂ©cessite des molĂ©cules dispersantes ultra-puissantes, celles par exemple dont les chaĂźnes latĂ©rales sont les plus longues et qui fournissent les forces de dispersion les plus fortes[17].
Le remplacement du clinker de Portland, en partie ou en totalitĂ©, par d'autres ciments fait Ă©galement l'objet d'Ă©tudes. Les dĂ©chets tels que les scories provenant des hauts-fourneaux et les cendres volantes provenant des centrales alimentĂ©es au charbon sont dĂ©jĂ utilisĂ©s comme matĂ©riaux cimentaires supplĂ©mentaires (Supplementary cementing materials, SMC) depuis quelques dĂ©cennies. Le dĂ©fi de cette substitution est de remĂ©dier Ă certains effets nĂ©gatifs qui tiennent principalement au dĂ©veloppement prĂ©coce de la force. Avec un remplacement de 50 % du clinker par des cendres volantes, la rĂ©sistance de dĂ©part diminue de façon spectaculaire (IdĂ©alement pour un entrepreneur de construction, le bĂ©ton de l'aprĂšs-midi, devrait ĂȘtre dĂ©moulĂ© le lendemain matin.) Le potentiel de remplacement du clinker est finalement limitĂ©. La mise en place de SCM a Ă©tĂ© assez bonne - mais la production de ces matĂ©riaux est minĂ©e par la demande de ciment. Fabriquer du ciment Ă partir d'un mĂ©lange de scories et de ciment Portland est assez simple, remplacer entiĂšrement le clinker par du laitier nĂ©cessite l'ajout d'un alcali au mĂ©lange pour l'activer - et l'alcali peut alors continuer Ă attaquer l'agrĂ©gat. La rĂ©action alcali-silice devient un problĂšme, parce que le temps passant on a dĂ©couvert que beaucoup d'agrĂ©gats sont rĂ©actifs. Par exemple, en Suisse, beaucoup des 300 barrages construits dans les annĂ©es 1950 et 1960 commencent Ă montrer des signes de cette rĂ©action. C'est un problĂšme qu'il faille attendre 60 ans avant que ce dĂ©faut ne se manifeste[17].
Un substitut de clinker plus viable Ă long terme, est en termes de disponibilitĂ©, le calcaire finement broyĂ©. L'ajout de 5 % peut avoir des effets positifs, en amĂ©liorant la microstructure du bĂ©ton. Et pour les bĂątiments tels que les maisons individuelles, oĂč l'on n'a pas besoin de grande rĂ©sistance, on peut remplacer 20 % du clinker, en gardant de bonnes performances. Car c'est un obstacle clĂ© de l'utilisation efficace du bĂ©ton, l'incapacitĂ© actuelle de prĂ©dire facilement la performance d'un mĂ©lange particulier, et qui tient Ă l'incapacitĂ© Ă comprendre de maniĂšre complĂšte les rĂ©actions chimiques en Ćuvre dans la formation du bĂ©ton, connaissance devant laquelle on a souvent reculĂ© au profit d'une sorte d'approche empirique. Selon les normes europĂ©ennes, quelque 170 types de ciment sont disponibles, et si une personne veut construire une structure, il est presque impossible de dĂ©cider du matĂ©riel optimal pour la structure qu'il souhaite construire. Ce manque actuel de connaissances signifie que souvent un bĂ©ton est utilisĂ© plus fort et en plus grande quantitĂ© que ce que le travail exige[17]. Nanocem (en) est un consortium de groupes universitaires et privĂ©s qui Ă©tudie les propriĂ©tĂ©s du ciment et du bĂ©ton sur des Ă©chelles nano- et micromĂ©triques, et met l'accent sur la rĂ©duction des Ă©missions de dioxyde de carbone Ă tous les stades de la production[17].
Classes de résistance
En application de la norme[18], les bétons de masse volumique normale et les bétons lourds sont classés selon leur résistance à la compression, ce classement[19] est de la forme Cx/y.
x désigne la résistance caractéristique exigée à 28 jours, mesurée sur des cylindres[20] de 150 mm de diamÚtre sur 300 mm de haut ; y désigne la résistance caractéristique exigée à 28 jours, mesurée sur des cubes de 150 mm de cÎté.
