Usine sidérurgique d'Unterwellenborn
Maxhütte Unterwellenborn
Stahlwerk Thüringen
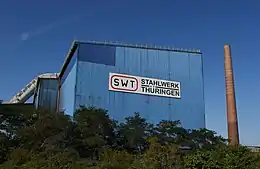
Type d'usine |
Usine sidérurgique (en) |
---|
Opérateur |
Maxhütte (Sulzbach-Rosenberg) (d) (- Friedrich Flick (- Société par actions soviétique (d) (- Volkseigener Betrieb (- Treuhand (- Arbed (- Alfonso Gallardo DÃaz (d) (- Companhia Siderúrgica Nacional (depuis ) |
---|---|
Effectif |
373 () 4 900 () 4 410 () 5 275 () 6 341 () 4 500 () 6 500 () 2 000 () 687 () |
Produits |
Poutrelles, traverses en acier |
---|
Localisation | |
---|---|
Coordonnées |
50° 39′ 18″ N, 11° 26′ 06″ E |

L'usine sidérurgique d'Unterwellenborn est une aciérie électrique spécialisée dans la production de poutrelles. Fondée en 1872 comme Maxhütte Unterwellenborn, en tant que filiale de la Maxhütte de Sulzbach-Rosenberg (de), sa présence en Allemagne de l'Est amène à sa nationalisation en 1946, puis à sa privatisation en 1992.
Modernisée afin de produire des poutrelles à partir de ferrailles recyclées dans un four électrique, elle fait partie, depuis 2012, du groupe sidérurgique brésilien CSN, sous le nom de Stahlwerk Thüringen.
Histoire
Construction
L'opportunité d'une usine sidérurgique dans le secteur de Kamsdorf est soulignée par Ernst von Fromm sr. (1854–1923) au début des années 1870, des minerais de fer sans phosphore y ayant été trouvés. Sur sa suggestion, le conseil de surveillance de la Maximilianshütte de Sulzbach-Rosenberg (de) approuve l'acquisition, en 1872, de mines de fer locales pour 71 000 florins[1].
Le , la Maxhütte de Sulzbach-Rosenberg obtient de l'administration du duché de Saxe-Meiningen l'autorisation d'édifier une usine sidérurgique à Unterwellenborn[2]. En 1873, les mines sont modernisées avec une machine à vapeur et, le , le premier haut fourneau est mis à feu. C'est un engin moderne, fonctionnant au coke, d'une capacité de 50 t/j à 6 tuyères avec un gueulard Parry. Enfin, en 1876-1877, un chemin de fer connecte les hauts fourneaux aux mines et, en 1878, le deuxième haut fourneau est mis à feu[1] - [3].
En 1878, la fermeture de l'usine de Maxhütte-Haidhof, qui converti la fonte d'Unterwellenborn en acier est décidée, et une nouvelle aciérie Bessemer est décidée à proximité des hauts fourneaux. Celle-ci, équipée de deux convertisseurs modernes de 6 tonnes, est mise en service en 1880. L'usine d'Unterwellenborn est la deuxième en Allemagne, après celle de Dortmund-Hörde, à être dotée d'une aciérie Bessemer intégrée. En parallèle, une petite production de spiegeleisen de qualité (il est notamment exempt de cuivre) positionne l'usine sur un marché de niche très rémunérateur. Bien que l'usine d'Haidhof continue de laminer les produits d'Unterwellenborn[3], un laminoir à rails est démarré cette année-là [1], .
En , le 3e haut fourneau est mis à feu. En 1886, une batterie de 4 cowpers (6 m de diamètre et 18 m de haut) est mise en service : elle permet de réduire la consommation de coke de 40 %. Enfin, en 1888, le 4e et dernier haut fourneau est mis à feu : l’usine peut produire jusqu'à 100 t de fonte brute par jour[1].
