Projection thermique
La projection thermique fait partie des procédés industriels de traitement de surface avec apport de matière par voie sèche. Elle consiste à projeter à l’aide d’un gaz vecteur un matériau, généralement sous forme de poudre, à haute température et à grande vitesse, sur un substrat (surface de la pièce à revêtir) généralement métallique, afin de former un revêtement.
Ce revêtement, aussi appelé « couche » ou « dépôt », sert à fonctionnaliser la surface, c’est-à -dire à modifier ses propriétés physiques ou chimiques (en matière de corrosion, fatigue thermique, usure, frottement, réactivité, etc.). Il peut aussi avoir une fonction esthétique.
Les techniques de projection thermique permettent de réaliser des dépôts granulaires (10 à 100 µm d’épaisseur) et massifs (>100 µm d’épaisseur) de morphologies très variées. Des procédés plus récents permettent également la réalisation de dépôts nanostructurés.
Divers procédés existent. Les opérateurs sont dits « métalliseurs ». Ils sont souvent exposés à l'inhalation de métaux toxiques, à des degrés dépendants du procédé utilisé, selon l'environnement de travail, et selon le bon port des protections respiratoires et autres[1].
Principe de base
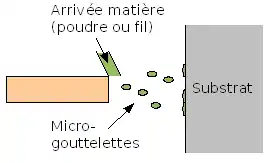
La projection thermique est un procédé en ligne de mire qui se présente sous la forme d’une torche (on parle également de chalumeau ou fusil de projection) avec une buse d’où est expulsé un gaz vecteur transportant la matière à déposer. La torche peut être manipulée comme un pistolet par l’opérateur ou bien montée sur un dispositif automatisé tel un bras robotisé.
Le gaz vecteur sert à accélérer et transporter jusqu'au substrat de fines particules (typiquement 5 à 100 micromètres) qui peuvent être à l'état liquide, pâteux voire solide. Ce gaz vecteur peut être aussi source enthalpique, permettant de chauffer ces particules jusqu'au point de fusion. D'autres procédés utilisent un arc électrique pour fondre le matériau.
Les particules ainsi projetées sur le substrat s'écrasent selon leur vitesse, état physique, température etc. formant des lamelles (ou splats).
L'accumulation et l'empilement des lamelles sur le substrat permet de réaliser le revêtement.
Historique
L’invention de la projection thermique est attribuée à Max Ulrich Schoop, un ingénieur suisse. Son idée était de réaliser des revêtements adhérents à partir d’impacts de particules issus d’une poudre chauffée venant s’écraser sur la pièce à traiter (substrat), pour réaliser des dépôts métalliques denses. Cette idée lui aurait été inspirée de l’observation de ses enfants tirant à la carabine sur le mur de son jardin où les balles de plomb formaient des impacts écrasés[2] - [3].
Il dépose deux brevets en Allemagne et en Suisse en 1909 [4] - [5]. Dans les revendications des brevets, le terme de projection thermique est défini comme "une méthode où le métal liquide est pulvérisé sur la surface au moyen d’une substance gazeuse sous pression". Les brevets de M. U. Schoop décrivent comment réaliser des dépôts de cuivre, d’argent, d’étain, de zinc, d’aluminium et d’autres alliages sur pratiquement tous types de substrats (métal, bois, verre, papier, tissus) par un apport de poudres finement divisées traitées par une flamme soufflante. Un gaz porteur peut aussi être utilisé pour accélérer et diriger le jet de poudres. Schoop voit dans son invention un procédé pratique et peu onéreux dans l’application des revêtements antirouille sur les ponts et les coques des navires.
L’utilisation d’un plasma comme source de chaleur n’apparait que dans les années 60 dans un contexte d’émulation autour des plasmas thermiques générés par arc électrique [6]. Les premiers brevets sont ceux de Gabriel M. Giannini en 1960 (Plasmadyne Corp., Californie, USA) [7] et de Robert M. Gage en 1962 (Union Carbide, Buffalo, NY, USA) [8]. Ils s’inspirent du générateur plasma haute température de H. Gerdien et A. Lotz (1922) [9].
Dans les années 1980 est développé en URSS la technique de projection dynamique à froid (Cold Spray) à partir de l'observation accidentelle de la formation rapide de dépôts lors de l'érosion de particules exposées à un écoulement grande vitesse chargé de poudre fine[10].
