Dépôt de fil fondu
Le dépôt de fil fondu (DFF)[1] ou Fused deposition modeling (FDM)[2] ou encore Fused Filament Fabrication (FFF)[3] est une technologie d'impression 3D[4]. On appelle aussi ce procédé impression 3D par extrusion de matériau Material Extrusion 3D printing (MEX)[5].
Cette technologie consiste à déposer de la matière à l'état liquide couche par couche. La technologie utilise le plus souvent un filament de matière polymère qui est fondu puis extrudé pour construire une pièce couche par couche. Le matériau d’apport est extrudé au travers d’une buse sur la table de la machine. Le mouvement de la table ou de la buse permet de créer une couche de matériau ayant la géométrie désirée. La succession des différentes couches permet de créer la pièce finale.
Les filaments peuvent être composés de diverses matières, mais les plus communes sont le PLA et l’ABS[6]. Le MEX permet aussi de mettre en forme des mélanges de polymères et de poudres métalliques ou céramiques[7] - [8]. Pour la production de pièce de céramique ou métallique, des étapes de déliantage et de frittage seront nécessaires afin de retirer le liant polymérique utilisé lors de l’extrusion et pour densifier la pièce finale[9]. Le matériau d’apport peut être sous forme de granule, de fil ou de pâte dépendamment du type d’extrudeur utilisé[8].
Histoire
Cette technique a été mise au point en 1988 au sein de l’entreprise Stratasys, sous le nom de FDM. Le brevet de la technologie a expiré en 2009 et, tout de suite après cela, la diffusion des imprimantes DFF a connu un grand succès. Le terme Dépôt de Fil Fondu est neutre en français, mais en anglais il est préférable d'utiliser l'acronyme de FFF, car celui-ci a été formulé après la fin du brevet par des associations telles que RepRap, alors que le nom FDM reste la propriété de Stratasys.
Procédé
Le DFF utilise l’extrusion d’une matière polymère qui est poussée dans une buse d’impression. Dans la grande majorité des imprimantes, la matière est stockée sous la forme d’un filament. La buse d’impression est chauffante, et fait fondre le polymère lors du passage dans la buse. Le débit d’impression est contrôlé par une roue en amont de la buse. Celle-ci tourne et entraîne le filament, le forçant dans la buse.
Le polymère qui est éjecté de la buse par la pression est en fusion et va se coller sur le matériau en dessous de lui. Afin de contrôler le dépôt, et afin de rester en phase liquide, la hauteur entre la buse et le matériau sur lequel on imprime est contrôlée. Cette distance, que l’on appelle hauteur de couche, est directement reliée au diamètre de la buse. En effet, les buses ont un diamètre qui varie commercialement entre 0,3 et 1 mm et la hauteur de couche ne doit pas dépasser le tiers de ce diamètre. La hauteur de couche varie donc entre 30 et 300 μm sur les imprimantes du commerce, selon la buse.
Variantes
La technique de DFF ne nécessite pas que la matière soit sous la forme d’un filament : celle-ci peut aussi prendre la forme d’un cylindre, d’une pâte/barbotine (dans ce cas, il n'y a pas de fusion de la matière, qui est déjà sous une forme fluide, mais une injection par piston, le reste de la technique étant le même), ou de granules.
