Adrien Chenot
Adrien Chenot, né le à Bar-sur-Aube[1], et, mort le à Paris[2], est un ingénieur français, connu pour ses inventions en métallurgie ainsi que ses recherches sur les gaz manufacturés. Il est notamment l'inventeur d'un des premiers procédés modernes de réduction directe du minerai de fer, fondé sur l'utilisation de charbon réagissant avec le minerai dans des cornues. Il expose les premiers échantillons de minerai de fer préréduit à l'Exposition universelle de Lisbonne de 1849[3], et est récompensé par une médaille d'or à Exposition universelle de Paris de 1855[L 1] - [note 1].
Nom de naissance | Claude Bernard Adrien Chenot |
---|---|
Naissance |
Bar-sur-Aube (France) |
Décès |
Paris (France) |
Nationalité | Français |
Domaines | Métallurgie, gaz manufacturés |
---|---|
Diplôme | École des mines de Paris |
Biographie
Né à Bar-sur-Aube, il est scolarisé à Nancy puis à Paris. En 1820, il entre à l'École des mines de Paris, et au sortir de cette école, il est attaché au Secrétariat général de la direction des ponts et chaussées. Il quitte quelque temps après ce poste pour exploiter des mines en Auvergne[3].
En 1826, il est sollicité par le duc de Raguse pour y mener des études métallurgiques à Châtillon-sur-Saône, où il dépose un premier brevet relatif à la fabrication directe du fer en traitant le minerai en poudre, mêlé de charbon, sur une sole de four à réverbère. En 1932, il construit à son domicile de Haute-Saône un premier appareil de réduction directe, qui fait sensation chez les maîtres de forges voisins, puis vient s'installer à Clichy-la-Garenne[3].
Il s’intéresse également à la production de gaz manufacturé, plus particulièrement les gaz de bois pour l'alimentation des fours à réverbère. Jusqu'en 1842, il travaille et brevette sur les gaz, les huiles de schiste, les sulfates de plomb, etc.. Il invente l'emploi d'alcalins pour la déphosphoration et la désulfuration de gaz manufacturés, et propose une classification des gaz combustibles fondée sur leur réactivité avec les alcalins. Il étudie l'emploi des matériaux poreux, les éponges, pour améliorer la production des gaz, etc[3].
En 1849, il se replonge dans ses recherches métallurgiques liées à la réduction des oxydes métalliques[3]. Le développement de la métallurgie directe, qui consiste à produire des métaux sans passer par les étapes de fusion (au haut fourneau) et d'affinage (alors réalisé péniblement par puddlage), passe par une optimisation scientifique des réactions chimiques réalisées jadis empiriquement dans les bas fourneaux. Cette approche lui semble alors capable de révolutionner la métallurgie :
« En effet, dégager la chaleur par oxydation et l'absorber par réduction en donnant lieu à des courants électro-chimiques et électro-dynamiques, qui répartissent rapidement les effets locaux dans l'univers, tel est le grand mécanisme qui fonctionne dans la nature par les actions des corps à l'état naissant ou d'éponges. La science de la fabrication des éponges métalliques doit donc désormais servir de base non seulement à l'art métallurgique, mais à tous les autres[3]. »
— C.-B.-A. Chenot, 1849
Sa connaissance de la production des gaz réducteurs est essentielle pour la mise au point de ses procédés de réduction d'oxydes : il améliore simultanément l'obtention des gaz nécessaires à ses procédés métallurgiques, tout comme les procédés eux-mêmes. Il comprend également l'importance qu'a la pureté du minerai pour assurer un intérêt économique aux procédés de réduction directe, et invente une « électrotrieuse » qui retire aux minerais bruts une partie importante de leur gangue stérile[3].
Ses recherches concernent l'obtention d'éponges métalliques de beaucoup de corps (aluminium, calcium, silicium, baryum, etc.), dont il étudie aussi les propriétés de leurs alliages avec le fer[3].
Chenot meurt en 1855, âgé donc de seulement 52 ans, encore actif mais très affaibli par les gaz inhalés lors de ses expérimentations. Il est d'ailleurs l'un des premiers à avoir signalé la toxicité du monoxyde de carbone[3] - [5] - [6].
