Façonnage du verre
On classe généralement dans le façonnage du verre les opérations effectuées sur les objets en verre après qu'ils ont été mis en forme à la sortie du four de fusion et soumis à la recuisson.
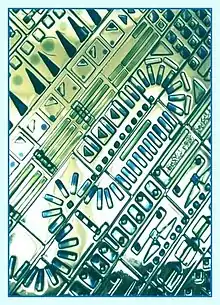
Cependant certains produits en verre, et notamment le verre plat (verre à glace, verre à vitre, verre coulé) et les tubes, sortent de l'usine en format standard de grandes dimensions et doivent être, avant tout façonnage, séparés en éléments correspondant chacun à un objet (une vitre, un pare-brise, un tube d'une longueur déterminée).
C'est la découpe.
Celle-ci est le plus souvent effectuée à l'aide d'une molette en acier au tungstène ou d'un diamant que l'on appuie sur le verre pour y tracer le contour désiré.
Quelques chocs appliqués sur la face opposée à la découpe au moyen d'un manche de l'outil, développent les fissures amorcées par ce dernier et la découpe est ensuite achevée en provoquant une flexion de part et d'autre du tracé. S'il ne s'agit pas d'une simple coupe rectiligne on supprime les fragments de verre restant à éliminer par flexion ou à la pince à gruger.
Pour des dalles d'une certaine épaisseur l'emploi d'une scie rotative à couronne abrasive assure une découpe régulière. Le tronçonnage des tubes se fait également par traçage au diamant, sur le tube en rotation, de la découpe à effectuer et en libérant par un léger choc et le tronçon ainsi préparé. Certains façonnages sont effectués dans les verreries, les autres par les façonniers spécialisés (miroitiers, souffleurs de verre au chalumeau, opticiens, lunetiers, vitraillistes…) ou par les industries utilisatrices.
Le façonnage peut se faire de deux façons :
- À froid par traitement de la surface des objets en verre sans déformation de masse vitreuse, par enlèvement de matière.
- À chaud par déformations de tout ou partie de la masse de l'objet en verre préalablement rendu malléable par une forte augmentation de température uniforme ou localisée. Une des techniques les plus spectaculaires est appelée fusing, que certains artistes appliquent à des projets ambitieux.
Mais il faut en outre tenir compte de la trempe, thermique ou chimique, qui n'entre exactement dans aucune de ces deux catégories et correspond obligatoirement à un dernier façonnage sur des objets ayant acquis leur forme définitive.
Façonnage à froid
Le façonnage à froid consiste à modifier l'aspect extérieur des objets en verre :
- soit mécaniquement, en usant les parties de ces objets que l'on désire éliminer par arrachage progressif des particules de verre qui les composent ;
- soit chimiquement, en les faisant disparaître par dissolution sous l'action d'un produit capable d'attaquer le verre (l'acide fluorhydrique le plus souvent) ;
- soit par revêtement, en appliquant sur la surface des objets envers des produits (métaux, peinture, et émaux, composés chimiques) auxquels leur mode d'application et leurs caractéristiques assurent une adhérence efficace au verre.
L'usure par frottement
L'arrachage progressif des particules de verre qui caractérise ce procédé est obtenu par le frottement rapide et répété, ou par projection brutale, sur la surface à traiter de matières dures appelées « abrasifs ».
Les principaux abrasifs utilisés dans le cadre de l'usure par frottement sont le sable, le grès, l'émeri, le carborundum, le diamant. Ce dernier étant le plus efficace mais aussi de loin le plus coûteux. Le choix entre ces différents produits dépend de la nature des travaux à exécuter et de leurs prix de revient très différents les uns des autres.
L'agressivité, et donc l'efficacité, des abrasifs dépend de plusieurs éléments :
- leur dureté superficielle ;
- la pression qu'on leur fait exercer sur le verre ;
- la vitesse de frottement réalisée, qui joue un rôle capital.
Une autre caractéristique importante des abrasifs utilisés est la grosseur de leurs grains. C'est pourquoi chaque opération d'usure superficielle peut comporter trois étapes :
- un dégrossissage, ou ébauche, pour lequel on emploie des grains abrasifs d'une certaine grosseur ;
- un doucissage qui, à l'aide de grains beaucoup plus fin, permet d'aplanir la surface en la rendant régulière mais dépolie ;
- un polissage employant des grains d'une extrême finesse (généralement de l'oxyde de fer sous forme de potée, ou d'oxyde de cérium) qui donne à la surface traitée un aspect uniforme et restituent au verre sa transparence.
