De Havilland Gyron
Le De Havilland PS.23 ou PS.52 Gyron, initialement connu sous la désignation Halford H-4, fut le dernier turboréacteur conçu par Frank Halford quand il travaillait pour De Havilland. Conçu pour surpasser tout ce qui pouvait alors exister ou être en construction, le Gyron fut le moteur le plus puissant de son époque, produisant une poussée de 89 kN à sec et 120 kN avec la postcombustion allumée (que les Britanniques désignent plutôt « réchauffe »). Ce moteur était toutefois beaucoup trop gros pour pouvoir être réellement utilisé à l'intérieur d'un avion, et il ne fut jamais produit en série. Il fut cependant conçu plus tard un modèle réduit de ce moteur, le Gyron Junior, qui ne représentait que 45 % du moteur original, et qui connût un succès bien plus important[1].
De Havilland Gyron (caract. Gyron DGy.1) | |
![]() Un Gyron au de Havilland Aircraft Heritage Centre. | |
Constructeur | ![]() |
---|---|
Premier vol | |
Utilisation | Hawker P.1121 (jamais construit) |
Caractéristiques | |
Type | Turboréacteur monocorps avec postcombustion |
Longueur | 3 950 mm |
Diamètre | 1 400 mm |
Masse | 1 940 kg |
Composants | |
Compresseur | Axial à 7 étages avec stators à géométrie variable |
Chambre de combustion | Annulaire regroupant 17 brûleurs |
Turbine | Axiale à 2 étages |
Performances | |
Poussée maximale à sec | 66,72 kN |
Poussée maximale avec PC | 88,96 kN |
Taux de compression | 5,6 |
Débit d'air | 129,27 kg/s |
Conception et développement
Le Gyron fut la première conception à flux axial d'Halford. Il s'agissait alors d'un total renouveau, comparé aux anciens moteurs ayant tous utilisé des concepts à flux centrifuge basés sur ceux de Frank Whittle, tels les Goblin (H-1) et Ghost (H-2). Destiné à les remplacer, le Gyron fut également l'un des tout-premiers moteurs à avoir été directement conçus spécifiquement pour le vol supersonique.
Initiative du programme et contraintes de conception
La décision qui initia la conception du Gyron fut prise en 1950[2], période à laquelle les ingénieurs entreprirent une série de travaux intensifs et d'expérimentations, afin d'explorer et de tenter de comprendre le domaine du vol supersonique, en particulier ses conséquences sur la conception des turboréacteurs, leurs écoulements aérodynamiques internes, l'évolution des contraintes thermiques, ainsi que les influences des hautes vitesses sur le comportement de la combustion à l'intérieur des moteurs. Cette phase d'expérimentations, qui fut loin d'être facile, fut associée à de très nombreux essais au sol et en vol. L'année suivante le directeur de la compagnie Frank Halford prît la décision de se lancer dans la conception d'un moteur à très forte puissance, opérant dans le domaine Mach 2 à Mach 3, qui devrait être développé sur les fonds propres de la compagnie, le projet n'étant lié à aucune réelle demande de la part du gouvernement ou d'un constructeur d'avions externe à De Havilland. Ce fut un pari plutôt risqué, car cette expérience allait sérieusement piocher dans les ressources internes à la compagnie, et pour un projet qui n'allait finalement concerner que d'hypothétiques appareils sortis entre cinq et quinze ans plus tard[2]. Il fallait donc, pour les ingénieurs et leurs dirigeants, mettre idéalement à profit tous les résultats issus des expériences et des longues heures de travail passées sur les bancs d'essais, afin de ne pas mettre inutilement l'avenir de l'entreprise dans une position difficile.
