ContrĂ´le non destructif
Le contrôle non destructif (CND) est un ensemble de méthodes qui permettent de caractériser l'état d'intégrité de structures ou de matériaux, sans les dégrader, soit au cours de la production, soit en cours d'utilisation, soit dans le cadre de maintenances. On parle aussi d'essais non destructifs (END) ou d'examens non destructifs[1].
Utilisations
Ces méthodes sont utilisées dans l'ensemble des secteurs industriels. On peut citer notamment :
- l'industrie pétrolière (pipelines, tubes, barres, soudures, réservoirs) ;
- l'industrie navale (contrĂ´le des coques) ;
- l'aéronautique (poutres, ailes d'avion, nombreuses pièces moteurs, trains d'atterrissage, etc.) ;
- l'aérospatiale et l'armée ;
- l'industrie automobile (contrĂ´le des blocs moteurs) ;
- la sidérurgie ;
- la fonderie ;
- la chaudronnerie et la tuyauterie en fabrication ;
- l'industrie de l'énergie : réacteurs nucléaires, chaudières, tuyauterie, turbines, etc. (maintenance des installations) ;
- le ferroviaire en fabrication et en maintenance notamment pour les organes de sécurité (essieux, roues, bogies) ;
- l'inspection alimentaire ;
- le Génie Civil et le bâtiment.
Et en règle générale dans tous les secteurs produisant :
- des pièces à coût de production élevé en quantité faible (nucléaire, pétrochimique, par exemple) ;
- des pièces dont la fiabilité de fonctionnement est critique (BTP, nucléaire, canalisation de gaz, par exemple).
Mais également dans des secteurs moins industriels comme l'archéologie !
Les agents qui effectuent ces contrôles peuvent être certifiés selon les normes en vigueur, si la règlementation l'exige, si le client le demande, ou si l'entreprise utilise ce moyen comme assurance de la compétence de ses opérateurs dans le cadre de sa politique qualité.
Acteurs
Les acteurs de la profession sont nombreux : prestataires, formateurs, fabricants de matériels, laboratoires de recherche, centres techniques industriels ainsi que les industriels utilisateurs.
Par ailleurs, plusieurs organismes à but non lucratif existent en France, avec des vocations complémentaires :
- La Cofrend (Confédération française pour les essais non destructifs) est un organisme « tierce-partie » qui gère le système de certification selon deux normes[2] :
- norme française et européenne NF EN 473 intitulée : « Essais non destructifs, qualification et certification du personnel END ». Cette norme a été écrite en avril 1993, révisée en 2000 puis en 2008. Sous ce référentiel, la certification se répartit dans trois comités sectoriels :
- produits métalliques (CCPM) regroupant la fonderie[3] (anciennement CCF) et les produits en acier (CCPA) ;
- maintenance ferroviaire (CFCM) ;
- fabrication et maintenance (CIFM) ;
- norme européenne EN 4179 dont l'équivalent américain est la NAS 410. Pour les pièces destinées à l'industrie aérospatiale (aéronautique et espace), les CND sont considérés comme des procédés spéciaux et doivent être qualifiés comme tels. En France, ces certifications sont regroupées sous le comité sectoriel aéronautique COSAC de la Cofrend.
- norme française et européenne NF EN 473 intitulée : « Essais non destructifs, qualification et certification du personnel END ». Cette norme a été écrite en avril 1993, révisée en 2000 puis en 2008. Sous ce référentiel, la certification se répartit dans trois comités sectoriels :
La certification a une durée de validité de cinq ans (renouvelables) et ce sont plus de 12 000 personnes qui sont ainsi certifiées, c'est-à -dire qui ont passé avec succès un examen théorique et pratique. Par ailleurs, la Cofrend est accréditée par le Cofrac selon l'ISO 17024[2].
- PRECEND[4], plateforme régionale d'innovation, structure associative financée par des fonds européens, nationaux et régionaux pour aider et assister les entreprises dans leur problématiques de contrôles non destructifs.
- ECND-PDL[5], qui regroupe les compétences des laboratoires de recherche en CND, qui sont nombreux en Pays de la Loire
Ces trois organismes collaborent pour animer la profession, notamment en diffusant l'information (documentation technique à disposition, journées d'information…) et sont au service des entreprises pour leur permettre de trouver les bons interlocuteurs.