On peut décliner la fabrication additive par extrusion de matériau en trois familles selon le principe d’extrusion utilisé. La première famille regroupe les systèmes qui utilisent un apport continu de matière à l’état solide. La matière est ensuite fondue lors de son passage dans la buse par un apport d’énergie thermique. On peut distinguer deux méthodes de mise en forme de la matière qui alimentera l’extrudeur : une bobine de filament ou une cartouche cylindrique. La bobine de filament, principe largement utilisé pour la fabrication additive des polymères par fil fondu (Fused Filament Fabrication ou FFF), présente l’avantage d’offrir une extrusion continue. Toutefois, comme le filament doit conserver une certaine flexibilité pour permettre l’enroulement, la fraction volumique de poudre dans le mélange est limitées à un maximum 60%[10]. Cette faible proportion de poudre risque de générer des problèmes lors du déliantage ou du frittage et conduire à la production de pièce contenant un taux de porosité plus élevé. Ce type d’extrusion est donc moins adapté pour la production de pièce de céramique ou de métal et convient mieux à la mise en forme de pièces polymériques seulement. Pour éviter ce problème, certaines imprimantes optent alors pour une alimentation via une cartouche cylindrique linéaire. Cette méthode permet alors d’augmenter la fraction volumique de poudre dans le mélange, mais on perd l’intérêt principal de l’extrusion en continu. Pour cette famille d’extrusion, la principale difficulté est de conserver un débit de matière constant[11]. Comme la viscosité des polymères varie généralement en fonction de la température et du taux de cisaillement[12], le système doit être en mesure de compenser en temps réel le glissement entre les roues motrices et le fil de matière. En effet, si la viscosité du fil fondu augmente, la pression dans l’extrudeur est plus grande et occasionne alors un glissement plus important. Le diamètre du filament ou de la cartouche doit aussi être constant sur toute sa longueur pour éviter des fluctuations de débit. Finalement, cette famille a aussi l’inconvénient de nécessiter une mise en forme du mélange avant de pouvoir procéder à l’extrusion.
La deuxième famille d’extrudeur est celle utilisant le principe de vis sans fin. Ici, le mélange est ajouté sous forme de granulé dans le réservoir de la machine et sera liquéfié par l’énergie thermique et mécanique lors de son passage dans la vis sans fin. L’extrudeur à vis a pour avantage de liquéfier au fur et à mesure le mélange requis pour l’impression, il est ainsi possible d’imprimer sans interruption des pièces de volume important puisque du mélange peut être ajouté sans suspendre le procédé d’impression. Ce type d’extrudeur permet d’utiliser une grande variété de mélange avec des chargements solides élevés[13]. Cependant, un extrudeur à vis est généralement lourd, encombrant et dispendieux. Ce type d’extrudeur est largement répandu pour la production de pièces polymériques, car des pressions élevées sont requises pour leur mise en forme. En MEX de pièces métalliques ou céramiques, la nature abrasive des mélanges entraîne l’usure prématurée de ce type d’équipement qui doit alors être conçu spécifiquement pour ce type de mélange[14]. Pour les mélanges à faible viscosité, les faibles pressions nécessaires à la mise en forme du mélange ne justifient pas l’intérêt de s’équiper d’un système coûteux et complexe comme ce type d’extrudeur.
La troisième famille regroupe les systèmes où le matériau est inséré directement dans le réservoir sous forme liquide ou sous forme de granulé qui sera ensuite liquéfié par un apport d’énergie au réservoir. Une fois le mélange à l’état liquide, deux méthodes peuvent être utilisées pour extruder la matière via la buse. La première est similaire à une seringue, où le déplacement du piston est contrôlé par une pression d’air. Ce principe, limité en pression, est principalement utilisé pour la fabrication de pièce de très petite taille, généralement en céramique, par micro-extrusion avec des buses très fines pouvant aller jusqu’à 0.1 µm de diamètre[15]. La deuxième méthode utilise un piston motorisé qui est utilisé pour forcer le mélange à l’extérieur du réservoir via la buse. Cette technique permet l’utilisation d’une grande diversité de matériau et de mélange[16]. La précision du contrôle de la vitesse de déplacement du piston est cruciale afin d’avoir une maîtrise adéquate sur le débit sortant de matière[17]. Il est généralement avantageux d’avoir un diamètre de piston faible afin que sa vitesse de déplacement ne soit pas trop limitée (i.e., un faible déplacement du piston n’engendre pas le déplacement d’un grand volume de matière). Le volume du réservoir ne doit pas être trop élevé puisque dû à la composition de certains mélanges, les poudres en suspension dans le liant polymérique cherchent à se déposer dans le bas du réservoir sous l’effet de la gravité, rendant ainsi le mélange hétérogène. Pour les pièces de plus grande dimension, il peut donc être nécessaire de remplir le réservoir à plusieurs reprises. Il est à noter que les mélanges à très faible viscosité peuvent être problématiques pour l’extrudeur à piston puisque la matière tend à s’écouler de la buse par gravité sans que le piston y applique une force.