Passage à la fonte Thomas
Le , la Maxhütte décide d'acheter les gisements de minerais de Richard von Swaine (de) à Schmiedefeld am Rennsteig. Ceux-ci consistent en chamosite, un minerai siliceux pauvre, contenant 35 % de fer, qu'un grillage amène à 41 %. Le gisement est important : il consiste en deux strates, une supérieure de 1 600 m de long et 10 à 25 m d'épaisseur (puis diminuant), et une strate inférieure, riche mais épaisse de 2 m[1].
Ce minerai est abondant mais phosphoreux : l'adoption du procédé Thomas en complément du Bessemer est nécessaire. En , une nouvelle aciérie à Rosenberg devient capable d'assurer la conversion de la fonte phosphoreuse produite à Unterwellenborn. De 1891 à 1895, les hauts fourneaux bénéficient d'un programme d’agrandissement et de modernisation. En 1892, deux hauts fourneaux produisent chacun 150 t/j de fonte, soit plus que l'ensemble de l'usine dix ans auparavant[1].
Cependant, en 1898, le contrat de fourniture en lingots d'acier à la Königin Marienhütte (de), à Cainsdorf (de) (Zwickau) prend fin et la petite aciérie Bessemer est fermée le . Le site devient une pure usine à fonte pour l'affinage Thomas à Rosenberg. Cette configuration est peu rentable et, désireuse de répondre aux besoins futurs des chemins de fer de l'État de Saxe, une usine sidérurgique Thomas moderne avec des laminoirs est mise en service à Lichtentanne, près de Zwickau, le [1].
Au début du XXe siècle, l'usine se spécialise de plus en plus dans l'acier Thomas. Deux fours à chaux, à Pößneck et à Öpitz , destinés à l'alimentation des convertisseurs, sont mis en service en 1904. La production de spiegeleisen est progressivement abandonnée entre 1904 et 1909. Les mines sont modernisées avec l'installation d'énergie pneumatique et électrique[1].
Le coke vient des bassins houillers de l'ouest de l'Allemagne[4], essentiellement de Westphalie, puis de Saxe et de Bohême. Le coût important des achats amène l'entreprise à acquérir une concession de houille à Hamm (de), dans la Ruhr. Le fonçage d'un double puits commence en 1902, mais des entrées d'eau et des dégagements de grisou pénalisent l'exploitation. Dans les années qui suivent, près de la moitié des ressources financières de l'usine sont englouties dans ce projet. En , l'exhaure est en panne. Une entrée d'eau supplémentaire en août arrête l'extraction. Ces événements, conjugués avec la mobilisation de la Première Guerre mondiale, condamnent la mine : l'aventure se solde par une perte de plus de 14 millions de marks. L'entreprise, au bord de la banqueroute, n'est sauvée que par l’interventionnisme du Reich et par l'achat de coke à des concurrents[3].
Intégration dans le groupe Flick gâchée par la conjoncture
Au lendemain de la Première Guerre mondiale, l'usine est, à l'instar de la sidérurgie allemande, très affaiblie. En 1921, Robert Röchling prend la présidence du conseil de surveillance et la Maxhütte peut s’approvisionner en coke à partir de la mine de Röchling à Solingen[3]. En complément, la Maxhütte fusionne avec le Groupe Flick. Un grand programme d'investissement est engagé. Mais la concurrence féroce entre Friedrich Flick et les magnats de la Ruhr prive l'usine de son approvisionnement en coke[1]. Enfin, l'occupation de la Ruhr, entre et , prive l'Allemagne de coke. L'usine importe du coke d'Angleterre, mais le coût est si prohibitif que la fermeture temporaire est inévitable[5]. En , la production s'interrompt jusqu’en : tous les hauts fourneaux sont arrêtés pendant 6 mois. Le programme d'investissement se fait au ralenti[1].
