Fabrication de l'acier
La fabrication de l'acier est l'ensemble des étapes nécessaires à l'élaboration de lingots, blooms, brames ou billettes ayant la composition finale de l'acier désiré. Elle se décompose en plusieurs grandes étapes : la métallurgie primaire (qui fournit l'acier en fusion), la métallurgie secondaire (où la composition du métal en fusion est ajustée), puis la coulée et sa transformation (par exemple, par laminage).
Lors de la première phase, la fabrication commence à partir du minerai de fer ou de la ferraille (chutes de métal). Lorsque le minerai de fer est utilisé, il peut être introduit sous forme d'aggloméré ou de boulettes dans un haut-fourneau pour être réduit grâce au coke, et produire de la fonte liquide. Il doit alors passer dans un convertisseur pour produire l'acier en fusion. Cette filière est la plus répandue. Alternativement, le procédé de réduction directe permet de transformer le minerai de fer sans passer par un haut-fourneau ou un convertisseur. Les fours à arc électrique sont alors utilisés pour produire l'acier en fusion à partir du minerai de fer préréduit ou de la ferraille.
Lors de la phase suivante, la métallurgie en poche a pour but de nettoyer l'acier (calmage, dégazage, affinage) et de le mettre à nuance (ajout des éléments d'alliage).
L'acier est ensuite coulé au travers d'une lingotière de section adaptée à la forme du demi-produit à fabriquer, en utilisant un procédé de coulée continue ou en lingots, puis est laminé aux dimensions souhaitées des brames ou des blooms.
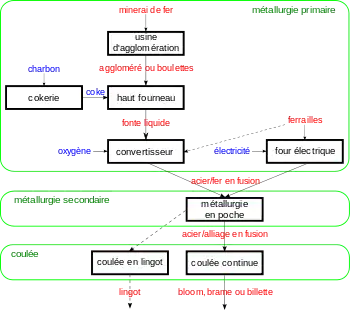
Métallurgie primaire
Usine d'agglomération
Le minerai de fer possède des propriétés chimiques et physiques qui le rendent inexploitable en l'état par le haut fourneau. Il lui manque en particulier :
- la résistance mécanique nécessaire pour supporter l'écrasement dû à l'empilage des matières dans le haut fourneau ;
- la porosité permettant la circulation du vent des tuyères vers le gueulard ;
- la composition chimique en oxydes, pour maîtriser le laitier.
Les minerais sont préparés par broyage et calibrage en grains qui s'agglomèrent entre eux. Le mélange obtenu est cuit sous une hotte à 1 300 °C. L’aggloméré obtenu est ensuite concassé et calibré puis chargé dans le haut fourneau avec du coke.
Cokerie
De façon simplifiée, le coke est du carbone presque pur doté d'une structure poreuse et résistante à l'écrasement. Il est utilisé comme un puissant réducteur. Il est obtenu à partir de la houille, après que celle-ci ait été libérée de ses composants indésirables. Pour cela on la fait cuire, à l'abri de l'air, dans les fours de la cokerie à 1 250 °C durant 17 heures. En brûlant dans le haut fourneau, le coke apporte la chaleur nécessaire à la fusion du minerai ainsi que le carbone nécessaire à sa réduction.
Haut fourneau
On y extrait le fer de son minerai. Minerai et coke solides sont enfournés par le haut, le gueulard. L'air chaud (1 200 °C) insufflé à la base provoque la combustion du coke (carbone presque pur). Le monoxyde de carbone ainsi formé va réduire les oxydes de fer, c'est-à -dire leur prendre leur oxygène et, de ce fait, isoler le fer. Il se chargera cependant en carbone pendant son séjour dans le creuset et se transformera en fonte. La gangue est un produit secondaire du haut fourneau (c'est la part stérile du minerai de fer) ; elle est récupérée, à la sortie du haut fourneau, à l'état liquide, mêlée à d'autres oxydes. La densité moindre de ce résidu le fait flotter au-dessus de la fonte. Ce résidu est appelé laitier de haut fourneau et est principalement exploité pour la fabrication du ciment.
Convertisseur à l'oxygène
Cet outil assure la conversion de la fonte en acier.
La fonte en fusion est versée sur un lit de ferrailles. On brûle les éléments indésirables (carbone et résidus) contenus dans la fonte en insufflant de l'oxygène pur. Il s'y forme, là aussi, un résidu, le laitier d'aciérie, qui est séparé de l'acier au moment de la vidange du convertisseur. On obtient de l'acier liquide sauvage, qui est versé dans une poche. Il est appelé acier sauvage, car, à ce stade, s'il était coulé, il se solidifierait en provoquant de nombreuses projections dues au rejet des gaz dissous (essentiellement du monoxyde de carbone).
Réduction directe
La réduction directe est un ensemble de procédés d'obtention de fer à partir de minerai de fer, par réduction des oxydes de fer sans fusion du métal. Le produit obtenu est du minerai de fer préréduit.
Historiquement, la réduction directe concerne l'obtention d'une loupe au bas fourneau. Ce procédé a été abandonné, au début du XXe siècle, au profit du haut fourneau qui produit du fer en deux étapes (par réduction-fusion donnant une fonte, puis par affinage dans un convertisseur).
Mais divers procédés ont été mis au point au cours du XXe siècle et, depuis les années 1970, l'obtention de minerai de fer préréduit a connu un développement industriel remarquable avec l'essor, notamment, du procédé Midrex. Conçus pour remplacer le haut fourneau, ces procédés ne se sont jusqu'ici avérés rentables que dans certains contextes économiques particuliers, ce qui limite encore cette filière à moins de 5 % de la production mondiale d'acier.