L'attaque du verre par l'outil peut se produire de trois façons :
- l'outil peut être directement abrasif : soit taillé dans une pierre naturelle agressive comme le grès et l'émeri ; soit artificiellement formé par l'agglomération de grains d'abrasif séparés plus ou moins gros (grès, émeri, carborundum) soit formé d'une ossature métallique sur laquelle est appliqué et fixé, sur les seules parties de sa surface appelées à attaquer le verre, un revêtement formé d'une concrétion diamantée (poussière plus ou moins fine de diamant agglomérée au moyen d'un liant très résistant qui peut-être au besoin du bronze ou de l'acier…).
- il peut être utilisé pour user le verre sans être directement abrasif : il est alors généralement en fonte et entraîne dans son mouvement de rotation des grains de sable plus ou moins fins en suspension dans de l'eau que l'on insère entre lui et l'objet en verre à attaquer et auxquels revient le rôle d'abrasifs (il porte alors le nom de lapidaire, platine ou rondeau).
- il peut être enfin utilisé pour le polissage : Il ne s'agit plus alors d'user le verre, qui a déjà pris sa forme définitive, mais de parfaire la régularité de sa surface en réalisant une sorte de lustrage. On peut employer des outils en bois, en métal recouvert de feutre, ou en feutre aggloméré, mais ils sont le plus souvent en liège naturel ou aggloméré. Ils agissent en frottant sur le verre les grains minuscules de potée ou d'oxyde de cérium dont on les saupoudre.
Les outils destinés à l'usure mécanique du verre sont généralement classés en grandes catégories qu'on peut ramener à trois :
- Les meules : qui ont la forme d'une roue tournant autour de son essieu et peuvent attaquer le verre soit par leur face plane frontale soit par la jante.
- Les outils de perçage : sortes de cylindres creux tournant sur eux-mêmes en s'enfonçant dans le verre par leur base circulaire.
- Les fraises : qui englobent pratiquement tous les autres outils qui agissent le plus souvent sur des objets en verre à surface de révolution se trouvant fréquemment eux-mêmes en rotation.
Mais en fait on peut passer sensiblement de l'une à l'autre de ces catégories sans pouvoir fixer de frontières précises entre elles. Il n'y a pas de différence de principe, par exemple entre une meule utilisée pour dresser une surface plane, une fraise d'optique qui sert à réaliser des surfaces sphérique et une perceuse qui creuse un trou cylindrique dans une dalle de verre. La différence essentielle ne provient pas de l'outil (il s'agit en fait dans chaque cas d'un cylindre à parois plus ou moins épaisse attaquant le verre par sa base) mais des mouvements respectifs du verre et de l'outil l'un par rapport à l'autre (translation pour la meule, rotation pour la fraise, enfoncement la perceuse). C'est donc par simple commodité de présentation qu'on adoptera ci-après le classement en meules, perceuses et fraises. On y ajoutera une quatrième catégorie, celle des petits outils de gravure, bien que ceux-ci, malgré les différences de fabrication et de dimensions, puissent être considérés comme des meules de tout petit format.
Outils de gravure à la roue (taille à la roue)
Il n'y a pas de limite précise entre la taille et la gravure. La taille comporte plus particulièrement des travaux d'usure superficielle qui s'apparentent au biseautage des glaces et à la réalisation de sillons décoratifs d'une certaine ampleur et de faible courbure. La gravure a une action plus ponctuelle qui permet de creuser sur des objets en verre des sillons de toutes formes et de toutes dimensions, et elle peut aller jusqu'à la réalisation de véritable sculpture sur verre. Alors que la taille s'effectue sur des meules de plus grandes dimensions, la gravure exige des outils dont le disque abrasif comporte un diamètre plus petit (compris entre quelques millimètres et quelques centimètres). La meule abrasive est remplacée par un disque ou molette formé d'une petite feuille de métal (cuivre ou plomb par exemple) que le graveur découpe et façonne lui-même. Il la fixe ensuite sur l'extrémité effilée de la broche qui transmet le mouvement de rotation provoqué par le tour. Les dimensions réduites de l'outil qu'il emploie permettent au graveur de lui présenter l'objet à façonner dans toutes les positions nécessaires à la réalisation du décor souhaité et en respectant toutes les nuances et finesse du modèle proposé. Il s'agit bien entendu d'un travail artistique très délicat pour lequel le graveur assure sa stabilité et sa liberté de mouvement en s'appuyant sur des accoudoirs judicieusement disposés.