La résistance caractéristique est définie par la norme comme étant la valeur de résistance en dessous de laquelle peuvent se situer 5 % de la population de tous les résultats des mesures de résistance possibles effectués pour le volume de béton considéré (fractile de 5 %). Cette résistance caractéristique, une pression, est exprimée en MPa ou en N/mm2.
Les classes de résistance normalisées sont C8/10, C12/15, C16/20, C20/25, C25/30, C30/37, C35/45, C40/50, C45/55, C50/60, C55/67, C60/75, C70/85, C80/95, C90/105 et C100/115.
Ces classes sont définies par la résistance à la compression du béton et sont :
- la classe C 16/20 : ce bĂ©ton peut ĂȘtre utilisĂ© pour des Ă©lĂ©ments non armĂ©s et donc peu sollicitĂ©s ;
- la classe C 20/25 : pour des bĂ©tons peu exposĂ©s et soumis Ă de faibles sollicitations. Cette classe peut ĂȘtre utilisĂ©e pour des bĂ©tons lĂ©gĂšrement armĂ©s, par exemple dans les fondations et dalles sur sol ;
- la classe C 25/30 : pour colonnes, poutres et dalles sans sollicitation exceptionnelle. Cette classe satisfait aux exigences de résistance et de durabilité requises dans les bùtiments.
Pour les bétons légers le classement est de la forme[21] LCx/y (art. 4.3.1 tableau 8), les classes de résistance normalisées sont LC8/9, LC12/13, LC16/18, LC20/22, LC25/28, LC30/33, LC35/38, LC40/44, LC45/50, LC50/55, LC55/60, LC60/66, LC70/77 et LC80/88.
Quatre (cinq) rÚgles à respecter pour avoir un béton durable.
Les 4C : Ciment contenu : avoir une teneur en ciment suffisante ; Cover : avoir un enrobage suffisant ; CompacitĂ© : Le facteur E/C doit ĂȘtre optimal â cela limitera les vides (+compact) Curing : ProtĂ©ger le bĂ©ton frais contre la dessication et le gel
(ContrĂŽle : ContrĂŽler lâapplication des 4 C prĂ©cĂ©dents)
Classe de consistance
La consistance du bĂ©ton peut ĂȘtre mesurĂ© par l'essai dâaffaissement au cĂŽne dâAbrams. Cet essai classe le bĂ©ton en 5 classes de consistance, allant de la classe S1, dĂ©crivant un bĂ©ton trĂšs peu fluide, jusqu'Ă la classe S5, dĂ©crivant un bĂ©ton trĂšs fluide. Cet essai est dĂ©crit par la norme NF EN 12350-2.
Cet essai peut ĂȘtre aussi nommĂ© « slump test », terme venant directement de l'anglais.
Classe d'exposition
Le bĂ©ton est classĂ© selon plusieurs critĂšres dĂ©crivant son environnement et tous les type de dĂ©gradation qu'il pourrait subir. Il existe 6 classes d'exposition (X0, XC, XD, XS, XF et XA) dĂ©crivant toutes un type diffĂ©rent d'attaque, comme par exemple la corrosion induite par carbonatation, ou l'altĂ©ration par cycle gel/dĂ©gel. Ces classes d'exposition impactent la formulation d'un bĂ©ton pour qu'il rĂ©ponde aux exigences de l'environnement dans lequel il sera mis en Ćuvre.
Importance économique
Avec une production annuelle de cinq milliards de mÚtres cubes, il est le matériau le plus consommé au monde (selon les pays, 5 à 10 fois la consommation de métaux, 10 à 30 fois celle de carton ou plastique)[22]
En France
Ce secteur tient une place Ă©conomique importante, dans le secteur public, comme dans le privĂ©. Il subit la crise de 2008, mais bien moins qu'en Espagne ou au Portugal selon les producteurs[23] - [24]. Si l'on considĂšre la vente de bĂ©ton prĂȘt Ă lâemploi comme un indicateur d'activitĂ©, l'Italie, lâAllemagne et la France ont Ă©tĂ© en 2011 les trois plus gros producteurs de ces bĂ©tons, avec plus de 40 millions de mĂštres cubes chacun[24].