Principes généraux

Quelle que soit la méthode adoptée, on peut représenter la mise en œuvre d'un système CND suivant le synoptique suivant : la cible se caractérise par un ensemble de paramètres que l'on va chercher à estimer afin de former un diagnostic d'intégrité. La mise en œuvre d'un système CND adéquat va permettre de produire un certain nombre de signaux qui sont fonction des paramètres recherchés. Une étape « d'inversion », plus ou moins compliquée, est bien souvent nécessaire afin de retrouver les paramètres initiaux de la pièce.
Dans l’industrie pétrolière, plus spécifiquement, les canalisations sont inspectées de manière interne par des systèmes automatisés. Le déplacement à plus ou moins grande vitesse de ces outils et les résolutions attendues nécessitent alors des moyens de CND très performants comme l'utilisation d'EMAT. Sur les pipelines, on utilise des racleurs instrumentés[6] et sur les forages profonds, des sondes de diagraphie[7].
Différentes méthodes de contrôle
Les normes NF EN ISO 9712 août 2012 (qui annule et remplace la norme EN 473) et EN 4179 définissent un certain nombre de symboles pour les méthodes usuelles (cf. tableau).
Ces symboles correspondent généralement à l'abréviation de la désignation anglaise de la méthode, par exemple, le symbole « PT » pour le ressuage vient de penetrant testing. Cependant, il existe de nombreuses autres méthodes qui ne sont pas sujettes à la certification des contrôleurs, et n'ont donc pas de terminologie normée : c'est le cas par exemple du radar, très utilisé dans le génie civil.
Méthode END | Symbole |
---|---|
Émission acoustique | AT |
Courants de Foucault | ET |
Étanchéité | LT |
Magnétoscopie | MT |
Ressuage | PT |
Radiographie | RT |
Ultrasons | UT |
Examen visuel | VT |
Shearographie | ST |
Thermographie | TT |
ContrĂ´le par examen visuel (VT)
Le contrôle visuel est une technique essentielle lors du contrôle non destructif. L'état extérieur d'une pièce peut donner des informations essentielles sur l'état de celle-ci : des défauts évidents (comme des pliures, des cassures, de l'usure, de la corrosion ou fissures ouvertes). Un examen visuel doit être effectué dans de bonnes conditions assurant avant tout un éclairage suffisant. Le niveau d’éclairement minimum requis est de l’ordre de 350 lx. L’accessibilité de la partie à examiner doit permettre d’approcher l’œil à au moins 60 cm, sous une incidence de 30°. Lorsque la partie de la pièce à contrôler n’est pas accessible par un examen direct, on utilise un appareil appelé « endoscope ». Il s’agit d’un appareillage constitué de miroirs et lentilles. La méthode est appelée « contrôle par endoscopie ». Des défauts cachés sous-jacents présentant une irrégularité sur la surface extérieure peut être une indication de défaut plus grave à l'intérieur. Choisir la technique la plus adaptée en CND pour des examens approfondis déterminer des limitations des autres techniques CND choisies (accès, état de surface, etc.). Les tests d'étanchéité, les tests pneumatiques et les épreuves hydrauliques comportent aussi un examen visuel pour mettre en évidence des fuites éventuelles.
ContrĂ´le par ressuage (PT)
C'est une méthode destinée à révéler la présence de discontinuités ouvertes en surface de pièces métalliques, essentiellement, mais aussi en céramique. Elle consiste à badigeonner (par immersion ou par pulvérisation électrostatique, parfois mais rarement, au pinceau) la cible avec un liquide fluorescent ou coloré en rouge, qui pénètre dans les discontinuités. Après nettoyage de la cible, un révélateur est appliqué et, en faisant « ressuer » le liquide resté dans les fissures, va les révéler.
Cette méthode semble très simple à mettre en œuvre et elle est sensible aux discontinuités ouvertes. On peut mettre en évidence des discontinuités de 10 µm d'ouverture, cent fois plus fines qu'un cheveu. De plus, elle nécessite l'utilisation de produits non récupérables, voire contaminés après utilisation (exemple d'une centrale nucléaire où on essaie de réduire le volume des déchets), mais cette méthode est irremplaçable pour la mise en évidence de discontinuités débouchantes présentes dans les matériaux non ferromagnétiques ou non conducteurs d'électricité.
ContrĂ´le radiologique (RT)
.png.webp)
Rayons X (RTX)
Les rayons X en contrôle non destructif sont principalement utilisés pour réaliser des radiographies X. L'avantage de cette technique est de fournir des informations directement exploitables sur l'intérieur des objets ou des matériaux. L'étape d'inversion peut être assez réduite et la résolution spatiale suffisamment bonne. Toutefois, l'interprétation des images demande de l'expertise et la réalisation des clichés nécessite des conditions de sécurité pour l'opérateur et l'environnement.