Il fut déterminé qu'en raison des hautes vitesses visées, le dessin de l'entrée d'air du moteur serait d'une importance capitale, car il avait dès lors un rôle très important à jouer dans le fonctionnement de l'ensemble. L'air arrivant dans l'entrée d'air avait en effet un très haut potentiel d'énergie cinétique, qu'il devenait alors intéressant d'exploiter via un dessin d'entrée d'air bien pensé. Cette dernière pouvait en effet convertir ce fort potentiel d'énergie cinétique en une pression élevée en amont du compresseur, ce qui permettait à ce dernier de n'avoir qu'une faible compression à effectuer pour obtenir le taux de compression nécessaire au fonctionnement du moteur[2]. Il devint donc évident que cet élément devait être conçu pour amener l'air d'admission avec la plus grande efficacité. Il fut également déterminé que si de hautes vitesses devaient être atteintes, un flux de gaz plus rapide, et donc une poussée plus forte, devait être produit, ce qui devenait possible sans pour autant diminuer de manière exagérée l'efficacité de l'avion ainsi équipé. De plus une amélioration en poussée spécifique et en consommation spécifique pouvait être obtenue en augmentant la température des gaz en entrée de la turbine.
Le taux de compression bien plus important d'un moteur supersonique implique inévitablement un taux d'expansion plus important dans son système d'échappement. Comme ce ratio est virtuellement constant, le taux d'expansion dans la tuyère propulsive augmente en même-temps que la vitesse. Si ce taux d'expansion doit être utilisé à son efficacité maximale, une tuyère convergente puis divergente capable d'effectuer une détente supersonique est nécessaire. Afin de cerner les caractéristiques exactes de ces effets, des courbes de poussée spécifique et de consommation spécifique, en fonction des taux de compression et des températures de turbines, furent produites pour une large plage de conditions de vol. Ces courbes démontrèrent que si une très haute température pouvait être appliquée à la turbine (dans un futur proche), un taux de compression bien particulier (entre 5 et 6 : 1) permettait d'obtenir la meilleure efficacité pour le vol supersonique dans la stratosphère[2].
Premiers essais
La conception du H.4 (quatrième moteur de Halford chez De Havilland) démarra fin 1951. Rapidement redésigné Gyron, il était un moteur monocorps simple et léger conçu pour produire une poussée aux environs des 80 kN, ce qui était très largement au-dessus de ce que pouvaient produire les autres moteurs connus de l'époque. Il était constitué d'un compresseur axial à sept étages et d'une turbine à deux étages reliés par un arbre central de fort diamètre, l'ensemble mobile étant maintenu dans le moteur par seulement deux roulements[2]. La chambre de combustion était de type annulaire et disposait d'injecteurs de carburant en tête. En marge de la fabrication des pièces pour ce moteur, certaines pièces principales additionnelles furent fabriquées pour être testées sur des bancs pendant les quelques mois précédant la mise en route du moteur fini. La plus importante fut certainement un compresseur, construit pour des tests individuels à C. A. Parsons Ltd. (en), ainsi qu'une unité de tests anciennement utilisée pour le Ghost, qui fut modifiée pour supporter les dimensions et la poussée plus importantes du futur Gyron[2]. Ce fut sur cette plateforme d'essais que fut démarré pour la première fois le Gyron DGy.1, le . Exceptés quelques petits réglages mineurs sur les ailettes de stator d'entrée, les caractéristiques de performances visées furent rapidement atteintes, le moteur produisant des poussées très élevées seulement quelques semaines après sa première mise en route. En avril de la même année, une fois les capacités du moteur établies, l'entreprise reçut un contrat de développement et un appui financier de la part du Ministry of Supply (en) britannique.
