Revêtement d'avion
Le revêtement d'un avion est la surface extérieure qui recouvre une grande partie de ses ailes et de son fuselage. Les matériaux les plus couramment utilisés sont des alliages d'aluminium des séries 2000 et 7000 (contenant notamment du zinc, du magnésium ou du cuivre).
Histoire
_(12243203404).jpg.webp)
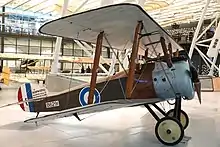
Les avions ont d'abord été construits selon une structure en treillis (truss). Le principal inconvénient de la structure en treillis est son manque de forme profilée. Dans cette méthode de construction, des longueurs de tube, appelées longerons, sont soudées en place pour former un châssis bien contreventé. Des entretoises ou haubans, soit des contreventement verticaux et horizontaux sont soudés aux longerons et donnent à la structure une forme carrée ou rectangulaire vue de l'extrémité. Des entretoises supplémentaires sont nécessaires pour résister aux contraintes qui peuvent provenir de n'importe quelle direction. Des longerons et des cloisons, ou cadres, sont ajoutés pour façonner le fuselage et soutenir le revêtement[1].
Au fur et à mesure que la technologie progressait, les concepteurs d'avions ont commencé à enfermer les éléments de treillis pour rationaliser l'avion et améliorer ses performances. Cela s'est fait d'abord avec des revêtements en tissu , qui étaient enduits, qui ont finalement cédé la place à des métaux légers tels que l'aluminium. Dans certains cas, la peau extérieure a pu supporter tout ou partie des charges de vol. La plupart des avions modernes utilisent une forme de cette structure de revêtement travaillant, connue aussi sous les noms de construction monocoque ou semi-monocoque[1].
La construction monocoque utilise une peau sollicitée (stressed skin) pour supporter presque toutes les charges, un peu comme une canette de boisson en aluminium. Bien que la construction monocoque très solide ne soit pas très tolérante à la déformation de la surface. Par exemple, une canette de boisson en aluminium supporte des forces considérables aux extrémités de la canette. mais si le côté de la boîte se déforme légèrement en supportant une charge, il s'effondre facilement[1]. Étant donné que la plupart des contraintes de torsion et de flexion sont supportées par la peau externe plutôt que par une ossature ouverte, le besoin de contreventement interne a été éliminé ou réduit, ce qui a permis d'économiser du poids et de maximiser l'espace[1]. Les premières structures monocoques étaient en contreplaqué moulé, dans les avions monocoque en bois.
Le bois
Le bois n'avait pas véritablement de rivaux au début de l'aviation. Il alliait légèreté et robustesse, qui sont les deux premiers critères de choix d'un matériau de l'aviation[1] - [2]. Le bois était aussi un choix « naturel » : sans façonnage, le bois fait aussi bien que l'acier fortement mis en forme[2]. Le bois se compose principalement de fibres creuses constituées de chaînes cellulosiques interconnectées (les trachéides) disposées plus ou moins en spirale autour des fibres dans le sens de leur dimension la plus longue. Les parois des fibres et autres cellules sont infiltrées d'un matériau amorphe appelé lignine, qui lie également les cellules ensemble si fermement que lors de la rupture, la séparation se produit généralement dans les parois des fibres plutôt que dans la liaison entre les fibres. À des fins mécaniques, le bois peut donc être considéré comme étant composé de tubes de longueur indéfinie solidement soudés ensemble plutôt que de fibres séparables de longueurs variables[3]. Ce qui vient d'être dit ici ne s'éloigne pas de la définition d'un matériau composite. La structure cellulaire du bois lui confère une microforme interne, augmentant les performances du matériau en flexion[2].
