Usine sidérurgique de l'ouest du Japon
JFE Steel West Japan Works
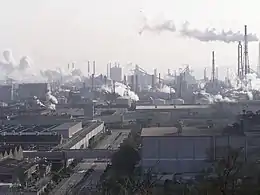
Type d'usine |
Usine sidérurgique (en) |
---|
Opérateur |
---|
Production |
18,69 mégatonne d’acier () |
---|
Localisation |
---|
L'usine sidérurgique de l'ouest du Japon, actuellement JFE Steel West Japan Work, est un complexe sidérurgique sur les bords de la mer intérieure de Seto. Elle a été créé en 2003 par la fusion des deux usines sidérurgiques de Mizushima (ja) (Kawasaki Steel) avec celle de Fukuyama (NKK), situées sur le rivage nord de la mer intérieure, c'est-à -dire sur Honshū.
En 2021, l'usine est propriété de JFE Holdings. C'est l'un des plus gros complexes sidérurgique au monde.
Historique
Usine de Mizushima
La construction par Kawasaki Steel de l'usine de Mizushima commence en 1961. En 1967, le premier haut fourneau, le HF1, est mis à feu en même temps qu'une aciérie et un laminoir à tôles fortes : c'est l'acte de naissance d'une filière intégrée. Sa capacité initiale est de 2 Mt/an[1].
Dans les années qui suivent une constellation d'ateliers se greffe à la filière initiale, dont un laminoir pour profilés lourds, un train continu à chaud, un train à froid, un train à barres, etc. En 1973 le HF4 est mis à feu, ainsi que le convertisseur à oxygène n°6[1].
À partir de la deuxième moitié de la décennie 1970, l'usine se modernise pour améliorer sa compétitivité. En 1976, le train à tôles fortes n°2 qui est mis en service est totalement automatisé. Un trail à billettes et la ligne de recuit continu n°1 sont mis en service en 1984. Des lignes de finissage et revêtement sont aussi construites[1].
En 1994, le train à barres est équipé d'un laminoir à 4 cylindres. En 1998, c'est au tour du train à fil d'être équipé de cette technologie. Si l'idée est ancienne car elle permet de fortes passes tout en garantissant une excellente précision dimensionnelle du laminage des profils ronds, elle butait jusqu'alors sur la complexité du laminoir et sur le grossissement indésirable des grains. La solution développée, novatrice, consiste à combiner ce laminage avec un laminoir classique à 2 cylindres[1].
À la fin du XXe siècle, l'usine développe des modèles informatiques pour gérer la complexité croissante de son carnet, qui pénalise la gestion de production de cette usine géante. Tant le séquencement de la production des différents alliages, que les imprévus consécutifs au marché, sont modélisés afin de conserver une bonne efficience[1].
En 2002, 8,55 Mt ont été produites, consistant essentiellement en des coils laminés à chaud (2,39 Mt), des plaques d’acier (1,83 Mt), des bobines laminées à froid nues ou revêtues (2,34 Mt), des produits longs (1,19 Mt) et des semi-produits sidérurgiques divers (0,47 Mt). L'usine est alors un complexe sidérurgique parfaitement intégré exploitant[1] :
- trois chaînes d'agglomération (surface totale de 1 005 m2) ;
- une cokerie (6 batteries totalisant 464 fours) ;
- trois hauts fourneaux (HF2 de 2 857 m3, HF3 de 4 359 m3 et HF4 de 5 005 m3) ;
- deux aciéries de conversion (3 convertisseurs de 180 t et 3 convertisseurs de 320 et 290 t) et une aciérie électrique (1 four électrique de 30 t et un de 100 t). Ces fours desservent quatre outils de dégazage, puis quatre coulées continues à brames à 2 lignes chacune, deux à blooms totalisant 10 lignes et une voie lingot ;
- un train continu à chaud capable de laminer 2 200 mm de large et d'autres laminoirs à chaud spécialisés (plaques, profilés lourds, profilés moyens et fil) ;
- un laminoir à froid pour les bobines et d'autres laminoirs à froid spécialisés (pour acier électrique et fil) ;
- plusieurs lignes de finissage et revêtement (galvanisation, étamage, décapage, production de tubes,, etc.).
