Méthode bergamasque
La méthode bergamasque[note 1] est un procédé historique d'affinage en trois étapes, dans un même foyer, de la fonte brute en acier naturel.
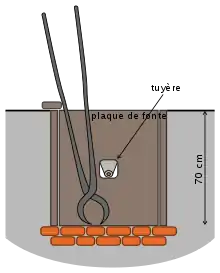
Comme son nom l'indique, elle a été mise au point en Lombardie, probablement au cours du XVIe siècle, à la fin duquel elle se diffuse dans l'ensemble des Alpes. Elle est abandonnée au cours de la première moitié du XIXe siècle, remplacée par des méthodes plus économes en combustible.
Éléments lexicaux
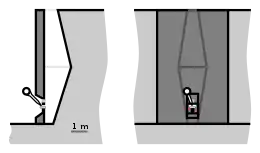
La méthode d'affinage bergamasque s'inscrit dans l'espace technique lombard, pionnier dans les techniques de production d'acier à partir de fonte[note 2]. Ainsi, le qualificatif « bergamasque » s'aplique à un ensemble de procédés et d'outils mis au point dans le nord de l'Italie, et utilisé dans les Alpes. En 1844, Émile Gueymard écrit ainsi que :
« Les pays d'Allevard et d'Articol, placées dans le voisinage de la Savoie et du Piémont, ont été pendant des siècles sous l’influence des procédés italiens ou bergamasques.
Pendant longtemps il y a eu uniformité dans toutes les usines de l'Italie, du Piémont, de la Savoie et du Dauphiné. Même forme au dehors, même coupe en dedans, même machine soufflante, mêmes chargements en minerais et en charbons, mêmes outils[G 1]… »
— Émile Gueymard, Statistique minéralogique, géologique, métallurgique et minéralurgique du Département de l'Isère
Les hauts fourneaux dits « à la bergamasque » ont un profil interne très simple, consistant en deux pyramides quadrangulaires reliées par leur base et qui l'une et l'autre ont une face verticale. Ils sont sans ouvrage, adossés à un relief,d'une hauteur d'environ 7 m. La tuyère est fortement inclinée vers le bas et le vent frappe une dalle de schiste qui brise et dévie le jet d'air. Ainsi la combustion est diffuse et l’allure est assez froide. L'alimentation en vent se fait par quelques trompes hydrauliques. L'appareil peut réaliser des campagnes assez longues, de plusieurs années[A 1] mais la section rectangulaire est bien moins performante que les formes se rapprochant du cercle[G 2].
Histoire
La méthode d'affinage bergamasque a été inventée en Lombardie (probablement sur les rives du Serio[G 3]). L'affinage de la fonte y est attesté très tôt, dès le XIVe siècle[3]. La technologie se diffuse vers la fin du XVIe siècle dans les Alpes[4], notamment dans le Dauphiné et la Savoie[A 2], en Suisse[G 3], en Autriche et en Italie[A 3]. Elle a été mise au point dans un secteur où les minerais de fer, donc les fontes, sont riches en manganèse (de 5 à 8 %, soit proches d'un spiegeleisen)[A 4]. Il y a ce « fait bien connu que ce procédé n'a jamais été employé que pour les fontes manganésifères. Il s'est répandu sur toute la chaîne des Alpes, d'une part dans la Savoie et le Dauphiné, de l'autre dans le Tyrol et la Carinthie, contrées où l'on ne trouve presque que des minerais spathiques. La seule exception à mentionner est la Toscane où l'affinage bergamasque est employé pour des fontes truitées, obtenues au moyen des minerais de fer oligiste de l'Île d'Elbe[A 3]. »[note 3]
Au milieu du XIXe siècle, la méthode, dont les trois étapes génèrent des dépenses de travail et de combustible excessives, est très critiquée pour son inefficacité. La technologie bergamasque est associée aux « procédés qui semblaient encore, il y a 30 ans, appartenir aux siècles les plus reculés pour ce qui est de la consommation de combustible[G 3] ». Cet avis est très largement partagé, mais ce handicap est en réalité assez relatif. Par contre, la qualité des fers obtenus est généralement inférieure à celle des fers issus de la méthode comtoise. Quoi qu'il en soit, les inconvénients de la méthode bergamasque ne sont généralement pas uniquement dus au procédé d'affinage en lui-même, mais plutôt à la mauvaise optimisation des feux et à la faiblesse des martinets[A 5].
Ainsi, les procédés bergamasques disparaissent pendant la première moitié du XIXe siècle en France, supplantés par les forges catalanes[G 4] et la méthode comtoise[A 5]. En 1836, la dernière forge française qui l'emploie, en Isère, cesse la commercialisation de fers produits avec cette méthode[5], Mais en Lombardie, la méthode bergamasque reste encore, à la même époque, d'un usage courant[A 5].
