Recyclage des batteries
La collecte et le recyclage des batteries est l'activité visant à récupérer les métaux toxiques, rares, précieux ou économiquement valorisables présents dans les batteries, ou d'autres composants des batteries (acides et plastique notamment).
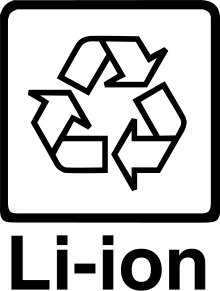
Il vise aussi à réduire la quantité de batteries retrouvée dans les ordures ménagères (en dépit du tri sélectif) quand et là où il existe, et en dépit des interdictions et logos précisant que les piles et batteries ne doivent pas être jetées avec les ordures ménagères.
Les batteries sont en effet l'une des sources d'accumulation dans l'environnement de certains métaux lourds et d'autres produits chimiques pouvant mener à la contamination du sol et la pollution de l'eau[1].
Le recyclage des piles et batteries est une activité très polluante, et dangereuse pour la santé et l'environnement si elle n'est pas pratiquée de manière conforme aux bonnes pratiques du recyclage des métaux non ferreux.
L'essor des véhicules électriques et hybrides augmente le volume de batteries mises sur le marché, renforçant les enjeux environnementaux de gestion en fin de vie de ces batteries.
Jusqu'en 2009 les quantités recyclées étaient faibles. Elles étaient collectées par divers opérateurs pour être recyclées, mais sans garantie de traçabilité (ces batteries pouvaient être broyées au même titre que des batteries au plomb) ni de recyclage ou valorisation de toutes les matières (polluantes ou non). À l’instar des manufacturiers pneumatiques[2], les constructeurs automobiles ont souhaité bénéficier d’une filière identifiée, traçable et sûre pour le recyclage des batteries de leurs véhicules. Pour cela ils se sont rapprochés d’industriels du recyclage et de la récupération qui affirment pouvoir garantir la traçabilité de la collecte à l’émission du certificat de recyclage
Types
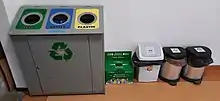
En théorie, tous les types de batteries peuvent être recyclés, et devraient légalement l'être dans la plupart des pays.
Certaines le sont plus que d'autres. Ainsi, aux États-Unis, les batteries au plomb ne sont recyclées qu'à près de 90 %[3] - [4]. D'autres types, tels les piles alcalines et les accumulateurs (nickel-cadmium (Ni-Cd), nickel-hydrure métallique (Ni-MH), lithium-ion (Li-ion) et nickel–zinc (Ni-Zn)), peuvent aussi être recyclés.
Batteries au plomb
.jpg.webp)
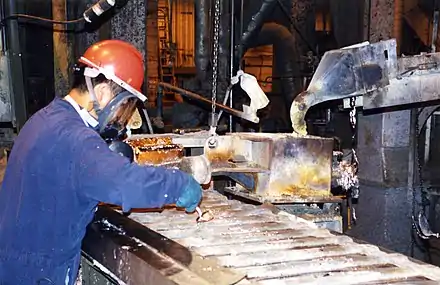
Ce type recoupe, entre autres, les batteries de voiture, de cart de golf, les batteries nomades, les VRLA battery (en), les batteries de motocyclettes ainsi que certaines batteries commerciales.
On recycle ces dernières en les passant à la meule, neutralisant l'acide et séparant les polymères du plomb. Le matériel ainsi récupéré est recyclé de plusieurs manières, dont la reconstruction de nouvelles batteries.
Plusieurs villes offrent un service de recyclage des batteries au plomb. Dans certains États américains et certaines provinces canadiennes, les batteries au plomb sont consignées.
Piles oxyde d'argent-zinc
Principalement utilisées dans les montres, les jouets et certains équipements médicaux, les piles oxyde d'argent-zinc contiennent une petite quantité de mercure.