Essais poussés et validation opérationnelle
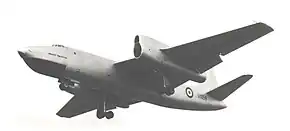
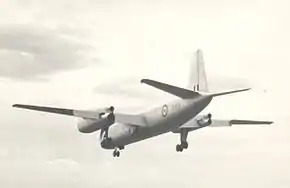
Pendant la première année de développement, un Gyron doté d'un système de combustion et de pales de turbines modifiés parvint à effectuer au mois de mai un test de 25 heures à 57,83 kN, et au mois d'octobre, plus de 150 heures de fonctionnement avaient été réalisées, dont une partie pour la définition de la poussée réelle du moteur. En , un test de 25 heures fut effectué à 60,05 kN de poussée, qui fut suivi par d'autres séries de tests pendant lesquelles les températures et les régimes maximals du moteur furent progressivement relevés. Cela permit d'accomplir une passe d'essais à 73,39 kN de poussée, suivie par une autre série d'essais de plus de 100 heures à 79,18 kN de poussée[2]. Puis en septembre, devant les très bons résultats rapportés par ce moteur, et au vu de son état général très satisfaisant, plusieurs nouvelles séries de tests furent menées à 88,96 kN de poussée (20 000 lbf). Cette performance impressionnante, qui fut déclarée comme étant la caractéristique définitive du DGy.2, plaça le Gyron bien en avance sur tous les moteurs existants ou en cours de développement de cette époque[2].
Les tests de développement du Gyron pour le programme d'essais en vol à venir furent lancés en , menant rapidement à un autre essai réussi de 25 heures de fonctionnement à 67,61 kN en , afin de valider le moteur avant de l'installer dans son avion d'essais. Le mois d'avril suivant, un Gyron « bon pour le vol » fut livré à la compagnie Short & Harland Ltd. à Belfast, en Irlande du Nord, qui modifia spécifiquement l'un de ses bombardiers quadrimoteurs Sperrin (en) (un concept de bombardier qui devint finalement un avion d'expérimentations) pour en faire un banc d'essais volants. Le moteur effectua son premier vol en juillet, installé dans la nacelle basse de l'aile gauche de l'avion, à la place d'un des Rolls-Royce Avon d'origine. Rapidement, l'avion fut expédié vers Hatfield et les essais en vol poussés du Gyron purent commencer. À la fin de l'année, l'avion fut renvoyé à Belfast pour qu'un autre Gyron soit également installé dans la nacelle droite de l'appareil, ce qui mènera à de légers problèmes de contrôle de l'avion vers les 50 000 pieds d'altitude, mais sans gravité. En avril de la dernière année, le Gyron avait accompli un vol de validation opérationnelle à 80,07 kN de poussée[2]. Pendant toute la période d'essais en vol, le moteur avait accompli ses tests à une cadence soutenue et, après une ultime test de répétition générale en , un run officiel de 150 heures à 66,72 kN du DGy.1 fut accompli en août de cette même année. Le constructeur put alors affirmer sans aucune hésitation que ce résultat était le plus haut niveau de poussée atteint par un turboréacteur dans tout le monde occidental. D'autres essais de développement furent ajoutés, permettant d'apporter des modifications mineures aux turbines et à la chambre de combustion, ce qui permit au moteur d'encore améliorer la poussée produite.
Tous ces travaux ont été rendus possibles en particulier grâce à la mise en place, dès 1954, d'un nouveau banc d'essais aux dimensions généreuses, adaptées à ce moteur et permettant une exploitation et une analyse très fine des résultats obtenus pendant les essais. Ce banc, installé à Hatfield, portait le numéro 25 et était totalement isolé phoniquement, ce qui permettait aux ingénieurs d'effectuer des essais continus de 24 heures par jour, un atout indéniable pour la réalisation de tests de fonctionnement de 150 heures sans interruption. Une autre étape imporatnte dans le développement du Gyron intervint en , lorsqu'un moteur de 66,72 kN de poussée fut poussé à 88,96 kN grâce à l'ajout d'un dispositif de postcombustion. Cet ajout important fut ensuite testé avec une tuyère à section variable de type convergente/divergente, et la poussée augmenta progressivement encore, jusqu'à atteindre 111,21 kN sur le DGy.2[2]. La section de postcombustion fut développée en deux versions, l'une courte, l'autre plus longue, pour des applications aéronautiques spécifiques.
Caractéristiques
Bien qu'étant d'une puissance élevée, le Gyron respectait en fait la philosophie bien établie de la société De Havilland, qui combinait une haute efficacité mais un concept simple et fiable. Ces caractéristiques avaient déjà été mises en place depuis la conception des anciens moteurs Ghost et Goblin[2].