Principaux types de projection thermique
Il existe de nombreuses manières de réaliser la projection thermique, mais les plus couramment utilisées dans l'industrie sont dits par projection par chalumeau "flamme-fil", par arc-fil, "flamme-poudre", flamme supersonique, à arc électrique ou encore "High Velocity Oxy-Fuel" (HVOF) ou au plasma (plasma d'arc soufflé...)[11] - [1].
- Procédé gaz-flamme.
- Procédé plasma.
Énergie chimique
- Flamme d'oxygène à haute vitesse (High Velocity Oxy-Fuel, HVOF)
- Canon à détonation
- Flamme (Flame Spraying, FS)
Énergie électrique
- Fil à l'arc électrique (Arc Wire Spraying, AWS)
- Plasma (Plasma Spraying, PS)
- Sous air :
- Conventionnelle (Air Plasma Spraying, APS, ou Conventional Plasma Spraying, CPS)
- Projection voie liquide (Liquid Plasma Spraying, LPS)
- Suspension (Suspension Plasma Spraying, SPS)
- Solution (Solution Precursor Plasma Spraying, SPPS)
- Sous atmosphère spécifique :
- Sous eau (Underwater Plasma Spraying, UPS)
- Sous gaz inerte (Inert Gas Plasma Spraying, IGPS)
- Sous vide (Vacuum Plasma Spraying, VPS)
- Sous atmosphère contrôlée (Controlled Atmosphere Plasma Spraying, CAPS)
- Sous air :
Énergie cinétique
- Projection dynamique Ă froid (cold spray)
Flamme simple
Ce procédé utilise la combustion d'un gaz pour projeter le matériau d'apport sur le substrat. En général, on utilise un chalumeau. Cette technique est très simple et très répandue dans l'industrie, mais elle est limitée en température et en vitesse de projection. Il est possible de projeter indifféremment le matériau sous forme de poudre ou de fil.
Flamme supersonique
Le système à projection par flamme supersonique (High Velocity Oxy-Fuel, HVOF) est une amélioration de la projection au chalumeau. Il utilise le principe des moteurs-fusées pour créer une flamme avec une vitesse d'éjection des gaz très importante.
Plasma d'arc soufflé
Les torches à plasma d'arc soufflé utilisent le confinement d'un arc électrique pour augmenter fortement sa température (le cœur du dard plasma se situe généralement entre 6 000 et 14 000 K, une grande partie du jet étant à température bien moindre) de façon à générer un plasma à partir d'un gaz plasmagène. Ce plasma sert ensuite à fondre et à accélérer le matériau à projeter.
Selon le mélange de gaz utilisé, les propriétés du plasma varient, permettant de modifier la conductivité thermique (transfert de la température au matériau, le temps de séjour restant très faible et, si la conductivité est insuffisante, insuffisant pour fondre le matériau) ou de modifier la viscosité du jet (vitesse des particules). Ainsi les gaz les plus couramment utilisés en projection thermique plasma sont l'argon, l'hydrogène, l'hélium et l'azote. L'argon et l'hélium sont recherchés pour leur viscosité tandis que l'hydrogène, l'hélium et l'azote sont recherchés pour la conductivité. Ainsi un plasma d'argon est très peu efficace pour chauffer un matériau sauf pour les très bas points de fusion comme le zinc, il lui est alors généralement ajouté de l'hydrogène pour permettre de fondre la plupart des matériaux.
Trois milieux de projection sont utilisés suivant les caractéristiques souhaitées du revêtement :
- dans l'air sous pression atmosphérique (Atmospheric Plasma Spraying, APS), le plus courant ;
- dans un gaz neutre (souvent l'argon) à la pression atmosphérique (Inert Gas Plasma Spraying, IPS). Permet de projeter des matériaux fortement oxydant et augmente la température de l'écoulement. L'intérêt de cette technique réside principalement à la réalisation de revêtements sur substrats trop sensibles thermiquement. Des machines à plus hautes pressions ont été développées comme le CAPS pouvant atteindre environ 3 bars sans trouver réellement de débouchés ;
- dans un gaz neutre à faible pression (100 mbar) (Low Pressure Plasma Spraying, LPPS). Augmentation de la vitesse de projection et donc de la densité et de l'adhérence du dépôt tout en évitant l'oxydation du matériau d'apport et du substrat.
Des développements sous très faibles pressions (environ 1mbar) sont en cours d'industrialisation visant à allier les caractéristiques des techniques de type PVD et la productivité du procédé plasma.