L’impression
Le DFF commence à la création de la pièce à l'aide d'un logiciel de CAO. Ce modèle est exporté sous forme d'un fichier STL dans lequel la pièce est représentée par un ensemble de triangles orientés dans l'espace à trois dimensions. Ce fichier est interprété par un logiciel d’impression – tel que Cura – qui découpe le solide en tranches et crée des supports si nécessaire. La buse suit un parcours pour chaque couche, celui-ci est contrôlé par de nombreux paramètres dans le logiciel d’impression, comme le taux de remplissage, le motif de remplissage, la hauteur des couches, le nombre de cordons d’impression… Ce solide tranché est ensuite transformé en instructions pour l’imprimante 3D, sous forme d’un fichier GCODE. Celui-ci contient les instructions de déplacement de la buse selon les axes X et Y et, en fonction des machines, les instructions de déplacement de la buse ou du plateau selon l'axe Z. Le GCODE est ensuite traduit par l’imprimante qui actionne des moteurs (servomoteur ou pas-à-pas) afin de traduire le mouvement. À chaque fin de couche, la distance entre le plateau et la buse augmente de l’incrément de hauteur de couche. Ce procédé continue jusqu’à la fin de la pièce.
Afin d’avoir une bonne adhérence entre le cordon et la couche inférieure, que ce soit la pièce ou le plateau, la température doit être contrôlée. En effet, les plateaux sont chauffés au-dessus de 60 °C, et le contrôle de température de la chambre d’impression (ou de la pièce s'il n'y a pas de chambre) permet une meilleure impression en évitant les malformations. De plus, une atmosphère contrôlée en gaz inerte améliore la qualité des impressions, mais la mise en place d’une enceinte étanche autour de l’imprimante et le contrôle du contenu de celle-ci est plus difficile pour le grand public que celle d’une simple enceinte isolante.
Le matériau d’impression
De nombreux types de polymère sont disponibles pour l’impression. Des matériaux plastiques sont de plus en plus utilisés dans le domaine industriel. Les plus courants sont le PLA, l’ABS, le PVA en tant que support, car soluble à l’eau, le PC, le Nylon, le PET(G), le PP et le PA[18]. On peut aussi trouver des matériaux renforcés avec des fibres, notamment du PLA/PET chargé en fibres de carbone ou du Nylon chargé en fibres de verre. De plus, certains filaments à but esthétique sont chargés en bois, en pierre ou en métal afin que la texture, le poids et l’esthétique soient différents de ceux du plastique. Enfin nous pouvons retrouver des filaments flexibles tel que le TPU. A noter que pour imprimer ce genre de matériaux, il faut que le moteur entraînant la roue cranté servant à pousser le filament dans la buse soit monté en "direct drive". C'est a dire directement sur la tête d'impression. Cet installation est nécessaire pour éviter que le filament de se tasse dans la tube guide utilisé dans le cas d'un moteur d'extrusion déporté. Ce type de filament présente des propriétés mécaniques très intéressantes.
La fabrication par extrusion permet mettre en forme des mélanges poudre-liant avec une approche similaire au moulage par injection des poudres. Le MEX-HP présente un fort potentiel industriel pour le développement d’un procédé de fabrication additive de pièces métalliques aux géométries complexes. En effet, puisque les propriétés finales des pièces sont principalement contrôlées par le frittage, les industries de pointe plus conservatrices tel que l’aéronautique[19] sont plus enclines à adopter ce procédé de fabrication additive.
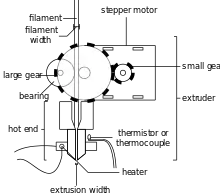
Phénomènes physiques
Durant l’extrusion, le filament en polymère est poussé dans la buse d’impression par des rouleaux. Au contact de la buse chauffée et par diffusion, le filament passe à un état visqueux et, avec la pression générée par l’avancée continue du filament, est extrudé de la buse. Le flux de la matière, les paramètres de chauffe et le comportement du flux sont les principaux phénomènes à prendre en compte durant une impression.
Puisque les rouleaux sont les seules pièces contrôlées durant l’extrusion, le filament subit :
- une contrainte en extension entre les rouleaux et la bobine.
- une contrainte en compression entre les rouleaux et la buse.
