Usine d'agglomération
Une usine d'agglomération est une installation sidérurgique servant à fritter le minerai de fer pour le rendre apte à l'utilisation dans le haut fourneau. Le minerai de fer est tout d'abord mélangé avec de la castine et un combustible solide bon marché (houille, rebuts de coke). L'opération d'agglomération proprement dite consiste à brûler le combustible pour atteindre la température de frittage du minerai. Le produit obtenu, appelé « aggloméré », a une composition chimique, une porosité et une tenue mécanique compatibles avec le fonctionnement du haut fourneau.
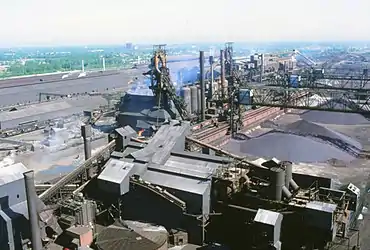
Pour le haut fourneau, l'usine d'agglomération a donc un rôle semblable vis-à -vis du minerai de fer, à celui de la cokerie vis-à -vis du charbon[note 1]. L'agglomération permet également de recycler de nombreux résidus ferreux mais, paradoxalement, il s'agit souvent de l'installation émettant le plus de rejets atmosphériques d'un complexe sidérurgique.
On trouve aussi des installations d'agglomération de minerais non ferreux, dédiées aux minerais de zinc[2], de plomb[3], de cuivre[4]… Si elles sont de taille bien plus modeste que celles de la sidérurgie, leur fonctionnement et leur intérêt sont identiques.
Historique
.JPG.webp)
Dans la plupart des pays, comme la Russie, la France et l'Allemagne, les gisements de minerai de fer se présentent sous une forme poussiéreuse ou sableuse. Sous cette forme, le minerai ne peut pas être chargé dans le haut fourneau car il serait alors, soit emporté par le vent qui y est insufflé, soit fritté en une couche imperméable. L’intérêt de la calcination des minerais avait été compris dès la mise au point des premiers bas fourneaux, et plusieurs procédés sont alors développés. La méthode primitive, consistant à pratiquer un grillage[note 2] en meule, est abandonnée vers la fin du XIXe siècle à cause de sa trop grande dépense en combustible[L 1] - [5]. Les fours à réverbère, et surtout les fours à cuve, les remplacent alors. Ces derniers ont un bon rendement, à la fois grâce au confinement de la réaction et grâce au fonctionnement à contre-courant (les matières solides descendent et les gaz montent)[L 2].
Ces fours à griller le minerai étaient alors des cuves inspirées des hauts fourneaux et des fours à chaux et étaient des outils peu productifs[4] - [L 3]. Le procédé Greenawald, qui en automatise le principe[6], connait vers 1910 un certain développement en permettant la production de 300 000 tonnes annuelles[7].
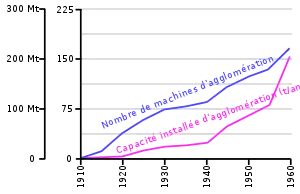
Au début du XXe siècle apparaissent des procédés continus, comme le procédé Smidth utilisant un four en forme de tambour tournant dont la longueur approchait 100 m[SF 2]. Ces procédés disparaissent avec la mise au point d'un procédé continu de calcination sur grille par Arthur Smith Dwight (1864 - 1946)[8] et Richard Lewis Lloyd, qui travaillent ensemble dans la mine de cuivre de Cananea, au nord du Mexique. Leur première machine est commence ses essais en 1906 sur des minerais de cuivre et de plomb[4]. Ceux-ci déposent alors conjointement une série de brevets, dont celui du concerne plus particulièrement :
« un appareil dédié à la calcination et à l'agglomération des minerais [consistant] en un mécanisme dont l'élément portant et déplaçant le minerai est une série de sections connectées par des liaisons flexibles de manière à former un convoyeur à chaîne sans fin, se déplaçant dans un plan vertical[9]. »
— A. S. Dwight & R. L. Lloyd, brevet du 3 juin 1907
Les deux inventeurs fondent en 1907 la Dwight and Lloyd Metallurgical Company. Ils construisent de nombreuses machines et vendent des licences dans le monde entier, dont notamment au constructeur d'usines allemand Lurgi (de). La première machine d'agglomération utilisant le procédé Dwight-Lloyd (de) et dédiée au minerai de fer est construite en 1910 aux États-Unis[4]. En Allemagne, Bochumer Verein (de) l'adopte dès 1917, alors que la première chaîne d'agglomération française, à Fontoy, est datée de 1952[SF 3] - [note 4].