Côté mécanique, le moteur est doté d'une entrée d'air frontale circulaire, d'un compresseur axial de diamètre extérieur constant utilisant une combinaison de rotors et de stators, un arbre de fort diamètre reliant ce compresseur à sa turbine, d'un collecteur amenant l'air comprimé à la chambre de combustion annulaire et contenant une extension interne pour maintenir le roulement de la turbine, et un système de rayons à l'intérieur ailettes des premiers étages de turbine pour apporter un soutien radial au roulement arrière. Les points de levage du moteur sont situés au-dessus de l'entrée d'air et sur le carénage de l'anneau de turbine avant[2].
L'emploi d'un taux de compression relativement modéré, et donc impliquant un nombre réduit d'étages de compresseur, ainsi que la conception annulaire de la chambre de combustion, permirent de réduire la longueur globale du moteur, ainsi que l'utilisation d'une architecture légère à seulement deux roulements principaux. La réalisation d'un assemblage suffisamment rigide entre le rotor du compresseur et l'arbre de transmission est obtenue en utilisant de fins disques en acier pour maintenir les ailettes des compresseurs et leurs tambours plaqués contre les disques adjacents. La charge centrifuge appliquée aux ailettes des rotors est également employée pour augmenter la résistance axiale des disques en cours de fonctionnement[2]. Le compresseur est attaché à l'arbre de transmission sur sa face arrière. L'arbre de transmission, à proprement parler est constitué d'une espèce de trompette à parois fines, dont le diamètre se réduit vers l'arrière, reliée en sa partie arrière à un petit arbre cylindrique, ce dernier étant relié à la turbine à deux étages. La rigidité de l'assemblage rotatif est due en grande partie à la forme évasée de l'arbre de transmission[2].
Les effets gyroscopiques produits au niveau des deux roulements sont transmis à la structure de l'avion via la structure du moteur et ses points d'arrimage. Les charges subies par le roulement avant sont transmises par l'intermédiaire des supports aérodynamiques radiaux disposés dans l'entrée d'air, alors que les charges du roulement arrière (qui est situé au niveau du rotor du premier étage de turbine) sont contenues à l'intérieur de l'anneau d'étanchéité intérieur de turbine par un ensemble de diaphragmes coniques. Ces charges sont ensuite transmises à l'anneau étanche extérieur par des entretoises radiales de faible section installées à l'intérieur de chacune des ailettes de stator de la turbine, qui véhiculent en même temps l'air de refroidissement de ces dernières. À la fabrication, ces entretoises étaient précontraintes d'une façon assez similaire à celle employée pour les rayons d'une roue de vélo[2].
Les charges internes entre les points d'attache avant et arrière du moteur sont supportées par le carénage du compresseur et l'entrée d'air avant. Afin de disposer d'un point d'attache arrière capable de supporter à la fois la dilatation thermique axiale et radiale du moteur, le carénage de la tuyère est doté d'un support en V qui s'aligne automatiquement avec les roulements internes. Ce support en V est, lui, relié directement à la structure de l'avion porteur[2].
Entrée d'air
L'entrée d'air du moteur est constituée d'un double carénage annulaire en alliage magnésium/zirconium ZRE-1, maintenant en place le carénage du roulement principal avant du moteur, via sept supports aérodynamiques, aussi désignés entretoises. Un carénage à une seule paroi et de conception légère aurait probablement subi des déformations lorsque le moteur aurait évolué à hauts régimes pendant des manœuvres violentes, ce qui amena les ingénieurs à concevoir cette structure à double paroi, très légère mais très solide. Considérée comme une prouesse dans le domaine de la fonderie, elle a été fabriquée par la société Sterling Metals, Ltd. Les problèmes de démoulage étaient atténués par le soudage de plaques sur les cavités d'accès après que le sable ait été enlevé et le moulage nettoyé. Une utilisation intéressante avait été faite des espaces vides entre les deux parois, en les divisant transversalement en trois compartiments séparés. L'un d'entre-eux, avec une capacité en liquide de trois gallons, servait à contenir l'huile moteur, tandis-que les deux autres amenaient de l'air chaud prélevé au niveau du compresseur vers l'avant du moteur, ou il dégivrait les ailettes de stator du premier étage de compresseur ainsi que les entretoises aérodynamiques qui soutenaient l'arbre de transmission du moteur. Ce flux d'air était aussi envoyé dans l'ogive couvrant le roulement avant, qui abritait aussi des engrenages, des arbres et des renvois d'angle entraînant des accessoires installés à l'intérieur de ce carénage[2].