La force requise pour extruder la « fonte » doit être suffisante pour contrer la perte de charge à travers le système. Cette perte de charge dépend de la viscosité du filament une fois passé à l'état fluide et de la géométrie de l’écoulement. Des phénomènes de rhéofluidification se manifestent durant l’extrusion[12]. Le contrôle de la vitesse d’extrusion est également un paramètre important à contrôler afin de permettre une bonne adhésion des couches et une bonne précision dimensionnelle[11]. Le contrôle de la vitesse de refroidissement est également un paramètre déterminant pour le contrôle de la morphologie des macroporosités causée par le dépôt successif de couches de matière (défauts interjoncs). Plus le refroidissement est rapide, plus les porosités seront anguleuses ce qui amène à une diminution des propriétés mécaniques en raison de la concentration des contraintes plus importante[20]. Le refroidissement doit donc être assez rapide pour limiter l’affaissement entre le dépôt des couches, mais suffisamment lent pour permettre l’écoulement partiel de la nouvelle couche déposée dans les interstices à combler. Les principaux facteurs qui affectent la précision dimensionnelle et géométrique des échantillons produits par MEX sont l'épaisseur de la couche, l'orientation de construction, l'écoulement du matériau, la vitesse de remplissage, la température d'extrusion et la vitesse de refroidissement après le dépôt[21] - [22] - [23] - [24].
Déliantage des pièces métalliques et céramiques
Pour les pièces métalliques et céramique, le déliantage permet de retirer le liant polymérique qui agissait comme média de transport pour la poudre avant l’étape de frittage. Différentes méthodes peuvent être utilisées pour réaliser cette étape telle que la dissolution par solvant, par réaction catalytique (réaction chimique avec des vapeurs d’acide) ou encore par traitement thermique[25]. Une combinaison de plusieurs méthodes est aussi fréquente lors de l’utilisation de liant ayant de multiples constituants (i.e., majoritaire et de renfort). Dans la littérature actuelle en MEX, la majorité des pièces sont d’abord déliantées par dissolution dans un solvant pour retirer la majorité du liant. Le constituant de renfort permet à la pièce de conserver une certaine rigidité pour la manutention dans la fournaise où le reste du liant sera retiré par traitement thermique avant le début du frittage. Il est primordial de retirer complètement le liant avant que le frittage de la pièce débute puisque liant résiduel non éliminé avant la montée en température du frittage s'échapperait rapidement de la pièce et provoquerait la fissuration de la pièce ou la formation de suies pouvant contaminer la pièce en augmentant le taux de carbone du matériau[26]. Le liant des mélanges utilisés en MEX avec un extrudeur à piston est généralement composé majoritairement de cires organiques ou de polymères à faible densité. Il est donc possible de les décomposer et de les vaporiser à des températures relativement faibles, habituellement inférieures à 600°C[27]. Toutefois, le risque de grande déformation à ces températures est très élevé en raison de l’importante fluidité du liant polymérique. Le déliantage est souvent considéré comme l’étape la plus difficile à maîtriser dans le procédé puisqu’il faut éviter la formation de fissures ou la déformation des pièces[28]. Le déliantage thermique consiste simplement à placer la pièce extrudée dans un four et à augmenter la température de façon contrôlée jusqu’à la dégradation du liant polymérique.