Une structure monocoque en placage de bois moulé a été fabriquée avec succès dès 1912, le Deperdussin Monocoque par Louis Béchereau et en 1916 le LWF Model V (en)[4]. Une des méthodes notables et innovantes d'utilisation de la construction monocoque a été employée par Jack Northrop. En 1918, il a conçu une nouvelle façon de construire un fuselage monocoque utilisé pour le Loughead S-1. La technique utilisait deux demi-coques en contreplaqué moulé qui étaient collées ensemble autour de cerceaux et de longerons en bois[1]. La coque du Deperdussin Monocoque pesait 22 kg et pouvait être portée à bout de bras[5], et la demi-coque du Loughead S-1 pouvait être portée par deux hommes à bout de bras [6]. La construction monocoque en bois va d'abord être utilisée pour tous les avions de course à succès compris les avions Curtis (Curtiss R3C) et le vainqueur italien de la Coupe Schneider de 1926, le Macchi M.39 ; ainsi que pour certains avions militaires réussis de Grande-Bretagne et de France[7]. Les constructions monocoques les plus abouties sont le Lockheed Vega de 1927, construit en 132 exemplaires [8], et surtout le de Havilland Mosquito de 1941.
Dans l'entre-deux-guerres, l'attention des constructeurs d'avions, se porta sur des méthodes de moulage de contreplaqué, sous pression de fluide, qui formeraient des revêtements de poids acceptable, et qui seraient sécurisés contre le froissement et le flambage auxquels les métaux étaient soumis[9]. Le contreplaqué pourrait être façonné en courbes composées, disponibles jusque là uniquement grâce à l'utilisation de métaux légers emboutis et martelés[10]. De telles peaux en contreplaqué, variables d'une partie de surface à une autre en fonction des exigences de résistance, devraient former une coque à haute efficacité tant aérodynamique que structurelle et ne nécessiteraient que des éléments de charpente légers pour la supporter. Le contreplaqué moulé sera produit selon plusieurs techniques qui sont souvent désignées spécifiquement, comme les procédés Duramold, Vidal, Aeromold (Timm Aircraft (en), le Timm N2T Tutor) ou « vacuum-bag processes». L'expression la plus inclusive serait peut-être « fluid-pressure molding »[11]. La structure du de Havilland DH.98 Mosquito est en contreplaqué fait de balsa et de bouleau, particularité qui lui permet de disposer d'un poids plus faible qu'une structure métallique, pour assurer des missions de reconnaissance et de bombardement léger. Cette construction préfigure les conceptions populaires à noyau en nid d'abeille/faces en aluminium et les composites des années ultérieures[4]. Sa conception en bois se révèle un atout lors de l'apparition des premiers radars allemands, sa structure en bois le rendant difficilement détectable, contrairement aux avions à structure métallique[10].
L'aluminium
L'aluminium fut systématiquement écarté en 1917 pour la construction du Curtiss NC, car il était difficile d'obtenir de l'aluminium dont on puisse compter sur une structure et une résistance uniformes ; pour ces raisons, son utilisation pour la construction des nervures d'aile, ainsi que pour la construction d'autres pièces de résistance fut écartée au profit de l'épicéa[12]. L'utilisation d'aluminium dans les réservoirs de carburant et d'huile du Curtiss NC-4 en 1919, a été l'une des premières applications à grande échelle de ce matériau dans l'aviation plus lourde que l'air. Chaque réservoir de carburant de 200 gallons ne pesait que 70 livres, économisant un total de 630 livres par rapport aux réservoirs en acier équivalents[13].
Au cours du XXe siècle, l'aluminium est devenu un métal essentiel dans les avions. Le bloc-cylindres du moteur qui a propulsé l'avion des frères Wright à Kitty Hawk en 1903 était une pièce coulée en un alliage d'aluminium contenant 8% de cuivre ; des pales d'hélice en aluminium sont apparues dès 1907 ; d'autres pièces similaires en aluminium étaient courantes au début de la Première Guerre mondiale[14].
En 1916, Louis Charles Breguet conçoit un bombardier de reconnaissance (le Breguet 14) qui marque les premières utilisations de l'aluminium dans la structure travaillante d'un avion. À la fin de la guerre, les Alliés et l'Allemagne utilisaient des alliages d'aluminium pour les cadres structurels des ensembles de fuselage et des ailes.