En 2003, au moment de sa fusion avec le site de Fukuyama, l'usine exploite 3 hauts fourneaux et peut produire 8 Mt/an d'acier[1].
Usine de Fukuyama
L'usine de Fukuyama est fondée en 1965 par NKK. Les hauts fourneaux y sont mis à feu rapidement et à un rythme soutenu : HF1 en 1966 et HF2 en 1968. En 1973, l'usine exploite 5 hauts fourneaux et 3 aciéries. Par ailleurs, dans le même moment un train continu à chaud, un train à tôles fortes et un laminoir pour profilés lourds sont mis en servic[1].
En 1974, l'usine bat son record de production et produit 13,4 Mt d'acier. Mais dans le contexte de la crise mondiale de la sidérurgie (en) consécutive au Premier choc pétrolier, la demande s'effondre et l'usine doit réduire sa production. Dans la décennie qui suit, une série de fermeture de hauts fourneaux et d'aciérie fait progressivement baisser la production jusqu'à 13,4 Mt en 1986[1].
L'usine renonce alors aux volumes pour privilégier la valeur ajoutée de ses produits. Les marchés visés sont alors la tôle automobile, les aciers électriques, les tôles galvanisées, etc.[1]
En 1980, l'usine développe une technologie de refroidissement ultra-rapide, le OLAC (On-Line Accelerated Cooling). En 1998, une version évoluée est développée, le super-OLAC, qui est mise en service sur le train à profilés lourds en 2000, et le train à chaud en 2002[1].
En 2002, 10,19 Mt ont été produites, ce qui fait de cette usine la plus grosse usine sidérurgique du Japon. La production consiste essentiellement en des bobines laminées à froid nues (1,25 Mt) et revêtues (1,94 Mt), des plaques d’acier (1,08 Mt), des tubes (0,48 Mt), des rails et des profilés (0,84 Mt) et des semi-produits sidérurgiques divers (1,25 Mt). L'usine est alors un complexe sidérurgique parfaitement intégré exploitant[1] :
- deux chaînes d'agglomération (surface totale de 930 m2) ;
- une cokerie (3 batteries totalisant 444 fours) ;
- quatre hauts fourneaux (HF2 de 2 828 m3, HF3 de 3 223 m3, HF4 de 4 288 m3 et HF5 de 4 664 m3) ;
- deux aciéries (3 convertisseurs de 250 t et 2 convertisseurs de 320 t). Ces fours desservent quatre outils de dégazage, puis cinq coulées continues à brames totalisant 10 lignes, une à blooms à 4 lignes et une à billettes à 6 lignes ;
- deux trains continu à chaud capables de laminer 1 925 et 1 641 mm de large (le deuxième est dans le prolongement d'une coulée continue) et d'autres laminoirs à chaud spécialisés (plaques et profilés lourds) ;
- trois laminoirs à froid pour les bobines (dont deux en tandem avec le décapage) ;
- plusieurs lignes de finissage et revêtement (galvanisation, étamage, décapage, production de tubes,, etc.).
En octobre 2002, l'usine devient la première usine japonaise a franchir le seuil symbolique des 300 Mt de fonte brute produites pendant son existence. Dans la même période, l'usine réactive son haut fourneau HF2, retournant à une configuration à 4 hauts fourneaux et une capacité de production de 10 Mt/an d'acier : à ce moment-là , l'usine de Fukuyama devient la plus grosse usine sidérurgique au monde et la seule du Japon à exploiter quatre hauts fourneaux[1].
Complexe de Mizushima-Fukuyama (depuis 2003)
Le , la toute récente JFE Holdings fusionne l'usine de Mizushima de Kawasaki Steel avec celle de Fukuyama appartenant à NKK, située sur le rivage nord de la mer intérieure de Seto. Les deux sites combinés produisent 18 Mt/an d'acier : leur association crée un des plus gros complexes sidérurgique au monde[1].
La production d'acier du complexe a été de 18,69 Mt en 2019[2].
Références
- (en) « West Japan Works, JFE Steel », JFE Technical Report, JFE Holdings, no 1,‎ (lire en ligne [PDF])
- (en) « JFE Group Report 2020 » [PDF], JFE Holdings (consulté le )