Selon les relevĂ©s dâenquĂȘte de FIB-UNICEM[25], et les producteurs[24]. En 2005, le bĂ©ton prĂȘt Ă l'emploi reprĂ©sentait 39 365 800 m3 vendus, pour 3 365 407 000 euros dont 3 048 000 euros Ă lâexportation dans 542 entreprises ou sections dâentreprises, par 7 914 salariĂ©s (dont 4 310 cadres & ETAM), effectuant 6 164 000 heures de travail, pour une masse salariale brute (hors cotisations sociales) de 206 749 000 euros. En 2008, la fabrication de produits en bĂ©ton reprĂ©sentait 29 829 000 tonnes vendues, pour 3 146 757 000 euros dans 708 entreprises ou sections dâentreprises, par 20 526 salariĂ©s (dont 6 077 cadres et ETAM), effectuant 23 003 000 heures de travail, pour une masse salariale brute (hors cotisations) de 535 769 000 euros. La fabrication de supports en bĂ©ton armĂ© reprĂ©sente 120 700 tonnes vendues, pour 34 045 000 euros dans 9 entreprises ou sections dâentreprises, par 260 salariĂ©s (dont 131 cadres et ETAM), effectuant 225 000 heures de travail, pour une masse salariale brute (hors cotisations) de 6 866 000 euros.
En 2011 la France a produit 41,3 millions de mĂštres cubes de bĂ©ton prĂȘt Ă lâemploi en 2011, soit une hausse de +10,4 % (explicable pour 3 Ă 4 % par un « effet de rattrapage de 3 mois dâintempĂ©ries subis en 2010 » mais alors que la moyenne europĂ©enne a Ă©tĂ© de +2,7 %). La France est situĂ©e aprĂšs l'Italie (51,8 millions de mĂštres cubes, -4,8 %) et lâAllemagne (48 millions de mĂštres cubes, +14,3 %). La construction en bĂ©ton est dopĂ©e en Italie, Allemagne et Autriche notamment, par l'habitude de fabriquer des routes en bĂ©ton. Avec 0,638 m3 de bĂ©ton par habitant et par an en 2011 la France est au-dessus de la moyenne communautaire (0,613 m3), loin derriĂšre lâAutriche (1,254 m3 par habitant) qui utilise beaucoup de bĂ©ton pour construire des routes[24]. La France disposait en 2011 d'environ 1 800 centrales Ă bĂ©ton employant 14 500 personnes et 6 500 camions toupies[24]. En 2011, 22 % des bĂ©tons Ă©taient pompĂ©s (jusqu'Ă 30 % dans les dĂ©partements du Sud-Est) Avec 1 800 pompes Ă bĂ©ton, c'est moins qu'en Italie (2 400 camions pompes) et un peu plus qu'en Allemagne (1 600 camions pompes)[24]. La livraison est plus rapide et ne nĂ©cessite pas de grue, mais avec moins d'emplois (3 personnes contre 5)[24].
Métiers
La pratique du bĂ©ton se raccroche Ă la pratique du maçon et de la maçonnerie. On parle de bĂ©tonneur ou de maçon-bĂ©tonneur. Le travail dâĂ©laboration des coffrages se fait par le coffreur. L'ingĂ©nieur structure est responsables de l'Ă©tude des ferraillages et ferrailleurs de leur pose.
Recherche et développement
- Le CERIB, Centre d'Ă©tudes et de recherches de l'industrie du bĂ©ton manufacturĂ©[26], est créé en France en janvier 1967, (publication au journal officiel[27], au vu de la loi sur les Centres Techniques Industriels 48-1228 du 22 juillet 1948), actuellement financĂ© par une taxe parafiscale sur les produits en bĂ©ton et en terre cuite[28], qui travaille de concert avec le CIMBETON (Centre d'information sur le ciment et ses applications) et le CSTB (Centre scientifique et technique du bĂątiment), le CTMCC (Association des Centres Techniques des MatĂ©riaux et Composants pour la Construction) et l'EFB (Ăcole Française du BĂ©ton) et le SFIC (Syndicat Français de l'Industrie CimentiĂšre).
