Adsorption par inversion de pression
L'adsorption par inversion de pression, appelée aussi adsorption à pression modulée (APM) ou PSA (acronyme de l'anglais Pressure Swing Adsorption) est un procédé de séparation de mélanges de gaz au cours duquel ont lieu alternativement l’adsorption d’un gaz par un solide ou un liquide à une pression donnée, puis sa désorption à une pression plus faible[1].
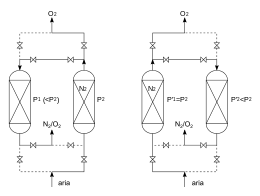
Il consiste à retirer un gaz d'un mélange gazeux, en utilisant son affinité chimique et ses caractéristiques particulières vis-à -vis d'un matériau solide, l'adsorbant exposé à une oscillation de pression rigoureusement contrôlée. Une adsorption sélective se produit grâce à des capacités d'équilibre différentes (adsorbant d'équilibre) ou par des différences dans les taux d'absorption (adsorbant cinétique)[2].
Selon le gaz à retirer, l'adsorbant change : les zéolithes, le charbon actif ou d'autres tamis moléculaire sont utilisés.
Le procédé a connu un développement industriel important à la fin du XXe siècle, notamment dans le retrait du CO2 dans l'étape finale de la synthèse de hydrogène, dans le raffinage du pétrole. C'est la technique la plus utilisée pour purifier l'hydrogène et elle correspond (au début des années 2000) à 20-30 % des coûts d'une unité de reformage[3].
Procédé
Histoire
Le développement de l'adsorption par inversion de pression débute dans les années 1930. Les premiers travaux sur le sujet sont brevetés par Finlayson et Sharp (de British Celanese Limited)[4], Hasche et Dargan[5] et Perley[6]. Mais après ces brevets, le développement de la technologie est lent. Dans les années 1950, de nouvelles recherches sont entreprises. En 1960, C. W. Skarstrom (Esso) dépose un brevet[7], et en 1964, P. Guerin de Montgareuil et D. Domine (Air liquide) font de même[8].
Cette technologie suscite l'intérêt des chercheurs à la fin des années 1970, lorsque le nombre de publications et de brevets augmente significativement (de quelques papiers par an à plusieurs dizaines). Actuellement, la recherche se concentre sur l'utilisation de nouveaux adsorbants (principalement les zéolithes), et l'amélioration de l'automatisation (pour avoir des cycles de plus en plus complexes et plus rapides).
Principe
L'adsorption par inversion de pression exploite le fait que, sous pression, les gaz ont tendance à être attirés par les solides, ou « adsorbés ». Plus la pression est élevée, plus le phénomène est important. Lorsque la pression diminue, le gaz se libère, ou se « désorbe ». De même, la quantité de gaz adsorbé dépend de sa nature chimique. Ainsi, en combinant ces deux propriétés, on peut privilégier la capture d'un gaz alors qu'il est mélangé avec d'autres, et le libérer en diminuant la pression.
Par exemple, si on comprime (entre 6 et 10 bars) de l'air dans un réservoir contenant des granulés de zéolithe qui attirent l'azote plus que l'oxygène, l'air sous pression qui s'échappera du réservoir sera plus riche en oxygène, puisque son azote a été fixé par les zéolithes. On peut ainsi obtenir un air riche en oxygène en faisant passer de l'air comprimé dans ce réservoir. Mais au bout d'un moment, les zéolithes seront saturées en azote. On doit alors les régénérer en faisant circuler de l'air sous basse pression dans le réservoir : celui-ci sortira en emportant l'azote. Le cycle peut alors recommencer indéfiniment. Ce procédé est aussi utile pour produire un air enrichi en oxygène (les générateurs d'oxygène portables utilisés pour les patients atteints de bronchopneumopathie chronique obstructive fonctionnent sur ce principe) que pour produire une atmosphère inerte.
Il arrive souvent que plusieurs réservoirs d'adsorbants soient associés pour avoir un débit continu de gaz. Par ailleurs, l'énergie pneumatique de la décompression peut être réutilisée pour aider la compression : il s'agit une pratique courante dans les applications industrielles.