Références
- « L'impression par dépôt de filament fondu », (consulté le )
- « Qu'est-ce que la technologie d'impression 3D FDM ? », sur Stratasys (consulté le )
- « Fused filament fabrication - RepRap », sur reprap.org (consulté le )
- Anne-Françoise Obaton, Alain Bernard, Georges Taillandier et Jean-Marc Moschetta, « Fabrication additive et besoins en contrôle », 17th International Congress of Metrology, EDP Sciences, (ISBN 9782759818662, DOI 10.1051/metrology/20150004001, lire en ligne, consulté le )
- (en) Chanun Suwanpreecha et Anchalee Manonukul, « A Review on Material Extrusion Additive Manufacturing of Metal and How It Compares with Metal Injection Moulding », Metals, vol. 12, no 3, , p. 429 (ISSN 2075-4701, DOI 10.3390/met12030429, lire en ligne, consulté le )
- « PLA, ABS, PETG... Guide d'achat des matériaux pour imprimante 3D en fonction de l'application », sur Filimprimante3D (consulté le )
- (en) N. Shahrubudin, T. C. Lee et R. Ramlan, « An Overview on 3D Printing Technology: Technological, Materials, and Applications », Procedia Manufacturing, the 2nd International Conference on Sustainable Materials Processing and Manufacturing, SMPM 2019, 8-10 March 2019, Sun City, South Africa, vol. 35, , p. 1286–1296 (ISSN 2351-9789, DOI 10.1016/j.promfg.2019.06.089, lire en ligne, consulté le )
- (en) Joamin Gonzalez-Gutierrez, Santiago Cano, Stephan Schuschnigg et Christian Kukla, « Additive Manufacturing of Metallic and Ceramic Components by the Material Extrusion of Highly-Filled Polymers: A Review and Future Perspectives », Materials, vol. 11, no 5, , p. 840 (ISSN 1996-1944, PMID 29783705, PMCID PMC5978217, DOI 10.3390/ma11050840, lire en ligne, consulté le )
- (en) Joamin Gonzalez-Gutierrez, Florian Arbeiter, Thomas Schlauf et Christian Kukla, « Tensile properties of sintered 17-4PH stainless steel fabricated by material extrusion additive manufacturing », Materials Letters, vol. 248, , p. 165–168 (ISSN 0167-577X, DOI 10.1016/j.matlet.2019.04.024, lire en ligne, consulté le )
- (en) Joamin Gonzalez-Gutierrez, Santiago Cano, Stephan Schuschnigg et Christian Kukla, « Additive Manufacturing of Metallic and Ceramic Components by the Material Extrusion of Highly-Filled Polymers: A Review and Future Perspectives », Materials, vol. 11, no 5, , p. 840 (ISSN 1996-1944, PMID 29783705, PMCID PMC5978217, DOI 10.3390/ma11050840, lire en ligne, consulté le )
- (en) Paramjot Singh, Qasim Shaikh, Vamsi K. Balla et Sundar V. Atre, « Estimating Powder-Polymer Material Properties Used in Design for Metal Fused Filament Fabrication (DfMF3) », JOM, vol. 72, no 1, , p. 485–495 (ISSN 1047-4838 et 1543-1851, DOI 10.1007/s11837-019-03920-y, lire en ligne, consulté le )
- (en) Arit Das, Eric L. Gilmer, Saeid Biria et Michael J. Bortner, « Importance of Polymer Rheology on Material Extrusion Additive Manufacturing: Correlating Process Physics to Print Properties », ACS Applied Polymer Materials, vol. 3, no 3, , p. 1218–1249 (ISSN 2637-6105 et 2637-6105, DOI 10.1021/acsapm.0c01228, lire en ligne, consulté le )
- (en) Qinglong He, Jie Jiang, Xianfeng Yang et Li Zhang, « Additive manufacturing of dense zirconia ceramics by fused deposition modeling via screw extrusion », Journal of the European Ceramic Society, vol. 41, no 1, , p. 1033–1040 (ISSN 0955-2219, DOI 10.1016/j.jeurceramsoc.2020.09.018, lire en ligne, consulté le )
- (en) Kedarnath Rane et Matteo Strano, « A comprehensive review of extrusion-based additive manufacturing processes for rapid production of metallic and ceramic parts », Advances in Manufacturing, vol. 7, no 2, , p. 155–173 (ISSN 2095-3127 et 2195-3597, DOI 10.1007/s40436-019-00253-6, lire en ligne, consulté le )
- (en) Laura del-Mazo-Barbara et Maria-Pau Ginebra, « Rheological characterisation of ceramic inks for 3D direct ink writing: A review », Journal of the European Ceramic Society, vol. 41, no 16, , p. 18–33 (ISSN 0955-2219, DOI 10.1016/j.jeurceramsoc.2021.08.031, lire en ligne, consulté le )
