Électronique imprimée
Le terme d'électronique imprimée désigne un ensemble de technologies qui ont émergées à partir des années 2010 et dans lesquelles des circuits électroniques entiers (composants et interconnection) sont réalisés par impression sur un substrat (polymère, céramique ou même papier). C'est une technologie très différente de celle du circuit imprimé, dans laquelle seule l'interconnexion est réalisée sur le substrat, sur lequel les composants, fabriqués séparément, sont implantés.
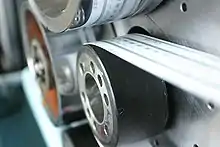
Des encres sont utilisées pour déposer sur un substrat (le plus fréquemment, papier ou polymère) des matériaux accomplissant les fonctions électriques voulues. Ces technologies sont adaptées à la réalisation en très grande quantité et à coûts très bas de circuits électroniques simples.
Méthodes de réalisation
Sur un substrat isolant, on ajoute des matériaux conducteurs et semi-conducteurs qui vont assurer les fonctions électroniques désirées. Ces matériaux sont dispersés dans une encre pour assurer leur disposition sur le substrat, à l'évaporation du solvant la couche désirée est créée[1]. Plusieurs techniques sont utilisées pour disposer l'encre sur le substrat. Au besoin, elles peuvent être combinées pour un même produit.
Impression jet d'encre
La technique la plus courante est celle de l'impression jet d'encre. Elle a entre autres avantages, celui de ne pas nécessiter l'usage d'un masque physique qu'il faut fabriquer : elle passe directement du modèle numérique au produit. Elle peut gérer de grandes tailles de substrat et une importante variété de matériaux. En revanche, la cadence de production est relativement limitée. Elle peut être améliorée en réalisant de grandes têtes d'injection, avec de très nombreux injecteurs pilotés en parallèle[1].
Sérigraphie
Dans le cas de la sérigraphie ((en) screen printing) l'encre est répartie sur le substrat selon le principe du pochoir. Le masque de sérigraphie est une toile composée d'un matériau tel que le nylon, masquée par un film continu complémentaire au motif désiré. Le film est positionné sur le substrat et l'encre est étalée à l'aide d'une raclette. Cette technologie est bon marché et adaptée à de très grands débits de production, son coût est faible, mais elle présente des limites de résolution. Typiquement, la résolution est comprise entre 50 et 150 µm[2].
- Machine de sérigraphie industrielle
- Principe de la sérigraphie. A: encre, B : raclette, C : motif, D : masque, E : cadre, F : impression
Impression offset
L'impression offset est une technique rapide, adaptée à de gros volumes de production, avec des coûts non récurrent assez élevés. Dans des travaux publiés en 2004[3], des motifs en encre d'argent avec une résolution de l'ordre de 20 μm ont été réalisés par impression offset. Un modèle (« gravure ») métallique est réalisé par un procédé électrolytique. Les motifs y sont créés en profondeur. L'encre est disposée dans le modèle, et reportée sur le substrat via un blanchet.
Impression par micro-contacts
L'impression par micro-contact offre une résolution excellente, largement sous le micron[4]. Dans cette technique, un « tampon » en polymère est réalisé, par moulage sur un wafer (sur lequel les motifs ont été réalisés par photolithographie). Le tampon est ensuite utilisé pour reporter l'encre sur le substrat.
- Réalisation d'un moule
- Encrage et application du moule
Impression laser
Une nouvelle technique d'impression laser a été démontrée en 2014[5]. Un wafer de verre, qui sert de substrat, est placé face à un wafer SOI. Un laser femtoseconde est utilisé pour arracher des microparticules de silicium, qui se déposent sur le substrat verre. En ajustant les propriétés du laser, on peut changer la taille et la cristallographie des particules de silicium, pour réaliser des fonctions électriques.
Substrats
Le choix du substrat est déterminé par la compatibilité avec le processus d'impression (recuit, mouillabilité de l'encre), les besoins de l'application (besoin ou non de flexibilité, transparence, résistance aux attaques chimiques, tenue à la températyre), et le coût[6]
Substrats en polymères
Les substrats constitués d'un film polymère, flexible et bon marché, sont les plus utilisés. On rencontre notamment des films de Polytéréphtalate d'éthylène (PET), Polynaphtalate d'éthylène (PEN), ou encore de polyimide, ce dernier étant caractérisé par une très bonne résistance aux hautes températures et aux agressions chimiques[6] - [7] - [8].