Four à arc électrique

Un four à arc électrique est un type de four qui utilise l'énergie thermique de l'arc électrique, établi entre une ou plusieurs électrodes de carbone et le métal, pour obtenir une température suffisante à sa fusion. Il a été progressivement mis au point à partir de la fin du XIXe siècle. Sa capacité va généralement d'environ 1 tonne à 400 tonnes. Il est principalement utilisé pour la production d'acier liquide (environ 35 % de la production mondiale).
Métallurgie en poche
Le rôle de la métallurgie en poche consiste à mettre à nuance et à température l'acier liquide issu du convertisseur.
Mise Ă nuance
Elle comporte plusieurs étapes, toutes facultatives, et dont l'ordre peut changer :
- le calmage de l'acier sauvage qui va consommer l'oxygène dissous dans l'acier. Pour cela, on jette dans l'acier liquide de l'aluminium (pour les produits plats) ou du silicium (cas des produits longs) qui, en s'oxydant, vont transformer l'oxygène dissous en oxydes ;
- le dégazage : l'acier va passer par un passage sous vide destiné à parfaire la décarburation entamée au convertisseur (dans ce cas-ci, il est nécessaire de conserver, au préalable, un minimum d'oxygène dissous). A cette étape on peut retrouver les opérations de déshydrogénation et, parfois, de dénitruration (abaissement de la teneur en hydrogène et azote respectivement) ;
- l'ajustement du laitier de poche, de manière qu'il ait la capacité d'absorber les impuretés comme les oxydes produits par le calmage ;
- l'affinage qui va ôter les derniers éléments indésirables, comme le soufre (désulfuration) ;
- l'ajout des éléments d'alliages.
Mise à température
La coulée continue demande typiquement des températures d'acier d'environ 30 °C au-dessus du liquidus de l'alliage. Les moyens de réchauffage sont, soit le four électrique à poches, soit un procédé chimique comme l'aluminothermie. Il est également possible de travailler tout le temps très chaud, pour ne refroidir à la bonne température qu'au dernier moment.
Coulée
Coulée continue
L'acier liquide est coulé, à environ 1 560 °C, dans une lingotière en cuivre de section carrée, rectangulaire ou ronde (selon le demi-produit fabriqué).
Au contact des parois de la lingotière, le métal se solidifie instantanément et commence à former une peau solide. L'acier est ensuite tiré vers le bas par un jeu de rouleaux et d'extracteurs et il achève de se solidifier, grâce essentiellement à des jets d'eau pariétaux.
À cause du refroidissement intense, le métal subit une histoire thermomécanique, lors de son parcours dans la machine de coulée continue. En fonction de cet historique (influencé notamment par la vitesse de coulée, la forme de la machine, l'intensité du refroidissement), la qualité du produit est plus ou moins bonne et le sidérurgiste pourra vendre plus ou moins cher le produit.
La coulée en lingots
La coulée peut être également faite en lingotière. Ce procédé, peu performant en termes de mise au mille permet cependant l'obtention d'alliages spécifiques, comme les aciers non calmés.
L’acier est coulé et solidifié dans des moules en fonte : les lingotières.
Une fois la solidification terminée, les lingots sont démoulés (le « strippage » (de l'anglais to strip qui signifie « retirer »).
Transformation
Après un réchauffage à 1 200 °C, les produits coulés sont écrasés dans un gros laminoir pour être transformés en brames (étape de « slabbing », pour les produits plats) ou en blooms (étape de « blooming », pour les produits longs).
Techniques de décarbonation
La fabrication de l'acier émet 2,6 milliards de tonnes de CO2 par an en 2021, soit 7 % à 11 % des émissions mondiales de CO2[1] - [2].
Produire une tonne d'acier par le procédé de fabrication basé sur l'utilisation du charbon dans un haut fourneau émet entre 1,8 et 2,2 tonnes de CO2[2]. Cette méthode traditionnelle est aujourd'hui utilisée pour produire 70 % de l'acier mondial. Afin de réduire ces émissions, les industriels ont déjà travaillé sur l'optimisation de leurs hauts fourneaux, via l'ajout de ferrailles recyclées ou la réutilisation des gaz et de la chaleur induits. La production d'acier à partir de ferrailles récupérées, dans des fours électriques, assure déjà 20 % de la production mondiale d'acier et même 40 % en Europe. Les fours électriques n'émettent plus que 300 à 700 kg de CO2 par tonne d'acier, en fonction de l'origine de l'électricité utilisée. Les efforts des sidérurgistes pour aller plus loin se concentrent sur l'opération de réduction du minerai de fer, c'est-à -dire d'extraction de l'oxygène pour obtenir du fer quasiment pur. Certains aciéristes opèrent déjà de telles « réductions directes » à l'aide de gaz naturel. L'objectif à terme est de remplacer le gaz naturel par de l'hydrogène vert, produit par électrolyse grâce à de l'électricité décarbonée. Cette technologie a été utilisée pour la première fois au monde en août 2021 par le sidérurgiste suédois SSAB avec son projet Hybrit. De nombreux projets sont en préparation en Europe (H-Acero[3] en Espagne). D'autres technologies, comme la capture du CO2 (projet 3D) ou l'électrolyse (projet européen Siderwin[4]), seront mises en production en France courant 2022[2].
Notes et références
- Comment décarboner la production de ciment et d’acier, Pour la Science, 2 mai 2022.
- « Recyclage, CCUS, hydrogène... Sept voies pour décarboner la production d'acier », Usine nouvelle,‎ (lire en ligne)
- (en) « H-Acero » (consulté le )
- (en) « Development of new methodologieS for InDustrial CO2-freE steel pRoduction by electroWINning » (consulté le )