Usine sidérurgique de Luleå
Norrbottens Järnverk
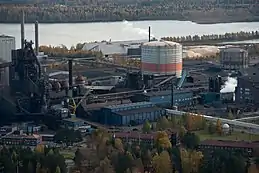
Type d'usine |
Usine sidérurgique |
---|
Produits |
---|
Situation | |
---|---|
Coordonnées |
65° 33′ 41″ N, 22° 12′ 30″ E |
![]() ![]() |
L'usine sidérurgique de Luleå, actuellement SSAB Luleå, est un complexe sidérurgique à Luleå, en Suède. Historiquement connu comme la Norrbottens Järnverk AB, ou NJA, c'est une ancienne entreprise publique sidérurgique[2]. Fondée en 1940, ses actifs sont intégrés en 1978 au groupe SSAB, qui en a fait le cœur de l'actuelle usine sidérurgique.
Histoire
Pour les références, voir dans le corps de l’article
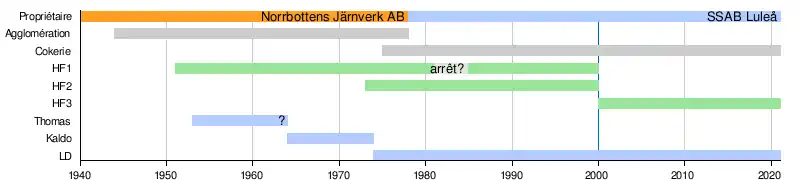
Les premiers projets d'usine sidérurgique datent de 1917, quand le Parlement suédois étudie la possibilité d'implanter un ou plusieurs hauts fourneaux électriques[note 1] à Norrbotten où le potentiel hydroélectrique était prometteur. Mais la Première Guerre mondiale et les besoins nationaux en électricité ont raison du projet[3].
En 1939, le gouvernement décide d'édifier une usine sidérurgique à Luleå et, en 1940, la Norrbotten Järnverk AB est créée. La zone comprise entre Svartöstaden (sv) et Aronstorpsviken (sv) est choisie comme emplacement pour l’usine, et les travaux de fondation et de terrassement commencent en 1941. La Seconde Guerre mondiale agitant alors l'Europe, le chantier est alors pénalisé par la mobilisation de la main d'œuvre et des matériaux. Le premier bâtiment de bureau est terminé en 1942, complétant les bureaux de la ferme Svensson à Aronstorp. La centrale thermique et deux fours électriques sont achevés en 1943. La premièce coulée du four électrique 1 se déroule le , le four 2 lui emboîtant le pas en novembre de la même année. Le , l'usine d'agglomération est démarrée[4]. La capacité du site s'élève alors à environ 60 000 t/an de fonte brute[5]. Des fours électriques démarrent en 1945, une fonderie en 1948, un haut fourneau au coke (dont la première coulée se déroule le [4]), un gazomètre et un blooming en 1951, une machine de coulée en gueuses, un laminoir dégrossisseur et un laboratoire en 1952. En 1953, une aciérie Thomas, un laminoir finisseur, un four à dolomie et un train de tréfilage sont démarrés[6].
En 1954, après des investissements supplémentaires, l'usine emploie environ 2 000 personnes. Elle consiste en un haut fourneau, un blooming et un laminoir dégrossisseur, produisant de plus de 200 000 t de produit laminés et environ 30 000 t de produits revêtus. L'usine est rentable jusqu'en 1962, quand la chute des prix des produits longs, notamment les rails et fils qui consistent l'essentiel de la production, conduisent à des pertes et des recapitalisations par l'État suédois[5]. Cette situation se produit alors que les laminoirs ont bénéficié d'un ambitieux programme d'investissement pendant les années 1960, au point qu'en 1963, le train à bandes est décrit comme le plus moderne d'Europe[6].
Pour améliorer sa compétitivité, l'usine investit et augmente sa production, qui atteint en 1970 environ 425 000 t de produits laminés, fabriqués par 3 400 employés. Une montée en gamme apparaît également nécessaire, ce qui amène à des investissements complémentaires. Au début des années 1970, la capacité de production atteint 1,6 Mt/an de fonte brute, 1,2 Mt/an d'acier brut, 0,8 Mt/an de produits pré-laminés et de 0,15 Mt/an de profilés soudés, essentiellement destinés à la construction navale. L'augmentation de la capacité a été obtenue par la construction d'un deuxième haut fourneau (démarré en [7]), d'une aciérie LD (pour remplacer l'aciérie Kaldo[8]) et de deux coulées continues. Une cokerie est également construite, pour alimenter l'usine dont les besoins en coke passent de 250 à 850 kt/an. Le déséquilibre entre les installations amont et aval, ces dernières datant d'ailleurs des années 1950, est cependant un handicap et une partie de la production est vendue à l'état de demi-produit[5].
