Electron beam physical vapor deposition
LâĂ©vaporation par faisceau dâĂ©lectrons (aussi Ă©vaporation par faisceau Ă©lectronique ; en anglais : Electron-beam physical vapor deposition / EBPVD, aussi simplement electron-beam evaporation) est une forme de dĂ©pĂŽt physique en phase gazeuse, plus spĂ©cifiquement dâĂ©vaporation sous vide, dans laquelle une anode cible sous vide poussĂ© est bombardĂ©e par un faisceau dâĂ©lectrons Ă©mis par un canon Ă Ă©lectrons. Le faisceau dâĂ©lectrons chauffe localement la cible, dont la matiĂšre (atomes ou molĂ©cules) se vaporise et condense sous forme de couche mince sur le substrat (et les parois de la chambre Ă vide)[1] - [2].
.jpg.webp)
Introduction
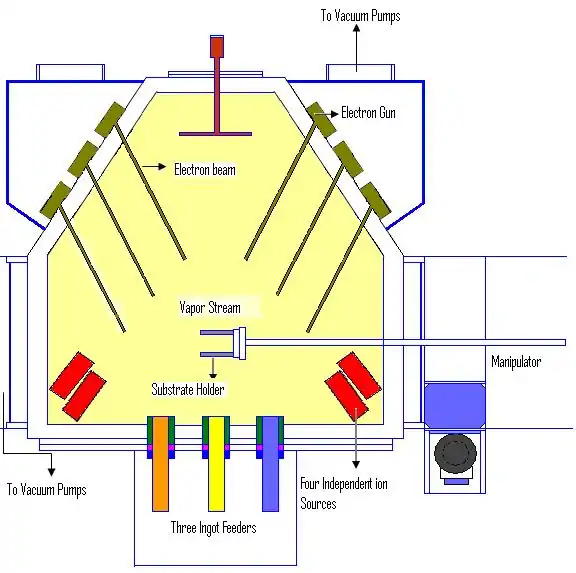
Le dépÎt de couches minces est une famille de procédés largement utilisés, notamment :
- dans lâindustrie des semi-conducteurs, pour la fabrication de matĂ©riel Ă©lectronique ;
- dans lâindustrie aĂ©rospatiale, pour crĂ©er des revĂȘtements de protection thermiques et chimiques afin de protĂ©ger les surfaces contre les environnements corrosifs ;
- en optique, pour conférer la réflectance (ou la transmittance) souhaitée à un substrat ;
- en mĂ©canique (aussi pour lâusinage : les outils de coupe), pour des revĂȘtements anti-usure ;
- et ailleurs dans lâindustrie, pour modifier des surfaces et obtenir les propriĂ©tĂ©s dĂ©sirĂ©es.
Les processus de dĂ©pĂŽt peuvent ĂȘtre classĂ©s en dĂ©pĂŽt physique en phase vapeur (PVD) et dĂ©pĂŽt chimique en phase vapeur (CVD). En CVD, la croissance du film se dĂ©roule Ă des tempĂ©ratures Ă©levĂ©es, conduisant Ă la formation de produits gazeux corrosifs, et il peut laisser des impuretĂ©s dans le film.
Le processus de PVD peut ĂȘtre effectuĂ© Ă des tempĂ©ratures infĂ©rieures et sans produits corrosifs, mais les vitesses de dĂ©pĂŽt sont gĂ©nĂ©ralement plus faible. Avec lâĂ©vaporation par faisceau dâĂ©lectrons, cependant, on obtient un taux de dĂ©pĂŽt Ă©levĂ© de 0,1 Ă 100 ”m/min Ă une tempĂ©rature de substrat relativement faible, avec une efficacitĂ© trĂšs Ă©levĂ©e dâutilisation de matiĂšre.
Processus de dépÎt en couche mince
Ăvaporation de la source
Dans un systĂšme EBPVD, la chambre de dĂ©pĂŽt (photo et schĂ©ma ci-contre) est usuellement sous haut vide, Ă une pression de âŻĂâŻ10-4 Torr, soit environ âŻĂâŻ10-2 Pa. Le matĂ©riau Ă Ă©vaporer est sous forme de lingot. On peut avoir plusieurs canons Ă Ă©lectrons, ayant chacun une puissance de quelques dizaines Ă des centaines de kW. Pour chaque source, le faisceau dâĂ©lectrons ainsi gĂ©nĂ©rĂ© est accĂ©lĂ©rĂ© Ă une Ă©nergie cinĂ©tique Ă©levĂ©e et concentrĂ© sur le lingot. Lorsque la tension dâaccĂ©lĂ©ration est comprise entre 20 kV - 25 kV et le courant du faisceau de quelques ampĂšres, ~ 85 % de lâĂ©nergie cinĂ©tique des Ă©lectrons est convertie en Ă©nergie thermique lorsque le faisceau frappe la surface du lingot ; les pertes sont ~15% par Ă©mission dâĂ©lectrons secondaires (et ~0.1% par rayons X)[2]. La tempĂ©rature de surface du lingot augmente, entrainant la formation de liquide fondu en surface, qui sâĂ©vapore dans le vide.
