Polyuréthane
Un polyuréthane ou polyuréthanne est un polymÚre d'uréthane, une molécule organique.
On appelle uréthane, ou plus couramment « carbamate », tout composé produit par la réaction d'un isocyanate et d'un alcool conformément à la réaction suivante :

Cette réaction était connue depuis plusieurs décennies lorsqu'en 1937, Otto Bayer découvrit comment en faire un plastique utilisable, exempt de polyisocyanate et polyol.
Les technologies de l'urĂ©thane ont Ă©tĂ© amenĂ©es aux Ătats-Unis en 1953 par Jean-Pierre Abbat (en) et Fritz Hartmann.
Dans les années 1970, l'utilisation de l'uréthane pour les roues a par exemple révolutionné les sports sur roulettes (patins à roulettes, planche à roulettes). Il se trouve aussi dans certains jouets.
Les polyurĂ©thanes peuvent ĂȘtre fabriquĂ©s avec une grande variĂ©tĂ© de textures et de duretĂ©s en variant les monomĂšres utilisĂ©s et en ajoutant d'autres substances. Ils sont utilisĂ©s pour les colles, peintures, Ă©lastomĂšres (« caoutchoucs »), mousses, fibres. Ainsi, ces plastiques aux vastes applications sont utilisĂ©s dans un grand nombre d'industries.
Principes chimiques des polyuréthanes
Polymérisation en chaßne
Il s'agit d'une rĂ©action chimique conduisant selon un mĂ©canisme radicalaire ou ionique Ă des macromolĂ©cules linĂ©aires ou rĂ©ticulĂ©es Ă partir de composĂ©s vinyliques (ayant une double liaison C=C) ou dâhĂ©tĂ©rocycles comme l'oxyde d'Ă©thylĂšne et le caprolactame. La masse molaire moyenne des macromolĂ©cules ainsi obtenues peut atteindre plusieurs millions de grammes par mole. Le greffage de chaĂźnes latĂ©rales sur les chaĂźnes dĂ©jĂ formĂ©es offre une multitude de possibilitĂ©s, certaines plus intĂ©ressantes que d'autres.
Polymérisation par étapes
Il s'agit du second mécanisme de polymérisation, à cÎté de la polymérisation en chaßne. Il se distingue de ce dernier par un mécanisme d'étapes indépendantes. Il repose sur la réactivité de groupes fonctionnels réagissant ensemble pour former un nouveau groupe qui liera chimiquement les deux bouts de chaßnes. Il existe deux types de polymérisation par étapes, la polycondensation et la polyaddition. La réaction menant à la formation de polyuréthanes fait partie des polymérisations par étapes et plus précisément des polyadditions.
Polycondensation
Il s'agit d'une rĂ©action de polymĂ©risation mettant en Ćuvre des monomĂšres au moins bifonctionnels (diacides, diols, diamines, etc.) pour former des chaĂźnes macromolĂ©culaires, avec dĂ©gagement de molĂ©cules de faible masse molaire (le plus souvent de l'eau).
Polyaddition
La polymĂ©risation par addition regroupe l'ensemble des rĂ©actions de polymĂ©risation mettant en Ćuvre des monomĂšres au moins bifonctionnels conduisant Ă des macromolĂ©cules, sans dĂ©gagement de petites molĂ©cules, contrairement Ă la polycondensation, par exemple les polyurĂ©thanes et polyurĂ©es par rĂ©action de diisocyanates avec des diols ou des diamines, les rĂ©sines Ă©poxyde par rĂ©action de prĂ©-polymĂšres porteurs de fonctions Ă©poxyde (DGEBA par exemple) avec des durcisseurs de type diamine, entrent aussi dans cette catĂ©gorie.
Les groupes isocyanate réagissent avec les alcools pour donner des groupes uréthane stables.
Cette réaction fut découverte par Charles Adolphe Wurtz[1] en 1849.
Pour les matiÚres plastiques et pour les élastomÚres, la formation de polyuréthanes à partir de diisocyanates et d'eau avec dégagement de CO2 a pris une importance toute particuliÚre car les mousses polyuréthanes sont trÚs utilisées au quotidien.