Projection à arc électrique double fil
Ce procédé, également appelé arc fil (arc wire spraying, AWS), utilise un gaz vecteur froid (typiquement de l'air ou de l'azote) et une source de courant. Un arc électrique (environ 6 000 K) est établi entre deux électrodes sacrificielles qui sont sous la forme de fils du matériau d'apport. Les matériaux utilisés doivent donc impérativement être conducteurs électriques. La matière ainsi fondue est atomisée par le gaz vecteur et dirigée sur la pièce à traiter. Les bobines de fils sont entraînées régulièrement afin d'obtenir un arc aussi continu que possible. Cette technique est l'une des plus anciennes (1918[3]). Elle offre une grande productivité et un faible coût.
Projection dynamique Ă froid
Cette technique (cold spray) est plus récente. Elle consiste à accélérer au-delà d'une vitesse critique le matériau d’apport (300 à 1 500 m/s) sous forme de poudre. Ces vitesses entrainent une déformation plastique à l’impact sur le substrat suffisamment importante pour former un revêtement adhérent. Il n'y a pas de combustion des gaz de projection, les températures de projection sont très faibles en comparaison des autres procédés (300 à 1 100 °C). La matière avant impact n'est donc pas fondue. Il faut cependant que le matériau projeté soit ductile pour pouvoir se déformer, ce qui limite généralement l’utilisation de cette technique aux métaux.
Canon à détonation
Contrairement aux procédés à flamme, le procédé n'utilise pas une combustion diffusante et continue, mais se sert de la détonation comme source de chaleur et vecteur de transport de la poudre. Il en résulte une forte accélération (environ 600 m/s) et une température élevée (env. 3 000 °C) des particules. C'est un procédé discontinu, il fonctionne à quelques hertz. Sous brevet il n'est exploité que par la société Praxair.
Matériaux d'apport
Un très grand nombre de matériaux sont utilisables avec l'ensemble des techniques ou avec une en particulier en forme de poudres, fils ou cordons. Tous matériaux peuvent être projetés. Cependant, les matériaux qui fondent en se décomposant tels que l'hydroxyapatite ou YBCO ou ceux qui n'ont pas point de fusion, tel que graphite, doivent être préparés avec plus de précautions. Soit par l'optimisation de paramètres de la projection (hydroxyapatite partiellement fondu), soit par une préparation de poudres avec les particules enrobées (graphite enrobé par nickel).
Plusieurs matières organiques peuvent être projetées par les torches appropriées.
Les métaux et les céramiques sont traditionnellement fréquemment employés, ils peuvent aussi être utilisés en composites pour modifier les propriétés du revêtement. Par exemple, les composites de carbures de tungstène (WC) avec du cobalt (Co) ou du Nickel (Ni) sont très souvent projetés. La particularité du WCCo est une forte augmentation de la dureté de la pièce de l'ordre de 900 à 1 000 HV.
Substrat (surface de la pièce à revêtir)
Dans les applications industrielles, les substrats sont généralement des pièces métalliques et des alliages, mais il est possible de traiter toute sorte de surface comme des bétons, des céramiques, des composites, du bois et des verres.
Cependant, des incompatibilités existent avec certaines techniques (fragilité, sensibilité thermique, forme trop complexe ou inaccessible) ou avec le matériau d'apport (problème de mouillabilité, adhérence, dilatation différentielle).
Préparation des surfaces
En plus d’être nettoyées, les surfaces à traiter subissent généralement une étape de sablage qui permet de créer une rugosité pour favoriser l’adhésion des particules déposées.
Les substrats peuvent aussi être préalablement chauffés avant la projection pour mieux contrôler les mécanismes de croissance et favoriser l’étalement des particules fondues.
Pendant l’étape de projection il est également possible de refroidir la pièce à l’aide de différents dispositifs comme par exemple en utilisant un flux d’air comprimé.
Risques et dangers pour la santé
Une étude de santé au travail de 2018 a caractérisé les émissions et évalué les niveaux d’expositions au chrome (Cr) et au nickel (Ni) à différents postes de projection thermique pour aider à élaborer de meilleures stratégies de surveillance des opérateurs. Elle s'est basée sur des prélèvements d'air individuels et d’ambiance in situ, mais aussi sur des analyses d'urine[1].