Le lingot est lui-mĂȘme enfermĂ© dans un creuset en cuivre, refroidi par circulation dâeau. Le niveau de liquide en fusion Ă la surface du lingot est maintenu constant par le dĂ©placement vertical du lingot. Le nombre de lingots dĂ©pend du matĂ©riau Ă dĂ©poser. Le taux dâĂ©vaporation peut atteindre 1 ĂâŻ10â2 g cmâ2 sâ1, bien plus que la pulvĂ©risation[1] - [2].
Stoechiométrie des couches
Certains composĂ©s, comme les carbures rĂ©fractaires tels que le carbure de titane et les borures comme le borure de titane et le borure de zirconium, peuvent se vaporiser de maniĂšre congruente, câest-Ă -dire en conservant leur stoechiomĂ©trie. Ces composĂ©s sont dĂ©posĂ©s par Ă©vaporation directe. Dans ce processus, ces composĂ©s, compactĂ©s sous la forme de lingot, sont Ă©vaporĂ©s dans le vide par le faisceau focalisĂ© dâĂ©lectrons de haute Ă©nergie et les vapeurs sont condensĂ©es directement sur le substrat[3].
Certains oxydes rĂ©fractaires et carbures subissent une dĂ©composition partielle lors de leur Ă©vaporation par le faisceau dâĂ©lectrons, ce qui entraine une stĆchiomĂ©trie diffĂ©rente du matĂ©riau initial. Par exemple, lâalumine (Al2O3), Ă©vaporĂ©e par faisceau dâĂ©lectrons, se dissocie partiellement. Certains carbures et nitrures rĂ©fractaires (tels que SiC, WC, TiN, ZrN et AlN) se dĂ©composent par chauffage et les Ă©lĂ©ments dissociĂ©s ont des volatilitĂ©s diffĂ©rentes[2]. Ces composĂ©s peuvent ĂȘtre dĂ©posĂ©s sur le substrat soit par Ă©vaporation rĂ©active ou par coĂ©vaporation. Dans le processus dâĂ©vaporation rĂ©active, le mĂ©tal est Ă©vaporĂ© Ă partir du lingot par le faisceau dâĂ©lectrons. Les vapeurs sont transportĂ©es par le gaz rĂ©actif, qui est de lâoxygĂšne en cas dâoxydes ou de lâacĂ©tylĂšne dans le cas des carbures[3]. Lorsque les conditions thermodynamiques sont rĂ©unies, les vapeurs rĂ©agissent avec les gaz Ă proximitĂ© du substrat pour former le film. Les films de carbure mĂ©tallique peuvent aussi ĂȘtre dĂ©posĂ©s par la coĂ©vaporation[2]. Dans ce processus, deux lingots sont utilisĂ©s, lâun pour le mĂ©tal et lâautre pour le carbone. Chaque lingot est chauffĂ© avec une Ă©nergie de faisceau diffĂ©rent de sorte que leur taux dâĂ©vaporation peut ĂȘtre contrĂŽlĂ©. Quand les vapeurs arrivent Ă la surface, elles se combinent chimiquement dans de bonnes conditions thermodynamiques pour former une couche mince de carbure mĂ©tallique.
Le substrat
Le substrat sur lequel le dĂ©pĂŽt de couche doit avoir lieu est nettoyĂ© aux ultrasons et fixĂ© sur le porte-substrat. Le porte-substrat est attachĂ© Ă lâarbre de manipulateur. Lâarbre manipulateur se dĂ©place en translation pour ajuster la distance entre le lingot source et le substrat. Lâarbre tourne aussi le substrat Ă une vitesse spĂ©cifique afin que le film se dĂ©pose uniformĂ©ment.
Le substrat peut ĂȘtre chauffĂ© afin dâamĂ©liorer la compacitĂ© des couches, selon la tempĂ©rature homologue et le diagramme structure-zone de Movchan & Demchishin[1] - [2] - [4]; ce chauffage peut ĂȘtre rĂ©alisĂ© par un flux dâĂ©lectrons Ă haute Ă©nergie de lâun des canons Ă Ă©lectrons ou par rayonnement infrarouge, avec des lampes de chauffage.
La microstructure et la compacitĂ© des couches peut aussi ĂȘtre optimisĂ©e par bombardement ionique (cf. ci-aprĂšs).
DépÎt assisté par flux ionique
Certains systĂšmes EBPVD sont Ă©quipĂ©s de sources dâions. Ces sources dâions sont utilisĂ©es sur le substrat pour la gravure, le nettoyage et le contrĂŽle de la microstructure du substrat : on parle de dĂ©pĂŽt assistĂ© par flux ionique (anglais : IBAD â ion-beam assisted deposition). Les faisceaux dâions bombardent la surface et modifient la microstructure du film. Lorsque la dĂ©position a lieu sur la surface du substrat chaud, les films peuvent dĂ©velopper une contrainte de tension interne due Ă lâinadĂ©quation des coefficients de dilatation thermique entre le substrat et le film. Des ions Ă haute Ă©nergie peuvent ĂȘtre utilisĂ©s pour bombarder ces revĂȘtements et y induire une contrainte de compression. Le bombardement ionique augmente Ă©galement la densitĂ© du film (rĂ©duction de la microporositĂ©) modifie la taille de grain et transforme un film amorphe en film polycristallin. Des ions Ă faible Ă©nergie sont utilisĂ©s pour les films pour la production de circuits intĂ©grĂ©s.