Mais lâĂ©lĂ©ment le plus important du procĂ©dĂ© de polyaddition des diisocyanates est leurs rĂ©actions sur les composĂ©s polyhydroxylĂ©s, car les groupes urĂ©thane ainsi formĂ©s (groupe ester de l'acide carbamique) sont stables. Dans les premiers temps des polyurĂ©thanes, on utilisait des diols de faible masse molaire comme le butanediol et par polyaddition avec le diisocyanate d'hexamĂ©thylĂšne (HDI), on obtenait des polyurĂ©thanes linĂ©aires (fibres polyurĂ©thanes). Dans les polyurĂ©thanes actuels, le groupe urĂ©thane est en fait seulement lâĂ©lĂ©ment de jonction entre les chaĂźnes macromolĂ©culaires. Ce groupe prĂ©sente une stabilitĂ© et une rigiditĂ© exceptionnelle, son Ă©nergie de cohĂ©sion dĂ©passe mĂȘme lĂ©gĂšrement celle de la fonction amide. Ceci explique les excellentes propriĂ©tĂ©s mĂ©caniques des polyurĂ©thanes, mĂȘme si les groupes urĂ©thane ne reprĂ©sentent quâune petite fraction de lâĂ©difice macromolĂ©culaire.
Principales utilisations
D'aprÚs une étude[2] de l'Ademe, l'emploi des polyuréthanes dans le monde se répartit de la façon suivante :
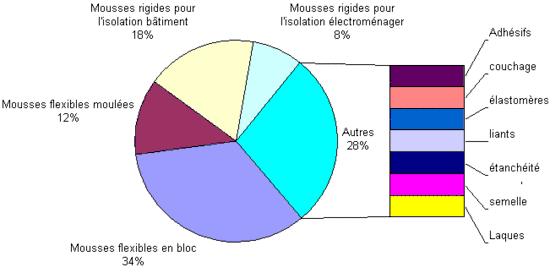
Mousses de polyuréthane
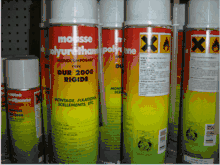
Les mousses flexibles sont particuliĂšrement utilisĂ©es en ameublement (assises des siĂšges et canapĂ©s), les mousses rigides sont intĂ©grĂ©es aux murs rideaux, ou des panneaux d'isolation (panneaux sandwich) utilisĂ©s dans le bĂątiment ou dans l'Ă©lectromĂ©nager (parois de rĂ©frigĂ©rateurs ou des chambres froides par exemple). L'ordre de grandeur de la conductivitĂ© thermique de la mousse de polyurĂ©thane se situe entre 0,023 et 0,028 W mâ1 Kâ1[3].
Sous la forme de mousse expansĂ©e, les mousses de polyurĂ©thanes sont largement utilisĂ©es pour leur qualitĂ© d'isolation thermique, leur adhĂ©rence sur tout support, leur pouvoir de flottaison, leur capacitĂ© Ă remplir les vides quels quâils soient et Ă permettre des emballages sur mesure, lĂ©gers et solides. Les mousses vendues en bombe ont une capacitĂ© d'expansion de l'ordre de 50 litres de mousse par litre de produit. La masse volumique de la mousse obtenue est de l'ordre de 40 kg mâ3.
Au début des années 1970, la mousse de polyuréthane a été utilisée pour construire au Texas un bùtiment expérimental, la TAO Earth House.
Colles
Les polyurĂ©thanes sont Ă la base de la fabrication de colles plus particuliĂšrement pour assembler le bois ou le collage des semelles de chaussures. Lâavantage principal de ce type de colle est sa rĂ©sistance Ă lâeau. La mousse de polyurĂ©thane est aussi un excellent matĂ©riau de collage utilisĂ©e astucieusement dans le bĂątiment en la dĂ©tournant de son usage premier pour par exemple coller des panneaux d'isolation sur des cloisons.
Roues et roulettes
Les polyurĂ©thanes intĂ©grant des ingrĂ©dients anti-abrasion sont utilisĂ©s dans la fabrication de roues et roulettes extrĂȘmement solides (patins Ă roulettes, planche Ă roulettes, caddy, etc.). D'autres variĂ©tĂ©s ont Ă©tĂ© dĂ©veloppĂ©es pour les pneumatiques, et des variantes micro-cellulaires de mousse sont largement utilisĂ©es pour les roues des fauteuils roulants et des bicyclettes mais aussi pour les amortisseurs, silentblocs et pare-chocs.