Papier
Le papier constitue le substrat le moins cher, et est donc étudié pour les dispositifs où la contrainte de réduction de coût est la plus forte. Il a une tolérance limitée à la température, ce qui limite les recuits utilisables. Le papier est calandré ou recouvert d'une finition hydrophobe, pour obtenir un état de surface qui permet d'une bonne tenue d'encre et une bonne résolution[9] - [10].
Céramique
Des substrats céramiques peuvent aussi être utilisés, lorsque des performances très élevées sont demandées, en matière de résistance à la température, de constante diélectrique ou de propriétés mécaniques. Un exemple de tel substrat est le dioxyde de zirconium (connu pour son utilisation comme faux diamant en joaillerie)[11]
Matériaux déposés
Métaux
La création des contacts électriques est le plus souvent obtenue avec un métal. L'encre est alors un colloïde, c'est-à-dire que des particules mésoscopiques de métal sont en suspension. Après évaporation du diluant, les particules métalliques sont agglomérées, mais un recuit est nécessaire pour établir des liaisons métalliques entre les grains et obtenir une bonne conductivité électrique. Une température de recuit élevée assure de meilleures propriétés électriques, mais contraint le choix du substrat, qui doit la supporter. Malgré son prix élevé, l'argent, excellent conducteur et se contentant de température de recuit modérée (de l'ordre de 200 °C), est le métal le plus utilisé. Le cuivre, le nickel, l'aluminium, l'or peuvent aussi être utilisés[12].
Les métaux ont une conductivité de l'ordre de 107 S/m, et restent la solution de choix pour réaliser l'interconnexion et les grilles des composants. Cependant, l'utilisation de métaux limite vite la flexibilité, en particulier au niveau des interfaces métal-polymère. Ainsi, quand la flexibilité est un critère important, on s'oriente vers des dispositifs se passant totalement de métaux, mais avec un important sacrifice en termes de conductivité. Des pâtes composant des particules métalliques ont une conductivité de l'ordre de 105 S/m, les solutions de graphites inorganiques sont légèrement en dessous, suivis des polymères conducteurs[13] - [14].
Oxydes métalliques
L'oxyde d'indium-étain est mis en œuvre pour réalisation d'électrodes dans des dispositifs qui ont besoin d'être transparents, comme pour l'affichage: en effet ce matériau a la propriété unique d'être à la fois conducteur électrique et transparent optiquement. Un autre oxyde métallique utilisé couramment, mais comme diélectrique, est le ZnO[12].
Des oxydes métalliques sont aussi mis en œuvre dans le rôle de semi-conducteurs. L'In2O3 est un semi-conducteur de type n, à grand gap et présentant une très bonne mobilité. Le CuO, quant à lui, est un semi-conducteur de type p, à faible gap et affichant une mobilité bien moindre. L'un et l'autre sont produits en déposant un précurseur et en opérant un recuit[15].
Carbone non-organique (nanotubes, graphène...)
Les nanotubes de carbone peuvent avoir un comportement électrique de type métal, ou de type semi-conducteur, selon le nombre de mailles atomiques dans leur circonférence. Ils peuvent constituer un moyen intéressant de réaliser des contacts électriques : ils ont une bonne conductivité, sont flexibles, éventuellement transparents, et contrairement aux métaux ne nécessitent aucun recuit[16] - [17].
Matériaux organiques
Des matériaux organiques sont également utilisés pour remplir des fonctions électriques.
Les semi-conducteurs organiques imprimables ont connu un important développement depuis les années 2000, et permettent désormais d'obtenir dans certains cas des transistors à effet de champ ayant des performances supérieures à ceux basés sur le silicium amorphe. Le PEDOT et le TCNQ font partie des molécules organiques servant de base à des composés semi-conducteurs[18] - [19].