En 1926, les conditions du marché s'améliorent. Après la fin de la modernisation des installations de traitement du gaz de haut fourneau, la construction de la nouvelle aciérie Thomas, décidée en 1921, reprend. Mais sa réalisation est moins prioritaire que la modernisation des hauts fourneaux qui reçoivent, en 1928, 7 nouvelles soufflantes à piston[1]. En 1928, l'aciérie et les laminoirs de Zwickau sont démontés et transférés à Unterwellenborn. Cette concentration industrielle est suivie d'une concentration financière l'année d'après : le Konzern de Friedrich Flick acquiert la Maximilianshütte récemment agrandie[4]. Des laminoirs sont construits : un duo réversible de 900 est mis en service le [1]. La production consiste alors en petites et moyennes poutrelles, en profilés marchands (plats, cornières, fers U, etc.) et en rails[2].
Mais les 3 convertisseurs Thomas, d'une capacité de 14 tonnes, sont trop petits. Le premier soufflage se déroule en . Malgré leur agrandissement à 16,5 tonnes puis à 17 tonnes, la suite des opérations confirme le sous-dimensionnement de l'aciérie[1]. Il en est de même pour les laminoirs, construits à l'économie[5].
La Grande Dépression frappe la sidérurgie allemande à partir de 1931. Un seul haut fourneau de l'usine reste à feu pour produire un peu de fonte de moulage et de spiegeleisen. La production de fonte Thomas est suspendue jusqu'en . La rénovation du haut fourneau 4, qui avait commencé en 1929, reprend et s'achève enfin en : cette année-là , la production atteint enfin un niveau nominal. Mais ces années difficiles ont perturbé la modernisation du site : le plan décidé en 1921 a mis 15 ans à être exécuté. L'obsolescence du site est évidente[1] : les aciers de qualité sont irréalisables avec le procédé Thomas.
En 1936, poussée la par relance du Troisième Reich, la production est revenue au nominal : « Les dommages causés par le déclin ont été éradiqués […] 1936 est l'année d'une construction sur une base renouvelée […] Le Vierjahresplan a fédéré ensemble toutes les forces. » Cette année-là , un four électrique de 17,5 tonnes démarre pour positionner l'usine sur les produits en acier inoxydable. Le deuxième four le suit un an plus tard[5].
Usine stratégique pour l'Allemagne de l'Est, qui décline rapidement (1945-1992)
t. de minerai | t. de fonte | t. de laminés | |
---|---|---|---|
1933[6] | 71 691 | 2 221 | |
1934[6] | 92 493 | 38 107 | |
1935[6] | 354 724 | 83 707 | |
1936 | 201 800[4] | 120 947[6] | |
1937[6] | 231 356 | 180 211 | |
1938[6] | 231 442 | 183 711 | |
1939[6] | 427 300 | 231 923 | 187 085 |
1940[6] | 228 941 | 183 321 | |
1941[6] | 215 983 | 176 344 | |
1942[6] | 221 194 | 161 549 | |
1943[6] | 254 640 | 169 347 | |
1944[6] | 426 242 | 150 435 | 174 235 |
1945[6] | 47 600 | NC | NC |
1946[6] | 212 500 | 82 800 | 62 000 |
1950 | 326 000[4] | 185 200[7] | |
1951[7] | 246 400 | ||
1952 | 475 000[8] | 278 000[7] | |
1953[7] | 296 000 | ||
1954[7] | 320 000 | ||
1955 | 381 500[4] | ||
1958 | 426 000[4] |
Une usine oubliée devenue stratégique
En 1945, l'usine est peu bombardée[4]. Mais elle est si obsolète que l'occupant russe ne la démonte pas dans le cadre des réparations de guerre, excepté l'usine de production de gros canons. Enclavée dans l'agglomération, elle a de plus un faible potentiel d'évolution. Mais cette situation lui permet aussi de conserver une main d'œuvre qualifiée et elle devient l'« usine-mère de la métallurgie de l'Allemagne de l’Est »[9]. De plus, elle est la seule usine sidérurgique intégrée (c'est-à -dire capable de produire en autonomie de l'acier à partir de ses mines) de la RDA. L'arrivée de la Guerre froide amène le Gouvernement socialiste à relancer l'usine et à la moderniser immédiatement[10] : le HF2 est relancé le , les 3 autres le suivent en 1949[11]. Les 3 mines de Kamsdorf (minerai de manganèse[10]), Schmiedefeld (sidérite de 22 à 35 % de fer[10]) et Wittmannsgereuth (de) (sidérite de 20 à 40 % de fer[10]) approvisionnent l'usine, cette dernière n'étant opérationnelle qu'à partir de 1944[6]. Ces mines extraient donc un minerai pauvre qu'un grillage peut élever à 44 % de fer[12].