Ameublement
Le polyuréthane est également employé dans la fabrication de meubles (coussins, assises de siÚges) et pour protéger les bordures des meubles à des fins de sécurité comme de longévité. Certains meubles entiÚrement fabriqués dans cette matiÚre sont célÚbres, comme H5&6 chair, ou à base de mousse polyuréthane parmi d'autres composants comme Tube chair.
Industrie automobile
Que ce soit dans les siĂšges, les appuie-tĂȘtes, les accoudoirs, les volants, les garnitures de pavillons, les tableaux de bord, les tablettes arriĂšre, faux planchers et autres fonds de coffre, les polyurĂ©thanes sont trĂšs employĂ©s dans lâindustrie automobile qui met Ă profit sa diversitĂ© pour ce qui est de la souplesse et de la densitĂ©. L'industrie automobile est Ă©galement trĂšs friande de mousses PU ayant pour rĂŽle l'isolation thermique et acoustique au travers de la fabrication de tapis d'insonorisation ou d'absorbeurs, que ce soit dans l'habitacle ou dans le compartiment moteur. Rigide ou souple, haute ou basse densitĂ©, expansible ou non, facilement renforçable avec la quasi-intĂ©gralitĂ© des fibres naturelles ou synthĂ©tiques du marchĂ© (sauf le PP). Un matĂ©riau Ă©minemment formable par moulage (injection haute ou basse pression, pulvĂ©risationâŠ). L'inconvĂ©nient majeur de ce matĂ©riau rĂ©side dans le fait qu'Ă©tant thermodurcissable, il ne peut pas ĂȘtre recyclĂ© et rĂ©utilisĂ© sous une forme identique. La sociĂ©tĂ© Bayer, par exemple, mais d'autres Ă©galement, le rĂ©injectent sous forme pulvĂ©rulente dans du produit vierge au moment de l'injection. Son coĂ»t le destine la plupart du temps aux vĂ©hicules de milieu et haut de gamme. Les caractĂ©ristiques intrinsĂšques du matĂ©riau lui permettent des mises en Ćuvre sur la base d'investissements qui peuvent aller du trĂšs lĂ©ger au trĂšs lourd selon le type de piĂšce et les cadencements.
Natation
Les premiers modÚles de combinaisons 100 % polyuréthane conçus par la marque italienne Jaked sont apparus en compétition en 2008. Les autres marques, Adidas, Arena, TYR, ont conçu des modÚles similaires, qui, enfilés par les meilleurs nageurs du monde, ont apporté un gain considérable pour ce qui est des performances. Les championnats du monde de Rome 2009 en ont été l'illustration[4]. Ces produits ont été interdits par la Fédération internationale de natation (FINA) à partir du début de l'année 2010.
Décoration
La mousse de polyuréthane est un matériau exceptionnel pour réaliser des éléments de décorations (fausses poutres, décors, sculptures, etc.) qui sont ensuite peints ou recouverts de matiÚre comme le crépi.
Nautisme
Les qualitĂ©s d'Ă©lasticitĂ©, de rĂ©sistance Ă l'humiditĂ© et ses capacitĂ©s de flottaison font du polyurĂ©thane un matĂ©riau fort utilisĂ© dans l'industrie nautique. Ainsi, certaines planches de surf ou planches Ă voile sont construites autour d'un noyau de polyurĂ©thane. Les boudins des cerfs-volants utilisĂ©s pour le kitesurf sont Ă©galement fabriquĂ©s en polyurĂ©thane. De mĂȘme, la coque des bateaux est souvent constituĂ©e de mousse de polyurĂ©thane intĂ©grĂ©e Ă une double peau de fibre de verre.
Dispositifs médicaux : préservatifs, gants chirurgicaux, pansements
De nombreux modĂšles de prĂ©servatifs sont fabriquĂ©s Ă partir du polyurĂ©thane. Ils prĂ©sentent l'intĂ©rĂȘt d'ĂȘtre moins allergĂšnes que le latex tout en prĂ©sentant de parfaits critĂšres de qualitĂ©.