Composants réalisés
Résistances
Les résistances sont obtenues en déposant sur une surface un matériau à conductivité assez faible. La valeur de la résistance est ajustée en jouant sur la géométrie, aussi bien sur les propriétés du matériau. Des polymères comme le PEDOT:PSS sont utilisés[20]. D'autres auteurs ont présenté des résistances en argent, produites par dépôt alterné d'encres de nitrate d'argent et d'acide ascorbique qui réagissent in situ pour produire une couche métallique[21].
Capacités
Trois méthodes sont utilisées pour réaliser des capacités. La plus simple est d'imprimer, de part et d'autre du substrat, des motifs en regard. C'est donc le substrat lui-même qui sert de diélectrique. Etant relativement épais (plusieurs centaines de nanomètres), il a une tenue électrique importante, mais la capacité surfacique est limitée. Ainsi, une capacité de l'ordre du nanofarad occupe plusieurs centimètres carrés. En outre, les deux ports de la capacité se situent des deux côtés opposés du substrat, ce qui peut être une contrainte de conception[21].
Des performances bien supérieures peuvent être obtenues en déposant sur la même face du substrat une première électrode, un diélectrique (organique ou inorganique) et une deuxième électrode. Pour augmenter encore la valeur de capacité par unité de surface, les couches peuvent être multipliées[22].
Enfin pour des valeurs faibles (quelques dizaines de picofarads), on peut réaliser des capacités coplanaires : on utilise le couplage capacitif entre deux électrodes situées sur la même face du substrat, parallèle, avec au besoin un motif inter-digité ou en spirale[21].
Inductances
Si les inductances discrètes prennent la forme d'un solénoïde autour d'un noyau ferromagnétique, les inductances imprimées sont généralement formées d'une simple piste en forme de spirale[21]. Néanmoins, certains auteurs ont démontré la possibilité d'imprimer un cœur ferromagnétique à base de cobalt pour réduire l'encombrement[23].
transistors à effet de champs
Un transistor à effet de champs entièrement constitué de matériaux polymère et réalisé par impression a été présenté dès 1994[13].
Optronique
Des diodes électroluminescentes organiques blanches réalisées par sérigraphie ont été présentées en 2009. Dans cette approche, une couche de polystyrène sert de polymère "hôte". Il est chargé de composés aromatiques qui assurent l'émission lumineuse[24].
Batteries
L'impression de batteries a été développée pour permettre à des systèmes électroniques imprimés de comporteur leur propre source d'énergie. Les électrodes sont déposées par impression, de même qu'un gel contenant l'électrolyte. Les chimies les plus utilisées sont de type lithium-ion et zinc-manganèse. Comme pour les capacités, la géométrie peut être en empilement (un multicoucle horizontal) ou coplanaire. Dans le deuxième cas, les électrodes se situent de part et d'autre d'un zone d'électrolyte, cette géométrie est plus adaptée aux systèmes étirables (moins de risque de court-circuit). Des batteries imprimées sont réalisées sur substrat textile, papier, et polymère[25].
Caractéristiques
Flexibilité
L'une des caractéristiques souvent mise en avant pour l'électronique imprimée est la flexibilité. En choisissant un substrat polymère (comme le polyimide) et des matériaux actifs adaptés, on peut en effet réaliser des circuits électroniques flexibles ou même étirables, ce qui a des applications dans le domaine médical notamment[26].
Marchés et aspects économiques
La délimitation des marchés visés par l'électronique imprimée résulte des considérations suivantes[27] :
- Les performances sont limitées (miniaturisation, vitesse d'horloge), ce qui ne permet pas de réaliser des circuits très complexes.
- Le coût marginal de production est très faible.
- La technologie est adaptée à de gros volumes.
Ainsi, les applications visées sont des circuits simples, dans des applications grand public où les réductions de coût sont recherchées.
Radio-identification (RFID)
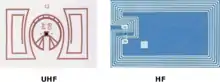
Les marqueurs RFID ont été l'un des premiers marchés visés, représentant une application à grand volume de production et faible valeur ajoutée : dans l'objectif de généraliser le marquage RFID des articles de consommation, le coût d'un marqueur doit être de l'ordre de 0,01US$[28]. Au début des années 2000, les marqueurs comportaient une antenne boucle imprimée, tandis que la partie intelligente était une puce silicium rapportée. L'effort s'est porté sur le développement de transpondeurs entièrement imprimés, beaucoup moins coûteux, mais nécessitant des progrès technologiques[29] - [30].