L'agglomération du minerai met une trentaine d'années pour se généraliser dans la sidérurgie. Alors qu'avant la Seconde Guerre mondiale, elle ne servait essentiellement à reconditionner les fines de minerai, elle s'est généralisée après 1945 au traitement des minerais crus. Actuellement son rôle est essentiel car elle permet de mélanger plusieurs minerais entre eux, et surtout d'y incorporer des déchets minéraux plus ou moins riches en fer. Ce rôle de recyclage améliore la rentabilité et limite les déchets des complexes sidérurgiques, qui génèrent de nombreux résidus riches en fer (laitiers, boues, poussières, etc.)[4].
À partir de 1965, en Europe, les minerais locaux sont progressivement abandonnés au profit des minerais riches importés. Les complexes sidérurgiques en bord de mer se développent et utilisent des minerais en provenance de 6 à 10 origines. Les minerais importés ont une structure chimique hétérogène et il est nécessaire de les homogénéiser, de façon à alimenter le haut fourneau avec une charge à peu près constante dans le temps. Les parcs d'homogénéisation qui sont apparus en Allemagne, se généralisent en Europe et au Japon, et plus tardivement, vers 1975, aux États-Unis. Cette homogénéisation chimique précède l'homogénéisation physique réalisée par le procédé d'agglomération lui-même[11].
Procédé
Opérations préliminaires à l'agglomération
Les minerais sont amenés depuis leur zone de stockage et distribués par un stacker, une énorme sauterelle qui va constituer un long tas d'homogénéisation, en forme de prisme. En faisant des va-et-vient le long du tas, le stacker répartit les minerais en couches qui s'empilent sur chaque côté du tas[11].
Ensuite, une excavatrice à godets (ou reclaimer), gros engin doté d'une roue-pelle capable d'excaver environ 1 200 t/h, reprend le minerai constituant le tas d'homogénéisation. Le minerai est repris en taillant verticalement dans le tas[11] - [note 5]. L'engin de reprise peut adopter différentes configuration : la roue-pelle peut être au bout d'un bras (comme dans une excavatrice à godets de mine), sur une structure en portique enjambant le tas,… On peut aussi utiliser des reclaimers doté de chaînes à godets.
- Un stacker en train de constituer un tas homogénéisation dans une mine. En arrière-plan, une excavatrice à godets en attente.
- Une excavatrice à godets sur chenilles. Sur les parcs d'homogénisation, l'excavatrice roule généralement sur des rails.
- Usine d'agglomération et hauts fourneaux d'Esch-Belval, au Luxembourg. On distingue, derrière les tas de stockage, deux tas d'homogénéisation, celui de gauche étant en train d'être repris par un reclaimer horizontal, en forme de portique de manutention.
- Reclaimer horizontal fonctionnant avec une chaîne à godets. Les deux structure triangulaire sont des herses. Un tel reclaimer fonctionne dans les deux directions.
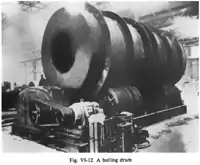
Le minerai homogénéisé est alors mélangé avec des fondants comme l'olivine[note 6] et la castine, ainsi qu'un combustible solide, généralement de la houille. Ces composants sont alors soigneusement mélangés, généralement dans des tambours de mélange, puis agrégés en petites boulettes, généralement à l'aide d'un tambour de nodulation.
Toutes ces manutentions représentent un aspect essentiel de l'intégration de l'usine dans un complexe sidérurgique : « une installation de préparation de la charge (criblage, concassage) exige beaucoup de place et des manutentions importantes. Sur un espace nouveau, l’installation peut être rationnellement conçue et les manutentions réduites. Par contre, les usines existantes n’ont pas été prévues pour ce type d’extension et, par conséquent, il faut installer les agglomérations soit à assez grande distance des hauts fourneaux, soit dans des espaces restreints et peu adéquats. » Dans les années 1950, cette contrainte a souvent alimenté les arguments en faveur de la construction de complexes sidérurgiques neufs contre la modernisation des sites existants[12].