Le polyuréthane constitue aussi la couche externe de certains pansements. En tant que semi-occlusif, il protÚge des micro-organismes ; on le trouve notamment dans les pansements hydrocolloïdes dont la couche interne est quant à elle du carboxyméthylcellulose (CMC). Il constitue aussi les pansements films adhésifs transparents dont on se sert comme pansement primaire, secondaire ou pour la fixation de cathéter. Les pansement hydrocellulaires sont constitués de trois couches de polyuréthane différentes : la couche la plus interne, microperforée en polyuréthane ou parfois en silicone, la couche centrale, en mousse de polyuréthane qui est absorbante, et la couche externe, un film semi-perméable de polyuréthane.
Industrie
Les films de polyuréthane sont utilisés pour protéger de la corrosion, l'abrasion et l'érosion de nombreux types d'équipements (ailes d'avions, trains, automobiles, pales d'éoliennes, etc.).
Textile
PolyurĂ©thane thermoplastique Ă©lastomĂšre, le Lycra (Spandex ou Ălasthanne) est créé par Dupont de Nemours. Sa chaine principale est composĂ©e Ă la fois de groupes urĂ©thane et de groupes urĂ©e. De nombreux vĂȘtements sont fabriquĂ©s Ă base de Lycra dont les propriĂ©tĂ©s extensibles en font un produit trĂšs adaptĂ© aux vĂȘtements de sport.
L'uréthane entre dans la composition des combinaisons spatiales pour fabriquer la couche pressurisée. Il est enduit sur une couche de nylon et recouvert d'une couche de Dacron.
Laques, peintures et vernis
Les polyurĂ©thanes sont largement utilisĂ©s dans les enduits, laques, peintures et vernis que cela soit dans le bĂątiment, l'ameublement, la construction automobile ou la protection du bois. Les vernis des « peintures mĂ©tallisĂ©es vernies » des automobiles sont des polyurĂ©thanes. Les combinaisons polyhydroxylĂ©es avec plus de deux hydroxyles conduisent, avec des polyisocyanates, Ă des macromolĂ©cules rĂ©tifiĂ©es qui sont trĂšs importantes dans le domaine des peintures. De telles combinaisons polyhydroxylĂ©es sont faciles Ă obtenir (exemple : estĂ©rification de diacides avec un excĂšs de polyols). GrĂące aux possibilitĂ©s de variation illimitĂ©es, on peut obtenir des peintures avec tous les degrĂ©s de duretĂ© ou dâĂ©lasticitĂ© voulus.
Réactivité du groupe isocyanate
DâaprĂšs la thĂ©orie de l'orbitale, la densitĂ© Ă©lectronique est la plus Ă©levĂ©e sur lâatome dâoxygĂšne et la plus faible sur lâatome de carbone ; par contre lâatome dâazote avec une charge nĂ©gative donne lieu Ă des formes mĂ©somĂšres. Ainsi lâatome de carbone peut ĂȘtre facilement attirĂ© par un nuclĂ©ophile et lâazote par un Ă©lectrophile.
Les isocyanates rĂ©agissent avec tous les groupes qui disposent dâun atome dâhydrogĂšne mobile (amines, alcools, acides, eau, etc.). En gĂ©nĂ©ral, la vitesse de rĂ©action pour l'addition dâun composĂ© avec un groupe isocyanate est dĂ©terminĂ©e par sa basicitĂ© : plus le composĂ© est basique plus sa vitesse de rĂ©action avec un groupe isocyanate sera importante. La vitesse de rĂ©action diminue dans lâordre suivant :
amines aliphatiques > NH3 > amines aromatiques > urées aliphatiques > alcools primaires > alcools secondaires > eau > urées aromatiques.
Les rapports de vitesse de rĂ©action entre les alcools primaires, secondaires et tertiaires sont environ : 1 / 0,3 / 0,05. Dans la pratique, il est important de travailler autant que possible en absence d'humiditĂ© sinon deux groupes isocyanate rĂ©agissent avec une molĂ©cule dâeau et dĂ©gagent du CO2 en formant des groupes urĂ©e.