Dans l'industrie lourde, le contrôle à l'aide des rayons X est utilisé notamment pour les soudures dans les centrales nucléaires et les chantiers navals et pétroliers, la corrosion des tuyaux, la structure des matériaux composites ou les fissures dans les pièces mécaniques complexes ainsi que pour les pièces de fonderie.
D'autres méthodes radiologiques de contrôle non destructif utilisent la fluorescence et la spectrométrie. Grâce au rayonnement rétrodiffusé, il est possible d'analyser le contenu atomique des objets et ainsi par exemple de détecter la présence de plomb ou d'autres matériaux toxiques dans les peintures, ou bien la présence d'explosifs dans des objets suspects.
Gammagraphie (RT gamma)
Cette technique de radiographie industrielle utilise une source de rayonnements gamma. Elle se rapproche de la radiographie par rayons X mais nécessite plus de précautions. La qualité d'image est également moins bonne. L'avantage principal réside dans l'énergie du rayonnement qui permet une meilleure pénétration que par les rayons X et la plus grande compacité des projecteurs et des sources. Les appareils de gammagraphie appelés gammagraphes (abrégé : GAM) fonctionnent à l'aide d'isotope radioactif stable (principalement iridium 192, cobalt 60 et sélénium 75). Ce sont des sources autonomes qui ne nécessitent aucune prise de courant contrairement au poste à rayon X.
La technique consiste à placer la pièce à radiographier entre la source de rayonnements et un film photographique contenu dans une cassette souple ou rigide. Après un temps d’exposition dépendant de la qualité du film, de l'isotope, de l'activité de la source radioactive, la nature et l’épaisseur du matériau radiographié, le film est développé. L'interprétation du film permet de mettre en évidence certains défauts de compacité de la pièce. Les domaines d’utilisation sont nombreux (chaudronnerie, fonderie, industrie du pétrole-chimique, construction navale et aéronautique).
Neutronographie
Le principe de la neutronographie est similaire à celui de la radiographie X et lui est complémentaire. Elle peut être effectuée grâce à un faisceau neutronique directement issu d’un réacteur nucléaire, ou indirectement d'un accélérateur d'ions, d'une source alpha-béryllium (souvent 241Am – 9Be), ou directement d’une source de 252Cf (émetteur de neutrons par fission spontanée). Elle est notamment utilisée pour le contrôle de matériaux hydrogénés situés à l'intérieur d'enceintes métalliques.
Jauges
Le principe des jauges est basé sur la loi de l’atténuation des rayonnements (loi de Beer-Lambert). On distingue :
- jauges de niveau : elles indiquent la présence ou l’absence de matériau sur le trajet horizontal du faisceau (source et détecteur placé de part et d’autre du matériau). Les sources utilisées sont des émetteurs bêta ou gamma selon l’épaisseur et la densité du matériau à mesurer. Elles sont utilisées pour le contrôle des réservoirs de liquides, des silos (sable, grains, ciment, etc.) ;
- jauges d’épaisseur : si le matériau est de densité constante, l’intensité du signal reçu par le détecteur sera fonction de l’épaisseur de celui-ci. Elles sont utilisées pour la mesure en continu de produits en feuilles : papiers, tissus ou caoutchouc par exemple.
ContrĂ´le par ultrasons (UT)
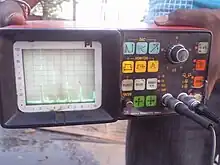
Le contrôle par ultrasons est basé sur la transmission, la réflexion et l'absorption d'une onde ultrasonore se propageant dans la pièce à contrôler. Le train d'onde émis se réfléchit sur les défauts puis revient vers le traducteur (qui joue souvent le rôle d'émetteur et de récepteur). L'interprétation des signaux permet de positionner le défaut et de définir ses dimensions relatives. Cette méthode présente une résolution spatiale élevée et la possibilité de trouver des défauts aussi bien dans le volume de la matière qu'en surface. L'étape d'inversion est simple, du moins pour les pièces géométriquement et matériellement simples. Cette méthode nécessite d'effectuer un balayage mécanique exhaustif de la pièce. Il est d'ailleurs souvent nécessaire de contrôler plusieurs surfaces de la pièce pour pouvoir faire une représentation tridimensionnelle des défauts.
