Revêtement intermédiaire
Dans les constructions en ossatures légères (de type baloon frame ou ossature à plateforme) le revêtement intermédiaire (en anglais : sheathing) recouvre l'extérieur de l'ossature d'un pan de toit, de mur, de plancher, ou de plafond. Fixé aux poteaux extérieurs, aux montants, aux chevrons ou aux solives, le revêtement intermédiaire consiste le plus souvent en des panneaux de contreplaqué, des panneaux à copeaux orientés, des panneaux de fibres, des panneaux isolants ou des plaques de plâtre[1]. Certains revêtements intermédiaires extérieurs assurent le contreventement de la paroi. Ils peuvent contribuer à l'isolation thermique de la paroi, résister à l'infiltration du vent et de l'humidité. Le revêtement intermédiaire fonctionne dans de nombreux cas comme une base de clouage pour les matériaux de finition extérieure[2].
_5%252C_mark_a_cut_line_for_the_staircase_of_a_newly_constructed_Mari.jpg.webp)
Sur le revêtement intermédiaire extérieur vient le bardage pour un mur, le revêtement de sol pour un plancher, et pour un toit, la couverture. Le revêtement intermédiaire d'un sol n'est souvent rien d'autre que le support de revêtement de sol[2].
_00148_(37296402190).jpg.webp)
Avant l'avènement des panneaux, les plateformes de plancher étaient constituées de planches en bois de construction[3]; de la même manière le revêtement intermédiaire extérieur des murs n'était autrement constitué qu'avec des planches de un pouce d'épaisseur nominal. Placées obliquement, elles pouvaient assurer en plus le contreventement de la paroi[4]. Sur les planches venait un papier de construction (un papier bouffant et absorbant, imprégné de bitume ou de poix), et ensuite, cloué sur le revêtement intermédiaire, le bardage en bois qui était peint. Côté intérieur venait un lattage qui était enduit de plâtre (Lath and plaster (en)).
Des panneaux de fibres ont été utilisés à partir de 1907 (fiberboard sheathing). Se décomposant au soleil et sous la pluie, ils ont été rendus résistants à l'humidité par imprégnation d'asphalte, d'où le nom de blackjack, gray board, or buffalo board. Selon le Boston Museum of Fine Arts, le panneau de fibres a été breveté pour la première fois en 1858 et a été produit par un certain nombre de fabricants, composé d'une variété de fibres végétales compris la bagasse de canne à sucre, des copeaux de bois, des sous-produits du bois, des déchets de papier, etc. Le panneau de fibre de bois fut vendu comme panneau structural et matériau isolant ; mais il ne fut plus ensuite vendu que comme matériau isolant. En 1920, les panneaux de fibre isolants ne représentaient qu'environ 4 % du revêtement utilisé pour les nouvelles constructions résidentielles ; en 1940, leur utilisation était passée à 20 % et en 1950 à 30 % ; en 1950, environ 50 % des revêtements muraux utilisés dans le MidWest des États-Unis était en panneaux de fibres, tandis que dans le Nord-Ouest Pacifique, où le bois d'œuvre était plus facile à obtenir, les panneaux de fibres isolants n'étaient utilisés que dans environ 10 % des nouvelles maisons construites[5]. Nombre de panneaux furent ainsi utilisés dont certains ont contenu de l'amiante.
Toutes sortes de fibres peuvent être agglomérées par pression. Les produits contenus dans la fibre suffisent à l'aggloméré sans adhésif supplémentaire. Toutefois, différentes substances seront ajoutées : colle de farine, colles, dextrine, plâtre, silicate de soude et argile, colophane, térébenthine, cire de paraffine (Homasote), asphalte (donnant une belle couleur noire foncée aux panneaux de fibres et les rendant peu attractifs pour les termites et fourmis charpentières[6].
Le contreplaqué se développe progressivement, servant premièrement dans l'aéronautique. Avant la fin des années 1920, l'utilisation du contreplaqué dans la construction des bâtiments était limitée aux portes. À la fin des années 1920, le contreplaqué est introduit pour les panneaux de construction[7].
Les années 1930 sont devenues une décennie d'expérimentation sur le logement, par la suite aiguillonné par l'entrée en guerre des Etats-Unis lors de la Seconde Guerre mondiale en 1941. Un certain nombre d'organisations privées ont assumé le rôle d'établissements scientifiques dans le but de créer une maison que la majorité des salariés américains pourraient acquérir. Certains ont exploré les principes de la production de masse et la préfabrication pour réduire le coût des matériaux de construction et du logement[8]. En 1935, le Forest Products Laboratory du département de l'Agriculture des États-Unis d'autre part, a développé une maison à structure panneautée en contreplaqué dite stress-skined, à revêtement travaillant (dans lequel les revêtements résistent à la flexion et aux efforts directs, « ajoutant ainsi à la capacité porteuse de l'ossature »[9]), ce qui a stimulé le développement de techniques de panneaux préfabriqués. Offrant des perspectives de profit intéressantes, dans le secteur des maisons à bas prix, le contreplaqué va devenir un matériau de choix par les premiers constructeurs de maisons modulaires et préfabriquées[10].