À ce stade, l'agglomération en boulettes de quelques millimètres de diamètre est très distincte du frittage qui est réalisé ultérieurement sur la chaîne d'agglomération : la cohésion est essentiellement réalisée grâce à de l'eau et de la chaux dosées dans le mélange.
Agglomération
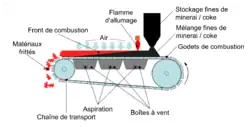
Le minerai est déposé sur la chaîne en deux couches superposées. L'épaisseur de la couche inférieure, qui protège les grilles et sert de filtre, varie entre 30 et 75 mm. Cette couche est généralement constituée de minerai déjà aggloméré : une granulométrie comprise entre 12 et 20 mm est généralement choisie. La couche supérieure consiste en un mélange homogène, essentiellement constitué de minerai, de combustible et de castine, dont l'épaisseur varie entre 350 et 660 mm. L'homogénéité chimique et la granulométrie de ce mélange sont garanties par les tambours d’homogénéisation et de nodulation.
Cette préparation passe alors sous la hotte d’allumage, consistant en une rangée d'une quinzaine de brûleurs qui mettent le feu au combustible présent dans la couche supérieure. Fréquemment, une deuxième rangée de brûleurs permet de maîtriser l’homogénéité et l'évolution de la température.
Le front de combustion se propage alors vers le bas, attisé par l'aspiration d'air qui se fait de haut vers le bas : le procédé est donc similaire à la combustion du tabac dans une pipe. La puissance d'aspiration est donc, tout comme la surface de la chaîne, un élément essentiel définissant la capacité de production de l'installation. Les fumées aspirées sous la partie active de la chaîne, très chargées en poussière de minerai, sont dépoussiérées. Le recyclage des poussières collectées dans toute l'installation est essentiel, car il peut concerner jusqu'à 60 % du produit déposé sur la chaîne.
La température visée au moment de la combustion doit permettre le frittage du minerai. Dans le cas de l'agglomération du minerai de fer, on vise généralement une température comprise entre 1 150 et 1 250 °C dans la zone de combustion, et entre 900 et 1 000 °C dans la zone brûlée pour éviter un refroidissement trop brutal de la couche agglomérée.
Arrivée à l'extrémité de la chaîne, la couche agglomérée se brise en tombant. Un broyeur brise les blocs en petits morceaux, puis le produit est refroidi à l'air, sur un refroidisseur généralement circulaire. Les morceaux d'aggloméré sont alors criblés : les morceaux inférieurs à 5 mm retournent dans le processus d'agglomération (ces « fines de retour » représentent, en moyenne, un quart de la production de la chaîne[13]), les morceaux plus gros, entre 5 et 12 mm, voire parfois 20 mm, sont envoyés au haut fourneau.
- Hotte d'allumage en début de chaîne d'agglomération.
- Chariot de chaîne d'agglomération, exposé à l'usine d'agglomération de Hüttenwerke Krupp Mannesmann (de).
- Refroidisseur circulaire pour le minerai de fer aggloméré.
Stratégies actuelles
Amélioration des caractéristiques physiques
Le coke, combustible essentiel des hauts fourneaux, étant coûteux, la calcination des minerais est effectuée dans une installation dédiée consommant un combustible meilleur marché comme de la poussière de coke ou du charbon[note 7]. La calcination permet, entre autres, le séchage, la décarbonatation de la gangue calcaire des minerais, le grillage des sulfures éventuellement présents (pyrite), et la déshydratation des argiles ou du gypse[10] - [SF 5].