D'autres techniques, telles que la méthode TOFD (Time of flight diffraction), utilisent le principe de diffraction des ondes ultrasonores pour la détection et la caractérisation des défauts. Les développements technologiques récents permettent également la mise en œuvre de « multiéléments », c'est-à -dire l'équivalent de plusieurs capteurs ultrasonores utilisés en même temps, ce qui permet de maîtriser la « forme » du train d'ondes émis. Par comparaison avec le contrôle par radiographie qui est également mis en œuvre pour la recherche de défauts dans le volume de la matière, les principaux avantages et inconvénients sont les suivants :
Avantages :
- ne nécessite qu'une seule face d'accès ;
- aucun danger lié à l'utilisation de source radioactive et de rayonnements ionisants ;
- plus grande sensibilité de contrôle sur les pièces de forte épaisseur ;
- résultat du contrôle en temps réel ;
- contrôle plus rapide pour des épaisseurs importantes ;
- meilleure sensibilité de contrôle pour les défauts filiformes (fissures, tapures, criques) d'orientation aléatoire ;
Inconvénients : ;
- certains matériaux métalliques sont difficilement contrôlables (matériaux à gros grains) ;
- contrôle plus lent pour les faibles épaisseurs ;
- plus faible sensibilité à la détection de porosités.
Émission acoustique (AT)
Le contrôle par émission acoustique consiste à recueillir l'émission d'une pièce ou structure soumise à sollicitation, par exemple lors d'une épreuve hydraulique ou pneumatique. La propagation des ondes ultrasonores élastiques dans le matériau, détectée par un maillage de capteurs, peut conduire à une localisation des sources d'endommagement du matériau en temps réel (fissuration…) et à une évaluation de leur sévérité. C'est une méthode globale (tout l'appareil est contrôlé en même temps) et dynamique (les défauts non évolutifs ne sont pas détectés).
Thermographie (TT)
Les méthodes de contrôle thermique consistent à exciter un matériau ou une structure par un apport d'énergie (mécanique, photonique, chauffage par induction, air chaud…). La diffusion de la chaleur dans le matériau et l'impact qu'elle a sur la distribution de température de surface renseignent sur les propriétés thermophysiques des matériaux et sur d'éventuels défauts ; un temps de propagation d'une onde de chaleur dans un matériau peut par exemple permettre de mesurer la diffusivité thermique du matériau et ainsi en déduire la conductivité thermique.
Les principaux avantages de l'ensemble de ces méthodes résident dans la possibilité d'effectuer un contrôle sans contact et automatisable. Les inconvénients sont liés à la lenteur du contrôle, au coût de l'investissement et à la difficulté de mise en œuvre des étapes d'inversion pour établir le diagnostic.
Magnétoscopie (MT)
La magnétoscopie est une technique de contrôle non destructif qui consiste à créer un flux magnétique intense à la surface d’un matériau ferromagnétique.
Lors de la présence d’un défaut sur son chemin, le flux magnétique est dévié et crée une fuite qui, en attirant les particules (colorées ou fluorescentes) d’un produit révélateur, fournit une signature particulière caractéristique du défaut.
Contrôle d'étanchéité (LT)
Les méthodes de contrôle d'étanchéité font appel à des gaz traceurs, couplés à des instruments très sensibles à des concentrations minimes de ces gaz traceurs. Les plus courants sont l'hélium, l'hydrogène (azote hydrogéné), l'utilisation du gaz SF6 est lui maintenant interdit par la règlementation. Actuellement, cette méthode n'est encore pas codifiée par le Cofrend, mais elle l'est dans de nombreux autres pays[8] les États-Unis par exemple.
Des méthodes de détection de fuite à l'aide d'un système de mesure en maintien de pression permettent une grande précision de détermination du taux de fuite, sans recourir aux gaz traceurs. Dans le contrôle des emballages, ces méthodes ont l'avantage de contrôler l'ensemble du volume scellé, et notamment l'ensemble des soudures (longitudinales et transversales) qui sont très souvent inaccessibles par le procédé de pliage.
Les méthodes de détection de fuite en bassin sans dépression externe ont une sensibilité de l'ordre de 250 µm pour une probabilité de détection de 70 % pour le contrôle de contenants à volume variable [9]. À cette difficulté intrinsèque du test en bassin, s'ajoutent les plis issus de la réalisation de l'emballage (soudure longitudinale), qui peuvent emprisonner des bulles d'air vues comme des fausses fuites.