En 2010, un transpondeur entièrement imprimé dans la gamme 13.56 MHz est présenté[28]. La réduction des coûts permise par l'impression a provoqué le décollage du marché de la radio-identification[31].
Écrans plats
Les progrès de l'optronique imprimée (diode électroluminescente organique imprimées) ont permis de mettre au points des écrans plats imprimés. L'entreprise japonaise Joled a lancé fin 2019 la production d'écrans plats à led organiques produit par impression[32] - [33].
Standards et structuration de la filière
A partir de 2007, l'(en) International Electronics Manufacturing Initiative a publié une feuille de route prévoyant les jalons de l'évolution technologique de l'électronique imprimée. L'objectif de cette démarche est de structurer la chaîne de valeur, à l'image de l'ITRS pour les technologies sur silicium[34].
Une revue scientifique spécialisée, (en) Flexible and Printed Electronics parait tout les trois mois depuis [35] .
Références
- (en) ZhouPing Yin, YongAn Huang, NingBin Bu et XiaoMei Wang, « Inkjet printing for flexible electronics: Materials, processes and equipments », Chinese Science Bulletin, vol. 55, no 30, , p. 3383–3407 (ISSN 1001-6538 et 1861-9541, DOI 10.1007/s11434-010-3251-y, lire en ligne, consulté le )
- (en) Woo Jin Hyun, Ethan B. Secor, Mark C. Hersam et C. Daniel Frisbie, « High-Resolution Patterning of Graphene by Screen Printing with a Silicon Stencil for Highly Flexible Printed Electronics », Advanced Materials, vol. 27, no 1, , p. 109–115 (DOI 10.1002/adma.201404133, lire en ligne, consulté le )
- (en) Marko Pudas, Juha Hagberg et Seppo Leppävuori, « Printing parameters and ink components affecting ultra-fine-line gravure-offset printing for electronics applications », Journal of the European Ceramic Society, vol. 24, nos 10-11, , p. 2943–2950 (DOI 10.1016/j.jeurceramsoc.2003.11.011, lire en ligne, consulté le )
- (en) Younan Xia et George M. Whitesides, « SOFT LITHOGRAPHY », Annual Review of Materials Science, vol. 28, no 1, , p. 153–184 (ISSN 0084-6600, DOI 10.1146/annurev.matsci.28.1.153, lire en ligne, consulté le )
- (en) Urs Zywietz, Andrey B. Evlyukhin, Carsten Reinhardt et Boris N. Chichkov, « Laser printing of silicon nanoparticles with resonant optical electric and magnetic responses », Nature Communications, vol. 5, no 1, , p. 1–7 (ISSN 2041-1723, DOI 10.1038/ncomms4402, lire en ligne, consulté le )
- Joseph Chang, Tong Ge et Edgar Sanchez-Sinencio, « Challenges of printed electronics on flexible substrates », (:unav), (DOI 10.1109/mwscas.2012.6292087, lire en ligne, consulté le ).
- (en) Valerio Zardetto, Thomas M. Brown, Andrea Reale et Aldo Di Carlo, « Substrates for flexible electronics: A practical investigation on the electrical, film flexibility, optical, temperature, and solvent resistance properties », Journal of Polymer Science Part B: Polymer Physics, vol. 49, no 9, , p. 638–648 (ISSN 1099-0488, DOI 10.1002/polb.22227, lire en ligne, consulté le ).
- Jarrod Vaillancourt, Haiyan Zhang, Puminun Vasinajindakaw et Haitao Xia, « All ink-jet-printed carbon nanotube thin-film transistor on a polyimide substrate with an ultrahigh operating frequency of over 5 GHz », Applied Physics Letters, vol. 93, no 24, , p. 243301 (ISSN 0003-6951, DOI 10.1063/1.3043682, lire en ligne, consulté le ).
