Production de l'aluminium par électrolyse
La production de l'aluminium par Ă©lectrolyse est le procĂ©dĂ© qui permet de fabriquer le mĂ©tal aluminium Ă partir de l'alumine extraite de la bauxite. Le procĂ©dĂ© a Ă©tĂ© inventĂ© simultanĂ©ment par Paul HĂ©roult en France et Charles Martin Hall aux Ătats-Unis en 1886, et il est couramment appelĂ© « procĂ©dĂ© Hall-HĂ©roult[1] ». Il permet la production de l'aluminium[2] dit « primaire », l'aluminium « secondaire »[3] Ă©tant issu du recyclage. Les deux scientifiques sont souvent dĂ©signĂ©s comme les « jumeaux de l'aluminium ».
Principe
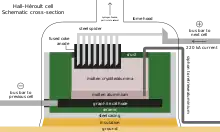
L'alumine est dissoute dans un bain fluoré d'électrolyse entre 950 °C et 1 000 °C suivant la réaction (simplifiée) suivante :
Suivant le principe de l'Ă©lectrolyse, un courant Ă©lectrique continu circule entre l'anode (pĂŽle +) et la cathode (pĂŽle -). Lâaluminium se forme Ă la cathode, oĂč il entre en coalescence dans une nappe dâaluminium liquide, selon la rĂ©action :
En pratique, il faut plusieurs milliers d'ampÚres pour produire une quantité significative d'aluminium : environ 7,65 kg d'aluminium par cellule par jour et par millier d'ampÚres.
Ă lâanode en carbone, le dioxyde de carbone gazeux se dĂ©gage sous forme de grosses bulles qui sâĂ©chappent dans lâatmosphĂšre :
La réaction globale s'écrit :
Le bain est ici considéré comme un électrolyte dans lequel se dissout l'alumine et ne tient aucun rÎle dans les réactions.
Détail
Bain d'électrolyse
La cryolithe est un composé défini de NaF (60 %pds) et AlF3 (40 %pds). Il existe deux types de bains cryolithiques :
- les bains basiques, mélanges de cryolithe et de NaF (NaF>60 % et AlF3 < 40 %pds) ;
- les bains acides, mélanges de cryolithe et d'AlF3 (NaF<60 % et AlF3 > 40 %pds).
Cette aciditĂ© en sel fondu est une aciditĂ© au sens de Lewis. Selon Lewis, un acide possĂšde un atome susceptible de se fixer sur un doublet Ă©lectronique libre alors qu'une base de Lewis est une espĂšce chimique possĂ©dant un doublet libre (aussi appelĂ© doublet non liant). Ici la molĂ©cule acide est le fluorure d'aluminium AlF3. On y dĂ©finit aussi un pF=âlog([Fâ]) par analogie au pH ou pOH. Les professionnels parlent en termes de cryolithe ratio (CR=NaF(%mol)/AlF3(%mol)) ou bath ratio (BR).
Le bain d'électrolyse est constitué principalement :
- d'un fluorure d'aluminium et de sodium : la cryolithe. Elle représente environ 80 % de la masse du bain d'électrolyse. La cryolite a comme composition : (AlF3, 3NaF). Initialement extraite au Groenland elle est désormais en majorité synthétique. La cryolithe a son point de fusion à 1 010 °C ;
- en fonction de l'acidité : du fluorure d'aluminium AlF3 ou de sodium NaF. Représente environ 10 % de la masse du bain d'électrolyse ;
- du fluorure de calcium : CaF2 qui est pratiquement inerte mais baisse les pressions partielles des composĂ©s du bain d'oĂč une diminution de l'Ă©vaporation du bain et une minimisation de l'insertion de sodium dans la cathode. ReprĂ©sente environ 5 % de la masse du bain d'Ă©lectrolyse.
La composition ionique du bain serait donc : Na+, Fâ, AlF3, AlF4â, et AlxOyFz3x-2y-z.
Ătant donnĂ© que tous les composants de l'Ă©lectrolyte sont (sans exceptions) ioniques et complexes il n'existe pas de thĂ©orie permettant la description des composants du bain. Pourtant les spĂ©cialistes utilisent la formule AlXOYFZ3x-2y-z plus proche de la rĂ©alitĂ© qu'Al3+, O2â et Fâ.