Batteries lithium-ion
Des partenariats ont été noués entre les constructeurs et les spécialistes du recyclage pour recycler les batteries lithium-ion des voitures électriques et hybrides rechargeables. Ainsi, Audi et Umicore ont mis en évidence lors d’essais en laboratoire que plus de 95 % du cobalt, du nickel et du cuivre peuvent être récupérés pour une réutilisation dans des batteries de traction neuves. Ils construisent un scénario pour une réutilisation à l’infini de ces matériaux stratégiques mis à disposition sous la forme d’une banque de matières premières[5].
Selon une étude de l'Académie chinoise des Sciences de 2017, le lithium était alors, quant à lui en pratique, perdu, faute de procédés compétitif face à la production minière[6].
En mai 2022, la société norvégienne Hydrovolt, créée par Hydro et Northvolt, inaugure son usine de recyclage de batteries, capable de traiter 12 000 tonnes de batteries par an, soit environ 25000 batteries de voitures électriques. Elle affirme pouvoir récupérer 95 % des matériaux utilisés dans ces batteries. Parmi les matières qu’il est possible de recycler, Hydrovolt traite le plastique, le cuivre, l’aluminium et la masse noire, une poudre englobant les matériaux des batteries lithium-ion, c’est-à -dire nickel, manganèse, cobalt et lithium ; elle en extrait les sels de manganèse, de cobalt et de lithium, récupérant ainsi des matériaux pour fabriquer ses futures batteries. Northvolt espère ainsi parvenir en 2030 à produire des batteries composées à 50 % de matériaux recyclés[7].
En octobre 2022, Orano investit 20 millions supplémentaires dans son centre de R&D de Haute-Vienne pour mettre en route un pilote industriel démontrant la faisabilité du procédé d'hydrométallurgie pour la récupération des matériaux d'intérêt avec un objectif de recyclage de 95 %. Le pilote précède la construction d'une usine, à horizon 2025-2026[8].
Le gouvernement français annonce le 13 février 2023 une aide de 30 millions € à deux programmes industriels de recyclage dans le cadre du plan d'investissement France 2030, à l'issue d'un appel à projets « Recyclage, Recyclabilité et Réincorporation des matériaux », lancé en octobre 2021. Le premier projet, porté par Veolia et le spécialiste belge des matériaux et des produits chimiques Solvay, prévoit un démonstrateur en cours de réalisation à Amnéville (Moselle), puis une première unité de traitement de batteries d'un volume de 10 000 tonnes par an en 2023, et vise une capacité de 30 000 tonnes par an en 2028. Le deuxième projet réunit deux « jeunes pousses » : Verkor et Mecaware, start-up lyonnaise versée de recyclage des batteries. Il consiste à récupérer et à recycler sur place les rebuts de la production de l'usine de batteries électriques que Verkor doit ouvrir à Dunkerque en 2025 ; le première unité de traitement des rebuts aurait une capacité de 6 000 à 8 000 tonnes par an. Par ailleurs, le groupe minier Eramet annonce l'ouverture, d'ici l'été 2023, d'une usine pilote de recyclage de batteries de voitures électriques à Trappes ; la collecte des batteries sera assurée par Suez[9].
Risques
Toutes les batteries contiennent des produits toxiques ou dangereux.
Leur recyclage artisanal est une source grave de danger pour l'environnement et la santé, notamment quand il est pratiqué par des procédés de démantèlement et de fusion en plein air. Il est - plus encore que le recyclage industriel[10] - en particulier cause de saturnisme, maladie qui a beaucoup diminué pour sa part qui était due au plomb dans l'essence, mais qui reste une des pathologies de la pauvreté et de l'exclusion[11] - [12].