La John B. Pierce Foundation, pionnière dans la recherche visant à développer de petites habitations commercialisables, utilisant des matériaux innovants et des composants préfabriqués, présente à l'Exposition universelle de New York, en 1939, un modèle de maison modulaire employant des panneaux structuraux en contreplaqué[11]. En 1941, lorsque les Etats-Unis entrent en guerre, la Pierce Foundation est associée à certain nombre de fabricants de panneaux, compris la Celotex Company et la Homasote Company qui seront alors partie prenante dans le développement de différents prototypes de maisons qui seront construites massivement pendant la Deuxième Guerre mondiale[8]. Ainsi le Celotex-Cemesto, un composite bagasse-amiante-ciment, servira à la construction de maisons préfabriquées, les Cemestos qui seront construites à des milliers d'exemplaires[12].
_40%252C_fastens_a_sheet_of_plywood.jpg.webp)
Dans les années 70, les planches ont laissé place aux panneaux structuraux, plus stables, requérant moins de manipulation et faciles à travailler, l’industrie n’est donc jamais retournée en arrière[3]. Lancés fin des années 1970, les panneaux à copeaux orientés ont remplacé progressivement les panneaux contreplaqués[13]. Un procédé de fabrication très automatisé et l’utilisation d’essences de bois feuillus sous-utilisées, un prix plus intéressant, lui ont permis de prendre les parts de marché du contreplaqué[14].
Les panneaux de revêtement structuraux résistent aux charges latérales et contribuent à la rigidité globale du bâtiment, éliminant la plupart du temps le besoin de contreventement. Les panneaux peuvent être installés verticalement ou horizontalement, à l'extérieur de l'ossature. Le revêtement appliqué verticalement ne nécessite généralement pas de blocage car tous les bords sont alignés avec les éléments de charpente. Le revêtement en contreplaqué appliqué horizontalement est plus solide que le revêtement appliqué verticalement, car les placages de la plus haute qualité et la plupart des plis sont orientés selon la longueur du panneau de contreplaqué. Cette résistance horizontale agit de concert avec la résistance verticale des montants. L'orientation horizontale est utilisée lorsque la rigidité du contreplaqué est requise pour le support des matériaux de parement, tels que les bardeaux ou le stuc[15]. Des panneaux de plâtre renforcés de fibres sont employés lorsqu'une résistance au feu est requise[15].
Les panneaux muraux contreventés revêtus de plaques de plâtre offrent moins de résistance aux charges latérales que ceux revêtus de panneaux de copeaux orientés (OSB), de panneaux de copeaux, de contreplaqué ou de bois de construction posé en diagonale[16].
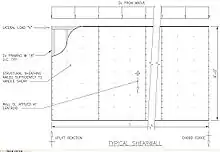
Lorsque les forces latérales sur les murs sont extrêmes, comme dans les zones sujettes aux ouragans ou aux tremblements de terre, des murs de contreventement (Shear wall (en)) spécialement conçus sont généralement nécessaires pour résister à ces forces. Ceux-ci permettent notamment d'éviter les déformations causées par les forces latérales en résistant au cisaillement[17].
Notes et références
- « Grand dictionnaire terminologique - revêtement intermédiaire », sur gdt.oqlf.gouv.qc.ca (consulté le )
- (en) H. Leslie Simmons, Olin's Construction: Principles, Materials, and Methods, John Wiley & Sons, (ISBN 978-1-118-06705-5, lire en ligne)
- « Panneaux revêtement sol | Québec habitation » (consulté le )
- (en) Forest Products Laboratory (U.S.), Wood Handbook: Basic Information on Wood as a Material of Construction with Data for Its Use in Design and Specification, U.S. Government Printing Office, (lire en ligne)
- « Fiberboard Building Wall, Ceiling & Roof Sheathing Insulating Board Sheathing, Sound Insulation Board Product Guide », sur inspectapedia.com (consulté le )
- « Beaverboard Buffalo Board Identification Beaverboard Wall Sheathing, Insulating Board Identification Key », sur inspectapedia.com (consulté le )
- « Twentieth-Century Building Materials: History and Conservation », sur www.getty.edu (consulté le )
- (en) David L. Ames et Linda Flint McClelland, Historic Residential Suburbs: Guidelines for Evaluation and Documentation for the National Register of Historic Places, U.S. Department of the Interior, National Park Service, National Register of Historic Places, (lire en ligne)
- « Unasylva - No. 101-102-103 - L'emploi de bois dans la construction d'habitations - Section 3 - Les produits du bois et leur utilisation dans la construction », sur www.fao.org (consulté le )
- (en) Internet Archive, American Builder and Building Age 1937-08: Vol 59 Iss 8, Simmons Boardman Publ Corp, (lire en ligne)
- (en) « Adventures in Atomic Tourism: Little Cemestos Houses for You and Me », sur McSweeney's Internet Tendency (consulté le )
- « Celotex® Cemesto Board History, ingredients, maintenance, repair », sur inspectapedia.com (consulté le )
- « Why OSB Continues To Outpace Plywood », sur www.architectmagazine.com (consulté le )
- « Revêtements structuraux », sur Cecobois (consulté le )
- (en) Rob Thallon, Graphic Guide to Frame Construction: Details for Builders and Designers, Taunton Press, (ISBN 978-1-56158-353-9, lire en ligne)
- (en-CA) Qccodes.ca, « Utilisation d’un revêtement de finition intérieur en plaques de plâtre pour assurer le contreventement requis - », (consulté le )
- « Grand dictionnaire terminologique - mur de contreventement », sur gdt.oqlf.gouv.qc.ca (consulté le )