Un point important dans la composition du bain est sa densité. La densité du bain est en général proche de 2 ce qui permet de faire couler au fond de la cellule l'aluminium métal de densité 2,3 sous la forme liquide à la température d'électrolyse.
Réactions à l'anode
Il existe deux types de cuves électrolytiques. Celle présentée dans la figure ci-dessus est appelée cuve à anodes précuites, désormais ce type de cuve est majoritaire. L'autre type de cuve est appelé cuve Söderberg dans laquelle la cuisson de l'anode se fait in situ. Cette cuve est de moins en moins utilisée car en plus de polluer, elle génÚre de moins bons rendements. L'anode est en carbone. Elle est fabriquée à l'aide de coke de pétrole calciné (coke de brai) et brai de houille.
à l'anode, se produit la réaction suivante :
La réaction secondaire suivante est :
Une rĂ©action nĂ©faste pour la cellule et l'environnement a lieu lorsque l'alumine vient Ă manquer dans la cellule. Cette rĂ©action est nĂ©faste car elle gĂ©nĂšre des fluorures de carbone, gaz qui dĂ©truisent la couche d'ozone et contribuent Ă l'effet de serre. Ils ne doivent pas ĂȘtre confondus avec les rejets de fluor, rapidement transformĂ© en acide fluorhydrique, dus Ă l'Ă©vaporation partielle des Ă©lĂ©ments du bain Ă la tempĂ©rature du procĂ©dĂ©. Ces rejets fluorĂ©s provoquaient autrefois â avant le captage de la majoritĂ© des gaz en usine â la maladie de la fluorose chez les animaux par substitution de l'hydroxyapatite des os en fluoroapatite.
Cette réaction est également néfaste pour la cellule car elle génÚre un gaz bloquant l'anode en s'y fixant (à la différence du CO2), le passage du courant est altéré et génÚre alors une surchauffe par effet Joule. Cette réaction est la suivante :
Réactions à la cathode
Le pÎle négatif de la cellule est en carbone. Ce bloc de carbone est en permanence recouvert d'aluminium liquide, l'ensemble bloc et métal liquide constitue la cathode en fond de creuset. Les bordures latérales du creuset, en graphite ou en carbure de silicium, sont protégées par du bain figé qui l'isole thermiquement et limite son usure (non représenté sur le schéma ci-dessus), ce bain figé est appelé talus.
à la cathode, se produisent les réactions électrochimiques suivantes :
- réaction primaire :
- réactions secondaires :
les produits de ces deux rĂ©actions provoquent l'endommagement progressif de la cathode. Le sodium en s'insĂ©rant la fait gonfler, flĂ©chir puis fissurer. Les carbures d'aluminium solubles partent en solution et Ă©rodent le bloc. Il faut donc pĂ©riodiquement â environ tous les cinq ans â remplacer les cathodes qui constituent le fond de la cuve d'Ă©lectrolyse : c'est l'opĂ©ration de « rebrasquage ».
Sous l'effet de la force de Laplace, l'aluminium métal se met en mouvement, les vagues de métal liquide ainsi provoquées peuvent, si elles sont excessives, provoquer des courts-circuits en allant toucher l'anode, générant par là des instabilités de conduite de procédé. Le brassage de l'aluminium dû à ces vagues contribue également à sa diffusion dans la nappe de bain situé au-dessus, il est alors immédiatement réoxydé en alumine et le rendement de la réaction s'en trouve réduit d'autant. Les concepteurs des cuves d'électrolyse disposent judicieusement les conducteurs de courant connectés à la cuve pour minimiser ces effets indésirables, grùce au respect de rÚgles d'équilibrage électriques et magnétiques. Les modÚles appliqués sont fort complexes et font appel à l'électro-magnéto-hydrodynamique.
L'aluminium liquide est rĂ©guliĂšrement pompĂ© par aspiration dans une poche mise sous vide partiel (sans en retirer la totalitĂ©). L'aluminium est ensuite transportĂ© dans des fours de maintien pour en ajuster la composition, et le rendre conforme aux spĂ©cifications du client, puis il est solidifiĂ© sous des formes variĂ©es selon l'application finale. Cela peut ĂȘtre des lingots destinĂ©s Ă la refusion en vue de prĂ©paration d'alliages de fonderie, des billettes destinĂ©es Ă l'extrusion (obtention de profilĂ©s), des plaques destinĂ©es au laminage (tĂŽles, boĂźte boissonâŠ) ou encore du fil.