Dans un isocyanate RNCO, si R est un groupe donneur dâĂ©lectrons, il exerce une action dĂ©saturante sur le groupe CO, la rĂ©activitĂ© de ce groupe NCO est donc affaiblie. Par contre, si R est un groupe aromatique, le doublet de lâazote est attirĂ© dans le noyau aromatique et la charge positive du carbone sâen trouve augmentĂ©e. Ainsi la rĂ©activitĂ© des groupes isocyanate forme la suite croissante suivante :
tert-butyle- < cyclohexyle- < n-alkyle- < benzyle- < phényle- < para-nitrophényle- < chlorosulfonyle-isocyanate.
Cependant la stabilitĂ© thermique de lâurĂ©thane formĂ© augmente dans le sens inverse.
Polyisocyanates monomĂšres
Les polyisocyanates les plus utilisés dans les peintures et vernis sont des adduits obtenus à partir des principaux diisocyanates mentionnés ci-aprÚs.
- Le diisocyanate de toluĂšne (TDI) vient en tĂȘte de la production mondiale.
Le TDI utilisĂ© est un mĂ©lange des deux isomĂšres ci-dessus (2-4 et 2-6). Ces mĂ©langes ont moins tendance Ă cristalliser que les isomĂšres purs. Le problĂšme de cet isocyanate est quâil a une forte tendance au jaunissement due Ă la prĂ©sence de cycle benzĂ©nique (carbones insaturĂ©s) ; par contre son prix est bas et il rĂ©agit rapidement (sĂ©chage rapide).
- Le diisocyanate d'hexaméthylÚne (HDI) est un diisocyanate industriel purement aliphatique.
Il conduit à des polyuréthanes trÚs stables à la lumiÚre solaire (car la chaßne carbonée est saturée), élastiques et résistants à la saponification et à la chaleur. Par contre il réagit moins vite que le TDI et son prix est plus élevé.
Temps de « séchage »
Pour les laques polyuréthanes, on appelle « temps de séchage » aussi bien le temps mis par le solvant pour s'évaporer que le temps de réaction de groupes NCO sur les groupes OH.
Manipulation, stockage et toxicologie des isocyanates
Les polyisocyanates sont des molĂ©cules trĂšs rĂ©actives dont lâemploi nĂ©cessite quelques prĂ©cautions :
- protection indispensable de la peau et des yeux ainsi que des voies respiratoires en cas dâexposition rĂ©pĂ©tĂ©e ;
- Ă©viter la prĂ©sence et le contact avec lâeau ;
- stockage à 250 °C maximum sous gaz sec et inerte (exemple : argon) si besoin est ;
- Ă©viter toute Ă©tincelle ou prĂ©sence dâĂ©lectricitĂ© statique (risque dâincendie) ;
- nettoyer Ă lâalcool avec un peu dâammoniaque mais pas Ă lâeau ;
- manipuler de préférence sous hotte aspirante ;
- les rĂ©actifs doivent ĂȘtre consommĂ©s dans les 10 Ă 15 jours aprĂšs ouverture ;
- les emballages doivent ĂȘtre refermĂ©s aprĂšs chaque utilisation ;
- dĂšs quâune prĂ©paration est faite, elle doit ĂȘtre utilisĂ©e dans un laps de temps donnĂ© avant sĂ©chage total, appelĂ© « pot life ».
Laques polyuréthanes commerciales
Les entreprises ne commercialisent que des laques polyuréthanes bicomposants, dont il faut faire le mélange avant d'appliquer la laque.