À l'arrière et à l'intérieur du carénage de l'entrée d'air se trouvaient des ailettes de stator à géométrie variable du compresseur. Initialement pleines et forgées en acier S.96, elles furent ensuite prévues pour être creuses, afin de recevoir l'air chaud du système de dégivrage précédemment cité. Chacune de ces ailettes était dotée à son extrémité interne d'une petite extension et installée dans un roulement sphérique, l'ensemble agissant comme un petit levier. Les leviers de toutes les ailettes étaient reliés à un unique anneau de commande entourant tout l'extérieur de l'arrière du carénage intérieur de l'entrée d'air. Le premier système automatique contrôlant cet anneau de commande était constitué de deux vérins hydrauliques peu accessibles et installés de manière tangentielle avec l'anneau. Le système développé plus tard était lui composé d'une biellette actionnée hydrauliquement passant au travers de l'une des entretoises aérodynamiques basses de l'entrée d'air, qui modifiait l'angle des ailettes en actionnant un engrenage directement relié à l'anneau de commande. Le mouvement de la biellette de commande, et donc des ailettes, était contrôlé de manière automatique par un système hydraulique employant du carburant sous pression, qui était lui-même dépendant d'un paramètre de fonctionnement moteur présélectionné[2].
Compresseur
À l'arrière du carénage de l'entrée d'air de trouvait le carénage du compresseur, divisé transversalement et longitudinalement en deux paires de carénages plus petits. La paire avant était usinée dans de l'alliage d'aluminium R.R.58, tandis-que la paire arrière, soumise à de plus hautes températures dues à la compression, était usinée dans des moulages réalisés en acier de soudage à haute résistance. Toutes les ailettes du compresseur étaient usinées dans des barres forgées en acier inoxydable S.62, qui était apprécié pour sa bonne capacité à amortir les vibrations (parmi d'autres qualités évidentes comme la résistance à la chaleur). Les ailettes de stator étaient maintenues dans des logements en forme de queue d'aronde usinés directement dans le carénage de compresseur. À leur extrémité la plus fine, les ailettes de stator étaient totalement enveloppées dans des anneaux contenant des joints en labyrinthe sur leur face interne. Ils étaient usinés avec une tolérance spécifique laissant un espace bien précis entre eux et l'arbre de compresseur[2].
Le rotor du compresseur était de construction très simple. Excepté le premier et le septième étages, les autres étaient constitués de disques fins en alliage d'acier S.97, usinés d'une pièce avec leur portion centrale, dont la face arrière était directement reliée au disque suivant par une légère dépression conique usinée en son centre. Intégrant un petit arbre de transmission sur sa face avant, le prelier étage (à l'avant) était également chargé de maintenir l'ensemble en position correcte pendant le fonctionnement. Le septième étage était relié à un huitième tambour central, contenant un joint d'étanchéité pur éviter les fuites d'air sous pression provenant du compresseur. Ce dernier tambour était attaché à l'arbre principal relié à la turbine. Des espaceurs en aluminium étaient insérés au milieu de ce huitième tambour pour atténuer les vibrations latérales. Un gros roulement à trois pistes était installé dans un carénage à l'arrière des entretoises de l'entrée d'air, supportant les efforts longitudinaux et transversaux de l'ensemble rotatif. Les ailettes des rotors étaient usinées avec leurs racines et étaient maintenues fermement contre les disques de rotors par une simple goupille, afin de limiter les effets vibratoires et les déformations à hautes vitesses. D'une conception simple, cette technologie se révéla pourtant très solide.