- (en) Lennart Waalkes, Jan Längerich, Felix Holbe et Claus Emmelmann, « Feasibility study on piston-based feedstock fabrication with Ti-6Al-4V metal injection molding feedstock », Additive Manufacturing, vol. 35, , p. 101207 (ISSN 2214-8604, DOI 10.1016/j.addma.2020.101207, lire en ligne, consulté le )
- (en) Lennart Waalkes, Jan Längerich, Philipp Imgrund et Claus Emmelmann, « Piston-Based Material Extrusion of Ti-6Al-4V Feedstock for Complementary Use in Metal Injection Molding », Materials, vol. 15, no 1, , p. 351 (ISSN 1996-1944, PMID 35009497, PMCID PMC8746147, DOI 10.3390/ma15010351, lire en ligne, consulté le )
- « Tableau des matériaux d'impression DFF », sur filimprimante3d.fr (consulté le )
- (en) Vaishnav Madhavadas, Divyansh Srivastava, Utkarsh Chadha et Sakthivel Aravind Raj, « A review on metal additive manufacturing for intricately shaped aerospace components », CIRP Journal of Manufacturing Science and Technology, vol. 39, , p. 18–36 (ISSN 1755-5817, DOI 10.1016/j.cirpj.2022.07.005, lire en ligne, consulté le )
- (en) Vladimir E. Kuznetsov, Alexey N. Solonin, Azamat Tavitov et Oleg Urzhumtsev, « Increasing strength of FFF three-dimensional printed parts by influencing on temperature-related parameters of the process », Rapid Prototyping Journal, vol. 26, no 1, , p. 107–121 (ISSN 1355-2546 et 1355-2546, DOI 10.1108/RPJ-01-2019-0017, lire en ligne, consulté le )
- (en) A. Boschetto et L. Bottini, « Accuracy prediction in fused deposition modeling », The International Journal of Advanced Manufacturing Technology, vol. 73, nos 5-8, , p. 913–928 (ISSN 0268-3768 et 1433-3015, DOI 10.1007/s00170-014-5886-4, lire en ligne, consulté le )
- (en) Ala’aldin Alafaghani, Ala Qattawi, Buraaq Alrawi et Arturo Guzman, « Experimental Optimization of Fused Deposition Modelling Processing Parameters: A Design-for-Manufacturing Approach », Procedia Manufacturing, 45th SME North American Manufacturing Research Conference, NAMRC 45, LA, USA, vol. 10, , p. 791–803 (ISSN 2351-9789, DOI 10.1016/j.promfg.2017.07.079, lire en ligne, consulté le )
- (en) Leonardo Santana, Jorge Lino Alves et Aurélio da Costa Sabino Netto, « A study of parametric calibration for low cost 3D printing: Seeking improvement in dimensional quality », Materials & Design, vol. 135, , p. 159–172 (ISSN 0264-1275, DOI 10.1016/j.matdes.2017.09.020, lire en ligne, consulté le )
- (en) Chun-Ying Lee et Chung-Yin Liu, « The influence of forced-air cooling on a 3D printed PLA part manufactured by fused filament fabrication », Additive Manufacturing, vol. 25, , p. 196–203 (ISSN 2214-8604, DOI 10.1016/j.addma.2018.11.012, lire en ligne, consulté le )
- (en) Lovro Gorjan, Aleš Dakskobler et Tomaž kosmač, « Partial wick-debinding of low-pressure powder injection-moulded ceramic parts », Journal of the European Ceramic Society, vol. 30, no 15, , p. 3013–3021 (ISSN 0955-2219, DOI 10.1016/j.jeurceramsoc.2010.07.011, lire en ligne, consulté le )
- (en) S. Banerjee et C. J. Joens, « 7 - Debinding and sintering of metal injection molding (MIM) components », dans Handbook of Metal Injection Molding (Second Edition), Woodhead Publishing, coll. « Woodhead Publishing Series in Metals and Surface Engineering », (ISBN 978-0-08-102152-1, DOI 10.1016/b978-0-08-102152-1.00009-x, lire en ligne), p. 129–171
- (en) Lovro Gorjan, Tomaž Kosmač et Aleš Dakskobler, « Single-step wick-debinding and sintering for powder injection molding », Ceramics International, vol. 40, no 1, Part A, , p. 887–891 (ISSN 0272-8842, DOI 10.1016/j.ceramint.2013.06.083, lire en ligne, consulté le )
- J.E Zorzi, C.A Perottoni et J.A.H da Jornada, « A new partially isostatic method for fast debinding of low-pressure injection molded ceramic parts », Materials Letters, vol. 57, nos 24-25, , p. 3784–3788 (ISSN 0167-577X, DOI 10.1016/s0167-577x(03)00179-4, lire en ligne, consulté le )