Aspects technologiques
Pour produire une tonne dâaluminium, la rĂ©action requiert 0,415 tonne de carbone, 1,920 tonne dâalumine tandis que 1,520 tonne de dioxyde de carbone est produite par la seule combustion des anodes. Le chauffage de la cellule, appelĂ©e aussi cuve d'Ă©lectrolyse, est entiĂšrement gĂ©nĂ©rĂ© par effet Joule.
La cuve d'électrolyse se compose des éléments suivants :
- un caisson en acier ;
- un garnissage isolant thermique constitué de briques réfractaires ;
- un creuset polarisé cathodiquement constitué d'un assemblage de blocs de carbone cuits à base d'anthracite et liés par une pùte carbonée appelée pùte de brasque ;
- des barres d'acier traversant le caisson et permettant la sortie (pÎle négatif) du courant à la cathode ;
- des ensembles anodiques constitués de tiges verticales en aluminium, fixées sur des pattes en acier qui sont scellées à la fonte sur les blocs de carbone ;
- une superstructure en acier, placée au-dessus du caisson et qui soutient les ensembles anodiques au-dessus du bain électrolytique ;
- un ensemble de conducteurs en aluminium qui transportent le courant de la cathode de la cuve précédente de la série de cuves vers l'anode de la cuve suivante ;
- un systĂšme d'aspiration des gaz vers la station de traitement ;
- un systĂšme d'alimentation en alumine.
La distance entre lâanode et le mĂ©tal est ajustĂ©e par des moteurs qui descendent progressivement les anodes en fonction de leur consommation par la rĂ©action Ă©lectrochimique. Par ailleurs, deux opĂ©rations principales sont effectuĂ©es rĂ©guliĂšrement :
- le soutirage de lâaluminium, qui sâeffectue par aspiration dans une poche de coulĂ©e grĂące Ă un tuyau en fonte plongĂ© dans la couche de mĂ©tal liquide ;
- le remplacement des anodes consommées, chaque anode est conservé durant environ 25 jours.
De maniĂšre Ă assurer la qualitĂ© de la production, de nombreux contrĂŽles sont effectuĂ©s : mesure de la hauteur de mĂ©tal et de bain, prĂ©lĂšvement et analyse du mĂ©tal, suivi de la tempĂ©rature et des paramĂštres Ă©lectriques. Une rĂ©gulation automatisĂ©e des paramĂštres de marche a permis dâamĂ©liorer grandement le rendement du procĂ©dĂ© et de rĂ©duire les Ă©missions de gaz a effet de serre.
Les cuves modernes sont constituĂ©es dâune vingtaine dâanodes soumises Ă une densitĂ© de courant de 0,8 A/cm2. Pour des raisons Ă©conomiques liĂ©es Ă la prĂ©paration du courant continu de forte intensitĂ© Ă partir du courant disponible en mode alternatif sous forte tension, le mĂȘme circuit Ă©lectrique alimente plusieurs cuves placĂ©es Ă©lectriquement en sĂ©rie. L'ensemble est de ce fait appelĂ© par la profession « sĂ©rie d'Ă©lectrolyse ». La sĂ©rie de cuves est gĂ©nĂ©ralement disposĂ©e en deux rangĂ©es parallĂšles (de parfois 2 Ă 200 cuves), dans deux halls de 1 km de long, sĂ©parĂ©s et Ă©loignĂ©s de 50 Ă 100 m.
La sous-station Ă©lectrique qui transforme le courant alternatif (plus de 200 kV) en courant continu (par exemple 1 800 V - 360 000 A), est constituĂ©e de plusieurs unitĂ©s placĂ©es en parallĂšle, chacune capable de livrer un courant d'environ 100 000 A. Le principe est basĂ© sur l'emploi de diodes, plus rarement de thyristors. Le courant produit doit ĂȘtre stable ; pour ce faire il est mesurĂ© prĂ©cisĂ©ment (sondes Ă effet Hall) et rĂ©gulĂ©. Enfin, au vu des puissances en jeu et des risques d'ouverture de circuit sur une cellule d'Ă©lectrolyse (anodes qui ne sont plus immergĂ©es dans le bain Ă©lectrolytique pour des raisons accidentelles), la sous-station est munie de moyens de surveillance et de dĂ©clenchement rapides.