À titre d'exemple, en France, dans l'île de La Réunion, un dépistage de routine par l’institut de veille sanitaire a mis en évidence un cas de saturnisme infantile grave en 2008–2009 dans un quartier pauvre de la commune du Port, alors que le saturnisme avait jusqu'alors été exceptionnel à la Réunion (10 cas environ, chez des adultes dans les années 1980, à la suite de l'utilisation de mortiers contenant du plomb pour préparer des aliments. Un nouveau dépistage a ciblé le voisinage et des analyses de sol ont été faites près du domicile de l'enfant et une enquête environnementale a été étendue au quartier, avec une sensibilisation des familles résidentes (287 personnes vivant dans 87 foyers) encourageant les parents à faire dépister les enfants de moins de six ans et les femmes enceintes. Les analyses ont montré que le sol était pollué en surface dans tout le quartier (jusqu'à 5 200 mg/kg, soit plus de 300 fois le bruit de fond pédogéochimique de l'île. 76 nouveaux cas de saturnisme plombémie dépassant 100 μg/L ont été mis en évidence par le dépistage (pour 148 personnes prélevées (soit 51 %). Toutes les victimes avaient moins de 15 ans (âge médian = 5,6 ans). La médiane des plombémies était de 196 μg/L (102–392 μg/L). Cette pollution et le problème sanitaire induit ont été attribués au recyclage sauvage dans le quartier de batteries de véhicules ou à d'autres activités diffuses de récupération de métaux[13].
Filière automobile électrique et hybride
Enjeu environnemental et sécurité des personnes
Les batteries de puissance qui équipent notamment les véhicules électriques et hybrides sont étudiées pour répondre à des normes de sécurité. Tant qu’elles sont dans leur emplacement prévu, c’est-à -dire dans le véhicule, et tant que ce véhicule n'est pas accidenté ou en fin de vie, il n’y a selon les fabricants aucun danger ni risques. Cependant extraire ces batteries de leur logement (pour échange standard, pour recyclage ou en fin de vie du véhicule) peut s’avérer dangereux à différents niveaux :
- Au niveau environnemental : Toute batterie contient des électrolytes et des métaux lourds qui, s’ils ne sont pas entièrement et proprement récupérés sont susceptibles de polluer ; ce pourquoi elles doivent être collectées pour être recyclées.
- Pour l’humain : Certains types de véhicules électriques ou hybrides possèdent des batteries dont la tension est élevée, les rendant dangereuses. Mêmes déchargées et non utilisées pendant plusieurs mois, elles peuvent toujours présenter une tension suffisante pour électrocuter une personne qui les manipulerait sans équipement de protection[14].
La réglementation européenne
La Directive Batterie 2006/66/CE spécifie dans son considérant 28 que « En matière de responsabilité, les producteurs de piles et d'accumulateurs et les producteurs d'autres produits dans lesquels sont incorporés une pile ou un accumulateur sont responsables de la gestion des déchets de piles et d'accumulateurs qu'ils mettent sur le marché »[15]. »
Ce principe de Responsabilité Elargie du Producteur (REP) signifie que si un fabricant souhaite mettre sur le marché un produit manufacturé, il doit s’assurer qu’il existe ou doit mettre en place individuellement, un système de collecte en vue de recycler ce produit, qui en fin de vie, deviendra un déchet dangereux et un déchet toxique.
En pratique, un constructeur automobile souhaitant commercialiser un véhicule électrique ou hybride en Europe doit s’assurer qu’il existe une filière de collecte et de recyclage de batteries de nouvelle génération sur le territoire de commercialisation.
Elles sont considérées comme étant des batteries industrielles au sens du code de l’environnement – Article R543-125 5° : « Est considéré comme pile ou accumulateur industriel toute pile ou accumulateur conçu à des fins exclusivement industrielles ou professionnelles ou utilisé dans tout type de véhicule électrique ; »
Une nouvelle directive « batteries », dont une première version a été publiée en 2020, est en négociation avec l'industrie. Elle s'intéresse à tout le cycle de vie d'une batterie. Le texte prévoit de porter le rendement du recyclage à 65 % dès 2025 et jusqu'à 70 % en 2030. Il prévoit des taux précis pour chaque métal, en particulier pour le lithium, pour lequel l'Europe redoute une pénurie, qui devra être recyclé à 35 % puis 70 %, mais aussi le cuivre, et surtout le nickel et le cobalt, deux métaux que l'Europe ne possède pas dans son sous-sol et qu'elle prévoit de recycler à 90 % d'ici à quatre ans. Le texte exige que ces matériaux recyclés soient progressivement incorporés dans les batteries, qui devront incorporer 4 % de lithium recyclé dès 2030 pour monter à 10 % en 2035[16].