Les abrasifs naturels
- Le quartz : Jusqu'au milieu du XIXe siècle, le grès a été le seul matériau utilisé pour l'abrasion, on sait qu'il est formé de grains de quartz agglomérés par des sédiments naturels (dépôts qui se forment dans un liquide ou des substances sont en suspension) Sa dureté relativement faible (7 sur l'échelle de Mohs) et l'irrégularité de sa constitution le rendent impropre à la plupart des travaux de précision.
- L'émeri est composé de cristaux d'alumine dans une proportion variable (35 à 70 %) noyés dans une masse d'oxyde de fer et de silice. Les cristaux sont petits et un grain d'abrasif peut être composé de plusieurs cristaux. L'émeri est surtout utilisé pour la fabrication des meules de meunerie, de toiles et papiers abrasifs, il sert à des travaux de polissage.
- Le corindon naturel est une alumine cristallisée plus ou moins pure originaire d'Afrique du Sud, de Madagascar, du Canada. Sa richesse en alumine est parfois très élevée. (94 %) Sa dureté atteint 9 sur l'échelle de Mohs. Il est possible de l'agglomérer avec des liants céramiques.
- Le diamant est le plus dur des abrasifs connus (classé 10 sur l'échelle de Mohs). Il peut être aggloméré au moyen de résines, de métaux ou même d'argiles vitrifiables. L'emploi de ces meules s'est étendu dans l'industrie de verre, de la pierre, des matériaux semi conducteurs et des matières plastiques.
Les abrasifs artificiels
- Le corindon artificiel ou l'alumine : abrasif que l'on obtient en fondant la bauxite au four électrique
- Le carbure de silicium ou carborundum : préparé en soumettant au four électrique un mélange de charbon et de silice.
Façonnage par attaque chimique du verre
L'acide fluorhydrique et certains de ses composés sont les seuls produits susceptibles d'attaquer chimiquement le verre à une vitesse suffisante pour que leur action soit pratiquement utilisable. Il suffit en effet de mettre un de ces produits en contact avec le verre pour qu'il élimine les couches superficielles de l'objet en verre d'une manière qui dépend de sa composition, de son degré de concentration et de la durée de l'exposition. L'action peut être superficielle et uniforme et avoir pour but le dépolissage du verre ou au contraire, en utilisant des bains de composition différente, le repolissage des parties d'objets dépolies au cours des opérations de taille. Elle peut être sélective et graver dans la paroi de l'objet en verre des figures de toutes sortes, lettres ou dessins. Le dépolissage est une action rapide et superficielle qui élimine la peau brillante du verre (précédemment obtenue par polissage au feu ou à la pierre ponce) et ôte au verre sa transparence en lui donnant un aspect mat et finement granité. La gravure agit plus ou moins profondément sur certaines parties seulement de la surface du verre en y faisant ressortir des motifs à but décoratif ou utilitaire.
Mode opératoire
Pour procéder il faut masquer à l'aide d'un vernis inattaquable à l'acide fluorhydrique les parties de l'objet qui ne doivent pas être creusées. On peut dessiner à l'aide du vernis les lettres et dessins à protéger. Quand on plonge ensuite l'objet dans l'acide, la gravure s'effectue sur tout l'entourage du sujet verni, celui-ci apparaissant alors en relief. Si l'on désire graver en creux (cas le plus fréquent) c'est le sujet de la gravure qui doit être en contact avec l'acide alors que l'entourage est protégé par le vernis. La solution la plus simple consiste dans ce cas à revêtir tout l'objet de vernis et à dégager ensuite le sujet à graver à l'aide d'un objet métallique plus ou moins pointu. Le travail de délimitation des parties à graver peut se faire directement à la main ou par interposition d'un pochoir comportant en découpe le motif à dégager. Le dégagement de ce motif peut se faire en plusieurs étapes (comme dans le cas de la gravure au jet de sable), ce qui permet d'obtenir une gravure de profondeur variable susceptible d'améliorer l'effet décoratif recherché. Lorsque la gravure est terminée, les objets en verre sont lavés et dégagés du vernis qui les couvre, à l'aide des solvants. On peut aussi utiliser un composé fluorhydrique actif sous la forme d'une pâte ou encre à graver à l'aide de laquelle on dessine sur cet objet les lettres ou dessins à graver.