Adsorbants
Outre leur propriété chimique, caractérisée par leur capacité à sélectionner un gaz, les adsorbants utilisés dans les PSA sont généralement des matériaux très poreux présentant une grande surface spécifique. Le charbon actif[9], le gel de silice, l'alumine activée (principalement utilisée dans les procédés de désulfuration[10]) et les zéolithes sont couramment utilisés. Étant donné que le gaz adsorbé forme une pellicule d'une ou quelques molécules d'épaisseur, plusieurs centaines de mètres carrés de surface spécifique par gramme de matière sont nécessaires pour obtenir une adsorption significative vis-à -vis du matériau utilisé.
En plus de leur sélectivité chimique pour certains gaz, les zéolithes et certains types de charbons actifs (les charbons tamis moléculaires) peuvent profiter de leur porosité très fine pour exclure les plus grosses molécules, que leur taille ne permet pas de pénétrer dans les cavités.
Enfin, il est possible d'empiler plusieurs strates d'adsorbants dans un réservoir afin d'additionner leur effets[10]. Par exemple, une première couche (tel que vu de l'entrée du réservoir) est souvent un gel de silice, adsorbant efficace vis-à -vis de l'eau et des hydrocarbures. La couche suivante est du charbon actif, adsorbant l'eau, le dioxyde de carbone et le méthane. À la sortie de la cuve se trouve une couche de zéolithe, qui adsorbe le monoxyde de carbone et d'autres impuretés. Avec un tel empilement, l'hydrogène n'est pas adsorbé.
Utilisations
La PSA est une technologie polyvalente, car il y est possible d'agir sur plusieurs variables : le type de matériau adsorbant et sa quantité, le type et la séquence des étapes du cycle, la durée des étapes, les pressions opératoires, la taille des colonnes et l'utilisation d'un seul ou de plusieurs lits[11].
Applications industrielles
Une application courante de l'adsorption par inversion de pression réside dans le retrait du dioxyde de carbone, comme étape finale de la production industrielle de dihydrogène (H2), pour son utilisation dans les raffineries de pétrole et dans la production d'ammoniaque (NH3). Les raffineries utilisent aussi souvent ce procédé pour retirer le sulfure d'hydrogène (H2S) de leur alimentation en hydrogène, et pour permettre le recyclage de leurs gaz issus des unités d'hydrodésulfuration et d'hydrocraquage.
Une autre application du procédé est l'épuration du biogaz pour retirer son dioxyde de carbone (après le traitement classique visant à diminuer le taux de contaminants tels que sulfure d'hydrogène, ammoniac, oxygène, azote, particules solides entraînées, microbes, siloxanes qui constituent habituellement moins de 4 % du volume du biogaz)[11]. En abaissant le taux de CO2 (qui constitue 40% du biogaz en moyenne) à moins de 3 % en volume, il permet d'augmenter la teneur en méthane (CH4) au point de produire du biométhane. L'équipement est compact, économe en énergie sûr et au fonctionnement simple et suffisamment bon marché pour qu'il soit adapté aux petites installations[12]et pour faire du biogaz une alternative valable au gaz naturel (dont la teneur en CO2 ne dépasse pas 3 %). Le biométhane peut alors servir de carburant de véhicules ou être injecté dans le réseau de gaz[11]. Son inconvénient était qu'il restait concurrencé par le lavage à l'amine et qu'il restait dans le CO2 extrait assez de méthane pour imposer un traitement supplémentaire afin de ne pas rejeter ce méthane résiduel dans l'atmosphère.
Un nouveau procédé de séparation a été récemment proposé (2016-2017) permettant un flux de CO2 presque pur (CO2> 99 %) en utilisant de la zéolite 5A comme adsorbant, dans deux unités PSA, la seconde complétant l'épuration faite dans la première en y renvoyant le CH4 résiduel[11]. La consommation d'énergie est de 1250 kJ par kg de biométhane (soit 550 kJ/Nm3 de biogaz)[11].
Le procédé est aussi utilisé en étape finale de la purification de l'hélium de 90 % à 99,995 %, après son extraction par distillation fractionnée du gaz naturel. L'adsorbant utilisé est du charbon actif[13]. L'ensemble du process se déroule à basse pression, donc dans un VSA, et à basse température[14].
L'adsorption par inversion de pression est aussi utilisée dans la sidérurgie pour retirer le CO2 des gaz produits. Dans les procédés de réduction directe, on peut ainsi améliorer le potentiel réducteur des gaz recyclés : quelques usines utilisant le procédé Midrex l'utilisent déjà . Le CO2 retiré peut être alors valorisé ou séquestré en sous-sol, de manière à limiter les émissions gaz à effet de serre. Des études cherchent à étendre l'adsorption de CO2 au haut fourneau (procédé ULCOS) ou à d'autres procédés de réduction directe comme le procédé Finex (en)[15].