Le 9 décembre 2022, le Parlement et le Conseil (représentant les États membres) européens ont trouvé un accord final sur la directive européenne sur les batteries durables. Les fabricants devront déclarer l'empreinte carbone totale de chaque batterie mise sur le marché européen, dès 2024 pour les batteries des voitures électriques. 73 % des batteries de téléphones ou d'ordinateurs, devront être collectées d'ici à 2030, et 61 % pour celles des vélos, scooters et trottinettes électriques, d'ici à 2031. D'ici à 2027, au moins 90 % du cobalt et du nickel des batteries ainsi que 50 % du lithium (puis 80 % en 2031) devront être recyclés. Les batteries des véhicules électriques devront incorporer 16 % de cobalt, 6 % de lithium et de nickel recyclés après 2031[17].
Efficacité recyclage
La Directive 2006/66/CE du Parlement Européen et du Conseil du relative aux piles et accumulateurs ainsi qu'aux déchets de piles et d'accumulateurs (et abrogeant la directive 91/157/CEE) définit dans son annexe III (Partie B) les « rendements minimaux de recyclage » :
« 3. Les processus de recyclage atteignent les rendements minimaux de recyclage suivants :
a) un recyclage d'au moins 65 % du poids moyen des piles et des accumulateurs plomb-acide, y compris un recyclage du contenu en plomb qui soit techniquement le plus complet possible tout en évitant les coûts excessifs;
b) un recyclage de 75 % du poids moyen des piles et des accumulateurs nickel-cadmium, y compris un recyclage du contenu en cadmium qui soit techniquement le plus complet possible tout en évitant les coûts excessifs ; et
c) un recyclage d'au moins 50 % du poids moyen des autres déchets de piles et d'accumulateurs. »
Les batteries des véhicules hybrides et électriques de nouvelle génération qui équipent notamment la Toyota Prius, BMW i3 sont des batteries au Nickel-Métal-Hydrure ou au Lithium-Ion. Ces types de batteries entrent dans la catégorie « autres déchets de piles et d'accumulateurs » de la Directive 2006/66/CE.
Engagement des constructeurs automobiles
Après deux ans de test réalisés avec des ingénieurs venus du Japon, Toyota France a choisi en 2010 la SNAM pour assurer la collecte, le recyclage et la traçabilité des batteries en fin de vie dans toute l'Europe[18].
D’autres constructeurs (Peugeot, Citroën, Honda, Volkswagen, Audi, Seat, Skoda, BMW) ont rejoint cette filière SNAM[19] qui est ainsi devenue la première filière européenne pour la collecte, la traçabilité et le recyclage de batteries industrielles issues des véhicules hybrides et électriques.
Volkswagen annonce en la construction d’une usine pilote de recyclage de batteries à Salzgitter, en Allemagne, avec l'objectif à terme de recycler 97 % de toutes les matières premières ; dans une première étape, l'ouverture en 2020 de l'usine de Salzgitter, avec une capacité initiale de traitement de 3000 batteries par an, permettra de porter le pourcentage de réemploi des composants d’un véhicule électrique de 53 % à 72 %[20].
La Société nouvelle d'affinage des métaux (SNAM), leader européen du recyclage des métaux des batteries usagées, investit 20 millions d'euros en 2022 dans une usine d'accumulateurs fabriqués avec les composants des batteries usées à Decazeville (Aveyron). Cette nouvelle batterie au lithium contient 80 % de matériaux recyclés et 20 % de neufs, a une durée de vie de 10 ans et est vendue 20 à 50 % moins cher qu'une batterie au lithium neuve, pour des applications stationnaires : énergies renouvelables, réseaux électriques et grandes entreprises[21].