- En 2007 à l'université de Leeds, John Forth et son équipe ont mis au point le « bitublock ». à base de 95 % de verre brisé, ferrailles et cendres, ce matériau serait six fois plus résistant que le béton classique.
- En 2016, un procĂ©dĂ© dĂ©nommĂ© « Solidia Technologies » (conjointement brevetĂ© par Air Liquide et une startup amĂ©ricaine) est prĂ©sentĂ© comme permettant de produire un bĂ©ton prĂ©fabriquĂ© Ă partir de ciment non-hydraulique. AdaptĂ© Ă la production de parpaings plaques, pavĂ©s autobloquants, etc. le procĂ©dĂ© est moins consommateur d'eau et Ă moindre empreinte carbone, car l'eau y est remplacĂ©e par l'injection de gaz carbonique qui en outre accĂ©lĂšre la formation de carbonate de calcium et le durcissement du bĂ©ton (complĂštement durci en 24 h au lieu de 28 jours)[29]. Le CO2 rĂ©agit en 24 heures avec les silicates de calcium du ciment, en permettant la production de calcite (CaCO3) et de silice (SiO2) qui rendront le bĂ©ton rĂ©sistant[29]. En 2013, Lafarge a passĂ© un accord avec Solidia pour s'assurer de pouvoir utiliser le procĂ©dĂ©. Selon un communiquĂ© d'Air Liquide ceci diminue jusqu'Ă 70 % de l'empreinte environnementale de ces bĂ©tons. Le CO2 pourrait ĂȘtre prĂ©levĂ© sur les cheminĂ©es des cimenteries, qui constituaient vers 2015 un gisement potentiel d'environ 800 millions de tonnes de CO2 par an[29]. En outre le clinker utilisĂ© pour le ciment peut ĂȘtre produit Ă 1 200 °C, soit environ 250 °C de moins que pour les ciments "classiques", permettant environ 30 % d'Ă©conomie d'Ă©nergie pour la cimenterie et une Ă©mission de CO2 Ă©galement rĂ©duire d'environ 30 %[30].
Notes et références
- « Site d'infociments, collection technique Cimbéton »
- Site du projet Recybéton, consulté le 2015-06-04
- Recyclage récupération ; Recybéton veut faire évoluer les normes,3 juin 2015
- Groupe Lafarge (2001) « 1er rapport de performance économique, sociale et environnementale ; "Construire un monde durable" »(Archive.org ⹠Wikiwix ⹠Archive.is ⹠Google ⹠Que faire ?), voir p. 34/60 (encart : les réductions des émissions de CO2)
- Thierry Kubwimana, Nicolas Bourneton, Nicolas Rouxel, AldĂ©ric Hauchecorne. Utilisation des bĂ©tons fibrĂ©s Ă ultrahautes performances en site portuaire. p. 685â692. DOI:10.5150/jngcgc.2010.079-K (Lire en ligne.)
- Jean-Michel Torrenti (1995) Comportement diffĂ©rĂ© du bĂ©ton dans les enceintes de centrales nuclĂ©aires : analyse et modĂ©lisation Laurent Granger 1 1995-02-15, Feed HAL:tel-00520675 (ThĂšse de Doctorat de l'Ăcole Nationale des Ponts et ChaussĂ©es), 406 p.
- P. Faucon, « Les composites ciment verre : Un matériau pour accéder à de nouveaux marchés », dans CongrÚs international du béton manufacturé N° 5, Paris, Fédération de l'industrie du béton, , 560 p. (présentation en ligne), II.59-II.71
- Thierry Lucas, « Les composites ciment-verre s'immiscent dans le B-TP », L'Usine nouvelle, no 2970,â (lire en ligne)
- Barrage de Petit-Saut
- Marcel Hurez, Béton architectonique, Ed. Techniques Ingénieur, (lire en ligne), p. 8-9
- Ghislain Loiseau et Catherine Juery, mis Ă jour par Jean-luc cellerier et Jean-Antoine Faby ; La dĂ©gradation de la qualitĂ© de lâeau potable dans les rĂ©seaux, Fonds national pour le dĂ©veloppement des adductions dâeau ; Office International de lâEau, SNIDE, PDF, 98 p.