Procédé Chenot de réduction directe
Principe
Le procédé Chenot est un des tout premiers procédés de réduction directe succédant aux bas fourneaux. Il s'agit d'un four à cornues de 10 m de haut, 1,5 m de large et 0,5 m de profondeur, associées par paires et dont les parois sont chauffées par 4 feux de houille. Les cornues sont chargées par le haut avec un mélange de charbon de bois et de minerai de fer, et leur contenu est évacué vers le bas dès que la charge est suffisamment réduite[P 1] - [G 1] - [4]. Malgré la présence d'un refroidisseur sous les cornues, conçu pour restituer sa chaleur au minerai enfourné, le « mode de chauffage est […] fort imparfait ; on perd plus de chaleur au-dehors qu'on en utilise dans la cornue même[G 2] ». En effet, pour produire une tonne de minerai de fer préréduit, le procédé Chenot consomme 350 kg de charbon de bois et 780 kg de houille, soit bien plus que les hauts fourneaux d'alors qui réalisent à la fois la fusion et la réduction, en consommant moins de 1 000 kg de coke[note 2] ; le rendement thermique du procédé est alors estimé à 26%, à comparer aux 70 voire 80% des hauts fourneaux de l'époque[G 4]. Ainsi, Isaac Lowthian Bell estime le coût en combustible 2,3 fois supérieur, et la perte en 3,5 fois supérieure à une fabrication par haut fourneau et convertisseur Bessemer[8] - [4].
Le minerai utilisé doit être d'excellente qualité (80 à 82% d'hématite), et séjourne près de 8 jours dans l'appareil (moitié du temps dans la cornue, puis dans le refroidissoir[4]). Les chargements et vidanges sont cependant partiels, donc plus réguliers : on compte une capacité de traitement de 1,2 à 1,5 tonne par jour de minerai, soit 400 tonnes annuelles par unité de production, bien loin des capacités de production des hauts fourneaux de l'époque[G 3]. L'éponge de fer obtenue contient 13% de stériles, qu'il faut chauffer et cingler, ou fondre, pour obtenir une masse de fer utilisable[G 5].
Impact technique
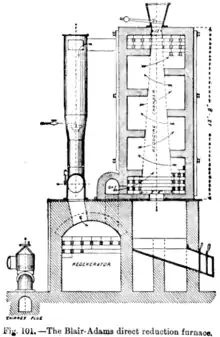
Le procédé marque cependant fortement ses contemporains car il exploite et valide la compréhension nouvelle des réactions chimiques d'oxydoréduction en métallurgie. Mais, bien qu'il illustre la parfaite connaissance de son auteur de la métallurgie moderne, il suscite de nombreuses interrogations quant à sa rentabilité :
« On a peine à comprendre aujourd'hui qu'on ait pu considérer à l'origine le procédé Chenot comme destiné à révolutionner l'industrie du fer, alors qu'il ne peut s'appliquer qu'à des minerais absolument purs, toutes les fois qu'on ne se résout pas à refondre l'éponge au creuset ou au four Martin. On ne comprend pas davantage que, dans une seule usine, dix fours aient pu être montés, représentant une dépense considérable, pour fabriquer un produit entrainant, par tonne d'éponge, une consommation de 1 400 kilos de charbon de bois pour la réduction et 1 723 kilos de houille pour le chauffage des cornues[note 3] : on ne pouvait transformer l'éponge en fer qu'en l'agglomérant au feu comtois au prix d'une nouvelle consommation de charbon et d'un déchet considérable[L 5]. »
— A. Ledebur, Manuel théorique et pratique de la métallurgie du fer
Opérationnel dans les années 1850 dans quelques usines en France (à l'usine de Chenot de Clichy en 1855, à Pontcharra en 1856 et Hautmont en 1857), en Espagne (à Barakaldo en 1852), en Belgique (à Couillet en 1856)[P 2] et en Italie[L 1]. Le procédé est également essayé aux États-Unis où une variante légèrement améliorée[note 4] par Blair fonctionne à Pittsburg jusqu'en 1846. Un autre four, à Ravensdale (North Staffordshire (en)), démarre en 1875, sans s'avérer plus rentable[G 7].
L'anglais Yates tire parti du fait que les foyers chauffant les cornues peuvent être alimentés par un gaz au lieu de houille, et propose dans ce sens une modification du procédé Chenot en 1860[G 6] - [P 3].