Procédés de recyclage thermiques
Les derniers investissements réalisés par la SNAM ont permis l’optimisation des procédés de récupération des éléments à forte valeur ajoutée dans les batteries. Cela a donné naissance à « Prométhée » (Procédé de Recyclage Optimisé MEcanique Thermique Hydrométallurgique d'Éléments Électriques), un procédé combinant les principales technologies nécessaires au recyclage, à un coût maîtrisé. Les procédés mécaniques (broyeurs, densitomètres, séparateurs magnétiques) assurent le broyage et le tamisage en particules plus ou moins fines, avec séparation des métaux.
Les procédés thermiques (fours à pyrolyse, distillation et fusion) détruisent les matières organiques, avec captation des polluants contenus dans les cellules, tout en séparant les métaux en fonction de leur température de fusion. Les lingots sont ensuite expédiés en fonderie. L’hydrométallurgie en étape finale permet de récupérer, purifier les fractions les plus fines et pour partie les plus recherchées comme le cobalt, le lithium ou les terres rares[22].
Procédés de recyclage mécaniques
Alors que la plupart des industriels spécialisés dans cette activité de recyclage utilisaient jusqu’à présent une méthode au cours de laquelle les cellules, pour être démantelées, sont portées à haute température (500 °C) dans des fours à pyrolyse, chauffés au gaz, procédé énergivore et émetteur d’une quantité non négligeable de CO2, la société allemande Duesenfeld utilise un procédé « à froid » : les cellules sont déchiquetées mécaniquement sous une atmosphère inerte d’azote afin d'éviter tout incendie ou explosion, puis la pression est réduite pour que l’électrolyte s’évapore ; il est récupéré et purifié par condensation, ce qui permet de l’utiliser dans de nouvelles batteries. Les métaux constituants des électrodes, comme le cobalt, le nickel, le manganèse, l’aluminium ou le lithium, une fois débarrassés de l’électrolyte, peuvent être facilement triés par des procédés classiques tels que la séparation magnétique ou gravimétrique et peuvent être réutilisés pour fabriquer de nouvelles cellules. Par rapport à la technologie conventionnelle par pyrolyse, cette technologie consomme 70 % d'énergie en moins, réduit l'empreinte carbone de 40 %, permet de réutiliser les métaux et l’électrolyte récupérés au lieu de nouveaux matériaux extraits dans des mines, pour fabriquer des batteries neuves en évitant l’émission de 3 tonnes de CO2 par tonne de batterie, évite les composés fluorés toxiques qui se forment dans les fumées du procédé classique par combustion et pyrolyse et permet de valoriser dans de nouvelles batteries jusqu’à 85 % du contenu des anciens accumulateurs[23].
Réemploi
Le réemploi consiste à offrir une seconde vie aux batteries n'ayant plus des performances jugées suffisantes pour leurs premiers usages. D’un point de vue environnemental, le réemploi des batteries est à privilégier par rapport au recyclage puisque cette stratégie de gestion de la fin de vie permet de prolonger la durée de vie des produits et donc d’augmenter l’efficacité d’utilisation des ressources[24].
Cette stratégie a également un intérêt économique. D’abord, elle répond à un enjeu de souveraineté économique en permettant d’économiser des ressources minières critiques importées (lithium, cobalt, nickel, etc). Ensuite, les revenus générées par la vente des batteries en fin de vie peuvent permettre aux constructeurs automobiles de réduire le prix de ventes de leurs véhicules. Le réemploi des batteries permet donc de faciliter l’accès à la mobilité électrique au plus grand nombre. Finalement, cette stratégie peut se déployer au niveau local ce qui permet d’assurer la création d’emplois non délocalisables[25].
Dans un rapport de 2020, l’ADEME indique que 549 véhicules électriques ont atteint la « fin de vie » au cours de l’année 2018, ce qui représente 0,0005 % des véhicules en fin de vie sur cette même année[26]. Les premières centaines de batteries disponibles pour une seconde vie sont exploitées dans différents projets pilotes impliquant des acteurs industriels et académiques[27].
