Fabrication des feuilles et bandes d'aluminium
La fabrication des feuilles et tôles d'aluminium inclut au minimum les étapes d'élaboration du métal liquide, de coulée, de laminage, de parachèvement et de contrôle qualité. Les tôles d'aluminium, comme de nombreux autres métaux, sont utilisées tous les jours. Les applications les plus prestigieuses sont le fuselage des avions ou les tôles de carrosserie automobile, mais les feuilles d'aluminium se trouvent aussi dans des applications plus communes telles que les emballages flexibles pour l'agroalimentaire.
Élaboration de l'aluminium liquide
Des lingots, des additifs et des déchets de la production sont chargés dans un four de fusion de plusieurs dizaines de tonnes de capacité (par exemple 50 tonnes).
Une partie du métal est transférée régulièrement du four de fusion vers un four de maintien, dont la capacité est d'environ 10 à 20 tonnes. Il permet de contrôler plus précisément la température du métal qui est un paramètre important dans le processus de coulée.
Un affineur de grain est ajouté soit dans les fours sous forme de tablettes, ou de morceaux soit en continu sous forme d’un fil qui se dissout au fur et à mesure dans les canaux de coulée. L’objectif est — comme son nom l'indique — de rendre les grains qui composent l’aluminium solidifié plus fins, et ainsi d’améliorer les caractéristiques mécaniques (cf. loi de Hall-Petch).
Du chlore ou du fluor est injecté dans le bain de fusion sous forme de gaz ou de granules, afin de diminuer la concentration en alcalins (Na, Ca, Mg, Li) néfastes aux caractéristiques mécaniques de l'aluminium.
Le métal passe par une poche où l'hydrogène de l'aluminium est dégazé par injection d'un autre gaz (azote ou argon) sous forme de bulles.
Le métal traverse ensuite un système de filtration (dalle en céramique poreuse, filtre à lit de gravier), qui agit comme une passoire à thé, pour retenir des particules et laisser passer le liquide.
Jusqu’à ce qu’il soit solide (vers 660 °C), l’aluminium liquide est orange et fluide.
De l’aluminium liquide à la bande
Il existe plusieurs procédés concurrents dont les deux principaux sont la coulée semi-continue verticale (Direct Chill)[1] et la coulée continue entre cylindres (Continuous Casting). La coulée semi-continue verticale permet une gamme d'alliages plus étendue et une production plus importante. La coulée continue entre cylindres, grâce à des étapes en moins, permet des temps/coûts de production et des investissements de départ plus faibles.
Coulée semi-continue verticale
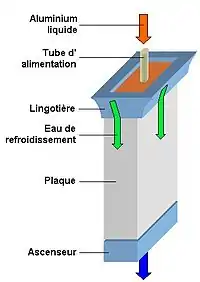
De d’aluminium liquide est versé régulièrement au niveau de la lingotière, un cadre refroidi à l'eau. Au fur et à mesure que l'aluminium se solidifie, la plaque qui se forme est descendue à l’aide du descendeur, jusqu’à ce qu'elle atteigne la longueur souhaitée.
Pour refroidir l'aluminium, de l'eau ruisselle d'abord sur la lingotière, puis continue de ruisseler sur la plaque en elle-même, d'où le terme anglais de Direct Chill.
La plaque est retirée de la fosse de coulée pour être stockée sur un parc. La coulée est dite semi-continue car la coulée s'arrête par exemple tous les 10 mètres.
Dans la sidérurgie, la coulée continue d'acier utilise aussi un cadre refroidi à l'eau. Mais comme l'intervalle de solidification de l'acier est nettement plus important que celui de l'aluminium, la plaque peut être plus longue, prendre un rayon de courbure pour être découpée en continu.
Laminage Ă chaud
La plaque est au préalable scalpée pour retirer la couche d’aspect irrégulier dû de la coulée puis chauffée entre 400 et 600 °C (d’où le terme de laminage à chaud, hot rolling en anglais). Sinon il faudrait une énergie considérable pour la laminer.
Ensuite, la plaque passe dans un laminoir réversible pour former une plaque très plate mais très longue (quelques centaines de mètres, une réduction d'épaisseur s'accompagne d'une augmentation de longueur dans les mêmes proportions), qui passe elle-même dans un laminoir à plusieurs cages pour obtenir un bon état de surface et une bande capable d’être enroulée (entre 700 µm et 5 mm d’épaisseur).