En 1860 aussi, l'américain Renton puis, en 1875, le français Verdié à Firminy, proposent une variante plus originale, consistant à utiliser la chaleur perdue à la cheminée des fours de puddlage[note 5] pour chauffer une cornue de dimension réduite. Mais, si « au premier abord, l’opération semble rationnelle, la réduction est incomplète, le déchet élevé, le bas de la cornue […] rapidement corrodé. Il est toujours difficile de coordonner, dans un même four, deux opération distinctes : la réduction par la chaleur perdue et l'affinage sur la sole du reverbère[G 6] ».
Enfin, son fils Eugène Chenot[note 6] poursuit les études de son père en construisant en 1862, à l'usine de la Ramade à Clichy, un four de réduction directe préfigurant les procédés continus de réduction directe aux gaz seuls, qui ne réussit cependant pas mieux que le procédé mis au point par son père[G 8].
L'obtention d'acier se fait en trempant une partie (environ un quart) de l'éponge de fer dans un liquide carburé (goudron de bois, etc.), puis en fondant les éponges carburées avec les éponges non carburées. L'acier obtenu ainsi est réputé de bonne qualité, quoiqu'il en existe de meilleurs. En 1867, le coût de revient de la tonne d'acier Chenot produit à Clichy est estimé à 1 097,29 Fr[P 4], et à 500 Fr à Barakaldo[P 5].
Autres contributions
Adrien Chenot a souffert des séquelles des intoxications au monoxyde de carbone subies lors de ses nombreuses expériences. Il a été notamment gravement intoxiqué en 1846, alors qu'il travaillait dans les usines du marquis de Sassenay, en Prusse. Selon lui, « l'oxyde de carbone se transforme en acide carbonique provoquant de ce fait une désoxydation mortelle. […] La cause des troubles physiopathologiques pourrait être également une brusque augmentation de la température due à la suroxydation du carbone dans le sang[5] ». Bien entendu, Chenot, qui « admet que l'oxyde de carbone joue dans le sang le [même] rôle de corps réducteur que dans la métallurgie[5] », ne peut proposer qu'une explication partielle dès lors qu'il n'analyse pas soigneusement les aspects physiologiques. Mais il reste le premier à proposer une théorie chimique du mécanisme d'intoxication par ce gaz[5] - [6]
Adrien Chenot militera aussi pour l'abrogation de la loi relative à l'établissement des grandes lignes de chemin de fer en France.
Publications et œuvres
- Claude Bernard Adrien Chenot, Souvenir de 1855. Exposition universelle. Crépuscule d'un nouveau système de métallurgie : rationnelle, positive et philosophique, Firmin Didot Frères, , 74 p. (OCLC 43484634, lire en ligne)
- Claude Bernard Adrien Chenot, Les Chaudières à vapeur sont des machines électriques. Les moyens de sûreté actuels sont impuissants. Moyen de générer la vapeur sans aucun danger. Machine à pressions égales et constantes permettant l'emploi des réactions chimiques., Carilian-Goeury et Dalmont, , 130 p. (OCLC 23422713, lire en ligne)
- Claude Bernard Adrien Chenot, Question des sucres d'un point de vue général, Thibaud-Landriot, , 76 p. (ASIN B001CE1Q5Q)
- Claude Bernard Adrien Chenot, Exercice 1845. L'Entente cordiale et Cie, société humanitaire pour la traite des blancs par les marons sous prétexte d'émancipation des noirs. Question des fers, fontes et aciers. Proposition du retrait de la loi de 1842 sur les chemins de fer, Fain et Thunot, , 35 p. (ASIN 2B001DAGG4U)
- Claude Bernard Adrien Chenot, Chemins de fer. Compagnie anonyme l'Entente cordiale et Cie, capital social la France… lettre à messieurs les membres des deux Chambres… Inopportunité des chemins de fer en France…, Fain et Thunot, , 34 p. (ASIN B001DAKH90)
- Claude Bernard Adrien Chenot, Note sur l'oxyde de carbone pur,
Notes et références
Notes
- Le métallurgiste américain Henry Marion Howe (en), très réservé sur l'efficacité du procédé, relativise les critères d'attribution (apparently on questionable grounds) de cette distinction[4].