Ce mélange a une durée de vie limitée par le temps de réaction entre ces deux composants (pot life). Ces composants sont :
- 1) un vernis contenant des polymĂšres hydroxylĂ©s (rĂ©sine) : cela peut ĂȘtre un fond, un vernis, une laque ou un apprĂȘt. Les propriĂ©tĂ©s physico-chimiques du film sont essentiellement dues Ă la nature de la rĂ©sine et/ou du liant utilisĂ©. GĂ©nĂ©ralement[5], on distingue trois types de rĂ©sines :
- acryliques hydroxylées
- laques haut de gamme pour la finition des salles de bains ou cuisines
- avantages : trÚs résistantes, transparentes et parfaitement non jaunissantes
- inconvénients : séchage long et prix élevé
- polyesters
- laques destinĂ©es aux finitions qui nĂ©cessitent de bonnes performances mais une rĂ©sistance au jaunissement plus faible (bureau, collectivitĂ©âŠ)
- avantages : assez résistantes, séchage plus rapide et prix plus bas
- inconvénients : résistance au jaunissement plus faible
- alkydes
- ce sont des résines polyesters modifiées à trÚs bas prix pour des gammes low cost
- elles sont de mauvaise qualité mais ont un prix trÚs bas comparé aux autres type de résines
- acryliques hydroxylées
- 2) un rĂ©actif et quelquefois un solvant pour une viscositĂ© plus basse. ConstituĂ© dâun solvant dĂ©shydratĂ© et un ou plusieurs polyisocyanates (TDI ou HDI), ces derniers ont Ă©tĂ© Ă©voquĂ©s prĂ©cĂ©demment.
En jouant sur la nature des parties 1) et 2), on obtient une multitude de combinaisons. Généralement on utilise du HDI pour réticuler une laque acrylique hydroxylée à cause de sa résistance au jaunissement alors que les polyesters sont associés avec des réactifs à base de TDI qui sÚchent plus vite et coûtent moins cher.
Index stĆchiomĂ©trique
En fonction des performances finales souhaitĂ©es, la quantitĂ© de rĂ©actif ne sera pas la mĂȘme. Le rapport [OH] / [NCO] ([OH] signifie concentration en OH) est appelĂ© indice ou index ou encore taux de rĂ©ticulation si la fonctionnalitĂ© moyenne des monomĂšres est supĂ©rieure Ă deux ou si l'indice est supĂ©rieur Ă l'unitĂ© pour un mĂ©lange de monomĂšres bifonctionnels.
- Si cet indice est de 1, on se trouve dans les proportions stĆchiomĂ©triques.
- En dessous, on parle de sous-indexation et le produit n'est pas totalement réticulé ; il peut ainsi s'avérer collant, mou et souple.
- Lorsque l'index est supérieur à l'unité, on parle alors de sur-indexation, ce qui correspond à la majorité des formulations industrielles afin d'éviter une sous-indexation du réseau par consommation des fonctions isocyanate dues à la présence d'eau résiduelle dans la part polyol mais aussi au fait que le titre en fonctions hydroxyle n'est pas toujours connu avec précision.
- Si les performances finales ne sont pas assez élevées, il faut augmenter le taux de réticulation, ce taux peut aller au-dessus de 100 %.
Commerce
En 2014, la France est nette exportatrice de polyurĂ©thane, d'aprĂšs les douanes françaises. Le prix moyen Ă la tonne Ă l'import Ă©tait de 3 600 âŹ[6].
Sécurité incendie et toxicité
Intoxication
La mise en Ćuvre des mousses polyurĂ©thanes entraĂźne des risques importants : le diisocyanate de toluĂšne est trĂšs toxique par inhalation[7], rĂ©actif, irritant et trĂšs volatil ; le diisocyanate de diphĂ©nylmĂ©thane est considĂ©rĂ© comme nocif par inhalation et susceptible de provoquer le cancer[8]. Ces vapeurs se dispersent dans l'atmosphĂšre et sont peu Ă peu neutralisĂ©es par la vapeur d'eau de l'environnement, ce qui contribue Ă la pollution des couches infĂ©rieures de l'atmosphĂšre.
Totalement polymérisés (c'est-à -dire aprÚs la stratification), les produits finis sont physiologiquement inactifs. Toutefois ils peuvent renfermer des résidus de catalyseurs et ainsi dégager des vapeurs d'isocyanates pendant quelques heures voire quelques jours.