- Ting Leng, Xianjun Huang, KuoHsin Chang et JiaCing Chen, « Graphene Nanoflakes Printed Flexible Meandered-Line Dipole Antenna on Paper Substrate for Low-Cost RFID and Sensing Applications », IEEE Antennas and Wireless Propagation Letters, vol. 15, , p. 1565–1568 (ISSN 1536-1225 et 1548-5757, DOI 10.1109/LAWP.2016.2518746, lire en ligne, consulté le ).
- (en) K. Torvinen, J. Sievänen, T. Hjelt et E. Hellén, « Smooth and flexible filler-nanocellulose composite structure for printed electronics applications », Cellulose, vol. 19, no 3, , p. 821–829 (ISSN 0969-0239 et 1572-882X, DOI 10.1007/s10570-012-9677-5, lire en ligne, consulté le ).
- (en) Sharadindu Gopal Kirtania, Manjurul Ahsan Riheen, Sun Ung Kim et Karthik Sekhar, « Inkjet Printing on a New Flexible Ceramic Substrate for Internet of Things (IoT) Applications », Micromachines, vol. 11, no 9, , p. 841 (ISSN 2072-666X, DOI 10.3390/mi11090841, lire en ligne, consulté le ).
- (en) Jolke Perelaer, Patrick J. Smith, Dario Mager et Daniel Soltman, « Printed electronics: the challenges involved in printing devices, interconnects, and contacts based on inorganic materials », Journal of Materials Chemistry, vol. 20, no 39, , p. 8446 (ISSN 0959-9428 et 1364-5501, DOI 10.1039/c0jm00264j, lire en ligne, consulté le )
- (en) F. Garnier, R. Hajlaoui, A. Yassar et P. Srivastava, « All-Polymer Field-Effect Transistor Realized by Printing Techniques », Science, vol. 265, no 5179, , p. 1684–1686 (ISSN 0036-8075 et 1095-9203, DOI 10.1126/science.265.5179.1684, lire en ligne, consulté le )
- (en) W. Clemens, W. Fix, J. Ficker et A. Knobloch, « From polymer transistors toward printed electronics », Journal of Materials Research, vol. 19, no 7, , p. 1963–1973 (ISSN 0884-2914 et 2044-5326, DOI 10.1557/JMR.2004.0263, lire en ligne, consulté le )
- (en) Suresh Kumar Garlapati, Tessy Theres Baby, Simone Dehm et Mohammed Hammad, « Ink-Jet Printed CMOS Electronics from Oxide Semiconductors », Small, vol. 11, no 29, , p. 3591–3596 (DOI 10.1002/smll.201403288, lire en ligne, consulté le )
- (en) Krisztián Kordás, Tero Mustonen, Géza Tóth et Heli Jantunen, « Inkjet Printing of Electrically Conductive Patterns of Carbon Nanotubes », Small, vol. 2, nos 8-9, , p. 1021–1025 (ISSN 1613-6810 et 1613-6829, DOI 10.1002/smll.200600061, lire en ligne, consulté le )
- (en) Mingjing Ha, Yu Xia, Alexander A. Green et Wei Zhang, « Printed, Sub-3V Digital Circuits on Plastic from Aqueous Carbon Nanotube Inks », ACS Nano, vol. 4, no 8, , p. 4388–4395 (ISSN 1936-0851 et 1936-086X, DOI 10.1021/nn100966s, lire en ligne, consulté le )
- (en) Jun Li, Yan Zhao, Huei Shuan Tan et Yunlong Guo, « A stable solution-processed polymer semiconductor with record high-mobility for printed transistors », Scientific Reports, vol. 2, no 1, (ISSN 2045-2322, PMID 23082244, PMCID PMC3474992, DOI 10.1038/srep00754, lire en ligne, consulté le )
- (en) Howard E. Katz, « Recent Advances in Semiconductor Performance and Printing Processes for Organic Transistor-Based Electronics », Chemistry of Materials, vol. 16, no 23, , p. 4748–4756 (ISSN 0897-4756 et 1520-5002, DOI 10.1021/cm049781j, lire en ligne, consulté le )
- (en) Sungjune Jung, Antony Sou, Enrico Gili et Henning Sirringhaus, « Inkjet-printed resistors with a wide resistance range for printed read-only memory applications », Organic Electronics, vol. 14, no 3, , p. 699–702 (DOI 10.1016/j.orgel.2012.12.034, lire en ligne, consulté le )