Type de minerai | Minerai cru : coke au haut fourneau |
Minerai aggloméré : coke au haut fourneau |
Minerai aggloméré : coke au haut fourneau + combustible à l'agglo |
---|---|---|---|
Minette lorraine | 1 100 | < 600 | 820 |
Minerai de fer riche | 750 - 800 | 500 | 500 |
Cette opération permet d'augmenter la teneur en fer dans le matériau aggloméré. Quant au coke économisé au haut fourneau, il est, à volume de four donné, avantageusement remplacé par du minerai, ce qui dope la productivité du four. Le frittage du minerai rehausse sa température de ramollissement. La charge reste donc plus longtemps granulaire avant de fondre, ce qui améliore la perméabilité du haut fourneau. Il devient alors possible de construire des hauts fourneaux de grande taille, plus adaptés aux contraintes économiques de la sidérurgie[10].
Amélioration des caractéristiques chimiques
Le procédé d'agglomération est un moyen de maîtrise de la composition du laitier de haut fourneau. En effet, l'utilisation d'un minerai donnant un laitier infusible aboutirait à un engorgement rapide du haut fourneau. L'ajout de castine permet aussi d'obtenir un laitier basique qui favorise la désulfuration de la fonte.
Historiquement, l'agglomération était un procédé permettant de reconditionner les particules fines de minerai qui auraient colmatés les hauts fourneaux si elles avaient été chargées telles qu'elles. La capacité du procédé à éliminer les éléments indésirables comme le soufre a été identifiée très tôt : le procédé d'agglomération sur chaîne élimine 80 à 95 % du soufre présent dans le minerai et ses additifs[4]. C'est également un moyen de se débarrasser du zinc élément « empoisonnant » les hauts fourneaux, car sa température de vaporisation, de 907 °C, correspond à celle d'un grillage bien mené[L 4] - [note 8]. Il est aussi possible de brûler des éléments combustibles mélangés aux minerais, ainsi que d'augmenter le degré d'oxydation du fer (par transformation de la magnétite en hématite). En effet, bien que cette opération paraisse a priori contraire à ce qu'on cherche à faire dans un haut fourneau, il est préférable de réaliser la chauffe et la réduction du minerai dans des étapes distinctes[15].
Recyclage
Le combustible de la chaîne d'agglomération est du poussier de coke. Celui-ci est en effet inutilisable au haut fourneau où il serait soufflé instantanément par le vent. En 1961, on estime le gain complet (productivité au haut fourneau et gain combustible) lié à l'agglomération de minerai de fer à 100 FF par tonne de fonte[12].
Enfin, en étant une usine de conditionnement de minerais, l'usine d'agglomération permet donc de mélanger des minerais très différents, et d'y intégrer des sous-produits de la fabrication de l'acier riches en oxydes de fer, comme les poussières et les boues issues du dépoussiérage des gaz de haut fourneau ou de convertisseur, les boues de haut fourneau et d'aciérie, les laitiers, les battitures et la calamine récupérées au laminage.
Évolutions en cours
En 2020, on dénombre 150 usines d'agglomération dans le monde[16].
Installation dédiée au recyclage, l'usine d'agglomération est, paradoxalement, une installation polluante qui rejette une grande quantité de poussières (50 % des poussières émises par un complexe sidérurgique intégré) contenant des dioxines. Les fumées aspirées sous la chaîne sont soigneusement dépoussiérées et les poussières recyclées dans le procédé. Mais l'efficacité des filtres électrostatiques utilisés dépend beaucoup des conditions du procédé, en particulier de la température des fumées. Avec la mise au point de filtres à manches de grande taille, les normes de rejets évoluent. Il est en effet possible de descendre sous les 1–15 mg/Nm3 dans le cas du filtre à manches, alors qu'on n'atteint que 20–40 mg/Nm3 dans le cas d'un électrofiltre conçu et exploité de manière à atteindre ces valeurs. Quant aux émissions de SO2 ou de NOx, elles peuvent être limitées par l'addition de réactifs dans la charge agglomérée ou dans les fumées[17].
Malgré ces émissions, la pollution émise par les usines d'gglomération reste plus tolérable que celle issue d'autres industries. Par exemple, les deux cheminées de l'usine d'agglomération de Duisbourg-Schwelgern (de), ou celle de Katowice (en), qui atteignent de 250 m, constituent un record alors que de telles hauteurs sont bien plus courantes dans les centrales thermiques ou les fonderies de cuivre. Dans tous les cas, l'augmentation de capacité des filtres reste la solution privilégiée[18].