Une cuve de 360 000 A produit environ 1 000 t d'aluminium par an. Une série de 360 cuves à 360 000 A (technologie de 2008) produit 360 000 t d'aluminium par an. La construction d'une usine de cette taille représente en 2012 un investissement d'environ 1,5 à 2 milliards de dollars selon la zone du projet.
Aspects énergétiques
à l'origine, les cuves (les marmites) avaient une intensité de 5 000 à 6 000 A pour une tension de 6 à 7 V. Actuellement (cas de l'usine Liberty Aluminium Dunkerque de Dunkerque), les cuves ont une intensité de 350 000 A pour une tension de 4,20 V. Seul 1,18 V est théoriquement nécessaire à la réaction, le reste est dû aux surtensions électrochimiques ainsi qu'à la chute ohmique dans l'électrolyte, les électrodes et les conducteurs[4].
Le rendement Faraday (rapport de la masse d'aluminium produite à la masse d'aluminium théoriquement déposable) est de l'ordre de 95 % : 95 % de l'électricité « utile » sert à la production et 5 % est perdu dans les réactions secondaires, dont principalement :
Cette réaction est possible car anode et cathode ne sont distantes que de quelques centimÚtres, ce qui peut entrainer un contact entre une bulle de CO2 et le métal mais aussi parce que l'aluminium métal se dissout à raison de 0,01 %pds dans le bain.
5,64 MWh dâĂ©nergie Ă©lectrique sont thĂ©oriquement nĂ©cessaires pour fabriquer une tonne dâaluminium. Cependant, lâĂ©nergie consommĂ©e est dâenviron 13,5 MWh/t, du fait dâune dissipation de lâĂ©nergie par effet Joule. Ce dĂ©gagement de chaleur suffit Ă maintenir la tempĂ©rature du bain aux alentours de 960 °C, mais implique Ă©galement un faible rendement Ă©nergĂ©tique global, de lâordre de 50 %.
Pour une usine dâĂ©lectrolyse contenant 360 cuves alimentĂ©es par 360 000 A sous une tension de 4,25 V, le gĂ©nĂ©rateur d'Ă©nergie doit fournir plus de 560 MW. En y ajoutant les auxiliaires, notamment la cuisson des anodes et la fonderie, une usine doit donc disposer dâune puissance de prĂšs de 600 MW, ce qui est considĂ©rable. Ceci reprĂ©sente environ la moitiĂ© de la puissance d'une tranche de centrale nuclĂ©aire. L'installation d'une usine de production d'aluminium se fait gĂ©nĂ©ralement Ă proximitĂ© d'une centrale Ă©lectrique : historiquement dans les massifs montagneux pour leur barrages hydrauliques (France, Suisse, Ăcosse, etc.), dorĂ©navant prĂšs des gisements de gaz (BahreĂŻn, Qatar, Oman, DubaĂŻ, Abou Dabi, Iran, etc.), de charbon (Afrique du Sud, Australie, Inde, Chine, etc.) ou d'autres ressources hydrauliques (Ătats-Unis, Canada, Russie, BrĂ©sil, IndonĂ©sie, AmĂ©rique du Sud, Cameroun).
Aspects environnementaux
Comme tout procĂ©dĂ© mĂ©tallurgique, la production de lâaluminium gĂ©nĂšre des Ă©missions gazeuses et des dĂ©chets en quantitĂ© importante, qui produisent des effets nĂ©fastes sur lâenvironnement et qu'il convient de contrĂŽler autant que faire se peut.
Traitement des résidus et des fumées
Les blocs cathodiques contiennent des fluorures et des cyanures et constituent des déchets dangereux. Ces matériaux ainsi que les réfractaires les accompagnant sont soit recyclés au travers de filiÚres contrÎlées (recyclage généralement privilégié par les autorités européennes), soit stockés pour traitement de neutralisation puis mise en décharge.
Les sels constituants lâĂ©lectrolyte, ainsi que les rĂ©sidus dâanodes, sont eux presque intĂ©gralement recyclĂ©s.
Le problĂšme de lâĂ©puration des gaz dâĂ©lectrolyse a pris de lâimportance dans les annĂ©es 1950-1970 avec les augmentations de capacitĂ© des usines dâĂ©lectrolyse, quand il est apparu que les rejets, sous forme de fluor particulaire et de fluor gazeux (principalement le fluorure dâhydrogĂšne HF), causaient des dĂ©gĂąts Ă proximitĂ© des usines. Initialement neutralisĂ©s par voie dite humide dans des tours de lavage afin de prĂ©cipiter le fluor sous forme de fluorure de calcium (CaF2); les gaz sont depuis les annĂ©es 1970 traitĂ©s par voie dite sĂšche, Ă savoir l'adsorption du fluor sur l'alumine qui ira alimenter les cellules d'Ă©lectrolyse, lĂ mĂȘme oĂč le fluor a Ă©tĂ© Ă©mis. Ce principe est remarquablement efficace (plus de 98 %) et contribue Ă la performance du procĂ©dĂ©.