Les premières conclusions des projets pilotes montrent que l’usage en seconde vie et le degré de collaboration des entreprises impliquées dans le projet impactent significativement l’intérêt économique de ce marché. Les applications stationnaires de stockage d’énergie ont été largement privilégiées dans ces projets[27]. Néanmoins quelques projets à plus petite échelle ont également testé l’utilisation de batteries de seconde vie dans des applications mobiles comme des bateaux électriques ou des robots chargeurs de véhicules électriques[28] - [29] Les résultats de ces projets pilotes semblent avoir permis de lever les incertitudes économiques sur la réutilisation des batteries puisque de grands groupes comme Daimler ou Renault ont annoncé la mise en place d’usines dédiées à la seconde vie [30].
Le réemploi des batteries soulève également des interrogations du point de vue de la faisabilité technique. Trois verrous scientifiques restent encore à lever pour faciliter le déploiement des batteries de seconde vie :
- L’estimation rapide de l’état de santé de la batterie est un prérequis pour l’usage en seconde vie. Sur une batterie neuve, l’état de santé n’a pas besoin d’être évalué à la réception. Tandis que sur une batterie qui a été sollicitée dans une première application et que l’on souhaite réutiliser, l’état de santé est méconnu. Afin de préserver l’intérêt économique de cette batterie de seconde vie, la méthode de caractérisation doit être la plus rapide possible et nécessiter le moins de moyens humains et expérimentaux possibles[31].
- L’évaluation de la durée de vie restante permet d’anticiper la défaillance des batteries surveillées et d’affiner les modèles économiques d’assurance par exemple. Cette information est capitale pour évaluer l’intérêt économique sur le long terme de la batterie de seconde vie par rapport à la neuve.
- Prise en compte des hétérogénéités de vieillissement : Étant donné les coûts prohibitifs du démontage et du réassemblage, les batteries de seconde vie sont généralement réutilisées sans modifications majeures de leurs structures. Or, les éléments vieillis constituant une batterie peuvent être particulièrement hétérogènes en termes d’état de santé. Ces écarts peuvent contraindre l’utilisateur à limiter la sollicitation en fonction des caractéristiques des éléments les moins performants. Pour faciliter l’usage de batteries contenant des éléments hétérogènes, l’équilibrage est communément utilisé. Cette solution vise à homogénéiser l’état de charge des différents éléments, pour permettre leurs utilisations sur l’ensemble de la plage de fonctionnement[32]. La mise en place d’une stratégie d’équilibrage permet dans une certaine mesure d’éviter le processus long et coûteux de caractérisation et tri des cellules.
Récupération des métaux à forte valeur ajoutée
Récupérer les métaux permet notamment de diminuer le coût de recyclage des batteries, car la valeur des métaux tels que les terres rares (La, Ce, Nd, Pr), le cobalt, le nickel, le cuivre, l’aluminium, le manganèse compense une partie du coût de collecte et traitement des batteries, permettant dans certaines filières l’autofinancement. La motivation écologique des metteurs sur le marché se double ainsi d'une motivation économique[33].
Notes et références
- (en) A. M. Bernardes, D. C. R. Espinosa et J. A. S. Tenori, « Recycling of batteries: a review of current processes and technologies », Journal of Power Sources, vol. 130, nos 1-2,‎ , p. 291-298 (ISSN 0378-7753, DOI 10.1016/j.jpowsour.2003.12.026)
- Aliapur
- (en) « Battery recycling in USA »(Archive.org • Wikiwix • Archive.is • Google • Que faire ?), United States Environmental Protection Agency
- (en) « Battery Recycling », Battery Council International
- Recyclage des batteries : Audi et Umicore vers un process à l’infini, automobile-propre.com, 29 octobre 2018.
- A Critical Review and Analysis on the Recycling of Spent Lithium-Ion Batteries, researchgate.net, décembre 2017.
- Hydrovolt : l’énorme usine de recyclage de batteries a ouvert en Norvège, automobile-propre.com, 18 mai 2022.
- Orano investit en Haute-Vienne dans le recyclage des batteries électriques, Les Échos, 24 octobre 2022.