Confisquée par la Russie, l'usine devient, le , une Société soviétique par actions (de) (SAG)[6]. Le [note 1] elle est rendue aux autorités allemandes. Le , elle est nationalisée sous la forme d'une Volkseigener Betrieb, sous le nom de VEB Maximilianshütte Unterwellenborn[6] - [4].
Refondation
Devenue stratégique, l'usine est modernisée et agrandie de 1947 à 1952. En 1948, deux fours pour réchauffer les blooms avant laminage sont mis en service[13] et le haut fourneau 4 est modernisé. L'année suivante, c'est une machine à couler les gueuses qui est mise en service[13]. En 1952, une usine d'agglomération Dwight-LLoyd est construite, l'atelier de forge est modernisé[9] et la construction d'un mélangeur de 1 000 tonnes est en cours[14], tandis que le HF4 est équipé d'un chargement automatique en 1952 portant sa capacité à 430 t/j[10]. En 1953, une installation de production d'oxygène neuve alimente les convertisseurs et les hauts fourneaux[15] - [16].
Symbole socialiste, l'usine est au cœur des actions sociales bénéficiant aux travailleurs de la métallurgie. La mobilisation de la Jeunesse libre allemande sous le slogan Max braucht Wasser, permets la construction en 85 jours d'un aqueduc d’alimentation des hauts fourneaux de 5 km, depuis la Saale via la Montagne rouge, dans un effort célébré par la propagande socialiste[11].
En 1955, l'usine est un ensemble cohérent, dont la production a doublé en 10 ans. Elle consiste en[9] - [16] :
- 1 chaîne d'agglomération ;
- 1 haut fourneau de 285 m3 à 430 t/j, 3 de 360 m3 à 350 t/j et un fourneau à cuve basse (de) à 40 t/j. La capacité est de 450 kt/an ;
- 1 mélangeur de 1 000 t, 4 convertiseurs Thomas de 15 t, 2 fours électriques de 25 t. La capacité est de 350 kt/an + 60 kt/an ;
- 1 blooming de 1 100. Capacité 240 kt/an ;
- 1 duo de 950 pour grosses sections, 1 trio de 700 pour sections moyennes et 1 trio pour plaques destiné à être intégré à terme dans un train continu à larges bandes.
La valorisation des laitiers est aussi un sujet essentiel. En 1891, la transformation de laitier de haut fourneau en pouzzolane avait dû être abandonnée, le ciment Portland surclassant facilement cette filière de revalorisation[1]. En 1905, la cimenterie est démarrée[11], modernisée après la Première Guerre mondiale[3], et encore une fois en 1958 : elle devient alors capable de produire 600 000 t/an de ciment[11].
Parallèlement, un effort de développement soutenu est engagé pour s’affranchir des approvisionnements défaillants en coke. Des bas fourneau sont mis au point, les « fourneaux à cuve basse (de) » (Niederschachtofen en allemand[14], ou low cupola furnace en anglais[10]) sont essayés afin d'extraire le fer des minerais pauvres et siliceux que l'usine reçoit de ses mines[17] - [4] mais la mise au point s'avère laborieuse et l'usine se trouve rapidement être la seule à persévérer dans cette technologie[10]. Le procédé Krupp-Renn, bien adapté à la réduction directe des minerais siliceux, est également adopté : deux fours de 3,6 m de diamètre et 60 m de long sont mis en service en 1953[18].