Contrôle d'étanchéité ITM TODA-15
La méthode de contrôle ITM TODA-15 associe une mise en dépression des éléments à contrôler (réservoirs et accessoires et canalisations associées) à une détection acoustique des « bruits de fuites » dans les zones non étanches. La dépression est l'élément physique qui provoque l'émission de turbulences dans les zones non étanches. Les « bruits » de fuite (turbulences) sont détectés grâce au positionnement de capteurs dans l'installation contrôlée (canalisations, réservoirs associés et accessoires). Les capteurs ATEX sont raccordés à une interface électronique (TODA Unit) qui permet, en combinaison avec un logiciel spécifique, le traitement des signaux acoustiques et la gestion du contrôle d'étanchéité. La méthode de contrôle ITM TODA-15 est principalement utilisée dans les installations de stockage travaillant sous pression atmosphérique.
Courants de Foucault (ET)
Les courants de Foucault (ET)[10] sont des courants qui apparaissent dans un matériau conducteur lorsque l'on fait varier le flux magnétique à proximité. Ils sont une conséquence de la loi de Lenz-Faraday.
Dans le cadre des END, c'est l'induction magnétique B que l'on fait varier grâce à l'injection dans une bobine d'un courant alternatif selon différentes fréquences. Cette bobine joue le rôle d'émetteur et parfois récepteur, la variation de flux dans le matériau crée des courants induits : les courants de Foucault (CF). En présence d'un défaut, leur circulation est perturbée par les variations de conductivité électrique dues à la géométrie du défaut. Cette perturbation entraine une variation du champ magnétique créé par les courants de Foucault que l'on peut détecter grâce à la bobine (capteur inductif de type fluxmètre). La technique consiste à utiliser une sonde munie d'une bobine et de mesurer aux bornes d'un pont une différence de tension engendrée par la variation d'impédance de la bobine excitatrice/réceptrice.
Les examens non destructifs par courants de Foucault peuvent être automatisés ce qui rend le contrôle rapide ; et pratique notamment si l'environnement de contrôle est potentiellement dangereux. En présence d'un défaut complexe, un complément d'examen par ultrasons peut être effectué pour mieux caractériser l'anomalie.
Méthodes couplées
Récemment, des méthodes couplées ont vu le jour, et pour certaines sont encore dans le domaine de la recherche : les méthodes électromagnétiques acoustiques, électromagnétiques ultrasonores ou magnéto-optiques.
Acoustique non linéaire
Plusieurs études ont montré que les méthodes acoustiques linéaires ne sont pas assez sensibles à l’endommagement très localisé. Devant une telle difficulté, les méthodes acoustiques non linéaires présentent une alternative importante capable de caractériser et éventuellement de déterminer les endommagements faibles ou précoces, localisés ou diffus. Ainsi depuis quelques années, l’acoustique non linéaire apparaît de plus en plus comme une nouvelle piste très prometteuse pour le contrôle et l’évaluation non destructive des matériaux de structure.
Voir aussi
Bibliographie
Jean Perdijon, Matériaux sous surveillance, Cachan, Éditions Lavoisier, 2021.
Articles connexes
Liens externes
- « Magnétoscopie - Historique et Technique (Document présenté lors des Journées Cofrend 2008) »(Archive.org • Wikiwix • Archive.is • Google • Que faire ?)
- Méthode de test d'étanchéité ITM TODA15
- ICNDT, The International Committee for Non-Destructive Testing
- EFNDT, European Federation for Non-Destructive Testing
- CIVA, logiciel de contrôle non destructif développé et édité par le CEA : http://www-civa.cea.fr/, http://www.extende.com/
- NDT Radio, application pour le contrĂ´le non destructif et la radioprotection. Application Android et Web
- IAEA The International Atomic Energy Agency
Références
- « Les CND, c'est quoi ? », sur cofrend.com (consulté le ).
- « Cofrend - Qui est la Cofrend ? », sur cofrend.com (consulté le ).
- « Formation et certification END pour le CCPM-Fonderie », sur ctif.com.
- « Precend - Qui sommes-nous ? », sur precend.fr.
- « ECND-PdL », sur ecnd-pdl.fr.
- Stéphane Sainson, Inspection en ligne des pipelines. Principes et méthodes, Éd. Lavoisier, 2007 (ISBN 978-2743009724), 332 p.
- Stéphane Sainson, Les diagraphies de corrosion. Acquisition et interprétation des données, Éd. Lavoisier, 2010 (ISBN 978-2743012014), 547 p.
- (en) American Society for Non Destructive Testing.
- ASTM.
- De l'anglais Eddy current testing.