Une fois mis en Ćuvre, les polyurĂ©thanes ont une toxicitĂ© trĂšs faible par rapport Ă de nombreux autres matĂ©riaux utilisĂ©s pour l'isolation ou pour le rembourrage des meubles. On peut cependant citer certains risques liĂ©s aux polyurĂ©thanes et aux additifs qu'ils peuvent contenir :
- les additifs polybromodiphĂ©nylĂ©thers (PBDE) - en l'occurrence le pentaBDE pour les polyurĂ©thanes - rĂ©putĂ©s toxiques, qui Ă©taient incorporĂ©s Ă ces mousses jusqu'en 2001 pour leurs propriĂ©tĂ©s ignifuges en cas d'incendie, ne sont plus sur le marchĂ©. Parmi les PBDE, seul le dĂ©caBDE est une substance reconnue comme sĂ»re, mais elle ne peut pas ĂȘtre incorporĂ©e aux mousses de polyurĂ©thane. D'autres retardateurs de flamme bromĂ©s, Ă©valuĂ©s comme sĂ»rs, ont Ă©tĂ© dĂ©veloppĂ©s et sont disponibles sur le marchĂ© pour les applications polyurĂ©thanes ;
- la colle polyuréthane ingérée gonfle dans l'estomac et peut s'avérer mortelle[9] ;
- en cas de combustion, ils dégagent des gaz mortels (cyanure d'hydrogÚne, monoxyde de carbone).
Incendie
Le polyurĂ©thane est un matĂ©riau inflammable. Lors de sa combustion, il dĂ©gage de nombreux gaz mortels, tels le cyanure d'hydrogĂšne et le monoxyde de carbone[10]. Au Royaume-Uni, en Irlande, et dans certains Ătats des Ătats-Unis, la rĂ©glementation oblige les fabricants de meubles rembourrĂ©s (canapĂ©s, matelas) Ă traiter les produits Ă l'aide d'additifs chimiques ignifugeants afin de rĂ©duire ce risque. En France et dans d'autres pays d'Europe continentale, les fabricants de meubles soutiennent les actions d'associations de protection de l'environnement contre les « retardateurs de flammes » et en font un argument pour ne pas utiliser d'additifs ignifugeants. De nombreux domaines d'utilisation des mousses de polyurĂ©thane exigent des propriĂ©tĂ©s « non-feu ». Dans l'automobile, les mousses et complexes doivent ĂȘtre classĂ©s par rapport Ă la norme D45 1333 ou FMVSS 302. Ces normes exigent une vitesse de combustibilitĂ© infĂ©rieure Ă 100 mm minâ1. Dans le domaine du bĂątiment, pour les lieux publics, les mousses doivent ĂȘtre traitĂ©es non feu. Un classement spĂ©cifique existe qui est le classement M1 selon la norme NF P92-501[11] - [12]. L'utilisation de cet isolant fait l'objet d'une aggravation du risque incendie pour les assureurs. UtilisĂ© dans un bardage mĂ©tallique, il dĂ©gage un acide en cas d'incendie qui dĂ©truit le bardage mĂ©tallique et nuit Ă la soliditĂ© de la structure du bĂątiment[13].
Notes et références
- isimabomba.free.fr, Charles Adolphe Wurtz
- Ătude de l'Ademe concernant le polyurĂ©thanne et ses utilisations
- (en) U. Jarfelt et O. RamnĂ€s, « Thermal conductivity of polyurethane foam - best performance », 10th International Symposium on District Heating and Cooling « Sektion 6 a: Heat distribution â pipe properties »,â 3-5 septembre 2006 (lire en ligne [PDF], consultĂ© le ).
- Bains Romains, sur Le Monde.fr (consulté le 30 juillet 2009)
- source Valspar
- « Indicateur des échanges import/export », sur Direction générale des douanes. Indiquer NC8=39095090 (consulté le )
- Fiche de toxicité, INRS
- Fiche de toxicité, INRS
- [PDF] Fiche de sécurité d'un fabricant de colle, sur toutcoller.com
- « ArrĂȘtĂ© du 21 novembre 2002 relatif Ă la rĂ©action au feu des produits de construction et d'amĂ©nagement », sur LĂ©gifrance (consultĂ© le ).
- « Norme NF P92-501 », sur Afnor (consulté le ).
- Note de la SCOR sur les panneaux sandwitch[PDF].
Liens externes
- Portail d'information sur le polyurĂ©thane, site dâinformation de lâindustrie dĂ©crivant les utilisations et atouts du polyurĂ©thane
- (en) Polyurethane synthesis
- Détails chimie