Cheminement monotone vers le déclin
La configuration générale de l'usine n'évolue plus guère pendant les 30 années suivantes. En effet, l'usine sidérurgique d'Eisenhüttenstadt devient, au début des années 1950, la priorité du Gouvernement de la RDA. Neuve et dotée d'un gros potentiel, son développement éclipse l'usine d'Unterwellenborn[2].
La vieille usine se concentre sur l'amélioration de son efficacité, au détriment des volumes et de la qualité (l'aciérie étant dépourvue de fours Martin-Siemens). Dix ans après la construction de l'agglomération des minerais, le chargement des hauts fourneaux est modernisé. Le , la mise à feu du HF4 permet de passer à un fonctionnement à 3 hauts fourneaux (à partir de 1968, le HF3 étant de réserve[11]), et en 1968, la marche à 2 hauts fourneaux (chacun ayant sa réserve) devient la norme. Les fours Krupp-Renn sont également arrêtés cette année-là [1] ainsi que le fourneau à cuve basse, qui avait été démarré en 1951[11].
Seuls les arrêts identifiés et de plus de 6 mois ont été représentés. En couleur claire, les périodes de mise en sommeil.

En 1970, un laminoir circulaire remplace la forge[11] et, l'année d'après, le blooming est électrifié. L'année suivante, en 1972, les convertisseurs Thomas passent au soufflage à l'oxygène (procédé QEK, un procédé de soufflage d'oxygène par le fond proche de l'OBM). Les hauts fourneaux sont maintenus en état : les planchers de coulée et le transport de la fonte sont reconstruits de 1977 à 1983. De plus, cette année-là , l'injection de charbon aux tuyères permet de réduire leur consommation de coke[1].
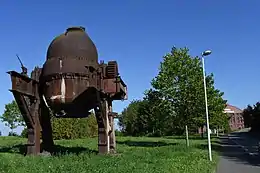
Le train continu à chaud combiné KFS (Kombinierte Formstahlstraße) entre en service le . Cet outil moderne et longtemps espéré consolide la pérennité de l'usine, alors que la situation politique et économique de la RDA devient de plus en plus fragile[2]. Sa capacité est de 500 à 600 kt/an[11]. Les vieux laminoirs ferment (notamment le trio[11]), alors qu'une dernière modernisation de l’aciérie permet d'essayer le procédé EFK au convertisseur, qui permet d'enfourner jusqu'à 90 % de ferrailles[1].
En 1990, la restructuration commence dans la foulée de la réunification allemande. L'aciérie électrique et le laminoir duo ferment temporairement, et la presse n'est mise en service que si des commandes rentables sont passées. Alors que la Maxhütte emploie 6 500 personnes avec ses succursales à Ohrdruf, Wünschendorf et Schmiedefeld en 1989, moins de 2 000 personnes restent aux effectifs moins de deux ans plus tard[11].
En 1992, l'usine illustre l'obsolescence de la sidérurgie est-allemande. Le soufflage à l'oxygène des convertisseurs a gommé le handicap lié à l'absence de fours Martin-Siemens, et a permis de doubler la productivité de l’aciérie. Mais la faible taille des hauts fourneaux, des convertisseurs et des fours électriques pénalise la productivité humaine, qui ne dépasse pas la moitié de l'usine d'Eisenhüttenstadt. Enfin, l'absence de coulée continue est une lacune criante, qui contraste avec le train ultra-moderne. La configuration de l'usine a peu changé[19] :
- 3 hauts fourneaux d'environ 500 m3. La capacité est de 850 kt/an ;
- 4 convertiseurs OBM de 25 t, 2 fours électriques de 20 t. La capacité est de 700 kt/an + 100 kt/an ;
- 1 blooming quarto de 1 100. Capacité 700 kt/an ;
- 1 train continu à profilé lourds. Capacité 770 kt/an ;
- 1 train à couronne (capacité 5 kt/an) et deux forges.