Procédé
Déroulement d'un affinage
Le foyer d'affinage est une fosse rectangulaire, typiquement de 0,6 m de large (c'est-à -dire de la varme au contrevent), la longueur de ces deux côtés faisant 0,7 m, et la profondeur 0,7 m. Les parois sont des plaques de fonte, alors que la sole est en briques. C'est donc un foyer assez profond (il l'est deux fois moins en Carinthie[6]), mais étant toujours à demi-plein de brasque, son volume utile est limité et fluctuant. La plaque avant (plaque de laiterol) dépasse pour pouvoir appuyer les outils et est percée pour vidanger les scories, une aire de travail est disposée à côté pour y gérer les matières, et une cheminée surplombe le foyer. La combustion est attisée par une tuyère inclinée de 20° vers le bas, alimentée par une soufflante, généralement une trompe semblable à celles des forges catalanes[A 6].
La première étape est la fusion lente de la fonte, puis sa solidification. Le foyer est rempli de charbon de bois jusqu'au dessus de la tuyère, les blocs de fonte sont dessus. La tuyère attise vigoureusement le feu, et le métal fond en une ou deux heures suivant la taille et la masse totale des blocs de fonte. Le métal fondu coule et se rassemble sous le charbon de bois. Une fois tout le métal fondu, le charbon de bois est retiré puis arrosé pour interrompre sa combustion : le bain liquide est alors découvert. On y jette alors une bonne quantité de battitures et pailles de fer oxydées (50 kg de pailles pour 250 kg de fonte), et l'ensemble est mélangé : le bain devient instantanément un agglomérat pâteux et hétérogène, une brèche métallique qui est extraite et refroidie à l'eau[A 6]. Cet agglomérat est appelé « mazelle » car la fusion s'étant déroulée dans une atmosphère oxydante, et un mazéage assez poussé s'est donc opéré avant même l'ajout des battitures[7].
La deuxième étape est la cuisson, ou le « pâtissage », des mazelles obtenues. Le foyer vide est comblé de brasque jusqu'au niveau de la tuyère. Une cinquantaine de kilos de fragments de mazelles est posée devant la tuyère, recouverte de poussier ou de petit charbon de bois. Un feu très doux est donné par la tuyère qui diffuse un faible débit de vent. Ainsi, les blocs de la mazelle s'agglomèrent et se soudent sans qu'il n'y ait fusion de la masse métallique. L'opération, qui dure 3/4 d'heure, est recommencée jusqu'à ce que toute la mazelle ait été convertie en gâteaux d'environ 50 kg[note 4] - [A 6].
La troisième étape est l'affinage proprement dit. Dans le foyer comblé de brasque jusqu'au niveau de la tuyère, un gâteau est posé d'un côté de la tuyère, et le charbon de bois de l'autre. Le métal est ramolli lentement, et s'écoule en grumeaux dans une dépression aménagée dans la brasque. Pendant cette opération, on ajoute encore des scories riches en fer ou des battitures entre la tuyère et le gâteau. Au bout de 3/4 d'heure, le gâteau est complètement fondu en loupe, et celle-ci est porté au martinet[A 6].
- 1re étape (fusion).
Les morceaux de fonte brute sont lentement fondus. On y ajoute alors au bain du fer oxydé. Une masse hétérogène de fonte à demi-affinée et d'oxydes se forme instantanément : la mazelle. - 2e étape (cuisson).
La mazelle est chauffée à feu doux, pour former une masse homogène, le gâteau.
Performance
Il faut environ 18 heures pour transformer la fonte en barres de fer. Comparée à d'autres méthodes d'affinage, la méthode génère un faible déchet de la fonte, même si on prend en compte que les battitures apportent un fer bon marché[note 5] au procédé. La première étape, de fusion lente en atmosphère oxydante, est un mazéage qui consomme tout le manganèse, évacué sous la forme d'oxyde de manganèse (MnO) avec les scories. Ainsi, lors de la dernière opération, l'oxyde de manganèse ne vient pas diluer les oxydes de fer amenés par les battitures : leur action oxydante est alors maximale lors de l'affinage[A 6]. Cette action préfigure le principe du puddlage gras mis au point vers 1830[8] - [note 6].
FeO / Fe2O3 | MnO | SiO2 | Al2O3 | CaO | MgO | ||
---|---|---|---|---|---|---|---|
Fusion-Mazéage | Lecco | 38,1 | 25,7 | 28,2 | 6 | 2 | |
Allevard | 45 | 29 | 23 | 1 | 2 | 1 | |
Affinage | Allevard 1 | 55,1 | 19 | 10,5 | 1 | 17 | 1 |
Allevard 2 | 80 | 8 | 3,5 | 0,5 | 7 | 0,5 |
Mais le poids de combustible brûlé atteint au moins le double de celui de la fonte affinée[note 7], le combustible coûte presque autant que la matière première. Ainsi, « ce qu'il y a de plus défectueux dans la méthode bergamasque, c'est la nécessité où est plusieurs fois l'ouvrier pendant l’opération de refroidir à peu près complètement le fourneau afin de reconstruire son feu de brasque[A 7]. » La deuxième étape, qui se fait à plus basse température, interrompt la chauffe et s'avère pénalisante, raison pour laquelle elle est parfois réalisée dans un foyer dédié[A 7].