En 1974, l'industrie sidérurgique mondiale est en crise. La Norrbottens Järnverk ne fait pas exception : surendettement, marché des produits longs et de la construction navale en repli, mélange d'installations obsolètes et modernes[5]. L'usine produit 830 kt, 589 kt par les hauts fourneaux et 241 kt par les fours électriques, alors qu'elle est capable de produire plus du double. En 1975, la capacité est de 1 700 kt/an, 4 985 employés y travaillent et le chiffre d'affaires est de 968 Mkr[note 2] - [9]. La stratégie, jusqu'ici orientée sur les volumes et l'export, est réorientée vers les produits à haute valeur ajoutée pour le marché national[7]. L'aciérie Kaldo est arrêtée en 1974 [9], le haut fourneau 1 de 1981[7]. Un ambitieux programme d'investissement, le Stålverk 80 (sv), est mis œuvre par les sociaux-démocrates. Il aboutit à la construction d'infrastructures publiques à Luleå, mais quand la non rentabilité de l'investissement industriel devient une évidence en 1976, le gouvernement conservateur Regeringen Fälldin I (sv) l'abandonne.
La production est rationalisée : l'usine d'agglomération est fermée en 1978 (les hauts fourneaux fonctionnent alors exclusivement avec des boulettes), mais le haut fourneau 1 est remis à feu en 1985. Le , le nouveau haut fourneau 3 démarre. Ce haut fourneau, qui intègre les dernières technologies, a une capacité de production de 2 200 kt/an. Construit sur l'emplacement du haut fourneau 2, il remplace les deux hauts fourneaux[note 3] - [10].
- La cokerie. À gauche, on distingue le convoyeur à bande qui part vers le haut fourneau, à 3 km de là.
- L'aciérie LD. Au premier-plan, en blanc, l'usine à oxygène.
- Les laminoirs.
Notes et références
Notes
- Un haut fourneau électrique est un haut fourneau doté d'électrodes en son creuset. Il permet de remplacer une partie du coke ou du charbon de bois nécessaire au fonctionnement par de l'électricité.
- Chiffres à comparer aux 1 150 kt/an, 6 145 employés générant un chiffre d'affaires de 1 300 Mkr à l'Usine sidérurgique de Borlänge, dont le positionnement qualitatif est net[9].
- Au moment de sa fermeture, le haut fourneau 1, construit en 1951, avec un gueulard à cloche et un unique trou de coulée, a une capacité de 650 kt/an. Le haut fourneau 2, construit en 1973, est plus un peu plus gros mais surtout bien plus moderne : il dispose d'un gueulard Paul Wurth et de deux trous de coulée : sa capacité est de 1 350 kt/an[10].
Références
- (sv) « SSAB i Luleå », SSAB
- (sv) « Norrbottens järnverk AB », dans Nationalencyklopedin (lire en ligne)
- (sv) Thomas Bucht, « Arbetsmiljön på Luleå Järnverk åren 1968-1981 : En undersökning av arbetsmiljön på järnverket i Luleå sett ur företagstidningarna Vårt NJA och Luleå Bulletinens synvinklar », Luleå tekniska universitet Institutionen för ekonomi, teknik och samhälle,
- (sv) « Svenskt Stål AB »
- (sv) Nils Gunnar Åsling, « Regeringens proposition 1976/77:57 om kapitaltillskott till Norrbottens Jämverk AB », Sveriges riksdag,
- (sv) « Program för Norrbottens industriarv » [PDF], (ISSN 0283-9636), p. 31
- (sv) Kristina Söderholm, Snart sluteldat för Luleås kråkor : Förhandlingar under 1970-talet inför tillvaratagandet av stålverkets överskottsgas i det lokala fjärrvärmenätet, Luleå, (ISBN 978-91-7583-842-7, ISSN 1402-1528, lire en ligne [PDF])
- (en) F. E. Brantley, Mineral yearbook, (lire en ligne [PDF]), p. 617 ; 619
- (sv) Handelsståls industrin inför 1980-talet, Stockholm, (ISBN 91-38-03332-1, ISSN 0375-250X, lire en ligne [PDF]), p. 92-93 ; 97
- (en) Lena Sundqvist Ökvist, Anna Dahlstedt et Mats Hallin, « The Effect on Blast furnace Process of changed Pellet Size as a Result of segregation in Raw Material Handling. » [PDF], SSAB,