Transformation en usine électrique compacte (depuis 1992)
Le l'entreprise luxembourgeoise Arbed acquiert l'entreprise. Le laminoir moderne est la pierre angulaire de l'usine. L'usine d'agglomération, les hauts fourneaux et l’aciérie sont rapidement fermés et démantelés. À leur place est édifiée une aciérie électrique dotée d'une coulée continue[2]. L'ARBED reprend 620 employés. Le four à courant continu de 120 tonnes et 120 MVA donne à l'usine une capacité de production de 630 000 tonnes/an de produits semi-finis[11]. Le , l'acier en fusion coule à nouveau à Unterwellenborn, après 3 ans d'arrêt de la phase liquide. La fusion de l'Arbed avec le français Usinor et l'espagnol Aceralia, pour donner naissance au groupe européen Arcelor en 2001, conforte l'usine. L'année suivante, d'importantes modernisations sont réalisées sur le train de laminage et les lignes de parachèvement[2].

En 2006, la fusion entre Arcelor et Mittal Steel s'accompagne de cessions destinées à limiter la position dominante de l’ensemble. L'usine est alors cédée au Groupe Gallardo (es). Ce nouveau propriétaire investit dans le dégrossissage du laminoir, mais aussi dans la limitation de l'impact environnemental de l'usine : le dépoussiérage est amélioré et un nouveau site de traitement des déchets est mis en place[2].
Mais en , étranglé par la crise économique espagnole, le Groupe Gallardo est contraint de fermer ou céder la plupart de ses usines. L'usine est revendue au groupe brésilien CSN[2].
Notes et références
Notes
- La date du est également évoquée[4].
Références
- (de) Albert Gieseler, « Maximilianshütte », Mannheim, (consulté le )
- (de) « Stahl, der seit 1872 trägt. », Stahlwerk Thüringen (consulté le )
- (de) « von Beginn an bis 1921… », sur https://www.mazet24.de/ (consulté le )
- Henri Smotkine, « Les caractères originaux de la sidérurgie en République Démocratique Allemande », Annales de géographie, no 378,‎ , p. 126-136 (lire en ligne)
- (de) « 1921 - 1939 », sur https://www.mazet24.de/ (consulté le )
- (en) « The Maximilianshütte at Unterwellenborn » [PDF], CIA, (consulté le )
- (en) « Rolled Steel Production in East Germany » [PDF], CIA, (consulté le )
- (en) « Maximilianshuette, VEB, Unterwellenborn » [PDF], CIA, (consulté le )
- (en) « Iron and steel plants in East Central Europe: a descriptive catalog » [PDF], CIA, (consulté le )
- (en) « Developments at Maxhuette, Unterwellenborn » [PDF], CIA, (consulté le )
- (de) « 1939 bis heute … », sur https://www.mazet24.de/ (consulté le )
- (en) « Development of the iron and steel industry in soviet zone Germany » [PDF], CIA, (consulté le )
- (en) « Production situation at Maximilianshütte Unterwellenborn (Thuringia) » [PDF], CIA, (consulté le )
- (en) « Miscellaneous Notes on the Metallurgical Industry » [PDF], CIA, (consulté le )
- (en) « Production situation at Maximilianshütte, Unterwellenborn » [PDF], CIA, (consulté le )
- (en) « Iron and steel industry of the GDR », Stahl und Eisen, vol. LXXIII, no 17,‎ (lire en ligne [PDF], consulté le ), traduit par la CIA
- Jacques Corbion (préf. Yvon Lamy), Le Savoir… fer — Glossaire du haut fourneau : Le langage… (savoureux, parfois) des hommes du fer et de la zone fonte, du mineur au… cokier d'hier et d'aujourd'hui, , 5e éd. [détail des éditions] (lire en ligne [PDF]), § Fourneau à cuve basse
- (en) J. Mach et B. Verner, « Czechoslovak Experience with the Krupp-Renn Process », UNIDO,
- (de) Helmut Wienert, « Die Stahlindustrie in der DDR », Rheinisch-Westfälischen Instituts für Wirtschaftsforschung, Berlin, Duncker & Humblot, no 52,‎ (ISBN 978-3-428-47341-0, DOI 10.3790/978-3-428-47341-0, lire en ligne [PDF])