Les Ă©missions dâoxyde de soufre (SO2) et dâhydrocarbures polyaromatiques (HAP) provenant de la prĂ©paration et de la combustion des anodes sont Ă©galement sources de pollution. La dĂ©gradation de la qualitĂ© des matiĂšres premiĂšres carbonĂ©es, dont la teneur en soufre augmente au fil des ans, ainsi que l'Ă©volution des rĂ©glementations, conduisent pour les usines de derniĂšre gĂ©nĂ©ration Ă installer des unitĂ©s de traitement du dioxyde de soufre, en sĂ©rie avec le traitement du fluor.
Ămission de gaz Ă effet de serre
Les problĂšmes environnementaux induits par le dĂ©gagement massif de CO2 et, dans une moindre mesure de perfluorocarbures (PFC), dans lâatmosphĂšre reprĂ©sentent une prĂ©occupation assez rĂ©cente liĂ©e au procĂ©dĂ© Hall-HĂ©roult, depuis quâil est avĂ©rĂ© que ces gaz Ă effet de serre participent au rĂ©chauffement climatique. Les mesures Ă©tablies en 1997 par le protocole de Kyoto tendent Ă instaurer des quotas dâĂ©missions et concernent donc lâindustrie de lâaluminium.
La rĂ©action dâĂ©lectrolyse produit des quantitĂ©s importantes de dioxyde de carbone : la production annuelle dâaluminium (38 millions de tonnes) aboutit au dĂ©gagement dans lâatmosphĂšre dâenviron 78 millions de tonnes de dioxyde de carbone. Le tĂ©trafluoromĂ©thane (CF4(g)) et lâhexafluoroĂ©thane (C2F6(g)) sont la deuxiĂšme classe de gaz Ă effet de serre produits par le procĂ©dĂ©. Ces PFC sont produits lors de lâeffet dâanode, Ă raison dâenviron 1 kg de CF4 par tonne dâaluminium. Dâune stabilitĂ© de lâordre de plusieurs milliers dâannĂ©es, ces composĂ©s absorbent dix mille fois plus le rayonnement infrarouge que le dioxyde de carbone. Le pouvoir rĂ©chauffant du CF4 vaut 6 630 fois celui du CO2 Ă horizon de 100 ans[5]. Ils ne se forment pas dans la nature et lâindustrie de lâaluminium en est la premiĂšre source dans le monde. Seule une amĂ©lioration dans la gestion du procĂ©dĂ© semble pouvoir permettre de supprimer les Ă©missions. L'utilisation d'anodes inertes pourrait fortement faire diminuer les Ă©missions de gaz Ă effet de serre, mais le procĂ©dĂ© consomme environ 80 % d'Ă©nergie en plus[6].
Par ailleurs, la production de l'Ă©lectricitĂ© nĂ©cessaire au procĂ©dĂ© reprĂ©sente indirectement une source de production importante de gaz Ă effet de serre, puisque prĂšs dâun tiers de lâĂ©lectricitĂ© produite pour lâindustrie de lâaluminium provient de centrales Ă charbon. Au niveau mondial, 70 % des gaz Ă effet de serre (en Ă©quivalent CO2) Ă©mis pour la production de lâaluminium proviennent de la combustion des Ă©nergies fossiles destinĂ©es Ă la production dâĂ©lectricitĂ© pour les diffĂ©rentes opĂ©rations du procĂ©dĂ© (production de lâalumine, confection des anodes, Ă©lectrolyse). La rĂ©duction des Ă©missions passe donc Ă©galement par une modification des moyens de production de lâĂ©nergie.
Un point positif cependant : l'aluminium ne demande que trĂšs peu d'Ă©nergie pour ĂȘtre recyclĂ© (Ă©nergie de refusion relativement faible) ; il contribue de par son ratio rĂ©sistance/poids Ă la rĂ©duction de la consommation Ă©nergĂ©tique des systĂšmes de transport (terre, air, mer). De ce fait, au terme de quelques cycles de vie, il contribue in fine Ă la maĂźtrise des rejets de dioxyde de carbone.