Si le procĂ©dĂ© est rĂ©alisĂ© dans une atmosphĂšre (cf. stoechiomĂ©trie ci-dessus) ou si la vapeur est ionisĂ©e, un potentiel nĂ©gatif dâune tension de 100 V Ă 500 V peut ĂȘtre appliquĂ© sur le substrat pour y induire un bombardement ionique[1] - [2].
Un flux ionique peut aussi bombarder la cible, ce qui correspond Ă un autre procĂ©dĂ© : la pulvĂ©risation par faisceau ionique (anglais : ion-beam sputtering ou ion-beam deposition â IBD).
Avantages et inconvĂ©nients de lâEBPVD
Avantages
Le taux de dĂ©pĂŽt dans ce procĂ©dĂ© peut ĂȘtre aussi faible que 1 nm par minute et aller jusquâĂ un maximum de quelques micromĂštres par minute. LâefficacitĂ© de lâutilisation des matĂ©riaux est Ă©levĂ©e par rapport Ă dâautres mĂ©thodes, et le procĂ©dĂ© offre un contrĂŽle structurel et morphologique du film.
Un gros avantage par rapport Ă la variante classique de lâĂ©vaporation sous vide (creuset chauffĂ© par effet Joule) est le chauffage direct, ce qui Ă©vite largement lâinterdiffusion avec le creuset (contamination de la source et dĂ©gradation du creuset)[2].
En raison du taux trĂšs Ă©levĂ© de dĂ©position, ce procĂ©dĂ© a une application industrielle potentielle pour les revĂȘtements de protection dâusure et thermique dans lâindustrie aĂ©rospatiale, les revĂȘtements durs dans lâindustrie dâoutillage et outils de coupe et des films Ă©lectroniques et optiques dans lâindustrie des semi-conducteurs.
Inconvénients
LâEBPVD, comme lâĂ©vaporation sous vide en gĂ©nĂ©ral, est un processus de dĂ©pĂŽt « Ă vue ». Le mouvement de translation et de rotation de lâarbre aide pour le revĂȘtement de surface extĂ©rieure de gĂ©omĂ©trie complexe, mais ce processus ne peut pas ĂȘtre utilisĂ© pour recouvrir une surface intĂ©rieure de gĂ©omĂ©trie complexe (vias, tranchĂ©es, rugositĂ©, etc.).
Par rapport Ă la pulvĂ©risation cathodique, les atomes incidents nâont quâune faible Ă©nergie thermique, ce qui est moins efficace pour densifier la couche, comme le montre le modĂšle structure-zone modifiĂ© de Thornton[5]. Ce dĂ©savantage peut cependant ĂȘtre compensĂ© par un bombardement ionique.
Un autre problĂšme potentiel est que la dĂ©gradation du filaments du canon Ă Ă©lectrons entraine un taux dâĂ©vaporation non uniforme.
Voir aussi
Références
- (en) R. F. Bunshah, « High-rate evaporation/deposition processes of metals, alloys, and ceramics for vacuum metallurgical applications », Journal of Vacuum Science and Technology, vol. 11, no 4,â , p. 814â819 (ISSN 0022-5355, DOI 10.1116/1.1312759, lire en ligne)
- (en) B. A. Movchan, « Inorganic materials and coatings produced by EBPVD », Surface Engineering, vol. 22, no 1,â , p. 35â46 (ISSN 0267-0844 et 1743-2944, DOI 10.1179/174329406X85029, lire en ligne)
- (en) Douglas E. Wolfe et Jogender Singh, « Titanium carbide coatings deposited by reactive ion beam-assisted, electron beamâphysical vapor deposition », Surface and Coatings Technology, vol. 124, nos 2-3,â , p. 142â153 (DOI 10.1016/S0257-8972(99)00644-1, lire en ligne, consultĂ© le )
- (en) B.A. Movchan et A.V. Demchishin, « Study of the structure and properties of thick vacuum condensates of nickel, titanium, tungsten, aluminium oxide and zirconium oxide » (traduction du russe), The Physics of Metals and Metallography, vol. 28, no 4,â , p. 83-90 (lire en ligne)
- (en) John A. Thornton, « High rate thick film growth », Annual Reviews of Materials Research, vol. 7,â , p. 239-260 (DOI 10.1146/annurev.ms.07.080177.001323)
- (en) Cet article est partiellement ou en totalitĂ© issu de lâarticle de WikipĂ©dia en anglais intitulĂ© « Electron beam physical vapor deposition » (voir la liste des auteurs).