Elle confirme que les métalliseurs projetant de l’oxyde de chrome par plasma sont effectivement exposés à du Cr hexavalent (Cr VI), et note que dans certains cas les taux de chrome dans l'air dépassaient la VLEP-8 h de 1 μg/m3. La chromurie (taux de chrome dans les urines) était plutôt faible, (moins à 2 μg/g créatinine, c'est-à -dire bien en dessous de la valeur-limite américaine retenue pour les soudeurs (25 μg/g créatinine) mais proche de la valeur de 1,8 μg/g créatinine retenue par l’ANSES pour les employés affectés au chromage[1]. Le Ni urinaire chez les métalliseurs, tous procédés confondus était « relativement élevés par rapport à ceux des opérateurs non-exposés », les dernières valeurs étaient cependant presque comparables à celles de la population générale (11 μg/g créatinine et 3,8 μg/g créatinine respectivement)[1] ce qui laisse penser que les équipements de protection individuelle adaptés à l’activité et bien utilisés permettent de limiter les risques d'intoxication par des éléments traces métalliques[1]. Parmi les cas étudiés le procédé flamme-fil était le plus à risque. D'autres études doivent compléter ce travail[1].
Modélisation

Un procédé de projection thermique peut être modélisé[13], à des fins de compréhension fine des phénomènes (la modélisation peut accéder à des grandeurs qu'il est impossible de mesurer, comme le gradient de température au sein des particules lors de leur séjour dans le plasma), de mise au point et d'optimisation du procédé. Ce type de modélisation a recours à la mécanique des fluides numérique.
Exemples d'applications
Les domaines applicatifs sont très larges, du simple zingage pour les infrastructures métalliques (ponts), aux applications de plus haute technologie comme dans les moteurs à réaction d'avion avec la popularisation des abradables (matériaux très friables permettant à chaud de réduire les fuites par l'adaptation des dimensions lors de la mise en service). Ainsi on pourra noter son utilisation en électrotechnique, dans le médical (prothèses), les turbines à gaz, l'automobile (molybdénage des bagues de synchronisation entre autres), le nucléaire, etc.
Notes et références
- Nadège Jacoby & al. (2018) Évaluations biologique et atmosphérique des métaux en projection thermique [Archives des Maladies Professionnelles et de l'Environnement] ; Volume 79, Issue 3, May 2018, Page 373 | https://doi.org/10.1016/j.admp.2018.03.414.
- (en) « 100 years of thermal spray: About the inventor Max Ulrich Schoop », Surface and Coatings Technology, vol. 220,‎ , p. 3–13 (ISSN 0257-8972, DOI 10.1016/j.surfcoat.2012.10.034, lire en ligne, consulté le )
- C. ABERT, Thermisches Spritzen 100 Jahre M.U. Schoop, Association suisse pour la technique du soudage SVSXASS, (2009).
- M.U. SCHOOP, Verfahren zum Herstellen dichter, metallischer ĂśberzĂĽge, Patent-Nr. 258505, DE, (1909).
- M.U. SCHOOP, Verfahren zur Herstellung von dichten metallischen Schichten, Patent-Nr. 49278, CH, (1909).
- R.R. JOHN, W.L. BADE, Journal of the American Rocket Society, J4 31, (1961)
- G. GIANNINI, A DUCATI, Plasma stream apparatus and method, US Patent 2 922 869, (1960)
- R.M. GAGE, O.H. NESTOR, D.M. YENNI, Collimated Electric Arc Powder Deposition Process, U.S. Patent 3 016 477, (1962)
- H. GERDIEN, A. LOTZ, Wiss. Veroffentlichungen Siemenswerk 2, 489, (1922)
- Pawlowski, Lech., Dépôts physiques : techniques, microstructures et propriétés, Lausanne/Paris, Presses polytechniques et universitaires romandes, , 305 p. (ISBN 2-88074-529-2 et 9782880745295, OCLC 52998821, lire en ligne)
- C. Macqueron, « Simulation d’un écoulement plasma en 3D instationnaire avec injection de particules », sur Research Gate, (DOI 10.13140/RG.2.2.24427.85284).
- C. Caruyer, Modélisation de nanomatériaux injectés par voie liquide dans un jet de plasma pour la fabrication de nanostructures (thèse de doctorat), université de Bordeaux 1, .
Voir aussi
Bibliographie
- Lech Pawlowski, The Science and Engineering of Thermal Spray Coatings, Wiley, 1st edition, Chichester, England, 1995.
- Lech Pawlowski, Dépôts Physiques: Techniques, microstructures et propriétés, Presses Polytechniques et Universitaires Romandes, Lausanne, Suisse, 2003.
- Lech Pawlowski, The Science and Engineering of Thermal Spray Coatings, Wiley, 2nd edition, Chichester, England, 2008.