- Voiture électrique : la France accélère dans le recyclage des batteries, 14 février 2023.
- Uzu, G., Sauvain, J. J., Denys, S., Tack, K., Pradere, P., & Dumat, C. (2009, October). Evaluation de l'exposition humaine au plomb par ingestion et inhalation de PM10 et PM2, 5 émises par une usine de recyclage de batteries. In 2. Rencontres nationales de la recherche sur les sites et sols pollués (p. NC). ADEME Editions. Angers.
- Sinnaeve O, Berthier M, Guillard O, Perault MC & Oriot D (1999) Le saturnisme chronique chez l'enfant aujourd'hui. Une pathologie de la pauvreté et de l'exclusion. Archives de pédiatrie, 6(7), 762-767.
- Camara, B., Absa, L., Faye, P. M., Cabrale, M. N., Fall, M., Toure, A., ... & Diouf, A. (2010). P165-Récupération du plomb de batteries et saturnisme à Dakar, Sénégal. Archives de pédiatrie, 17(6), 91.
- Solet, J. L., Renault, P., Denys, J. C., Teulé, G., Dennemont, R. M., Domonte, F., ... & Polycarpe, D. (2013). Investigation et gestion d’un foyer de saturnisme infantile dans un quartier de la commune du Port, Île de la Réunion. Revue d'Épidémiologie et de Santé Publique, 61(4), 329-337. (résumé)
- Article paru dans la revue AUTO RECYCLAGE n°108 - Novembre 2013
- Directive Européenne 2006/66/CE
- Pourquoi l'Europe espère beaucoup du recyclage des batteries, Les Échos, 19 septembre 2022.
- Voitures, vélos, smartphones : l'Europe va contraindre les industriels à verdir leurs batteries, Les Échos, 12 décembre 2022.
- Viviez : la SNAM se prépare à un nouveau marché.html, ladepeche.fr, 13 octobre 2010.
- SNAM recyclera les batteries Honda, Les Échos, 10 avril 2013.
- Voiture électrique : Volkswagen s’intéresse au recyclage des batteries, automobile-propre.com, 24 février 2019.
- SNAM lance la fabrication de batteries recyclées, Les Échos, 12 janvier 2022.
- Tanong, K. (2016). Récupération par voie hydrométallurgique des métaux à partir des déchets de piles mélangées (Doctoral dissertation, Université du Québec, Institut national de la recherche scientifique).
- Recyclage des batteries : de plus en plus « vert », automobile-propre.com, 23 janvier 2019.
- « L'économie circulaire », sur Ministère de la Transition écologique (consulté le )
- « Le réemploi des batteries pour une mobilité durable pour tous », sur CARA, (consulté le ).
- « Rapport annuel de l'Observatoire des véhicules hors d'usage - Données 2018 », sur La librairie ADEME (consulté le )
- « DRA06 – Opération B3 : Seconde vie des batteries Li-ion | Ineris », sur www.ineris.fr (consulté le ).
- « Mob-Energy - Découvrez nos solutions », sur Mob-Energy (consulté le )
- « Le Black Swan, premier bateau à passagers équipé de batteries de seconde vie e... », sur fr.media.renaultgroup.com (consulté le )
- « Re-Factory : le site de Flins entre dans le cercle de l'économie circulaire - Renault Group », sur www.renaultgroup.com (consulté le ).
- (en) Honorat Quinard, Eduardo Redondo-Iglesias, Serge Pelissier et Pascal Venet, « Fast Electrical Characterizations of High-Energy Second Life Lithium-Ion Batteries for Embedded and Stationary Applications », Batteries, vol. 5, no 1,‎ , p. 33 (ISSN 2313-0105, DOI 10.3390/batteries5010033, lire en ligne, consulté le ).
- « L'équilibrage des batteries » (consulté le ).
- SNAM produit des alliages à partir de batteries, Les Échos, 6 mars 2013.
Voir aussi
Articles connexes
Liens externes
- (fr) ADEME
- (fr) Filière SNAM
- (fr) Commissariat à l'Énergie Atomique