Afin de prévenir la perte de pression d'air provenant du septième étage entre le carénage intérieur de la chambre de combustion et l'arbre de transmission de la turbine, le huitième disque de compresseur était doté d'un joint labyrinthe. En raison des vitesses élevées qu'il avait à supporter, impliquant le besoin d'un haut pouvoir d'isolement, il était renforcé par un anneau en carbone à son emplacement de fixation. Cet anneau était inséré en force dans un anneau en acier qui le maintenait précontraint, le joint étant ensuite plaqué contre l'arbre par la pression une fois le moteur en fonctionnement[2].
Chambre de combustion
Le canal d'entrée avant, disposé entre le compresseur et la zone où se produit la combustion, formait l'épine dorsale du moteur. En raison des températures que cette pièce devait subir, elle était formée de deux tambours en acier hautement résistant à double épaisseur, qui formaient le diffuseur et la sortie du compresseur. 17 supports aérodynamiques étaient intercalés entre le tambour interne et celui externe, procurant à la fois une résistance élevée aux contraintes subies en fonctionnement, mais servant également de support à la partie avant de l'assemblage de tubes à flamme. Boulonnée à l'arrière du tambour intérieur se situait une autre paire de tambours en acier résistant à la chaleur. Le tambour extérieur n'avait aucun rôle structurel et constituait l'une des parois internes de la chambre de combustion, tandis que le tambour intérieur était légèrement conique et s'étirait jusqu'au début des étages de turbine. Il était suivi d'un autre tambour conique qui soutenait le support de roulement principal arrière. Une grosse bride à l'extrémité avant de ce second cône fournissait des goujons de fixation pour la partie intérieure du collecteur d'entrée de turbine et pour un déflecteur conique apportant de l'air de refroidissement aux disques de la turbine[2].
La chambre de combustion du Gyron fut la partie du moteur la plus difficile à concevoir. Sous sa forme originale elle était dotée d'un museau annulaire, d'une plaque génératrice de turbulences et de tubes à flammes interne et externe, chacun en Nimonic 75. Le volume d'air externe, en acier résistant, jouait aussi un rôle structurel en supportant les contraintes du fonctionnement. L'assemblage utilisait en tout 18 brûleurs Lucas Duplex 3, qui diffusaient les jets de carburant vers l'avant du moteur (à contre-courant). Des goulottes inversant le sens du flux étaient installées à mi-chemin des tubes à flamme pour injecter de l'air vers l'avant dans la zone de combustion principale entre les injecteurs de carburant. Le maintien et l'ancrage de la flamme de combustion à l'endroit idéal dans la chambre était donc tributaire de cette recirculation d'air et de l'efficacité des plaques à turbulences. Une série de minces bandes ondulées étaient disposées vers l'arrière du tube à flamme pour que de l'air de dilution vienne refroidir l'intégralité de la face intérieur des tubes à flammes[2].
L'incroyable appétit en air du moteur empêchait aux ingénieurs de fournir un flux d'air suffisant pour tester l'efficacité de la conception de la chambre de combustion sous tous ses aspects. Cependant, les ingénieurs parvinrent quand-même à effectuer un test sur un banc à pression atmosphérique en même-temps que le Gyron fut lancé pour la première fois. En parallèle, de nombreux tests avaient été menés au laboratoire d'Halford. Tous les résultats issus de ces tests montrèrent que le moteur affichait des valeurs de température d'entrée de turbine non convenables, et il fallut modifier la conception de la chambre de combustion. Plusieurs formes nouvelles furent testées, parmi lesquelles une configuration à onze brûleurs internes et externes assez compliquée, censée améliorer et rendre plus uniforme le flux d'air vers les jets de carburant. Conséquence de ces travaux, d'autres modifications furent appliquées aux trous amenant l'air de dilution. Testées sur une configuration à 18 brûleurs, ces modifications démontrèrent une amélioration notable de la température des gaz en entrée de la turbine, et furent par ailleurs grandement responsables des 20 000 lbf (plus de 9 000 kgp) de poussée atteints par le Gyron DGy.2. Le choix final se porta sur un modèle de chambre à 17 brûleurs, afin de réduire la probabilité de résonance des pales de turbine sous certaines conditions[2].