Deux destins communs, deux hommes différents
Au-delĂ des deux hommes ayant inventĂ© la mĂȘme annĂ©e la production de l'aluminium par Ă©lectrolyse, et ce de maniĂšre indĂ©pendante, un fait aussi surprenant est qu'ils sont nĂ©s et morts la mĂȘme annĂ©e, en 1863 et 1914. Il semblerait mĂȘme que les deux scientifiques aient lu au mĂȘme Ăąge, Ă quinze ans, le mĂȘme ouvrage de l'auteur Henri Sainte-Claire Deville traitant de l'aluminium (De l'aluminium, ses propriĂ©tĂ©s, sa fabrication et ses applications, 1859)[7]. Toutes ces ressemblances leur ont valu le nom de « jumeaux de l'aluminium »[8].
Bien qu'ils eussent beaucoup de similitudes entre eux, HĂ©roult et Hall Ă©taient distincts par leur diffĂ©rente nature, mais aussi leur Ă©ducation et mĂȘme leur comportement. Au-delĂ du fait qu'ils aient inventĂ© tous les deux le procĂ©dĂ© de l'aluminium par Ă©lectrolyse, il n'en demeure pas moins qu'ils l'ont dĂ©veloppĂ© de maniĂšre diffĂ©rente, en termes de composition de bain de l'Ă©lectrolyse et de conception de cellule. Hall Ă©tait chimiste au contraire de HĂ©roult, ce qui constituait un certain handicap pour ce dernier pour dĂ©velopper une mĂ©thodologie adĂ©quate. Mais HĂ©roult Ă©tait aussi un expĂ©rimentateur imaginatif, et aprĂšs avoir passĂ© une annĂ©e Ă l'Ăcole des Mines Ă Paris oĂč par ailleurs il rencontra le fameux professeur et chimiste Henry Le Chatelier, il s'orienta plus vers la technologie. Il comprit par exemple que la cryolithe constituait le meilleur composant pour le bain Ă©lectrolytique. Ensuite, il se focalisa sur la cuve oĂč il rĂ©ussit Ă augmenter la dimension de l'anode et ainsi Ă diminuer la densitĂ© anodique. De son cĂŽtĂ©, Hall se focalisa sur le problĂšme de la composition du bain et consacra beaucoup plus de temps Ă expĂ©rimenter divers mĂ©langes avec de nombreux fluorures, ce qui n'Ă©tait pas tellement appropriĂ© compte tenu de leurs hautes aciditĂ©s et densitĂ©s[8].
Notes et références
- Ivan Grinberg et Jean Plateau, « Le brevet de Paul HĂ©roult pour un procĂ©dĂ© Ă©lectrolytique de prĂ©paration dâaluminium », Bibnum. Textes fondateurs de la science,â (ISSN 2554-4470, lire en ligne, consultĂ© le )
- « Aluminium », sur LâĂlĂ©mentarium (consultĂ© le )
- « Le recyclage de l'aluminium | Centre d'expertise sur l'aluminium - CeAl », sur CEAL - AluQuébec, (consulté le )
- (en) Kvande, Halvor et Warren Haupin, Inert anodes for AI smelters: Energy balances and environmental impact, Jom 53.5 (2001), 29-33.
- (en) « Global Warming Potentials (IPCC Second Assessment Report) », sur UNFCCC (consulté le ).
- SĂ©bastien Helle, DĂ©veloppement de matĂ©riaux d'anodes inertes pour la production d'aluminium (thĂšse de doctorat en sciences de l'Ă©nergie et des matĂ©riaux), UniversitĂ© du QuĂ©bec - INRS (Ănergie, matĂ©riaux et tĂ©lĂ©communications), (lire en ligne [PDF]), p. 19
- Lescale, 1986, p. 130 ; Caron, 1988, p. 40.
- (en) Maurice Laparra, The Aluminium False Twins. Charles Martin Hall and Paul HĂ©roultâs First Experiments and Technological Options, Cahiers d'histoire de l'aluminium, (lire en ligne).
Articles connexes
- Liste de producteurs d'aluminium
- Statistiques de production
- Découverte du procédé d'électrolyse par Charles Martin Hall et Paul Héroult
- Découvertes scientifiques simultanées