- De droite à gauche : bâtiment de la chaîne d'agglomération, filtre électrostatique, bâtiment des ventilateurs et cheminée. Usine d'agglomération de Teesside Steelworks (en) en Angleterre.
- L'usine sidérurgique de Katowice (en) est dominée par la cheminée de l'usine d'agglomération, qui culmine à 250 m.
Notes et références
Notes
- L'anthracite, qui est un charbon de haute qualité, peut partiellement remplacer le coke[1].
- Par ordre de températures croissantes : la calcination réalise, entre autres, une décarbonatation ; le grillage une oxydation ; le frittage qui donne une structure poreuse et solide (par fusion partielle).
- En 2000, on dénombre environ 240 chaînes d'agglomération dans le monde, nettement plus grosses que celles du début du XXe siècle[SF 1].
- Pour Michel Freyssenet, la généralisation trop tardive de l'agglomération de minerai en France est une des causes de la crise de la sidérurgie dans le bassin lorrain[10].
- Les sidérurgistes ont emprunté l'usage des roues-pelles aux cimenteries, où leur emploi était commun[11].
- L'olivine apporte aussi de la magnésie qui règle la basicité du laitier, limite la tendance à fuser du laitier cristallisé[SF 4], etc.
- Malgré son coût élevé d'investissement (estimé en 2005 à 40 $/tonne d'aggloméré annuelle, soit 200 M$ pour une grosse chaîne d'agglomération de capacité 5 Mt/an[13]) et de fonctionnement (estimé en 2005 à 60 $/tonne d'aggloméré[13]), l'usine d'agglomération se justifie aisément par l’amélioration significative de la consommation de coke du haut fourneau, par rapport à une marche en « minerai cru ». En effet, un « lit de fusion [à base de minerai] riche permet, dans le même haut fourneau, des productions supérieures de 30 à 40 % à celles qui seraient obtenues avec l'aggloméré lorrain, et de 100 à 120 % supérieures aux productions qui correspondaient au minerai lorrain cru[14] ». C'est le même raisonnement qui justifie l'investissement dans de coûteux fours à vent chaud ou des installations d'injection de charbon aux tuyères.
- Historiquement, le grillage des pyrites, résidus de la fabrication d'acide sulfurique, était uniquement destiné à ôter le soufre et le zinc. En effet, celles-ci contiennent 60 à 65 % de fer et moins de 0,01 % de phosphore, mais jusqu'à 6 % de soufre et 12 % de zinc[L 4].
Références
- (en) Craig L. Bartholomew et Lance E. Metz, The Anthracite Industry of the Lehigh Valley, Ann Bartholomew, , 227 p. (ISBN 0-930973-08-9)
- « Description du Zinc sur SocieteChimiquedeFrance.fr » (consulté le )
- « Description du Plomb sur SocieteChimiquedeFrance.fr » (consulté le )
- (en) Julius H. Strassburger, Dwight C. Brown, Terence E. Dancy et Robert L. Stephenson, Blast furnace : Theory and practice, vol. 1, New-York, Gordon and Breach Science Publishers, , 275 p. (ISBN 0-677-13720-6, lire en ligne), p. 221-239
- (de) Bruno Kerl, Grundriss der EisenhĂĽttenkunde, Leipzig, Verlag von Arthur Felix, , p. 66
- (en) William E. Greenawald, « The Greenawald Sintering Process », Mining and Scientific Press, vol. 122,‎ , p. 81-85 (lire en ligne)
- (en) L. Hand (Circuit Judge), DWIGHT & LLOYD SINTERING CO., Inc., versus GREENAWALT (AMERICAN ORE RECLAMATION CO., Intervener)., Circuit Court of Appeals, Second Circuit, (lire en ligne)
- (en) « Presidents of the Colorado Scientific Society: Arthur Smith Dwight (1864 - 1946) », Colorado Scientific Society
- (en) « Patent Number: US000916392 », United States Patent and Trademark Office