Des tests poussés à forte puissance qui suivirent montrèrent qu'une ultime évolution était nécessaire concernant la température atteinte à l'entrée de la turbine, afin de prévenir une dilatation (et un allongement) trop important des pales du premier étage de la turbine. Il fut déterminé que des changements étaient nécessaires dans les conditions de combustion de la zone primaire de la chambre. Ils furent effectués par l'ajout de générateurs de tourbillons en forme de canaux, qui divisaient le flux d'air provenant du compresseur en deux parties, avant de l'amener sur les plaques déjà prévues d'origine. Cette amélioration permettait à la chambre de combustion de disposer d'un flux d'air plus direct et uniforme.
Arbre principal et turbine
Joignant le rotor de compresseur à la turbine, l'arbre de transmission forgé en acier S.97 disposait de parois exceptionnellement fines sur toute sa longueur. Usiné en forme de trompette, sa forme lui apportait une très grande solidité et lui permettait de résister aux effets de la force centrifuge à hauts régimes de fonctionnement. Il était soutenu sur sa partie arrière par le roulement principal arrière (à une seule piste).
Afin de maintenir les deux disques de turbine concentriques entre eux et avec l'arbre principal, il était prévu que le disque du premier étage soit fixé sur l'arbre au moyen d'un accouplement Hirth, tandis que le disque du deuxième étage était relié au premier au moyen d'un tambour inter-étages équipé de chevilles. La partie avant de l'accouplement Hirth reposait sur des cannelures à l'arrière de l'arbre principal, et la moitié arrière de l'accouplement était usinée directement sur la face avant du premier disque. L'étirement radial du disque était autorisé par la disposition radiale des dents de l'accouplement, et, afin d'assurer un contact de adéquat soit effectué sur les dents du couplage dans toutes les conditions de vol, un grand anneau-écrou venait en butée contre la face arrière du premier disque de turbine[2].
Le disque du premier étage était issu d'une forge en alliage Firth-Vickers Rex 448, et le disque de deuxième étage, qui était également boulonné en son centre à l'arrière de l'arbre principal, était issu d'une forge en alliage William Jessops H.40. Ces deux matériaux sont des aciers ferritiques résistant à la chaleur. Les aubes de turbine étaient usinées à partir de pièces forgées, en alliage Nimonic 100 pour le premier étage et Nimonic 90 pour le deuxième, et étaient retenus dans les disques par des raccords-racines en sapin à cinq dentelures, dont l'apex était serré par des rivets en Nimonic 75 pour empêcher l'apparition de mouvements longitudinaux en cours de fonctionnement. Les aubes du premier étage de turbine étaient formées à partir d'une feuille en Nimonic 80A, dont les deux replis étaient soudés le long du bord de fuite. Les tirants tenant les racines des ailettes du stator passaient à travers un joint assurant également l'étanchéité de toute la partie arrière du moteur, ainsi que la rigidité de sa structure. Pour faire face à l'expansion radiale des ailettes, celles-ci se déplaçaient à l'intérieur de petites dépressions usinées dans les carénages annulaires intérieurs et extérieurs du moteur. L'anneau intérieur comprenait aussi des fentes chargées de transmettre l'air prélevé au compresseur vers les ailettes afin de les refroidir. Les anneaux entourant les ailettes étaient également refroidis par des flux d'air secondaires rejoignant le flux de gaz chauds après utilisation. Les ailettes du deuxième étage de turbine étaient des éléments usinés d'une seule pièce en Nimonic 80A et ne disposaient pas de canaux internes de refroidissement. Elles étaient également montées de manière radiale, mais avec un léger angle de déport, afin de rendre le moteur plus rigide lorsqu'elles étaient soumises à un échauffement et s'allongeaient[2].