La production de propène par la déshydrogénation du propane est réalisée par un adsorbant qui privilégie l'adsorption de méthane et d'éthane à celle de l'hydrogène[16] ;
La capacité des systèmes d'adsorption par inversion de pression à absorber le CO2 est bien adaptée à la capture de ce gaz à effet de serre avec sa séquestration géologique. L'adaptation de ce système est envisagée sur les centrales thermiques au charbon[17].
Modules compacts
L'utilisation d'adsorbants abouti des technologies économiques et compactes. Ils permettent l'obtention de gaz moins purs, et dans des quantités plus faibles, que les techniques cryogéniques de distillation fractionnée, mais souvent très suffisantes pour l'utilisateur.
La production d'oxygène ou d'azote de pureté « raisonnable » à partir d'air est facile avec des modules compacts. Comme les réservoirs sous pressions sont très contraignants à l'utilisation, surtout lorsqu'il s'agit d'oxygène, on utilise volontiers des petits générateurs PSA d'oxygène pour des applications médicales dans des endroits inaccessibles.
La production d'azote pur (jusqu'à 99,9995 %) à partir d'une source d'air comprimé est possible. Généralement, l'adsorption par inversion de pression est compétitive dans des gammes de débits et de pureté intermédiaires :
- pour l'azote : de 100 Nm3/h à 99,9 % de pureté, à 9 000 Nm3/h à 97 % de pureté ;
- pour l'oxygène : jusqu'à 1 500 Nm3/h avec une pureté comprise entre 88 % et 93 %[18]
La génération d'un gaz inerte dans la lutte contre l'incendie, où d'autres moyens (eau, poudre, mousse, etc.) ne peuvent pas être utilisés, comme dans les centres de données, peut être également assurée par des adsorbeurs.
L'adsorption par inversion de pression a été également évoquée comme une alternative future aux absorbants non régénératifs de CO2 et H2O des Primary Life Support System intégrés aux combinaisons spatiales. Cette technologie peut en effet augmenter l'autonomie sans alourdissement excessif[19]
Variantes
Adsorption en deux étapes
Cette variante (Double Stage PSA ou Double Step PSA pour les anglophones) permet par exemple la fabrication d'azote ou de biométhane très pur. Pour l'azote, elle consiste à faire passer l'air comprimé dans un premier tamis moléculaire en carbone pour obtenir de l'azote d'une pureté d'environ 98 % ; la deuxième étape consiste à faire passer cet azote dans un second tamis moléculaire en carbone pour lui faire atteindre une pureté finale de 99,888 %. Le gaz de purge de la deuxième étape est recyclé et sert de complément à l'air entrant dans la première étape. La purge est en outre aidée par une extraction active pour améliorer la performance du cycle suivant.
Bien entendu, le principe est généralisable à tous les gaz et adsorbants, et les étapes peuvent être multipliées lorsque la pureté finale le requiert, ou lorsque l'adsorbant est insuffisamment efficace.
Adsorption rapide (ou Rapid PSA)
L'adsorption par inversion de pression rapide est fréquemment utilisée dans les modules compacts de production d'oxygène. On peut ainsi diminuer significativement la quantité d'adsorbants lorsque la pureté n'est pas importante et que le gaz alimentant le système peut être gaspillé[20]. Le principe consiste à détendre brièvement la pression d'un côté tout en injectant le gaz à traiter (ici l'air) à l'autre extrémité : le gaz traité (riche en oxygène) est extrait, mais l'extraction est stoppée avant que le gaz injecté (qui s'est chargé en azote) arrive à la sortie. La compression est recommencée, et la détente suivante se fait dans le sens inverse[21].
Adsorption aidée par le vide (VSA ou VPSA)
Dans cette variante du procédé, on distingue le VSA (acronyme de Vacuum Swing Adsorption) dont toutes les phases se déroulent à pression inférieure ou égale à l'atmosphère, du VPSA (de Vacuum Pressure Swing Adsorption), qui passe alternativement d'une pression inférieure à une pression supérieure à l'atmosphère. Ces variantes sont courantes dans les applications industrielles. Elle consiste à augmenter l'efficacité des adsorbants en réalisant l'adsorption à très basse pression. Des installations de création de vide étant nécessaires[note 1], ce procédé se justifie lorsqu'il faut minimiser la quantité d'adsorbants.