- Ou 800 kg de charbon de bois, pour les quelques hauts fourneaux utilisant encore ce combustible[G 3]. À noter qu'un haut fourneau moderne ne consomme, à la fin du XXe siècle, que 480 kg de coke à la tonne de fonte[7].
- À la même époque, la production d'une tonne de fonte en fusion nécessite typiquement 740 kilos de charbon de bois[L 3] ou 1 100 kilos de coke[L 4].
- Les cornues sont cylindriques mais « en résumé, l'appareil de Blair, présente quelques perfectionnement de détail mais les inconvénients de la réduction sans fusion subsistent tous[G 6] ».
- Le rendement thermique d'un four à puddler ne dépasse pas 7 %[L 6].
- Né à Saponcourt en 1835, diplômé des Arts et Métiers (Angers, promotion 1850), Eugène Chenot débute dans les usines métallurgiques de Wendel. Il est ensuite associé dirigeant avec son frère aîné, Alfred, dans l'entreprise familiale à Clichy[9]. Après s'être ruiné dans des recherches sur la fabrication de vin à partir de raisins secs, il s'installe à la Guadeloupe pour y diriger l'usine sucrière Blanchet. Il meurt à Capesterre-Belle-Eau le 22 août 1908[10].
Références
- Archives de l'Aube, commune de Bar-sur-Aube, acte de naissance non numérotée, année XI républicaine (consulté le 12 octobre 2014)
- Archives de Paris reconstituées, acte de naissance non numérotée, année 1855 (consulté le 12 octobre 2014)
- Jean Chrétien Ferdinand Hoefer, Nouvelle biographie universelle depuis les temps les plus reculés jusqu’à nos jours, t. 10, Firmin-Didot Frères, (lire en ligne), p. 210-211
- [PDF](en) Henry Marion Howe, The metallurgy of steel, vol. 1, The scientific publishing company, (lire en ligne), p. 278-280
- Mirko Dražen Grmek, Raisonnement expérimental et recherches toxicologiques chez Claude Bernard, Librairie Droz S.A., (ISBN 978-2-600-03369-5, lire en ligne), p. 108-109
- (en) Christopher P. Hopper, Paige N. Zambrana, Ulrich Goebel et Jakob Wollborn, « A brief history of carbon monoxide and its therapeutic origins », Nitric Oxide, vol. 111-112,‎ 2021-06-xx, p. 45–63 (DOI 10.1016/j.niox.2021.04.001, lire en ligne, consulté le )
- [PDF](en) Best Available Techniques (BAT) Reference Document for Iron and Steel Production, Direction régionale de l'environnement, de l'aménagement et du logement, , 597 p. (lire en ligne), p. 291-293 ; 338-345
- (en) Isaac Lowthian Bell, Principles of the Manufacture of Iron and Steel : With some notes on the economic conditions of their production, George Routledge and Sons, , 34 p. (lire en ligne)
- Notice d'autorité : « Chenot, Eugène », sur symogih.org, Laboratoire de recherche historique Rhône-Alpes (LARHRA) (consulté le ).
- [PDF]« Notice nécrologique d'Eugène Chenot », Société des ingénieurs Arts et Métiers,
- Emmanuel-Louis Grüner, Traité de métallurgie — métallurgie générale, t. second, procédé de métallurgiques, chauffage et fusion, grillage, affinage et réduction, Dunod, (lire en ligne), partie I
- p. 244-249
- p. 244
- p. 245
- p. 247-248
- p. 249
- p. 251
- p. 250
- p. 240
- Adolf Ledebur (trad. Barbary de Langlade revu et annoté par F. Valton), Manuel théorique et pratique de la métallurgie du fer, t. II, Librairie polytechnique Baudry et Cie éditeur,
- p. 350
- p. 351-352
- p. 82 ; 99-101
- p. 90 ; 99-101
- p. 351
- p. 377-381
- J. Percy (trad. traduction supervisée par l'auteur), Traité complet de métallurgie, Paris, Librairie polytechnique de Noblet et Baudry éditeur, (lire en ligne)
- Tome 2, p. 532-545
- Tome 2, p. 533
- Tome 2, p. 545-550
- Tome 4, p. 168-171
- Tome 2, p. 536