Circuit carburant
Le système d'alimentation en carburant fut fourni dans son intégralité par la société Joseph Lucas (Gas Turbine Equipment), Ltd., qui avait déjà beaucoup participé à concevoir la chambre de combustion annulaire et le système de vaporisation du carburant qui l'occupait. Cette association entre le système de vaporisation et la large chambre annulaire était d'ailleurs une première dans l'industrie britannique. Le système d'alimentation comprenait de nombreuses pompes à débit variable, leurs filtres, une unité de contrôle proportionnelle et un distributeur de flux. L'unité de contrôle proportionnelle était composée d'une valve de contrôle du régime faisant également office de coupe-circuit, et de valves spécialisées, dont celle assurant un ralenti à vitesse constante au moteur. Un système séparé contenait le capteur d'altitude, qui permettait d'ajuster le débit de carburant en fonction de la pression atmosphérique extérieure autour de l'avion[2].
Lubrification
Un système à carter sec apportait de l'huile sous pression au roulement principal avant, ainsi qu'aux divers éléments mobiles (arbres et engrenages) contenus dans le cône d'entrée d'air et sur le carénage extérieur de celle-ci. Une fois utilisée, cette huile redescendait dans le carter via l'entretoise aérodynamique la plus basse à l'intérieur de l'entrée d'air. Des joints assemblés sous pression maintenaient l'huile dans les roulements en évitant les fuites indésirables. Elle était ensuite refroidie grâce à des échangeurs dans lesquels passait du carburant frais arrivant vers la chambre de combustion du moteur[2].
Système de démarrage
Le moteur était mis en route soit par un démarreur électrique Rotax de 45 ch alimenté en 110 volts continu, soit par un turbodémarreur fabriqué par De Havilland et fonctionnant au peroxyde d'hydrogène. Ces deux systèmes démarraient normalement le moteur en respectivement 30 et 10 secondes. Le démarreur électrique était relié au moteur par une boîte d'engrenages réducteurs via un petit arbre provenant de l'avant du rotor de compresseur[2].
Carrière opérationnelle
Le Gyron fut choisi pour plusieurs projets, en particulier l'avion d'attaque supersonique Hawker P.1121 (parfois désigné « Hurricane »), qui était censé devenir le remplaçant du Hawker Hunter. Ce projet fut cependant annulé. Un autre concept potentiellement basé sur le Gyron était l'intercepteur issu du Operational Requirement F.155 (en), qui utilisait en option le Rolls-Royce RB.106, mais qui fut lui-aussi abandonné en 1957. Le soutien financier du gouvernement britannique pour le Gyron fut lui-même supprimé en , après un investissement de 3,4 millions de Livres sterling[2] - [3].
Exemplaires exposés
Un exemplaire du Gyron est détenu par le musée de la Science de Londres, et un autre est exposé au public au de Havilland Aircraft Heritage Centre (en), St Albans.
Notes et références
- (en) Gunston 1989, p. 32.
- (en) « Gyron », Flight International, Flight Global/Archives, vol. 72, no 2532, , p. 163 à 168 (lire en ligne [PDF]).
- (en) Neil Harrison, « Cancelled projects: the list up-dated », Flight International magazine, vol. 92, no 3049, , p. 262 (lire en ligne [PDF]).
Voir aussi
Articles connexes
Bibliographie
- (en) John W.R. Taylor, Jane's all the World's aircraft : The annual record of aviation development and progress, London (UK), Jane's, , 62e éd. (ISBN 978-0-354-00094-9)
- (en) Bill Gunston, World encyclopedia of aero engines, Wellingborough New York, N.Y, P. Stephens Distributed by Sterling Pub. Co, , 192 p. (ISBN 978-1-85260-163-8, OCLC 21117189, présentation en ligne)