- [PDF]Michel Freyssenet, La sidérurgie française 1945-1979 : L'histoire d'une faillite. Les solutions qui s'affrontent, Paris, Savelli, coll. « Documents critiques », , 241 p. (ISBN 978-2-85930-030-2, OCLC 417353871, BNF 34648522, présentation en ligne, lire en ligne), p. 25 ; 28 ; 40-41 ; 67
- Jean-Yves Debost et Bernard Réal, Les rapports des industries de la manutention avec l'évolution des processus de production et des moyens de transport dans le cours de l'internationalisation du capital, Université des Sciences Sociales de Grenoble, Institut de Recherche Economique et de Planification, (lire en ligne [PDF]), partie 2, p. 47-64
- « La création d'un complexe sidérurgique maritime à Selzaete : Sidemar », Courrier hebdomadaire du CRISP, CRISP, no 124,‎ 1961 /34, p. 1-25 (DOI 10.3917/cris.124.0001, lire en ligne)
- Jacques Astier, « Agglomération des minerais de fer », dans Techniques de l'ingénieur Traité matériaux métalliques, Éditions techniques de l'ingénieur (lire en ligne)
- Jean Duflot, Encyclopædia Universalis (lire en ligne), « Sidérurgie »
- (en) Thomas Turner (dir.), The metallurgy of iron : By Thomas Turner... : Being one of a series of treatises on metallurgy written by associates of the Royal school of mines, C. Griffin & company, limited, coll. « Griffin's metallurgical series », , 3e éd., 463 p. (ISBN 1-177-69287-2 et 978-1177692878, lire en ligne), p. 87-88
- (en) Kevin Gordon, « How a German Steel Plant Improved Production with Sintering Technology », (consulté le )
- [PDF](en) Best Available Techniques (BAT) Reference Document for Iron and Steel Production, Direction régionale de l'environnement, de l'aménagement et du logement, , 597 p. (lire en ligne), p. 13-14 ; 119-139
- (de) « Die größte Filteranlage der Welt »,
- Adolf Ledebur, Manuel théorique et pratique de la métallurgie du fer, Tome I et Tome II (voir dans la bibliographie)
- Tome 1, p. 252-253
- Tome 1, p. 254-271
- Tome 1, p. 260-270
- Tome 1, p. 231-233 ; 245-247
- Jacques Corbion, Le Savoir… fer — Glossaire du haut fourneau, (voir dans la bibliographie)
- § Agglomération
- § Agglomération Smidth
- § Chaîne (d'Agglomération)
- § Olivine
- § Agglomération intégrale du minerai
- (en) Cet article est partiellement ou en totalité issu de l’article de Wikipédia en anglais intitulé « sinter plant » (voir la liste des auteurs).
- (de) Cet article est partiellement ou en totalité issu de l’article de Wikipédia en allemand intitulé « Dwight-Lloyd-Verfahren » (voir la liste des auteurs).
Bibliographie
- Adolf Ledebur (trad. Barbary de Langlade revu et annoté par F. Valton), Manuel théorique et pratique de la métallurgie du fer, Tome I et Tome II, Librairie polytechnique Baudry et Cie éditeur, [détail des éditions]
- Jacques Astier, « Agglomération des minerais de fer », dans Techniques de l'ingénieur Traité matériaux métalliques, Éditions techniques de l'ingénieur (lire en ligne)
- (en) Julius H. Strassburger, Dwight C. Brown, Terence E. Dancy et Robert L. Stephenson, Blast furnace : Theory and practice, vol. 1, New-York, Gordon and Breach Science Publishers, , 275 p. (ISBN 0-677-13720-6, lire en ligne), p. 221-239
- Jacques Corbion (préf. Yvon Lamy), Le Savoir… fer — Glossaire du haut fourneau : Le langage… (savoureux, parfois) des hommes du fer et de la zone fonte, du mineur au… cokier d'hier et d'aujourd'hui, , 5e éd. [détail des éditions] (lire en ligne)
Voir aussi
Articles connexes
Liens externes
- (en) United States Geological Survey Iron Ore Publications
- (en) « Lien vers le site de SteelUniversity.org »(Archive.org • Wikiwix • Archive.is • Google • Que faire ?)