La méthode bergamasque est proche la méthode nivernaise, cette dernière traitant cependant des fontes grises plus difficiles à affiner et employant plusieurs foyers. La méthode comtoise qui, dans les Alpes françaises, supplante la méthode bergamasque vers 1820, est très supérieure notamment pour la qualité des fers qu'elle permet d'obtenir[A 5] - [A 8].
Fonte (kg) | Charbon de bois (kg) | Main d'œuvre (jours) | ||
---|---|---|---|---|
Méthode bergamasque | Lecco / Val Sapina | 108 | 266 | 0,93 |
Dongo (air préchauffé) | 120 | 190 | 0,71 | |
Val Brembana (it) | 117 | 220 | 0,90 | |
Sovere et Val Camonica | 118 | 280 | 0,95 | |
Méthode comtoise | 135 | 140 | 0,84 | |
Méthode nivernaise | 135 | 285 | 1,00 | |
Méthode wallonne | 150 | 200 | 1,00 | |
Méthode styrienne | 110 | 300 | 1,00 |
Notes et références
Notes
- Les procédés relatifs à la fabrication d'acier naturel sont, en français, désignés sous le nom de « méthode » plutôt que de « procédé ».
- Le nord de l'Italie a été le berceau de plusieurs innovations technologiques dans l'histoire de la production de l'acier. On relève notamment, en 1463, une description de Le Filarète d'un procédé de fabrication d'acier par la méthode indirecte, c'est-à -dire haut fourneau puis affinage, à Ferriere[1], avec un haut fourneau dont la fonte était coulée deux fois par jour dans de l'eau pour en faire un granulé[2].
- La fait que la méthode bergamasque coincide avec la présence de minerais manganésifères ne signifie pas que ses spécificités sont nécessairement dues à ce contexte, ni qu'elle est plus efficace que d'autres pour les traiter.
- Audibert, qui décrit en 1842 la méthode telle qu'elle est pratiquée en Lombardie, réemploie le terme des fondeurs italiens cotizzo, pour décrire ces gâteaux[A 6]. En 1775, Grignon relève que les forgerons dauphinois appellent ces gâteaux coti de mazelle[7].
- Leur fer contenu dans les battitures coûte cinq fois moins que celui de la fonte[A 6].
- Avec des scories aussi oxydées et légèrement basiques, la méthode bergamasque peut donc réaliser une déphosphoration, à l'instar du puddlage gras.
- Audibert conteste les auteurs qui évoquent des consommations de combustible atteignant le triple, voire le septuple, du poids de fonte[A 6].
Références
- Ed. Audibert, « Notice sur l'affinage du fer par la méthode bergamasque dans les usines de Lombardie », Annales des Mines, Carilian-Gœury et Dalmont,‎ (voir dans la bibliographie)
- p. 625-626
- p. 613
- p. 674
- p. 623 ; 632-639
- p. 641-642
- p. 644-682
- p. 660
- p. 677-678
- Émile Gueymard, Statistique minéralogique, géologique, métallurgique et minéralurgique du Département de l'Isère, (voir dans la bibliographie)
- p. 735
- p. 736
- p. 774
- p. 778
- Autres références
- (en) Donald B. Wagner, Science and Civilisation in China : 5. Chemistry and Chemical Technology : part 11 Ferrous Metallurgy : (suite de Joseph Needham), Cambridge University Press, , p. 349–351 ; 354-355
- (en) B. G. Awty, « The blast furnace in the Renaissance period: haut fourneau or fonderie? », Transactions of Newcomen Society, vol. 61,‎ 1989–90, p. 67
- Corbion 2003, § Fournus
- Pierre Judet, « Industrie, société et environnement. Mines, hauts-fourneaux et forêts de basse Maurienne au XIXe siècle », Siècles, no 42,‎ (lire en ligne)
- Compte-rendu des travaux des ingénieurs des mines pendant l'année 1843, Imprimerie royale, (lire en ligne), p. 16
- Carl Johann Bernhard Karsten (trad. F. J. Culmann), Manuel de la métallurgie du fer, t. 3, Metz, , 2e éd. (lire en ligne), p. 128-130
- Jacques Corbion (préf. Yvon Lamy), Le Savoir… fer — Glossaire du haut fourneau : Le langage… (savoureux, parfois) des hommes du fer et de la zone fonte, du mineur au… cokier d'hier et d'aujourd'hui, , 5e éd. [détail des éditions] (lire en ligne), § Méthode Bergamasque
- John Percy (trad. traduction supervisée par l'auteur), Traité complet de métallurgie, Paris, Librairie polytechnique de Noblet et Baudry éditeur, (lire en ligne), p. 461
Voir aussi
Bibliographie
- Ed. Audibert, « Notice sur l'affinage du fer par la méthode bergamasque dans les usines de Lombardie », Annales des Mines, Carilian-Gœury et Dalmont, 4e série, t. 1,‎ (lire en ligne)
- Émile Gueymard, Statistique minéralogique, géologique, métallurgique et minéralurgique du Département de l'Isère, , 998 p. (lire en ligne)