- Schulhof P., Cabridenc R., Chedal J. QualitĂ© de lâeau dans les grands rĂ©seaux de distribution, TSM, 1990, no 11, 561-594
- « Accueil - Cadic intégrale », sur ifsttar.fr (consulté le ).
- « FD P18-464 », sur Afnor EDITIONS (consulté le ).
- « DTRF - Consultation d'une notice (Dtrf-0004269) », sur setra.fr (consulté le ).
- Amaury Cudeville, « Recycler le béton », Pour la Science, octobre 2011, p. 17-18.
- The concrete conundrum Chemistry World 62 Mars 2008 Royal Society of Chemistry. en ligne
- Norme NF EN 206/CN Béton Partie 1 : Spécification, performances, production et conformité. Cette norme n'est pas librement accessible sur l'internet mais vendue par l'AFNOR
- NF EN 206-1, art. 4.3.1 tableau 7
- Avant l'homologation de la norme NF EN 206/CN, les éprouvettes cylindriques, couramment utilisées en France, avaient comme dimensions 16 cm de diamÚtre sur 32 cm de haut. à partir de la norme NF EN 206/CN, ces cylindres doivent avoir des dimensions conformes à la norme NF EN 12390-1 (Essai pour béton durci Partie 1 : Forme, dimensions et autres exigences relatives aux éprouvettes et aux moules), soit 150 mm de diamÚtre sur 300 mm de haut.
- C comme Concrete et LC comme Light Concrete
- conférence de Paul Acker à l'Université de tous les Savoirs, 01/10/2000
- Lâorganisation europĂ©enne du bĂ©ton prĂȘt Ă lâemploi (ERMCO ou European Ready Mixed Concrete Organization) ; chiffres de production pour lâannĂ©e 2011
- BatiActu, BĂ©ton prĂȘt Ă lâemploi : pourquoi la France rĂ©siste Ă la crise (2012-08-29)
- Site de lâUNICEM
- Site du CERIB
- JO du 14 janvier 1967
- DĂ©cret no 2000-1278 du portant crĂ©ation dâune taxe parafiscale sur les produits en bĂ©ton et en terre cuite
- BatiActu (2016) Un béton qui séquestre du CO2, Publié le 01/07/2016.
- SolidiaTech (2016) The Science behind Solidia CementTM and Solidia ConcreteTM, PDF, 2 p., consulté le 4 juillet 2018
Annexes
Bibliographie
- Sous la direction de Jean-Pierre Ollivier et Angélique Vichot pour l'ATILH - La durabilité du béton - Presses de l'école des Ponts et Chaussées - Paris - 2008 (ISBN 978-2-8597-8434-8)
- Cimbéton, cahier des modules de conférence pour les écoles d'architecture - Janvier 2009 - Histoire du béton, naissance et développement 1818-1970
Articles connexes
- Matériau composite
- Bloc de béton
- Béton translucide
- Béton cyclopéen
- Coulis (maçonnerie)
- Retrait du béton
- Fluage du béton
- Carbonatation du béton
- Béton armé
- Louis Vicat, formulation du ciment artificiel et inventeur du clinker,
- Joseph Aspdin, inventeur du ciment Portland,
- Joseph Monier, inventeur du ciment armé
- Gustav Adolf Wayss et le développement du béton armé en Allemagne et en Autriche,
- Emil Mörsch, théorie et application du béton armé,
- François Hennebique, concepteur de structures en béton armé
- Auguste Perret, premier architecte Ă gĂ©nĂ©raliser lâusage du bĂ©ton armĂ© dans la construction
- EugÚne Freyssinet, inventeur du béton précontraint
- Union nationale des industries de carriÚres et matériaux de construction (France)
- Commission du ciment armé (1900)
- Béton bas carbone
- Musée du béton