L'aluminium n'était pas toutefois exactement le matériau idéal que l'on attendait. Les ailes en bois demeurent la norme jusque dans les années 1930, il était alors notoire qu'il était difficile de produire des ailes en métal aussi légères que celles en bois. Le feu était la cause majeure d'accidents pendant la Première Guerre mondiale, pour des avions qui étaient en bois couvert de tissus. Toutefois lorsque les premiers avions tout métal se sont imposés, la première cause de destruction était le carburant embarqué, conjugué à la faible résistance qu'offrait l'aluminium à la chaleur. L'aluminium fond à 540°C, la moitié de la température de fusion de l'acier. Le flambage du métal était une autre cause de soucis. Les avions à revêtement travaillant offraient un carénage lisse et une structure efficace, mais le flambage du métal demeurait un problème. La résolution du flambage impliquait un surcout qui rendait le bois attractif. Les rivets étaient une autre source de soucis, qui étaient un obstacle aux performances aérodynamiques de l'avion. Les partisans du métal ont toujours revendiqué la durabilité comme son plus grand avantage. Le bois, dit Junkers, « est sujet au… feu et à la pourriture, et se brise lorsqu'il se casse ; il éclate et se déforme sous l'effet de l'humidité… et les joints collés se fendent ; enfin il est attaqué par les insectes ». Les métaux sont en effet souvent plus durables que le bois, bien que les deux se détériorent lorsqu'ils ne sont pas protégés. Par contre, le duralumin, le métal le plus prometteur, présentait de graves problèmes de corrosion comparables aux problèmes de durabilité du bois. L'Alclad résoudra ce problème[15].
Notes et références
- (en) Cet article est partiellement ou en totalité issu de l’article de Wikipédia en anglais intitulé « Skin (aeronautics) » (voir la liste des auteurs).
- (en) Federal Aviation Administration (FAA), Pilot's Handbook of Aeronautical Knowledge: FAA-H-8083-25B, Ravenio Books, (lire en ligne)
- (en) « Introduction to Aerospace Materials | ScienceDirect », sur www.sciencedirect.com (consulté le )
- (en) E. A. Starke et J. T. Staley, « 24 - Application of modern aluminium alloys to aircraft », dans Fundamentals of Aluminium Metallurgy, Woodhead Publishing, coll. « Woodhead Publishing Series in Metals and Surface Engineering », (ISBN 978-1-84569-654-2, lire en ligne), p. 747–783
- Alphonsus V. Pocius, David A. Dillard et Manoj Kumar Chaudhury, Adhesion science and engineering, Elsevier, (ISBN 978-0-444-51140-9, 0-444-51140-7 et 0-08-052598-9, OCLC 162129877, lire en ligne)
- http://www.pionnair-ge.com/spip1/spip.php?article18
- https://www.sfomuseum.org/exhibitions/wooden-wonders-early-lockheed-aircraft/gallery#3
- (en) « Kockheed "vega" airplane : a commercial cabin monoplane », Aircraft Circular::National Advisory comitee for aeronautics, (lire en ligne, consulté le )
- (en) United States Federal Aviation Administration, Pilot's Handbook of Aeronautical Knowledge, Aviation Supplies & Academics, Incorporated, (ISBN 978-1-56027-750-7, lire en ligne)
- Carlile P. Winslow, United States, University of Wisconsin et Forest Products Laboratory (U.S.), Forest products and defense, U.S. Dept. of Agriculture, Forest Service, Forest Products Laboratory, coll. « [Report] ;R1250FU », (lire en ligne)
- (en) Bonnier Corporation, Popular Science, Bonnier Corporation, (lire en ligne)
- (en) Bruce E. Heebink, Fluid-pressure Molding of Plywood, U.S. Department of Agriculture, Forest Service, Forest Products Laboratory, (file:///C:/Users/grode/Downloads/FPL_1624ocr.pdf [PDF])
- (en) « Design and Construction of the NC Flying Boats », sur U.S. Naval Institute, (consulté le )
- « Navy's Flying Boats », sur www.navsea.navy.mil (consulté le )
- Emily Chen, « Economic and environmental evaluation of end-of-life aerospace aluminum options using optimization methods », Bachelor of science, Massachusetts Institute of Technology, (lire en ligne, consulté le )
- Eric Schatzberg, « Ideology and Technical Choice: The Decline of the Wooden Airplane in the United States, 1920-1945 », Technology and Culture, vol. 35, no 1, , p. 34–69 (ISSN 0040-165X, DOI 10.2307/3106748, lire en ligne, consulté le )