Coulée continue entre cylindres (Continuous Casting)
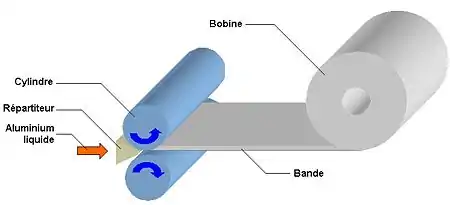
Ce procédé est aussi connu sous le nom de Twin Roll Casting ou encore ConCast. L'aluminium liquide, proche de la température de solidification, se répartit grâce à un répartiteur sur toute la largeur entre deux cylindres qui tournent en sens opposé. Au contact des cylindres refroidis à l’eau par des galeries internes, l'aluminium liquide se solidifie et forme une bande de métal de 3 à 9 millimètres d'épaisseur et de 1 à 2 mètres de large, qui est enroulée plus loin sur un mandrin. La vitesse de production est de l’ordre de 1 à 3 mètres par minute.
Lorsque la bobine atteint un certain diamètre, la bande est coupée, la bobine est retirée du mandrin, l'autre morceau de bande est engagé dans celui-ci, et une nouvelle bobine est commencée.
Ce processus est continu. Il s’arrête à la suite d'évènements qualité, de pannes ou après la casse de certaines pièces en matériaux réfractaires.
Autres procédés de coulée
- Coulée sur tambour (Single Drum Casting) ;
- Coulée sur roue (Wheel casting) ;
- Coulée entre bandes (Twin Belt Casting) ;
- Coulée entre blocs (Block Caster) ;
- Coulée continue verticale entre cylindres (Twin Drum Casting), vers le bas ou vers le haut.
Laminage à froid : réduction d'épaisseur
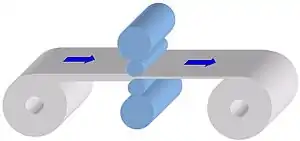
La fonderie livre au département « laminage » une bande de 500 μm à 9 mm. Le laminage à froid (cold rolling en anglais) a pour but de diminuer cette épaisseur jusqu'à l'épaisseur désirée. Pour cela, la bande est écrasée ou étirée entre deux cylindres plusieurs fois. Chaque passe permet de diviser l’épaisseur par deux. Par conservation de la matière, la longueur de la bobine est multipliée par deux. Un lubrifiant (une huile proche du kérosène ou des émulsions eau/huile toujours avec des additifs pour que le film résiste aux efforts de laminage) est nécessaire pour plusieurs raisons.
Premièrement, dans le but d'empêcher que la feuille ne soit en contact direct avec les cylindres pour éviter d'endommager la feuille (griffures…). Deuxièmement, dans le but de minimiser le coefficient de frottement afin de diminuer l'énergie nécessaire au laminage tout en évitant le patinage.
Les gros cylindres (cylindres d'appui) appuient sur les petits (cylindres de travail) et permettent de contrôler certains paramètres de planéité de la feuille et de résister aux efforts de séparation.
Durant les opérations de laminage, le grain s'allonge et le métal durcit, ce qui s'appelle l'écrouissage. Un métal trop dur devient difficilement laminable. Le métal peut être recuit (il est réchauffé entre 300 et 600 °C dans un four) après quelques passes pour l'adoucir (le rendre plus mou), et obtenir de nouveaux grains plus homogènes en taille (re-cristallisés) et moins allongés.
Lors de la dernière passe de laminage, deux feuilles sont laminées en même temps (opération de doublage) si l'épaisseur est suffisamment faible (< 80 μm). Pour cela, une deuxième bobine est disposée derrière la première et les feuilles de chacune des bobines sont insérées en même temps entre les cylindres. Il y a au moins deux avantages. Le premier est financier puisque deux feuilles sont laminées en une seule passe. Le deuxième est mécanique car deux feuilles résistent mieux à la rupture qu’une seule. C'est particulièrement utile pour les feuilles de 6 à 7 μm présentes dans les briques de jus de fruit et de lait.
Lorsque la feuille a été doublée, elle possède une face mate et une face brillante. La face mate est celle en contact avec une autre feuille d'aluminium. La face brillante correspond à la face en contact avec les cylindres du laminoir. À part cela, toute préférence pour l'une ou l'autre de ces faces n'est a priori que psychologique. L'oxygène, le CO2, la poussière, l'humidité, la chaleur, les microbes et la lumière ne passeront pas mieux à partir d'un côté ou de l'autre. L'aluminium est l'un des meilleurs matériaux contre toutes ces menaces envers les produits emballés. L'association avec un autre matériau produit un emballage résistant et très peu perméable à son environnement.