- S M Bidoki, J Nouri et A A Heidari, « Inkjet deposited circuit components », Journal of Micromechanics and Microengineering, vol. 20, no 5, , p. 055023 (ISSN 0960-1317 et 1361-6439, DOI 10.1088/0960-1317/20/5/055023, lire en ligne, consulté le )
- Benjamin S. Cook, James R. Cooper et Manos M. Tentzeris, « Multi-Layer RF Capacitors on Flexible Substrates Utilizing Inkjet Printed Dielectric Polymers », IEEE Microwave and Wireless Components Letters, vol. 23, no 7, , p. 353–355 (ISSN 1531-1309 et 1558-1764, DOI 10.1109/LMWC.2013.2264658, lire en ligne, consulté le )
- Hoseon Lee, Manos M. Tentzeris, P. Markondeya et Murali K. P. Raj, « Inkjet-printed ferromagnetic nanoparticles for miniaturization of flexible printed RF inductors », (:unav), (DOI 10.1109/aps.2013.6711157, lire en ligne, consulté le )
- (en) D.-H. Lee, J.S. Choi, H. Chae et C.-H. Chung, « Screen-printed white OLED based on polystyrene as a host polymer », Current Applied Physics, vol. 9, no 1, , p. 161–164 (DOI 10.1016/j.cap.2008.01.004, lire en ligne, consulté le )
- (en) Adnan E. Ali, Varun Jeoti et Goran M. Stojanović, « Fabric based printed-distributed battery for wearable e-textiles: a review », Science and Technology of Advanced Materials, vol. 22, no 1, , p. 772–793 (ISSN 1468-6996 et 1878-5514, PMID 34552390, PMCID PMC8451651, DOI 10.1080/14686996.2021.1962203, lire en ligne, consulté le )
- (en) Yuhao Liu, Matt Pharr et Giovanni Antonio Salvatore, « Lab-on-Skin: A Review of Flexible and Stretchable Electronics for Wearable Health Monitoring », ACS Nano, vol. 11, no 10, , p. 9614–9635 (ISSN 1936-0851 et 1936-086X, DOI 10.1021/acsnano.7b04898, lire en ligne, consulté le )
- (en) Mark A. M. Leenen, Volker Arning, Heiko Thiem et Jürgen Steiger, « Printable electronics: flexibility for the future », physica status solidi (a), vol. 206, no 4, , p. 588–597 (DOI 10.1002/pssa.200824428, lire en ligne, consulté le )
- Minhun Jung, Jaeyoung Kim, Jinsoo Noh et Namsoo Lim, « All-Printed and Roll-to-Roll-Printable 13.56-MHz-Operated 1-bit RF Tag on Plastic Foils », IEEE Transactions on Electron Devices, vol. 57, no 3, , p. 571–580 (ISSN 0018-9383 et 1557-9646, DOI 10.1109/TED.2009.2039541, lire en ligne, consulté le )
- V. Subramanian, J.M.J. Frechet, P.C. Chang et D.C. Huang, « Progress Toward Development of All-Printed RFID Tags: Materials, Processes, and Devices », Proceedings of the IEEE, vol. 93, no 7, , p. 1330–1338 (ISSN 0018-9219, DOI 10.1109/JPROC.2005.850305, lire en ligne, consulté le )
- V. Subramanian, P.C. Chang, D. Huang et J.B. Lee, « All-printed RFID tags: materials, devices, and circuit implications », (:unav), (DOI 10.1109/vlsid.2006.34, lire en ligne, consulté le )
- Future Market Insights Global and Consulting Pvt Ltd, « RFID Printers Market Expected to Witness a CAGR of 8.2% through 2018-2028- Future Market Insights », sur GlobeNewswire News Room, (consulté le )
- « Le japonais Joled construit une usine d’assemblage d’écrans Oled fabriqués par impression »,
- « Joled lance la première production d’écrans Oled par impression au monde », L'Usine Nouvelle,
- « New iNEMI roadmap to include printed electronics. - Free Online Library », sur www.thefreelibrary.com (consulté le ).
- « ShieldSquare Captcha », sur hcvalidate.perfdrive.com (consulté le )