Ce procédé présente d'autres avantages, comme la possibilité de travailler sans compresseur (la pression haute étant la pression atmosphérique), l'absence de condensats créés par la compression et, dans beaucoup de cas, de travailler dans un domaine de pression où les adsorbants sont plus efficaces. Des économies d'énergie allant jusqu'à 50 % ont été constatées par rapport aux systèmes classiques.
Notes et références
Notes
- Il faut donc prendre en compte l'investissement dans ces installations de création de vide. Mais celles-ci ne réclament pas de remplacements systématiques, comme les adsorbants, qui s'érodent à force de bouger lors des cycles de compression/décompression. Par contre, les fuites dans un système en dépression sont beaucoup plus difficiles à déceler pour un observateur extérieur que celles sur un système en surpression : les VPSA sont donc plus exigeants en maintenance.
Références
- Vocabulaire de la chimie et des matériaux, Termes, expressions et définitions publiés au Journal officiel, FranceTerme, 2018
- Ruthven D.M (1984) Principles of adsorption and adsorption processes. John Wiley & Sons
- Myers, D. B., Ariff, G. D., James, B. D., Lettow, J. S., Thomas, C. E., & Kuhn, R. C. (2002). Cost and performance comparison of stationary hydrogen fueling appliances. The Hydrogen Program Office.
- (en) Donald Finlayson et Alfred John Sharp, « Improvements in or relating to the treatment of gaseous mixtures for the purpose of separating them into their components or enriching them with respect to one or more of their components (Patent GB 365092 A) »,
- (en) Rudolph Leonard Hasche et William H. Dargan, « Separation of gases (patent US 1794377 A) »,
- (en) George A. Perley, « Method of making commercial hydrogen (patent US 1896916 A) »,
- (en) C. W. Skarstrom, « Method and apparatus for fractionating gaseous mixtures by adsorption (patent US 2944627 A) »,
- (en) P. Guerin de Montgareuil et D. Domine, « Process for separating a binary gaseous mixture by adsorption (patent US 3155468 A) »,
- Gao, S., Ge, L., Rufford, T. E., & Zhu, Z. (2017). The preparation of activated carbon discs from tar pitch and coal powder for adsorption of CO2, CH4 and N2. Microporous and Mesoporous Materials, 238, 19-26.
- [PDF](de) Michael Walter, « Druckwechseladsorption als Wasserstoffreinigungsverfahren für Brennstoffzellen-Systeme im kleinen Leistungsbereich »,
- R. Augelletti, M. Conti et M.C. Annesini, « Pressure swing adsorption for biogas upgrading. A new process configuration for the separation of biomethane and carbon dioxide », Journal of Cleaner Production, no 140,‎ , p. 1390-1398 (lire en ligne).
- Delgrado, J. A., M. A. Uguina, J. Sotelo, B. Ruiz and J. Gomez. 2006. “Fixed bed adsorption of carbon dioxide/ methane mixtures on silicalite pellets.” Adsorption 12:5–18
- (en) Clifford A. Hampel, The Encyclopedia of the Chemical Elements, New York, Reinhold Book Corporation, , 849 p. (ISBN 0278916430 et 9780278916432), p. 258
- (en) « How helium is made »,
- [PDF](en) Stanley Santos, « CO2 Capture in the Steel Industry: Review of the Current State of Art »,
- (en) « Propylene Production via Propane Dehydrogenation, Technology Economics Program », Intratec, deuxième trimestre 2012 (ISBN 9780615661025)
- (en) Carlos A. Grande et Simone Cavenati, « Pressure Swing Adsorption for Carbon Dioxide Sequesteration », dans 2nd Mercosur Congress on Chemical Engineering,
- [PDF]Air Products and Chemicals, Inc, « Systèmes de production de gaz PRISM® »,
- (en) Alptekin Gokhan, « An Advanced Rapid Cycling CO2 and H2O Control System for PLSS », NASA,
- (en) S. W. Chai, M. V. Kothare et S. Sircar, « Rapid Pressure Swing Adsorption for Reduction of Bed Size Factor of a Medical Oxygen Concentrator », Industrial & Engineering Chemistry Research, vol. 50, no 14,‎ , p. 8703 (DOI 10.1021/ie2005093)
- (en) Douglas M. Ruthven, Shamsuzzman Farooq et Kent S. Knaebel, Pressure Swing Adsorption, Wiley-VCH, (ISBN 9780471188186)