Parachèvement
L'un des points du cahier des charges concerne les dimensions. L'épaisseur a été donnée par les laminoirs. Le parachèvement a entre autres objectifs celui de mettre les bobines aux bonnes dimensions (largeur et diamètre) à l'aide de lames, cisailles ou autres systèmes de découpe.
Lors du parachèvement, les deux feuilles qui ont éventuellement été laminées ensemble (doublage) sont aussi séparées.
Enfin, les bobines subissent un recuit final dans un four. Le recuit sert à dégraisser les bobines et à obtenir les propriétés mécaniques désirées (par recristallisation ou durcissement secondaire). La feuille doit souvent être dégraissée pour retirer le lubrifiant à sa surface car elle subit souvent une nouvelle transformation : laquage, vernissage, impression, anodisation, coextrusion, contre-collage, colaminage, brossage, dégraissage chimique, texturation, vieillissement…
Contrôle qualité
L'objectif du contrôle qualité est de vérifier la conformité du produit au cahier des charges. Les points ci-dessous sont vérifiés selon le type de produit :
- Dimensions : largeur, épaisseur, etc.
- Propriétés mécaniques : essai de traction, essai de fatigue, essai de corrosion, etc.
- État de surface : lignes, tâches, picots, perforations, oxydation, etc.
- Composition chimique : Si, Mg, Zn, etc.
- Qualité du bobinage : télescopies, défauts de tension, voilement, planéité, etc.
- Dégraissage : mouillabilité, diamètre de goutte, quantité de carbone, etc.
- Qualité des traitements : grammage de pré-lubrification, uniformité, etc.
Emballage et expédition
Les produits (bobines ou plaques) sont emballés — par exemple mises sur des palettes ou dans des caisses — et sont envoyées aux clients dans le monde entier, par camion, bateau et parfois par avion.
Applications
- Agroalimentaire : papier aluminium, briques de lait et jus de fruits, barquettes de plats préparés, opercules (fromage blanc et yaourts), cols de bouteille (bière et champagne), paquets de biscotte, emballage chocolat et confiseries, emballages flexibles, emballage beurre et fromage ;
- Pharmacie et cosmétique : feuilles pour blisters, sachets comprimés effervescents, emballages flexibles ;
- Transport : fuselage des avions, radiateurs et carrosserie des voitures, coques des navires rapides, carénage des trains, isolation thermique ;
- Bâtiment : gouttières et descentes d'eaux pluviales, éléments de zinguerie, décoration intérieure et extérieure, panneaux isolation ;
- Boîtes boisson ;
- Aérosols ;
- Lithographique ;
- Autres : ailettes échangeurs de chaleur, tuyaux spiralés, gaines, blindage de câbles, tuyaux chauffage par le sol, scotch aluminium, panneaux de signalisation, poêles, culots d'ampoule.
Quelques fabricants de feuilles et bandes d'aluminium
Novelis, Alcan, Norsk Hydro, Alcoa, Comital, Teich, Carcano, Corus, VAW et Pechiney avant leur rachat.
Notes et références
- Constellium France, « Fascicule de brevet européen : Procédé de coulée semi-continue verticale multi-alliages (no 12748724.7) » [PDF], sur patents.google.com, (consulté le ), p. 1 / 17.
Voir aussi
Bibliographie
- Fonderies d'aluminium. Guide pratique de prévention 2. Analyse et prévention des risques liés aux machines de coulée. Coulée semi-continue verticale., Format PDF - 801 ko, Note documentaire INRS, Référence ND 1836, 1991, 17 pages.
- (en) Strip casting technology… a key to product quality. Menet, Basson, Maiwald, Cayol, Bosch, International Melt Quality Workshop, 25-.
- (en) Continuous casting of aluminium, Kammer, Talat lecture 3210, p. 27.
- Communiqué de presse sur l'exposition « L'âge de l'aluminium » présentée du au à la Cité des Sciences et de l'Industrie.
Liens externes
- (en) [PDF] Aluminium Rolling, Mill Technology (Achenbach).
- Processus de production de l'aluminium.
- Comment sont produites les cannettes.
- (en) European Aluminium Foil Association.
- (en) European Aluminium Association.
- (en) Aluminium Association.
- (en) Site de Novelis.
- (en) Site d'Alcoa.
- (en) Site de Alcan.